PROCEDURE
PROCEDURE |
Carry out trouble diagnosis shown in the following DTC table.
When performing trouble diagnosis which is not shown in the DTC table, refer to the next item Drive cycle.

DTC | Item | Condition |
P0030
|
HO2S Heater
Control Circuit (Bank 1 Sensor 1)
|
—
|
P0031
|
HO2S Heater
Control Circuit Low (Bank 1 Sensor 1)
|
—
|
P0032
|
HO2S Heater
Control Circuit High (Bank 1 Sensor 1)
|
—
|
P0037
|
HO2S Heater
Control Circuit Low (Bank 1 Sensor 2)
|
—
|
P0038
|
HO2S Heater
Control Circuit High (Bank 1 Sensor 2)
|
—
|
P0102
|
Mass or
Volume Air Flow Circuit Low Input
|
—
|
P0103
|
Mass or
Volume Air Flow Circuit High Input
|
—
|
P0107
|
Manifold
Absolute Pressure/Barometric Pressure Circuit Low Input
|
—
|
P0108
|
Manifold
Absolute Pressure/Barometric Pressure Circuit High Input
|
—
|
P0112
|
Intake
Air Temperature Circuit Low Input
|
—
|
P0113
|
Intake
Air Temperature Circuit High Input
|
—
|
P0117
|
Engine
Coolant Temperature Circuit Low Input
|
—
|
P0118
|
Engine
Coolant Temperature Circuit High Input
|
—
|
P0122
|
Throttle/Pedal
Position Sensor/Switch “A” Circuit Low
Input
|
—
|
P0123
|
Throttle/Pedal
Position Sensor/Switch “A” Circuit High
Input
|
—
|
P0130
|
O
2
Sensor
Circuit (Bank 1 Sensor 1)
|
—
|
P0134
|
O
2
Sensor
Circuit No Activity Detected (Bank 1 Sensor 1)
|
—
|
P0137
|
O
2
Sensor
Circuit Low Voltage (Bank 1 Sensor 2)
|
—
|
P0138
|
O
2
Sensor
Circuit High Voltage (Bank 1 Sensor 2)
|
—
|
P0181
|
Fuel Temperature
Sensor “A” Circuit Range/Performance
|
—
|
P0182
|
Fuel Temperature
Sensor “A” Circuit Low Input
|
—
|
P0183
|
Fuel Temperature
Sensor “A” Circuit High Input
|
—
|
P0230
|
Fuel Pump
Primary Circuit
|
—
|
P0245
|
Turbo/Super
Charger Wastegate Solenoid “A” Low
|
—
|
P0301
|
Cylinder
1 Misfire Detected
|
—
|
P0302
|
Cylinder
2 Misfire Detected
|
—
|
P0303
|
Cylinder
3 Misfire Detected
|
—
|
P0304
|
Cylinder
4 Misfire Detected
|
—
|
P0327
|
Knock Sensor
1 Circuit Low Input (Bank 1 or Single Sensor)
|
—
|
P0328
|
Knock Sensor
1 Circuit High Input (Bank 1 or Single Sensor)
|
—
|
P0335
|
Crankshaft
Position Sensor “A” Circuit
|
—
|
P0336
|
Crankshaft
Position Sensor “A” Circuit Range/Performance
|
—
|
P0340
|
Camshaft
Position Sensor “A” Circuit (Bank 1 or Single
Sensor)
|
—
|
P0341
|
Camshaft
Position Sensor “A” Circuit Range/Performance
(Bank 1 or Single Sensor)
|
—
|
P0447
|
Evaporative
Emission Control System Vent Control Circuit Open
|
—
|
P0448
|
Evaporative
Emission Control System Vent Control Circuit Shorted
|
—
|
P0452
|
Evaporative
Emission Control System Pressure Sensor Low Input
|
—
|
P0453
|
Evaporative
Emission Control System Pressure Sensor High Input
|
—
|
P0458
|
Evaporative
Emission Control System Purge Control Valve Circuit Low
|
—
|
P0461
|
Fuel Level
Sensor Circuit Range/Performance
|
—
|
P0462
|
Fuel Level
Sensor Circuit Low Input
|
—
|
P0463
|
Fuel Level
Sensor Circuit High Input
|
—
|
P0502
|
Vehicle
Speed Sensor Circuit Low Input
|
—
|
P0503
|
Vehicle
Speed Sensor Intermittent/Erratic/High
|
—
|
P0508
|
Idle Control
System Circuit Low
|
—
|
P0509
|
Idle Control
System Circuit High
|
—
|
P0512
|
Starter
Request Circuit
|
—
|
P0519
|
Idle Control
System Malfunction (Fail-Safe)
|
—
|
P0545
|
Exhaust
Temperature Sensor Circuit Low - Bank 1
|
—
|
P0565
|
Cruise
Control On Signal
|
—
|
P0604
|
Internal
Control Module Random Access Memory (RAM) Error
|
—
|
P0691
|
Cooling
Fan 1 Control Circuit Low
|
—
|
P0703
|
Torque
Converter/Brake Switch “B” Circuit
|
—
|
P0705
|
Transmission
Range Sensor Circuit (PRNDL Input)
|
—
|
P0710
|
Transmission
Fluid Temperature Sensor Circuit
|
—
|
P0716
|
Torque
Converter Turbine Speed Sensor
|
—
|
P0720
|
Output
Speed Sensor Circuit
|
—
|
P0726
|
Engine
Speed Input Circuit Range/Performance
|
—
|
P0731
|
Gear 1
Incorrect Ratio
|
—
|
P0732
|
Gear 2
Incorrect Ratio
|
—
|
P0733
|
Gear 3
Incorrect Ratio
|
—
|
P0734
|
Gear 4
Incorrect Ratio
|
—
|
P0741
|
Torque
Converter Clutch Circuit Performance or Stuck Off
|
—
|
P0743
|
Torque
Converter Clutch Circuit Electrical
|
—
|
P0748
|
Pressure
Control Solenoid “A” Electrical
|
—
|
P0753
|
Shift Solenoid “A” Electrical
|
—
|
P0758
|
Shift Solenoid “B” Electrical
|
—
|
P0771
|
Low Clutch
Timing Solenoid
|
—
|
P0778
|
Pressure
Control Solenoid “B” Electrical
|
—
|
P0785
|
Shift/Timing
Solenoid
|
—
|
P0851
|
Neutral
Switch Input Circuit Low
|
—
|
P0852
|
Neutral
Switch Input Circuit High
|
—
|
P0864
|
TCM Communication
Circuit Range/Performance
|
—
|
P0865
|
TCM Communication
Circuit Low
|
—
|
P0866
|
TCM Communication
Circuit High
|
—
|
P1134
|
A/F
Sensor Micro-Computer Problem
|
—
|
P1152
|
O
2
Sensor
Circuit Range/Performance (Low) (Bank1 Sensor1)
|
—
|
P1153
|
O
2
Sensor
Circuit Range/Performance (High) (Bank1 Sensor1)
|
—
|
P1301
|
Misfire
Detected (High Temperature Exhaust Gas)
|
—
|
P1400
|
Fuel Tank
Pressure Control Solenoid Valve Circuit Low
|
—
|
P1420
|
Fuel Tank
Pressure Control Sol. Valve Circuit High
|
—
|
P1446
|
Fuel Tank
Sensor Control Valve Circuit Low
|
—
|
P1447
|
Fuel Tank
Sensor Control Valve Circuit High
|
—
|
P1448
|
Fuel Tank
Sensor Control Valve Range/Performance
|
—
|
P1491
|
Positive
Crankcase Ventilation (Blow-by) Function Problem
|
—
|
P1518
|
Starter
Switch Circuit Low Input
|
—
|
P1544
|
Exhaust
Gas Temperature Too High
|
—
|
P1560
|
Back-up
Voltage Circuit Malfunction
|
—
|
P1700
|
Throttle
Position Sensor
|
—
|
P1711
|
Engine
Torque Control Signal 1 Circuit Malfunction
|
—
|
P1712
|
Engine
Torque Control Signal 2 Circuit Malfunction
|
—
|
P2006
|
Intake
Manifold Runner Control Stuck Closed (Bank 1)
|
—
|
P2007
|
Intake
Manifold Runner Control Stuck Closed (Bank 2)
|
—
|
P2008
|
Intake
Manifold Runner Control Circuit / Open (Bank 1)
|
—
|
P2009
|
Intake
Manifold Runner Control Circuit Low (Bank 1)
|
—
|
P2011
|
Intake
Manifold Runner Control Circuit / Open (Bank 2)
|
—
|
P2012
|
Intake
Manifold Runner Control Circuit Low (Bank 2)
|
—
|
P2016
|
Intake
Manifold Runner Position Sensor / Switch Circuit Low (Bank1)
|
—
|
P2017
|
Intake
Manifold Runner Position Sensor / Switch Circuit High (Bank1)
|
—
|
P2021
|
Intake
Manifold Runner Position Sensor / Switch Circuit Low (Bank 2)
|
—
|
P2022
|
Intake
Manifold Runner Position Sensor / Switch Circuit High (Bank 2)
|
—
|
P2227
|
Barometric
Pressure Circuit Range/performance
|
—
|
P2228
|
Barometric
Pressure Circuit Low Input
|
—
|
P2229
|
Barometric
Pressure Circuit High Input
|
—
|
PREPARATION FOR THE INSPECTION MODE |
Make sure that the fuel remains approx. half amount [20 — 40 litres (5.3 — 10.6 US gal, 4.4 — 8.8 Imp gal)] and the battery voltage is 12 V or more.
Raise the vehicle using a garage jack and place on rigid racks or drive the vehicle onto free rollers.
Vehicle Diagnostic Interface |
Warm up the engine.
Prepare the Vehicle Diagnostic Interface kit.

Connect the diagnosis cable to Vehicle Diagnostic Interface.
Connect the test mode connector (A) at the lower portion of instrument panel (on the driver’s side).
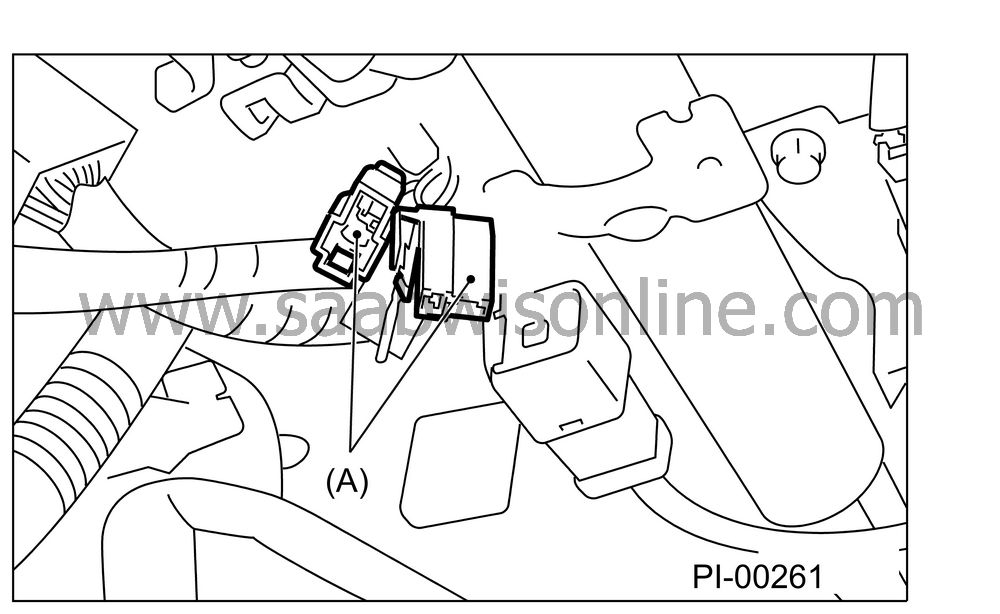
(A)
|
Test mode
connector
|
Connect the Vehicle Diagnostic Interface to data link connector located in the lower portion of the instrument panel (on the driver’s side).
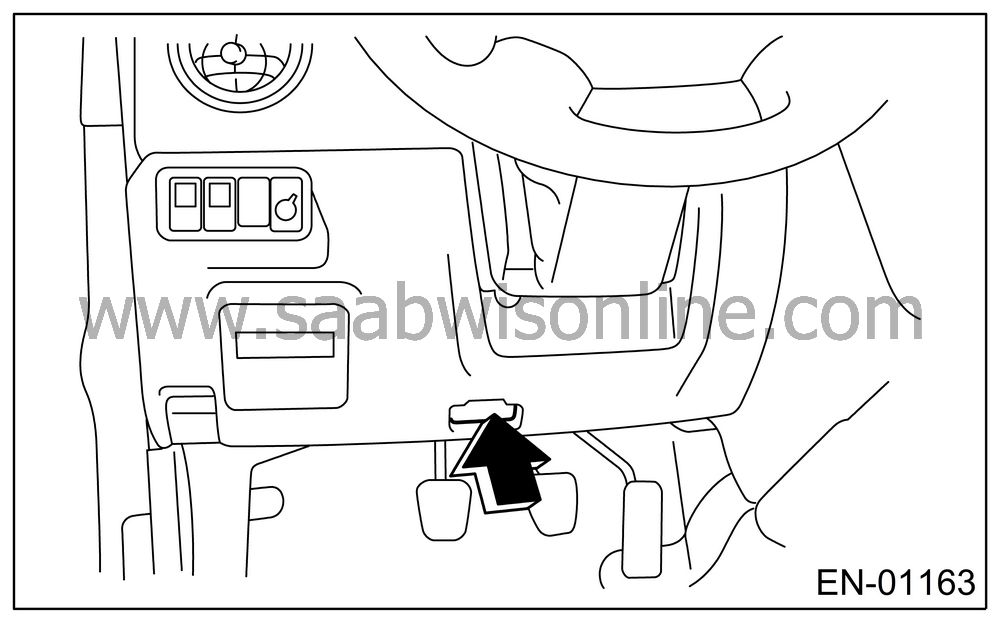
Important | ||
Do not connect the scan tools except for Vehicle Diagnostic Interface and OBD-II general scan tool. |
||
Turn the ignition switch to ON (engine OFF), and start the Vehicle Diagnostic Interface.
On the «Main Menu» display screen, select the {2. Each System Check}.
On the «System Selection Menu» display screen, select the {Engine Control System}.
Select the {OK} after the information of engine type is displayed.
On the «Engine Diagnosis» display screen, select the {Dealer Check Mode Procedure}.
After the “Perform Inspection (Dealer Check) Mode?” is shown on the display screen, select the {OK}.
Perform subsequent procedures as instructed on the display screen.
• |
If trouble
still remains in the memory, the corresponding DTC appears on the
display screen.
|
OBD-II GENERAL SCAN TOOL |
Warm up the engine.
Connect the test mode connector (A) at the lower side of instrument panel (on the driver’s side).
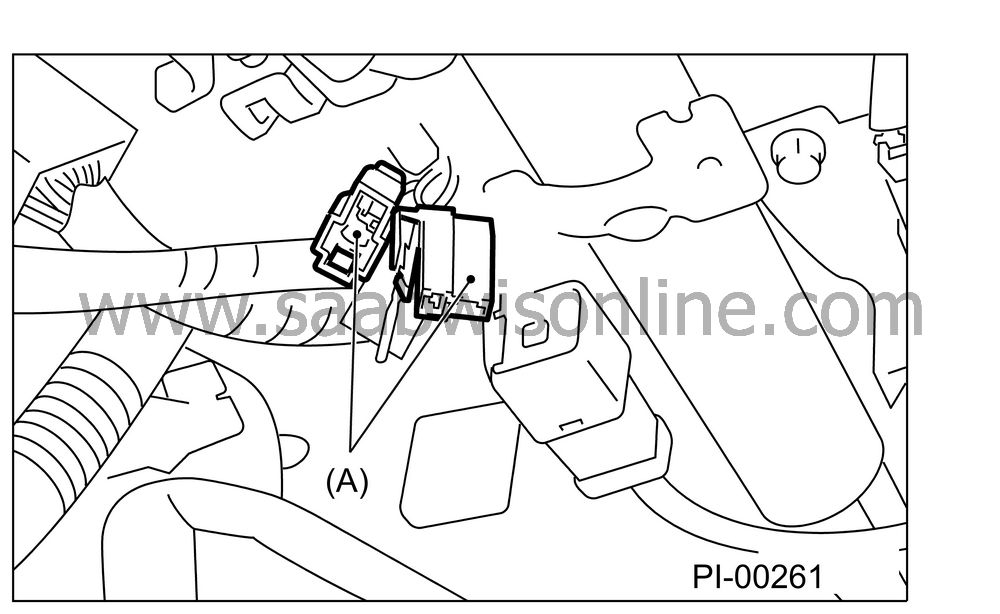
Connect the OBD-II general scan tool to its data link connector in the lower portion of instrument panel (on the driver’s side).
Important | ||
Do not connect the scan tools except for Vehicle Diagnostic Interface and OBD-II general scan tool. |
||
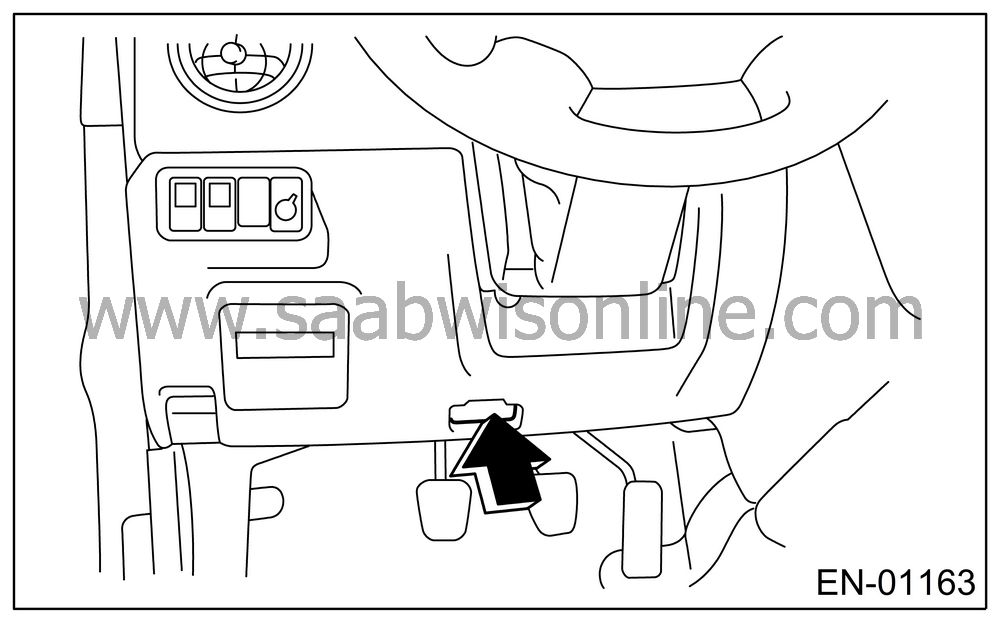
Start the engine.
Note | ||
• |
Ensure the select lever is placed in “P” range
before starting. (AT model)
|
|
• |
Depress the clutch pedal when starting engine. (MT model)
|
Using the select lever or shift lever, turn the “P” position switch and “N” position switch to ON.
Depress the brake pedal to turn brake switch ON. (AT model)
Keep the engine speed in 2,500 — 3,000 rpm range for 40 seconds.
Place the select lever or shift lever in “D” range (AT model) or “1st” gear (MT model) and drive the vehicle at 5 to 10 km/h (3 to 6 MPH).
Note | ||
• |
On AWD model, release the parking brake.
|
|
• |
The speed difference between front and rear wheels may
light ABS warning light, but this indicates no malfunctions. When
the engine control diagnosis is finished, perform the ABS memory clearance
procedure of self-diagnosis system.
|
Using the OBD-II general scan tool, check for DTC and record the result(s).
Note | ||
• |
For detailed operation procedures, refer to the OBD-II
General Scan Tool Instruction Manual.
|
|
• |
For detailed concerning DTC, refer to the List of Diagnostic
Trouble Code (DTC).
|