Boost pressure control
Boost pressure control |
- |
Desired value calculation
|
- |
Calculation of the current boost pressure and atmospheric pressure
|
- |
Boost pressure control
|
Desired value calculation |
The desired value calculation uses the parameters
- |
Engine speed
|
- |
Desired fuel quantity
|
- |
Atmospheric pressure from the boost pressure calculation
|
To determine the desired value for the boost pressure, a value is taken from a file that is dependent on the engine speed and the injected fuel quantity. This value is corrected for air pressure.
Calculation of the current boost pressure and atmospheric pressure |
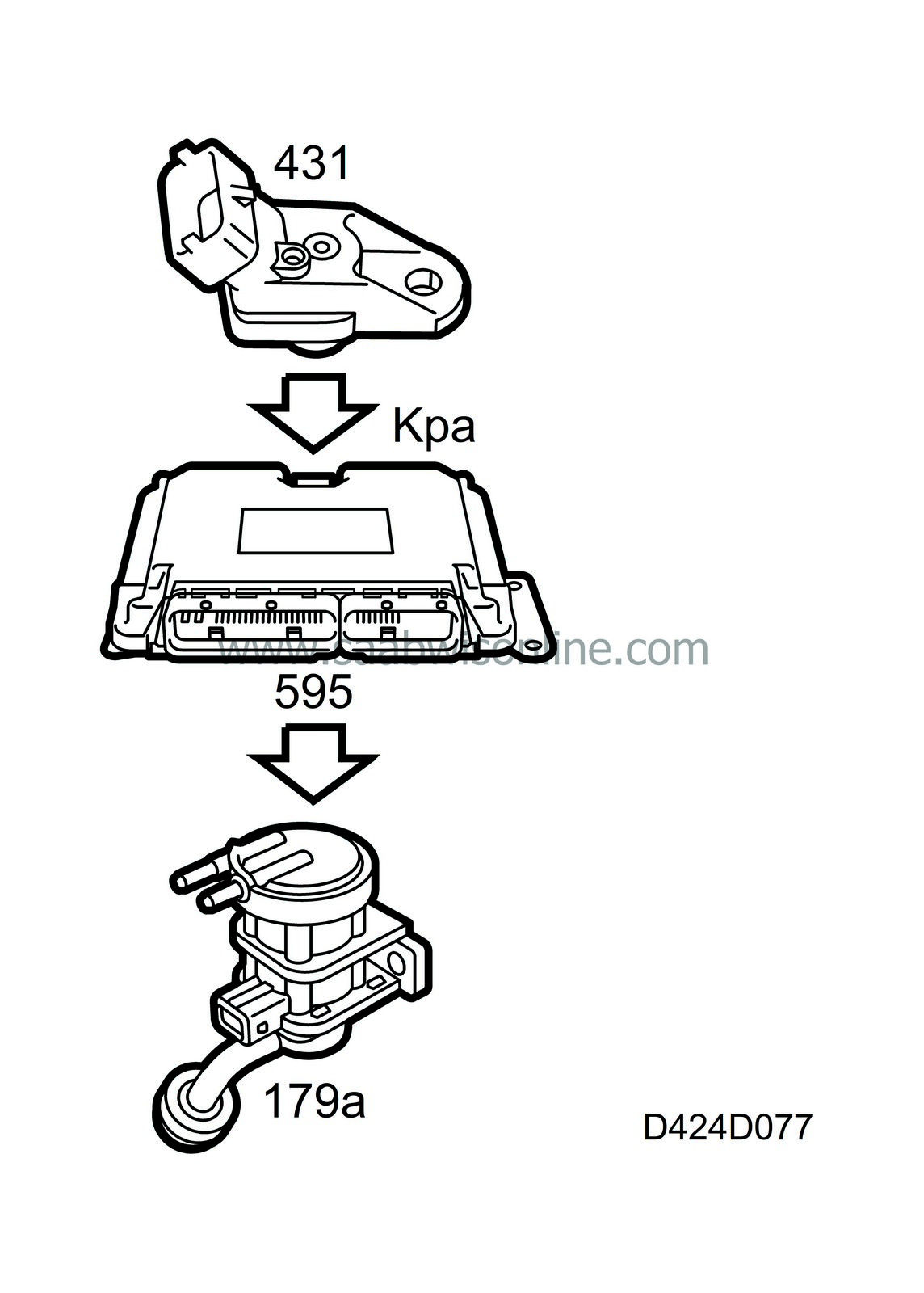
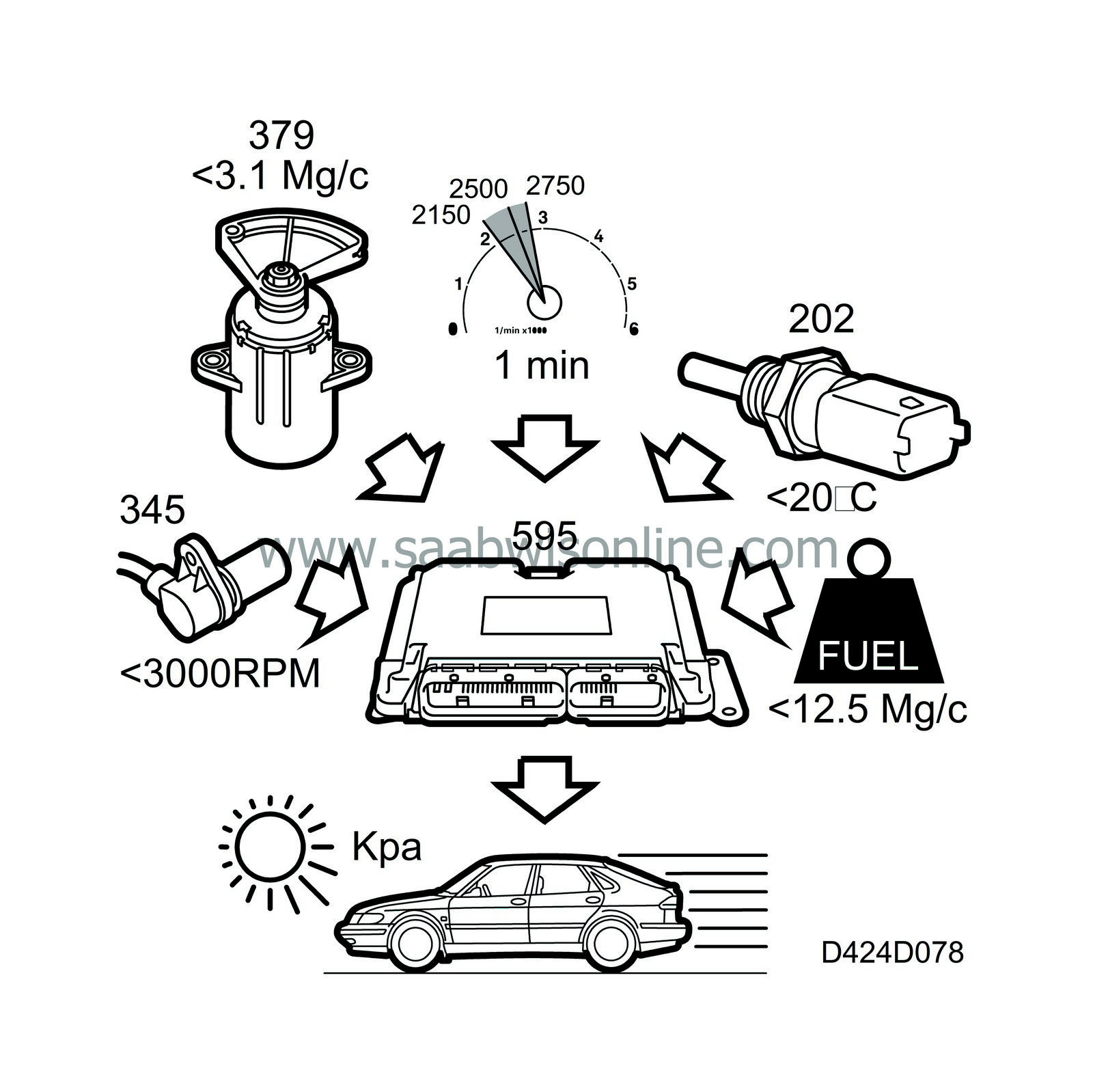
The boost pressure is retrieved from the manifold absolute pressure sensor (431) in the intake manifold and filtered before being passed on to the control module.
The atmospheric pressure is calculated with the manifold absolute pressure sensor (431) in the intake manifold. This is possible only if the following conditions have been fulfilled for longer than 2.5 seconds.
- |
The engine speed is below 3000 rpm
|
- |
The desired fuel quantity is less than 3.1 mg/combustion
|
- |
The change in engine speed is between -350 rpm and +250 rpm per minute
|
- |
The engine coolant temperature is below 20°C
or The injected fuel quantity is less than 12.5 mg/combustion |
Under these driving conditions, the current pressure in the intake manifold is taken to a correction list, where the reading from the intake manifold is compensated for the engine speed that applied when the reading was taken. After engine speed correction, the value is taken to be the atmospheric pressure.
If the calculation cannot be performed due to the above conditions, the result of the latest calculation is used instead.
Barometric pressure is measured when the ignition is turned to ON and also while the starter motor is cranking until the engine starts.
Boost pressure control |
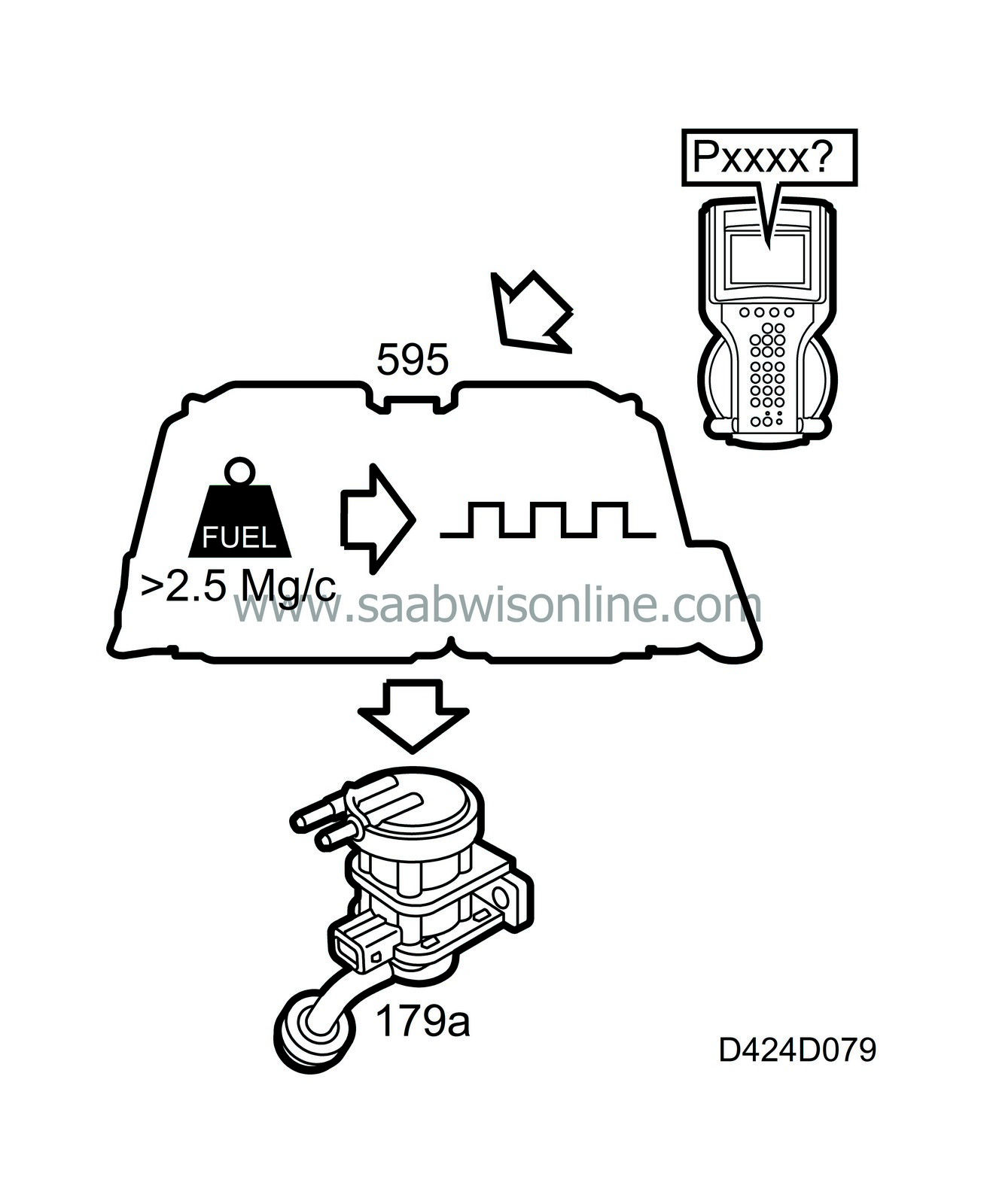
The timing ratio is regulated when the following conditions are met:
- |
No system faults (DTC)
|
- |
Injected fuel quantity exceeds 2.5 mg/combustion
|
The desired boost pressure value is converted to a timing ratio using pre-programmed tables. The timing ratio is then conveyed to the final stage control, where the signal is amplified and compensated for the battery voltage, see table.
Voltage (V)
|
Compensation value
|
9
|
1.4
|
14.2
|
1.0
|
16
|
0.775
|
This is done to compensate for a higher or lower voltage than 14.2 V resulting in a different valve lift and consequently an incorrect control of the valve.
The timing ratio is then available on the control module pin to be connected to the control valve for the turbocharger wastegate.