Brief description
Brief description |
The soft top on the Saab 9-3 convertible is raised and lowered with a hydraulic unit and five hydraulic cylinders that are operated with a switch in the centre console. The hydraulic unit and the cylinders are regulated by the STCS (Soft Top Control System).
The STC control module knows the position of the soft top and its components through information it receives from a number of microswitches and switches, which in some cases are built into the hydraulic cylinders. This means that the movement is sequential, which means that each movement must be completed before the next one can be started. The STC control module that controls the valves and the fifth bow lock motor must receive confirmation of the movement from the microswitches and switches within a certain time period. If this confirmation is not received, the movement will cease and the STC control module generates a diagnostic trouble code as well as it sends a bus message to SID that will show, for example, “CHECK SOFT TOP”.
The hydraulic unit, located in the torsion box behind the rear seat, has an integrated electric pump and a valve housing as well as two relays. The motor rotational direction can be reversed through the two relays that are controlled from the STC control module and their poles are reversed. In this way, the pump can either push or pull the soft top cylinder which lacks hydraulic valves for operation. The motor is protected against overheating through an overheating protection.
The valve block contains the hydraulic valves, whose task it is to control the flow of hydraulic oil to the hydraulic cylinders. The valve has two positions, active and at rest, and three oil connections, oil pressure delivery from the pump, oil pressure outlet to the cylinder and return to the reservoir.
There are four hydraulic cylinders for the operation of the soft top, two for the main sequence and two for the fifth bow which is located on the soft top mechanism. The hydraulic cylinders located on the left side of the soft top mechanism each have two integrated end position switches. These switches feed information to the STC control module when the hydraulic cylinders have reached their respective top and bottom end positions.
The hydraulic cylinder that operates the soft top cover is located together with the soft top cover drive mechanism in the boot. The hydraulic cylinder has an integrated end position switch which indicates when the soft top cover has reached its top position, that is “open”. When the soft top cover has reached its bottom position, “closed”, two microswitches in the soft top cover latch feeds information to the STC control module that the soft top cover is closed.
In addition to the mentioned switches and microswitches, there are another three microswitches and two switches.
Movement of the fifth bow is confirmed by an intermediate position sensor located on the left side of the soft top mechanism. It informs the STC control module that the fifth bow has reached its centre position.
To operate the soft top to its lowered position, the soft top storage in the luggage compartment must be lowered. There are two microswitches that confirm to the STC control module that the soft top storage is in its correct position.
In the windscreen member lock fitting, there is a reed switch sensitive to magnetic fields. At each one of the first bow latch hooks, there is a small permanent magnet that affects the reed switch when the first bow is very near the windscreen member. When the first bow is locked, the STC control module receives confirmation from the two reed elements.
There are four relays that control the window lifts and a relay that controls the fifth bow lock motor. The relays are located in a relay holder on each side behind the rear side upholstery. The window relays have three positions, inactive, active window up, active window down. The fifth bow relay also has three positions, inactive, fifth bow locked or fifth bow unlocked.
Together with the relays for the window lifts and the fifth bow latch motor, the four hydraulic valves are connected to a common communication bus called the VR (Valve Relay) bus. The STC control module sends an addressed message on the VR bus that can be used only by the unit for which it was intended. The valves or relays can then be set to active or at rest.
After the ignition has been turned off, the valves resume resting positions. If work is done with the soft top in the half open position, always use the special tool that keeps the soft top open. If the soft top is operated and stops during the movement (for example, ROOF switch is released), the valves will assume resting position after 20 seconds and the soft top will fall down.
|
The soft top mechanism comprises two parallel metal rails running along the side of the top. These are divided into three parts, a front rail integrated with the first bow, a middle rail and a rear rail. The three rails are hinged to each other. When the top is put down, the mechanism folds at the hinges and at the main pivot point where the soft top mechanism is fitted to the body.
Between the right and left rails there are five transverse bows. The bows are numbered from one to five, with number one at the front.
When the top is up, it is locked to both sides of the windscreen member with swivelling lock hooks that are operated with a latch handle in the middle of the first bow. The fifth bow of the top is locked to the soft top cover with two securing plates.
The soft top has an outer roof and headlining which are fastened to the soft top mechanism and the rear window frame.
The soft top cover acts as a lid on the lowered top and also as a seal on the fifth bow when the top is up. Its two front corners are locked with two locking mechanisms located on the inner side plates.
The soft top storage into which the top is lowered is located between the rear seat and the luggage compartment and also acts as a drain sheet to drain off any water from the top through drain holes in the sills. With the top up, the storage can suspended to increase the volume in the luggage compartment.
To enable the top to be raised (closed) even when there is a malfunction in the system, there is an emergency operation function built into the soft top system.
A valve is located on the hydraulic unit and when it is opened, the pressure is released from the soft top cover hydraulic cylinder. To unlock the soft top cover, you must use the wheel bolt tool (in the car tool kit) to crank the soft top cover drive mechanism so that the locks release. Then you can open the soft top cover and open the soft top by hand.
|
P-bus and I-bus |
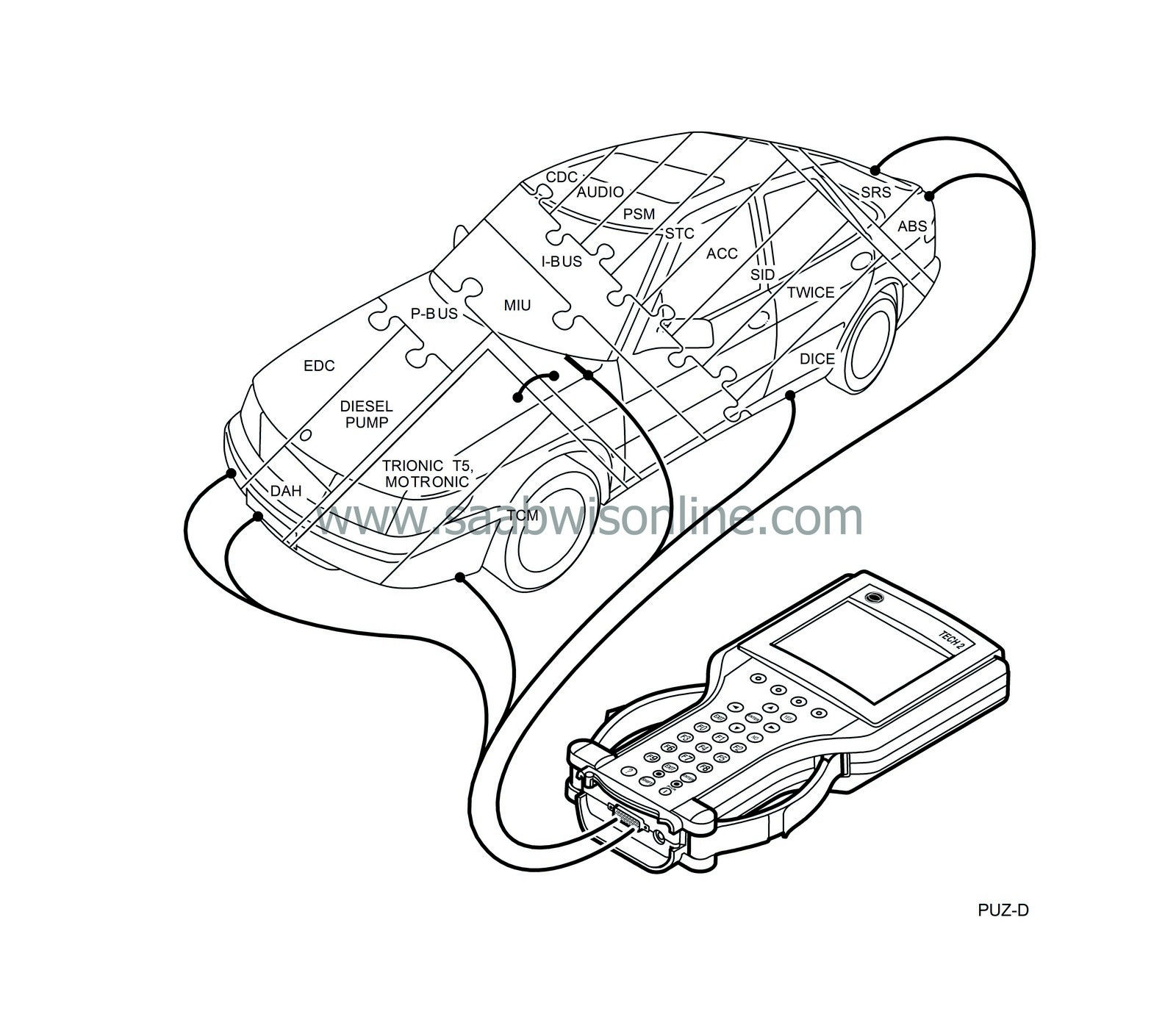
The two power train systems EDC and diesel pump are not connected to the I-bus, however. These systems require much faster communication to eliminate noticeable delays, e.g. when EDC requests a certain amount of fuel for injection.
Therefore, they are connected through a separate buss called the P-bus (Powertrain Bus). The P-bus has a data transfer rate ten times higher than that of the I-bus.
The P-bus is also connected to the MIU (Main Instrument Unit). The MIU ensures that the information that is available on one bus is also available on the other.