Brief description
Brief description |
The engine management system EDC 15 with diesel pump VP44 is a fuel management system for diesel engines with the main task of supplying the correct amount of diesel fuel to the combustion chamber at the correct point in time.
When the driver presses the accelerator pedal, a wire is stretched and affects a pedal position sensor. The pedal position sensor is read by the engine control module, which then becomes aware of the magnitude of the power output desired by the driver. The amount of fuel injected controls the power output of the engine and it is up to the control module to convert the desired power output from the driver or cruise control into the amount of fuel injected per combustion.
The control module calculates the optimum injection amount per combustion for all driving conditions based on emissions, engine strength, driveability and fuel consumption.
The EDC 15 diesel injection system with VP44 diesel pump is manufactured by Robert Bosch GmbH.
EDC 15 with diesel pump VP44 has the following advantages compared with older diesel injection systems:
• |
It is possible to control the injected amount of fuel individually for each cylinder.
|
• |
The system compensates for mechanical wear in the drive between the diesel pump and the crankshaft. Consequently, the correct moment for pressure build-up in the diesel pump is ensured during the whole service life of the engine.
|
• |
Load compensation is possible throughout the whole load and engine speed range.
|
• |
Efficient torque limitation when required.
|
• |
Cruise control easily integrated.
|
Control module, EDC 15 (595) |
The engine control module detects the request from the driver and calculates the permitted fuel quantity in mg/combustion with the help of sensors and information from the P bus.
It reads the digital information from the cruise control switch and, if requested by the driver, controls the speed of the car.
The control module sends a request on the P bus for a certain injected fuel quantity per combustion and a request for when this fuel quantity should be injected into the combustion chamber.
Diesel pump (598) |
The diesel pump reads the information on the P bus and governs the injected fuel quantity per combustion and starting time for pressure build-up in the high-pressure pump electro-hydraulically. The integral feed pump sucks fuel from the tank through the fuel filter to the diesel pump.
The pump has internal diagnostics, the result of which is sent on the P bus to the engine control module where any diagnostic trouble codes can be read.
Accelerator pedal position sensor (379) |
The accelerator cable turns a potentiometer, which informs the engine control module of the power output requested by the driver.
Coolant temperature sensor, engine management system (202) |
The temperature sensor informs the engine control module of the temperature of the engine. This information is used amongst other things to supply the engine with extra fuel during cold starting. It can also protect the engine against harmful overheating, as the control module limits the fuel quantity when there is risk of overheating.
Engine oil temperature sensor (559) |
The temperature sensor informs the engine control module of the temperature of the engine oil. This information can also be used to carry out a feasibility diagnosis on the engine coolant temperature sensor. It can also protect the engine against harmful overheating, as the control module limits the fuel quantity when there is risk of overheating.
Mass air flow sensor (205) |
The mass air flow sensor sends a voltage modulated signal about the mass air flow to the engine control module. The control module calculates the intake air mass per combustion based on the mass air flow.
Intake air temperature sensor (407) |
The temperature sensor informs the engine control module of the intake air temperature. The information is also used as a blocking condition during diagnosis functions.
Crankshaft position sensor (345) |
The position sensor sends a crankshaft-speed dependent alternating current to the control module. Each pulse is used to determine when the engine has reached top dead centre.
Manifold absolute pressure sensor (431) |
The pressure sensor informs the engine control module of the pressure in the intake manifold. This information is used to control the boost pressure in the turbocharger.
Control module, glow plugs (596) |
The control module supplies power to the glow plugs on request from the engine control module. It also reduces the power to the glow plugs when the engine has started. The glow plug control module has internal diagnostics, the result of which is sent through a lead to the engine control module where any diagnostic trouble codes can be read.
Cruise control switch (141) |
The driver can request that the engine control module retain the set vehicle speed or, alternatively, reduce or increase the set vehicle speed.
Clutch switch, cruise control (133) |
The switch informs the engine control module of the position of the clutch pedal. It is used to turn off the cruise control.
Brake switch, cruise control (134) |
The switch is used to carry out a feasibility assessment of the brake light switch.
Brake light switch (29) |
The switch informs the engine control module of the position of the brake pedal. It is used to turn off the cruise control.
Main relay, engine management system (229) |
The relay controls the power supply to the diesel control system.
Relay, A/C compressor (156) |
The relay turns the A/C compressor on and off after receiving a command from the engine control module.
Control valve, charge air (179a) |
The control valve controls the boost pressure with a vacuum from the vacuum pump.
Control valve, exhaust gas recirculation (404) |
The control valve controls the EGR valve with a vacuum from the vacuum pump.
Control valve, swirl throttle (403) |
The control valve controls the swirl throttle with vacuum from the vacuum pump.
P bus and I bus |
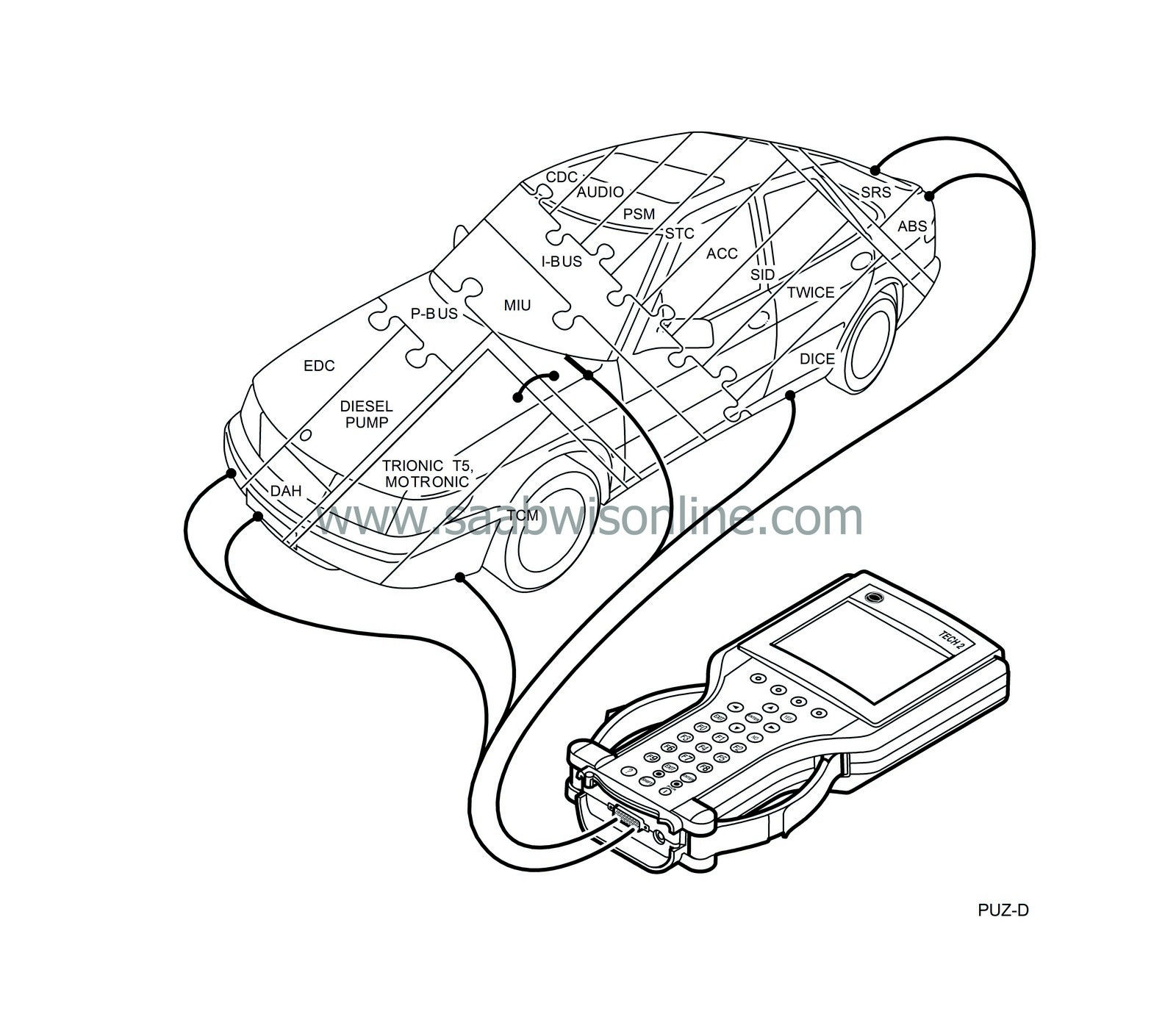
The two power-train systems, EDC and the diesel pump, are however not connected to the I bus. These systems require considerably faster communication so that no delays are noticeable, e.g. when EDC requests a certain fuel mass for injection.
Therefore, they are connected to a separate bus called the P bus (Power-train Bus). The data transfer rate on the P bus is ten times greater than that of the I bus.
The P bus is also connected to the MIU (Main Instrument Unit). The MIU is responsible for ensuring that information which is available on one of the buses is also made available on the other bus.