Description of operation, diesel engine
Description of operation, diesel engine |
The basic engine under the cylinder head is principally similar to a petrol engine. The difference is mainly in the dimensioning of the engine block and the crank section.
Combustion process, petrol engine |
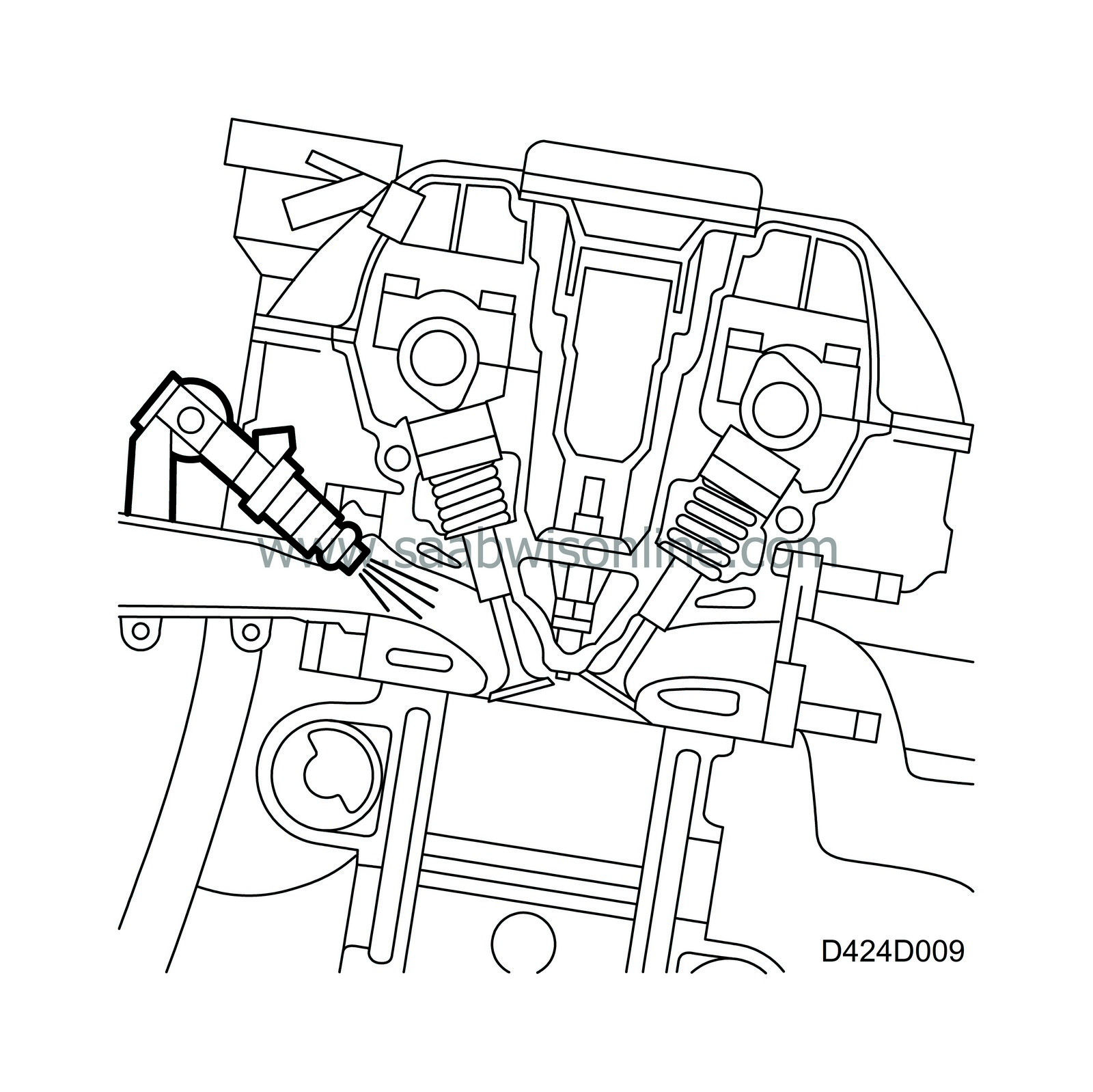
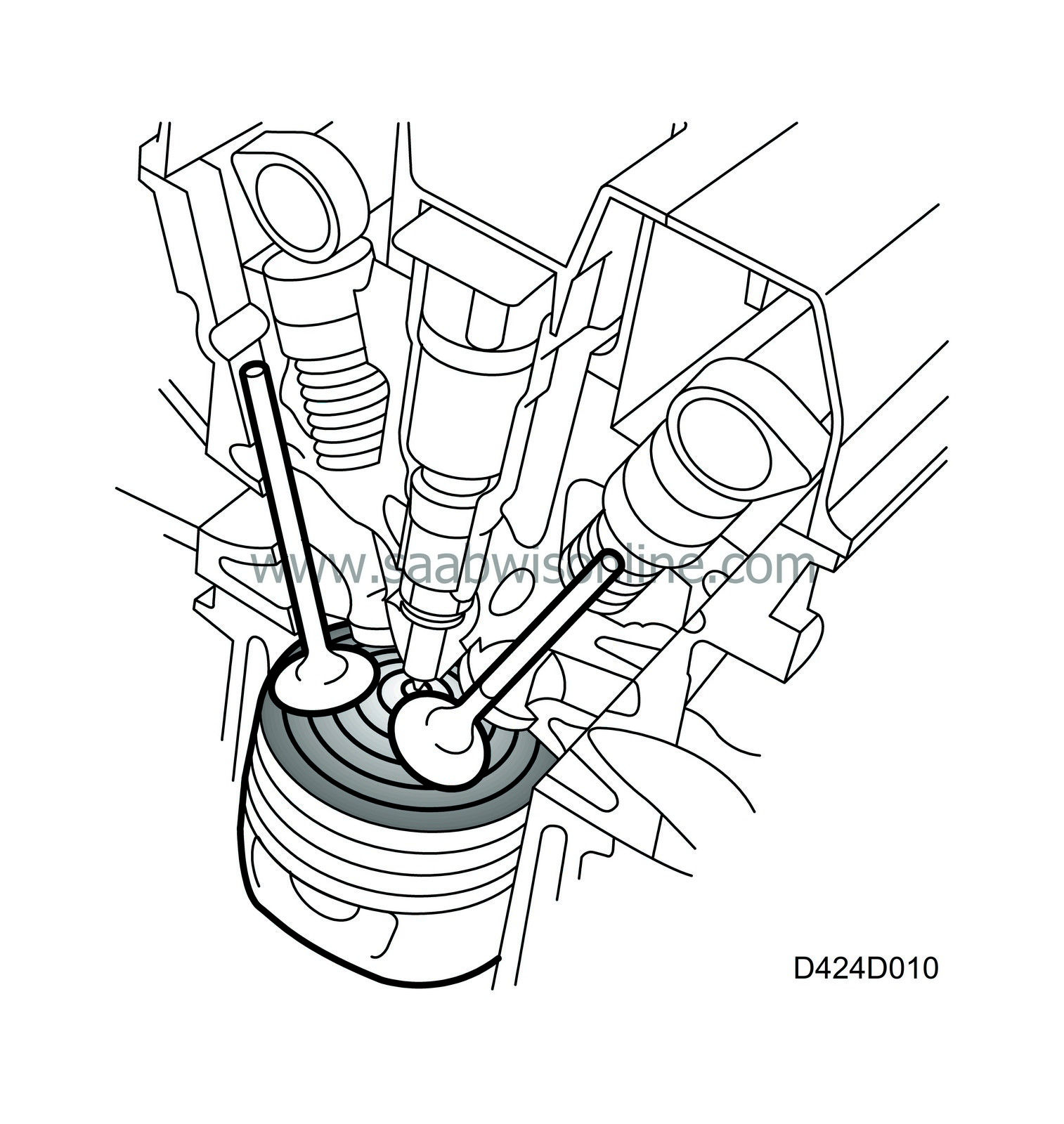
In petrol engines, the fuel/air mixture in the combustion chamber is mixed in advanced, i.e. the fuel and air are equally distributed in the mixture that is drawn into the combustion chamber.
A spark that occurs at just the right moment starts the combustion process in the compressed fuel/air mixture and the resulting flame front moves at an even speed through the combustion chamber.
The resultant increase in pressure is kept even and controlled and the maximum pressure is relatively low during the combustion process compared with that in a diesel engine.
Combustion process, diesel engine |
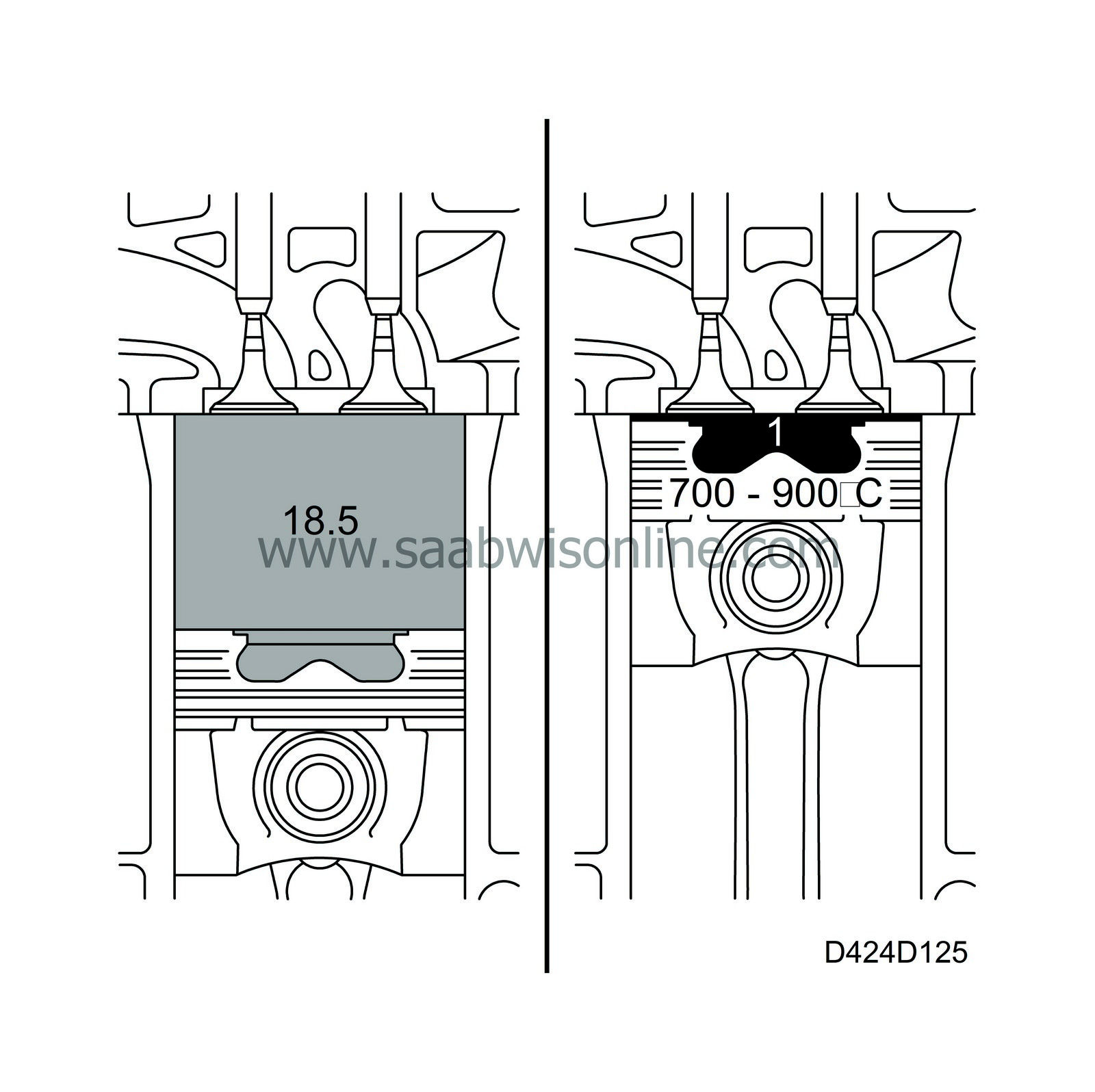
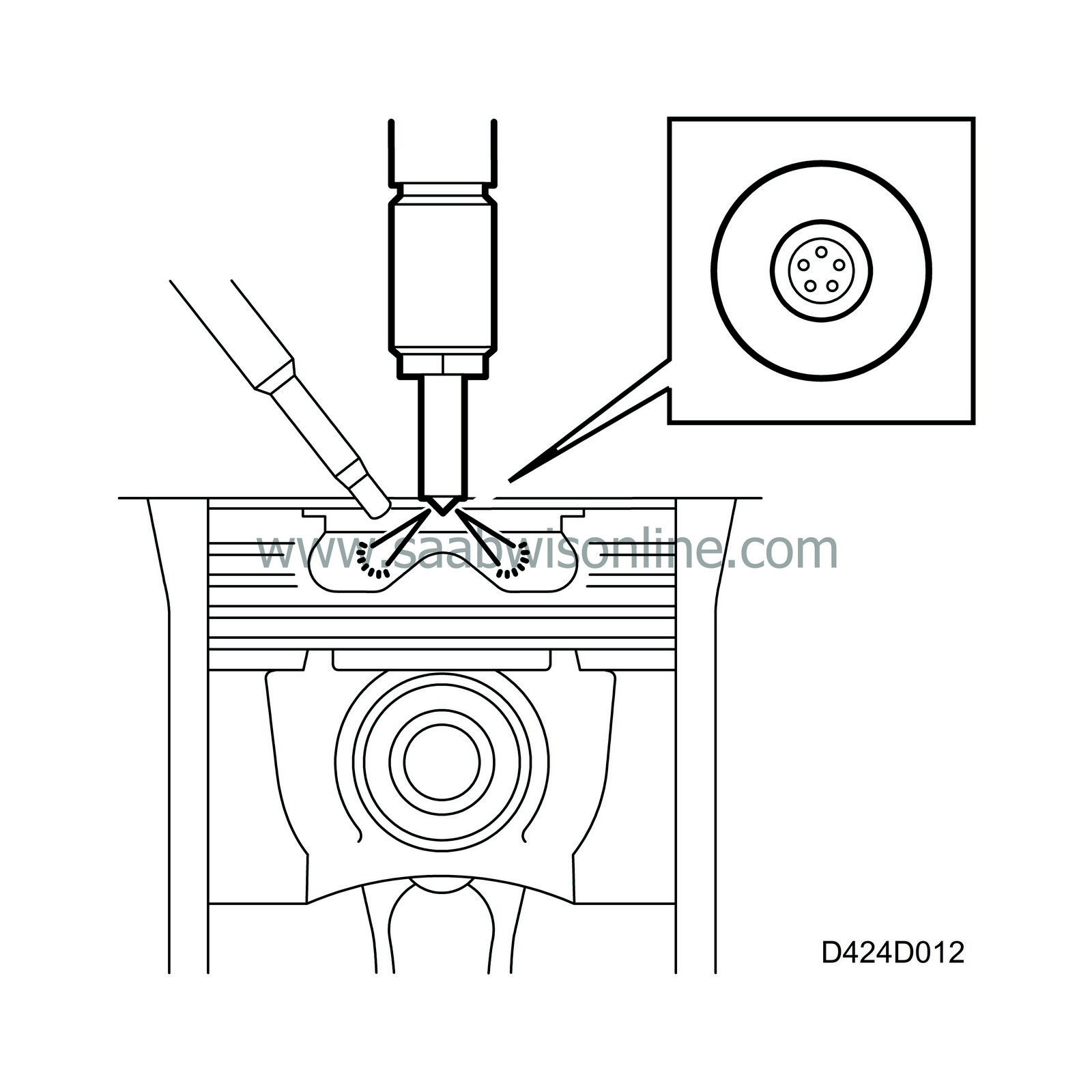
The combustion process in a diesel engine takes place according to another principle than that in a petrol engine, the engine draws in only pure air, which is then substantially compressed. The temperature at the end of the compression stroke is between 700-900°C (1292-1652°F). The fuel is injected into this extremely hot air in the combustion chamber, which is a dished area in the top of the piston. The moment for the start of the injection is very accurately selected to meet with exhaust emission values and so that the engine's thermal and mechanical strength is not put at risk.
In reality, combustion is an extremely fast process but if we slow it down we can see the following happening when the fuel is injected:
When the fuel pressure has risen so much that the needle starts to lift from its seat, the fuel starts to flow into the combustion chamber. This is called injection start.
Here, the fuel meets the warm compressed air and the foremost particles of fuel in the five jets from the nozzle meet air that is so hot that the fuel is heated to a temperature exceeding its flash point. The ignitability of diesel fuel is specified with a cetane number.
The time it takes for the fuel to be heated sufficiently for it to ignite is called the ignition lag and depends on a number of factors such as fuel quality, engine temperature, if the engine is worn, etc. There is always a certain ignition lag in a diesel engine, which results in there always being a greater or less amount of fuel outside the nozzle in the combustion chamber when combustion starts.
As combustion starts, the pressure increase takes place very quickly as all the fuel outside the nozzle is ignited almost simultaneously. It is at this stage, especially during cold starting, that the characteristic diesel knock occurs. The shorter the ignition lag, the lower the diesel knock. This means that everything that can be done to shorten the ignition lag will reduce the level of noise.
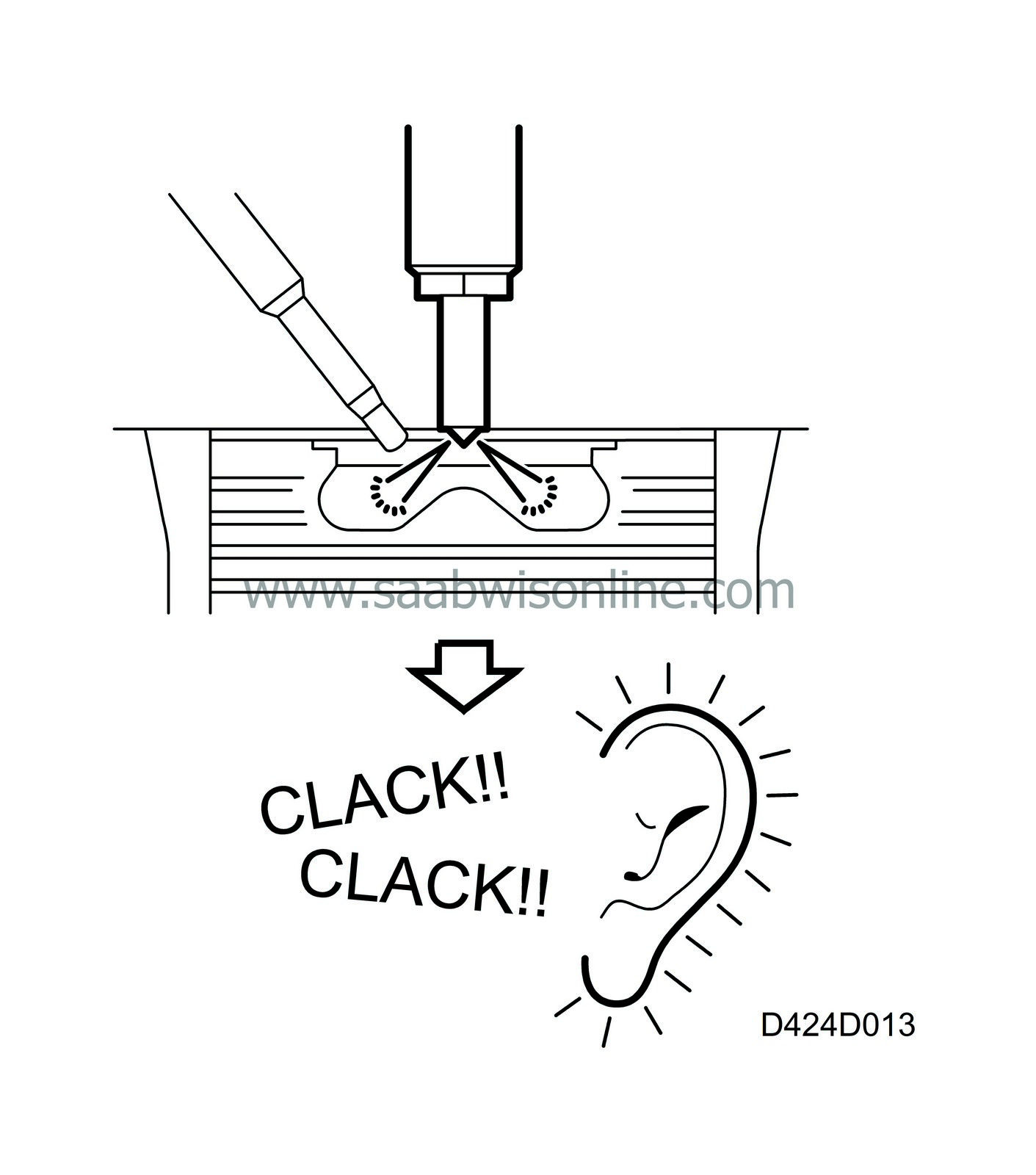
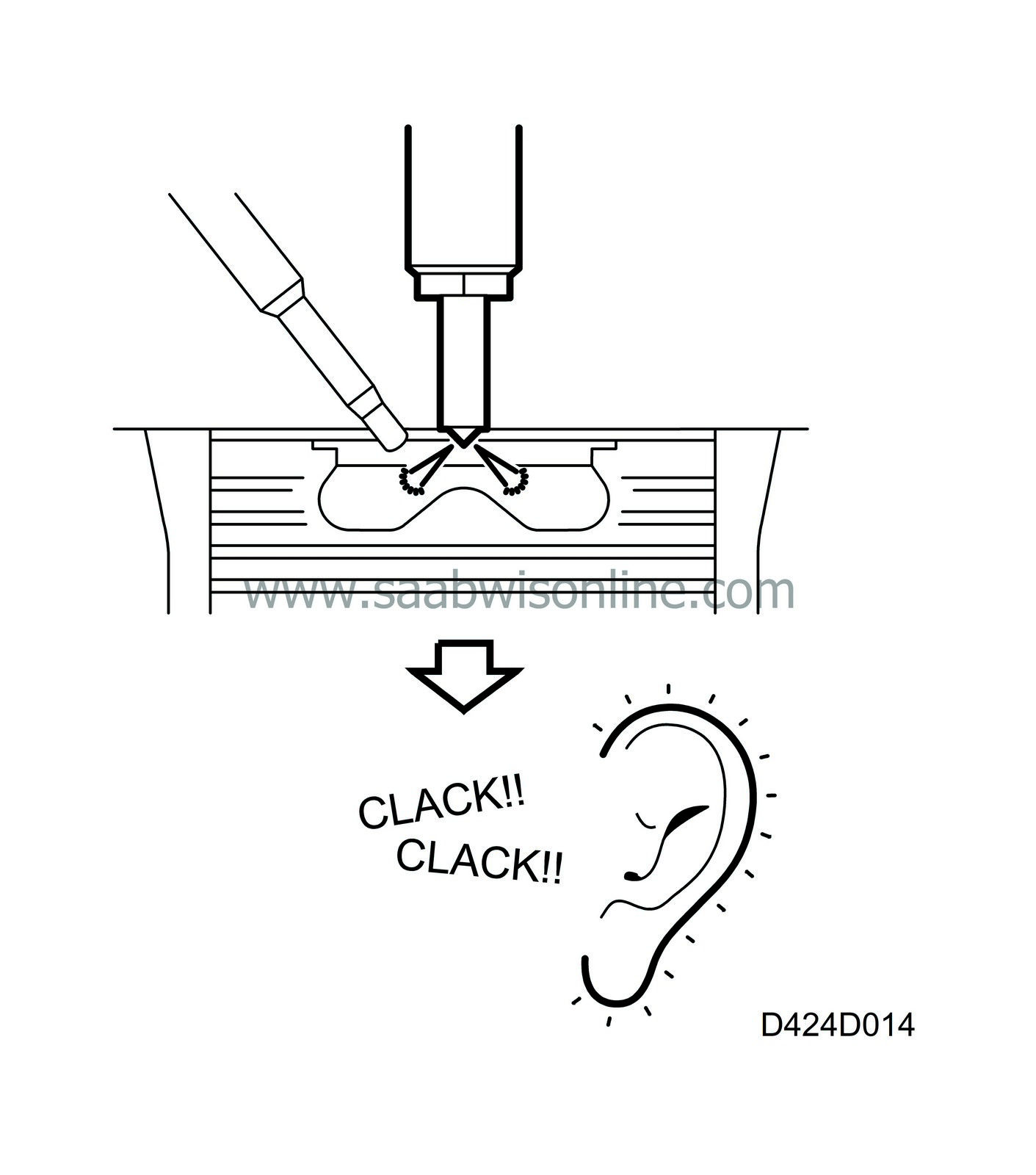
As the following fuel is injected into the combustion chamber, combustion will continue at the extremes of the fuel jets where the fuel only ignites between Lambda 0.3-1.5. The fuel is exposed to fresh air thanks to a powerful swirl forming in the combustion air so that combustion of all the fuel is complete. A large excess of air must be present in the combustion chamber compared with the theoretically sufficient ratio 14.7:1 for this method of combustion to work. A direct injection diesel engine normally works with an excess of at least 30%. With light loads, the excess of air can be considerably higher (close to 400%).
One great advantage of this method is that the exhaust gas temperature remains low, as the excess air cools the exhaust gases. There are only slight losses in the pump due to there not being an air throttle to hinder the flow of air through the engine.
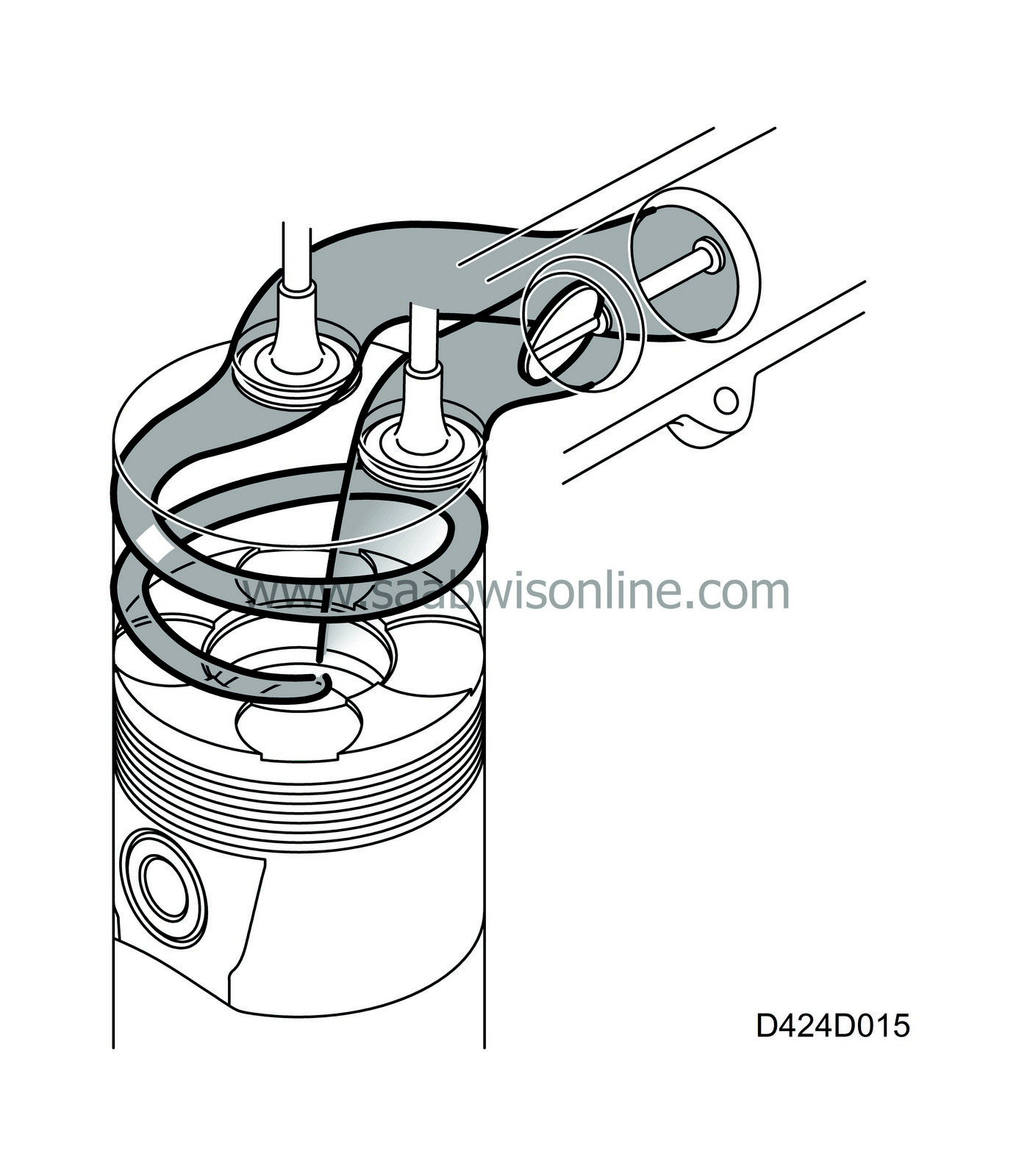
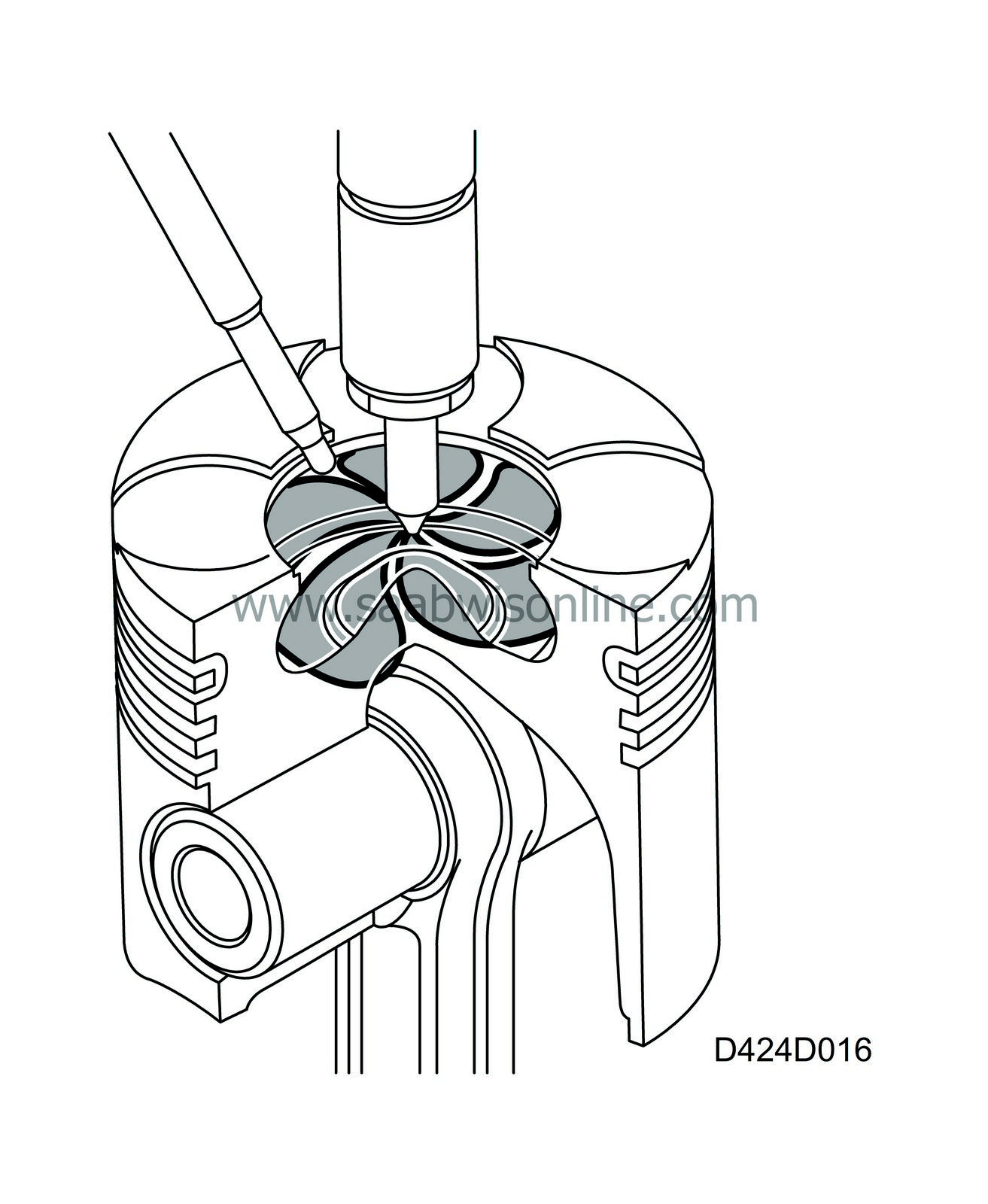
To obtain optimum combustion, the fuel must be as finely atomized as possible when it is injected into the combustion chamber. This means that the fuel pressure in the nozzle must be very high. The diesel pump creates this pressure (1000 bar) and distributes the fuel to the cylinder that is next in turn to ignite.
At such high pressure, diesel fuel does not behave according to the laws that normally apply to hydraulics but to acoustic laws instead. When the pump starts building up pressure, a pressure wave forms in the jet pipe that moves at the speed sound through the diesel fuel (1480 m/s) to the nozzle. When the pressure wave arrives, the nozzle opens (injection start). Thanks to acoustic laws being applied, it is possible to adapt the jet pipe and other injector components so that the pressure is amplified at the nozzle end of the jet pipe. Pressure amplification makes it possible to reach a nozzle pressure of approx. 1800 bar.
When the control module determines the required injection start, the difference in the start of pressure build-up and the injection start is taken into account.
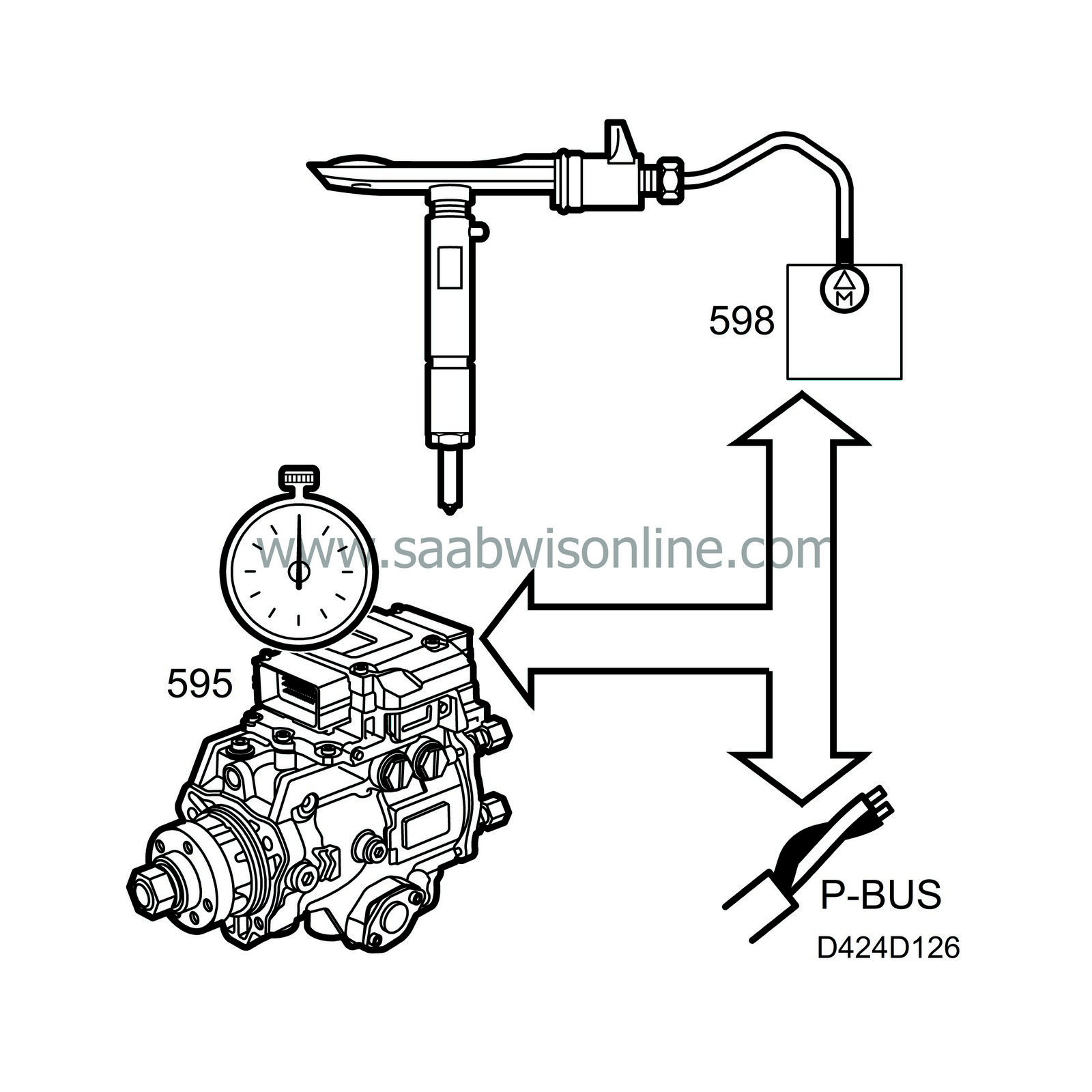
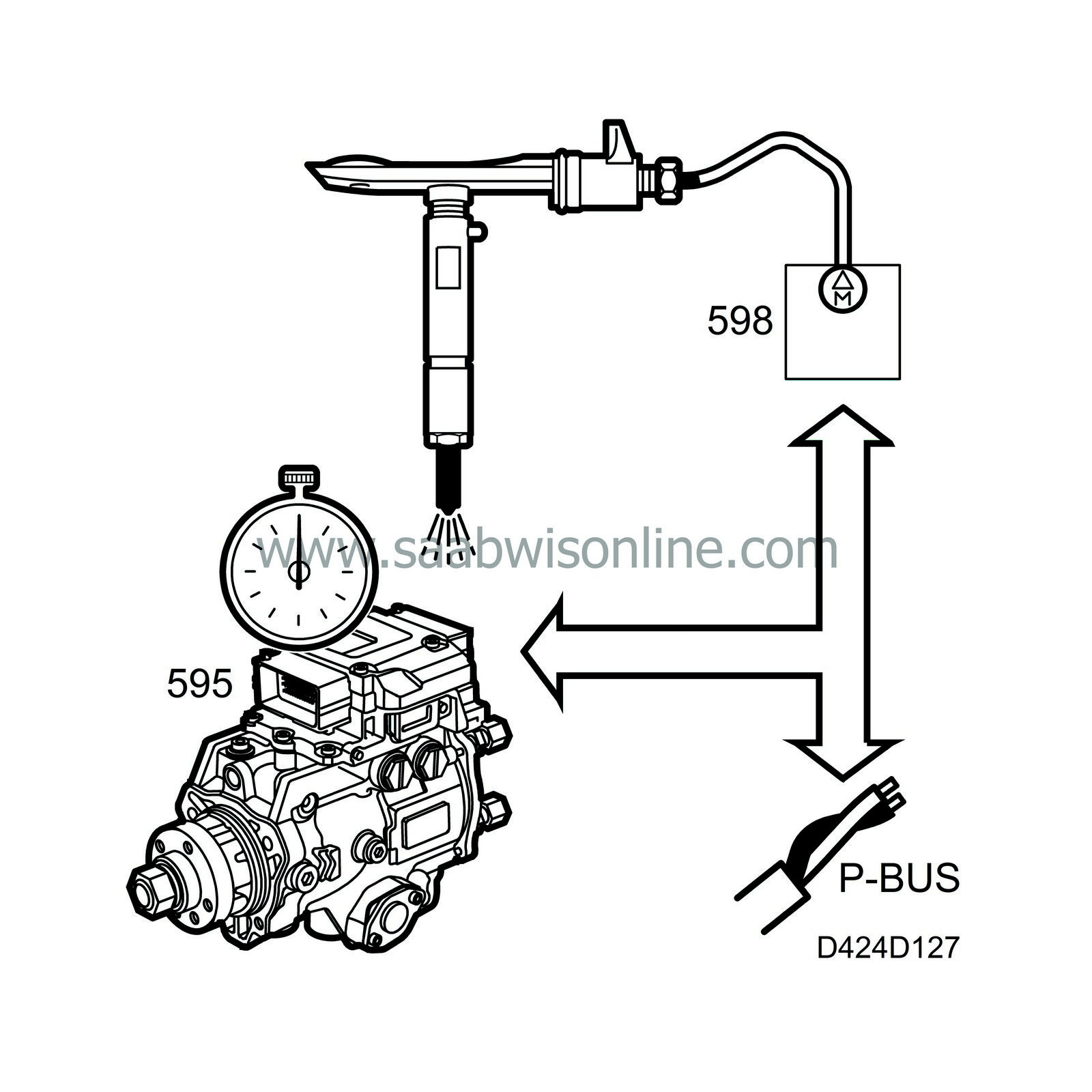