Brake function, Viggen
Brake function, Viggen |
The master cylinder and other hydraulic components are filled with brake fluid under zero pressure.
The inlet and outlet valves in the valve block are in the rest position, i.e. the inlet valves are open and the outlet valves closed.
Braking without ABS modulation |
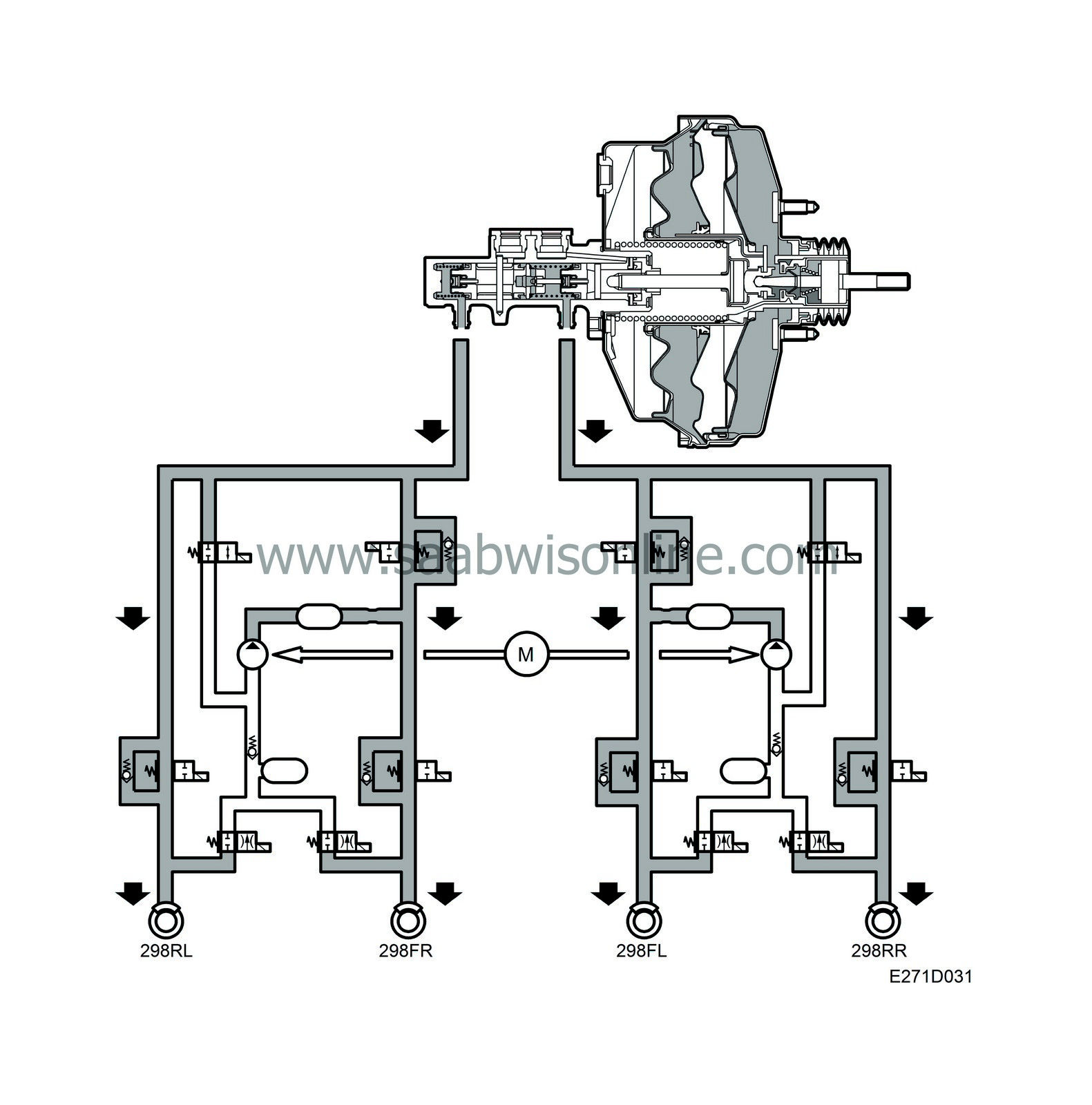
When the brake pedal is depressed, the vacuum passage is closed and the air passage remains constantly open. The greatest possible pressure difference now acts on the diaphragm and full servo assistance is obtained in the brake system.
The central valve for the primary plunger closes the return passage to the brake-fluid reservoir, and the pressure increases ahead of the plunger. The same pressure also acts on the secondary plunger, pressing it forwards and closing the its central valve.
In the hydraulic unit, the inlet valve is open and the outlet valve closed.
The hydraulic pressure in both brake circuits rises and, since the plungers have the same diameter, the pressure will be the same in both circuits in the valve block.
The pressure is propagated throughout the brake system and acts on the brake piston in each caliper. The brake pistons press the brake pads against the brake discs. When the brake pedal is released, the pistons in the master cylinder are retracted to the rest position and the central valves in the primary and secondary circuits are opened. The pressure is released and the piston in each wheel cylinder is returned to its rest position by means of the piston sealing ring.
Braking with ABS modulation |
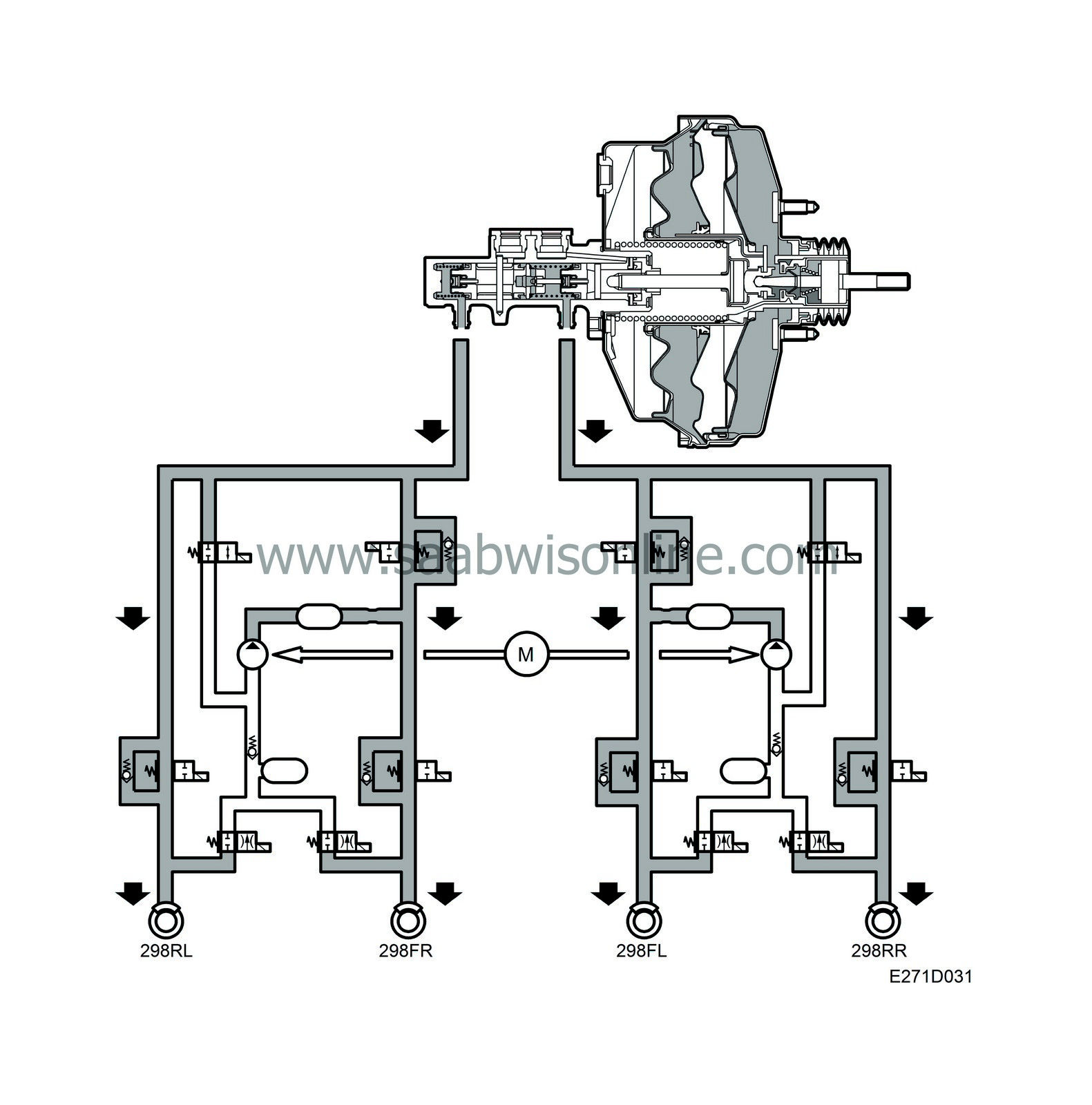
ABS modulation is activated when one or more wheels exceed the permissible slip threshold. The control module receives wheel-speed signals from a sensor on each wheel. If the slip threshold is exceeded, the control module will modulate the braking force, i.e. the pressure in the brake lines, by means of the solenoid valves. The braking force is controlled individually for each wheel.
The brake pressure to each brake circuit is governed by the reduction in wheel speed sensed by the wheel sensors. The control module controls the inlet and outlet valves in such a way that the greatest possible brake force is applied between the wheels and the road surface.
Pressure is retained when the inlet valve is closed and reduced when the outlet valve is opened at the same time as the return pump starts.
ABS modulation will continue until:
• |
The car has been brought to a standstill.
|
• |
The driver has reduced the pressure applied to the brake pedal such that the road surface is able to take up the brake force without any of the wheels tending to lock up.
|
The return pump, which returns excess brake fluid to the master cylinder, is activated only when the ABS mode is operative and the outlet valve is open.
The pressure in the flow of additional brake fluid is determined by the brake pressure in the master cylinder, which is in turn proportional to the pedal force applied.
Braking phases |
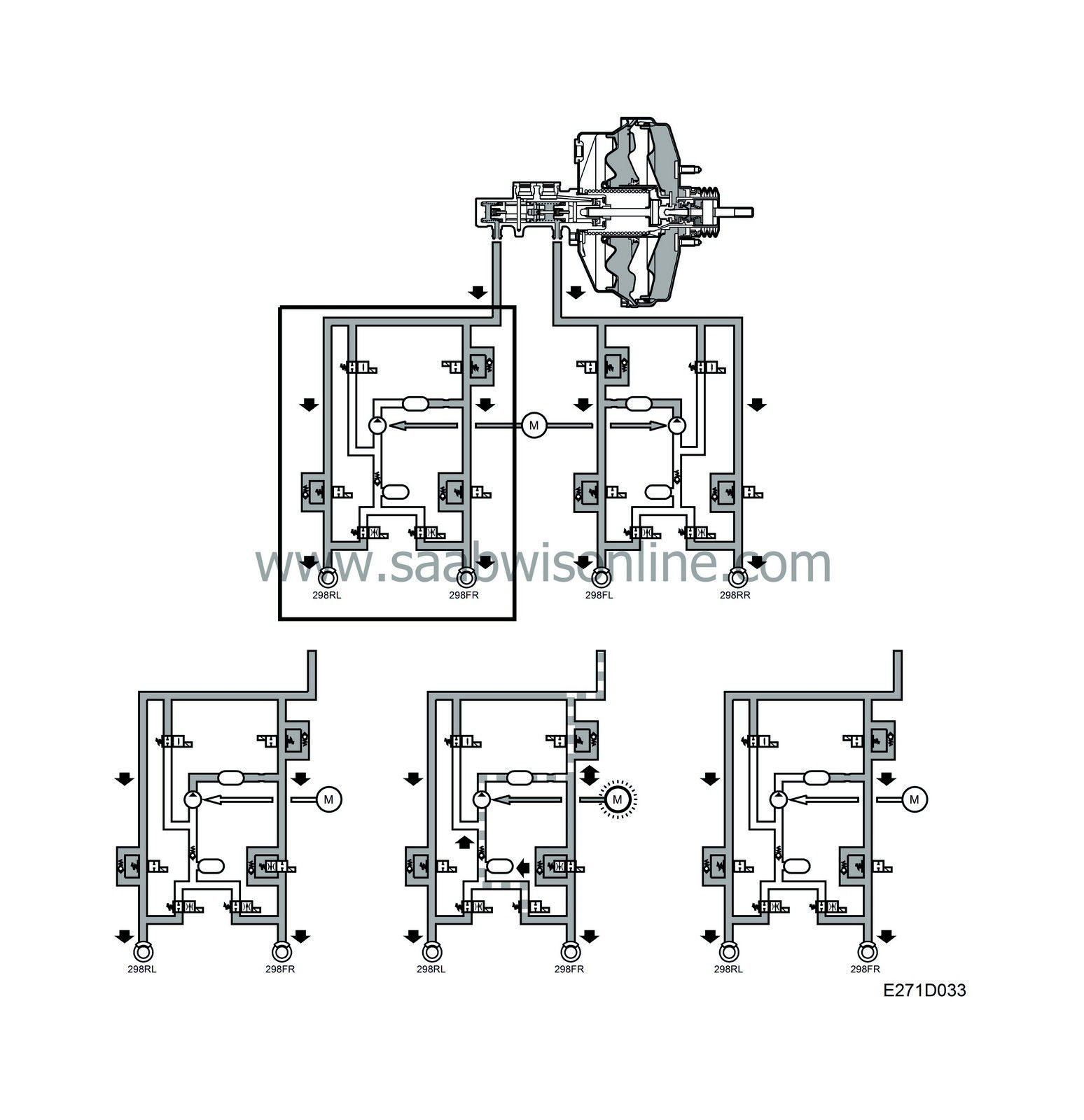