Purging
Purging |
Fuel that evaporates in the tank is passed through a pipe to the EVAP canister. The active charcoal in the EVAP canister becomes saturated as it absorbs the hydrocarbon vapours. When the engine starts, ambient air is drawn through the EVAP canister via the purge valve and a non-return valve in the intake manifold. The fuel vapours follow along with the air and are burned in the engine. When the pressure in the intake manifold exceeds barometric pressure, another non-return valve opens and the vapours are now purged to the suction side of the turbocharger.
The EVAP canister purge valve is normally closed. It is supplied with current from the main relay and is controlled with a 16Hz PWM from control module pin 17(B). However, the frequency is 8Hz during the tank integrity diagnosis.
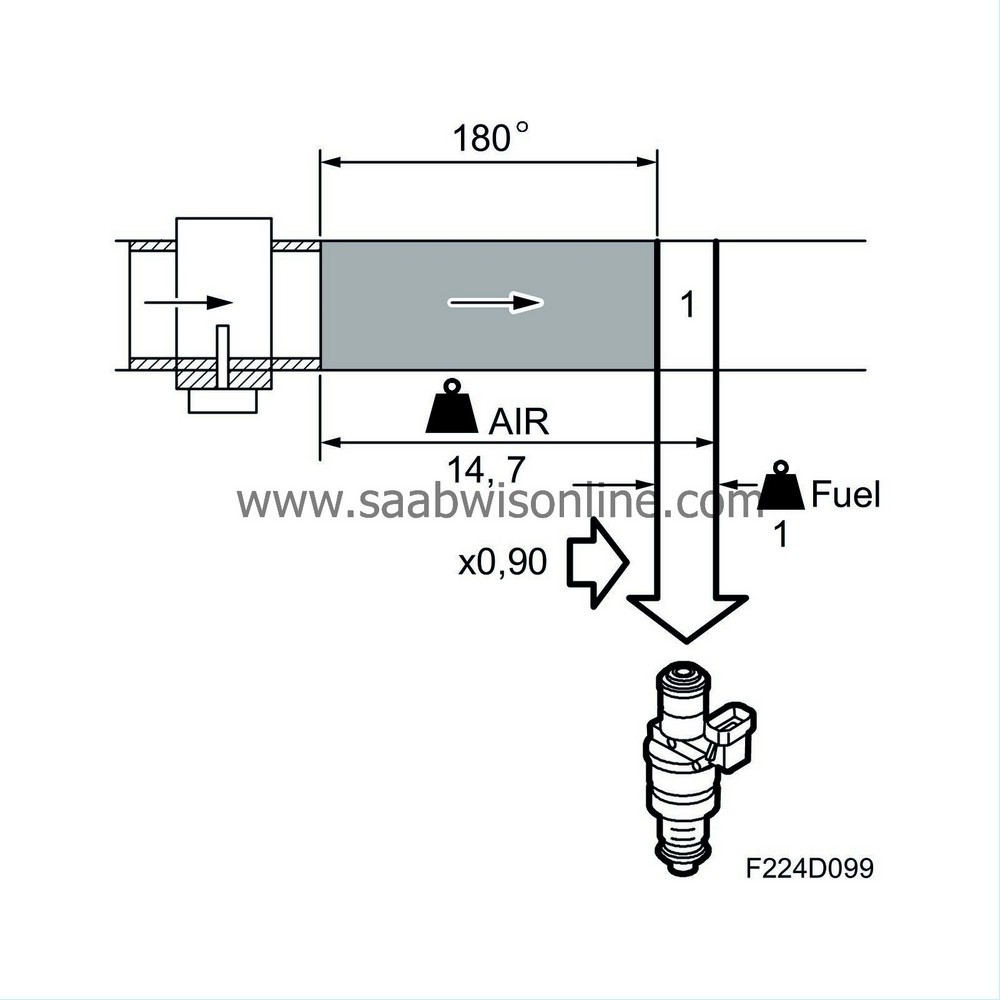
The flow is controlled by the pulse ratio so that it always constitutes a specific proportion of the total flow consumed by the engine.
If the flow has a fuel/air ratio other than 14.7:1, the closed loop control system will be affected. However, since it is not the task of closed loop to correct for the purge addition, the purging function has a correction factor which is affected by the closed loop as soon as purging starts. The entire departure of closed loop from 1.00 is added to the purge correction factor, which means that closed loop fluctuates round 1.00 (0%) even if the purge contains large quantities of hydrocarbons or consists of clean air.
When purge is not active, a factor of 1.00 is used and the entire fuel fault is corrected by closed loop and the multiplicative/additive adaptations.
The limits for purging adaptation are 0.75 and 1.25 respectively.
The following conditions must be fulfilled for purging to be engaged:
• |
Closed loop active.
|
• |
No fuel adaptation in progress; this takes place for 30 seconds every 5 minutes.
|
• |
Engine coolant temperature exceeds 40°C.
|
• |
If the charge air temperature is below 15°C, the vehicle speed must exceed 6 km/h.
The function is active during the whole driving cycle and reduces the risk of noise being heard from the valve. The valve makes more noise when it is cold. |
• |
Battery voltage below 16V.
|
• |
Tank integrity diagnosis inactive.
|
• |
Engine speed not more than 150 rpm below nominal idling speed.
|
The diagnostic tool shows 25% when the correction factor is 1.25 and -25% when the correction factor is 0.75.

Integrity diagnosis |
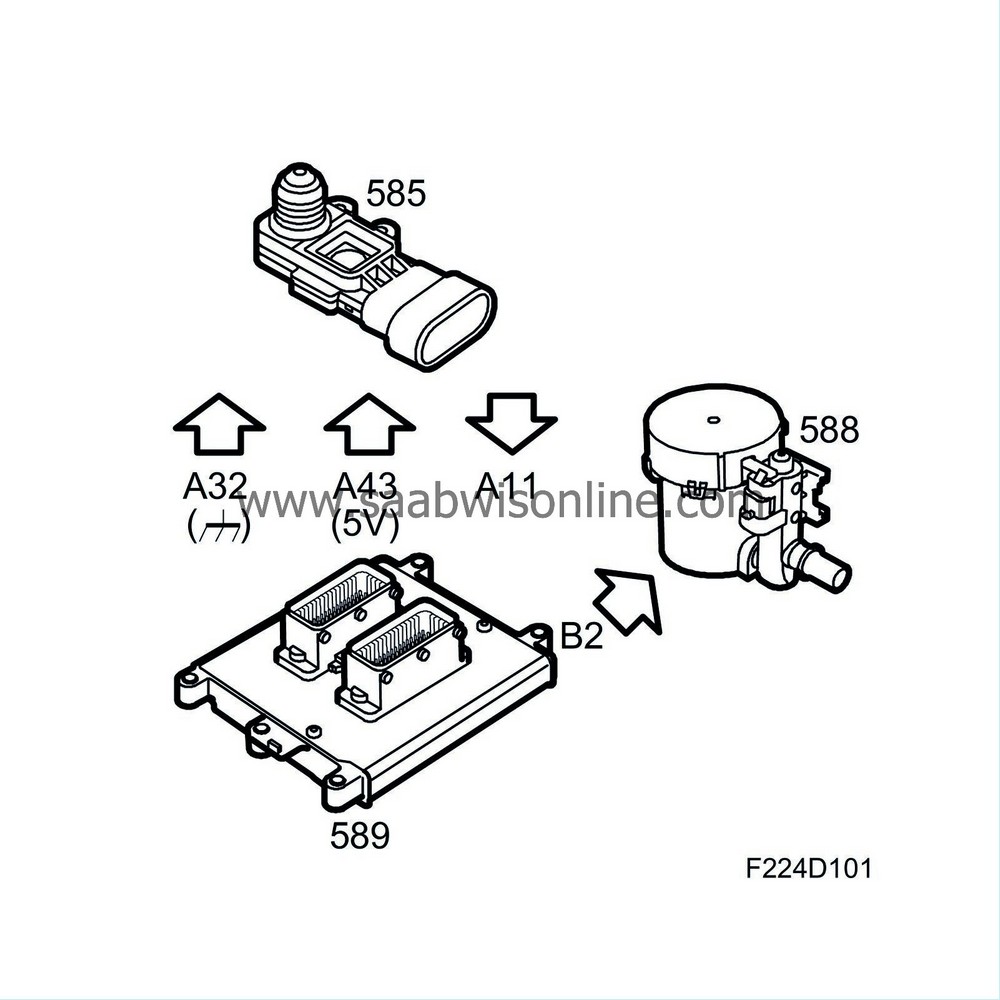
The on-board diagnostics must be able to detect a leak in the purge system corresponding to a hole with diameter 0.5 mm.
For this reason, there is a differential pressure sensor mounted on the fuel pump cover and a shut-off valve for the evaporative emission canister atmospheric connection. With the shut-off valve closed, it must be possible to create and maintain a vacuum in the tank using the EVAP canister purge valve. Otherwise, the system is leading and a fault code will be generated. The diagnosis is run once per driving cycle.
The pressure sensor is supplied with 5V from control module pin 43(A) and grounded from control module pin 32(A). Depending on the difference between the tank pressure and atmospheric pressure, the pressure sensor will apply a proportional voltage on control module pin 11(A).
The shut-off valve is open in zero current state. It is supplied with current from the main relay and is controlled from control module pin 2(B).