Balancer shafts
Balancer shafts |
Engine vibrations |
Great efforts are being made to improve the comfort for the car driver and passengers. Two areas that have been touched on are engine vibration and noise level, both of which are a result of the basic design of the engine. Gaseous forces are created during combustion, where chemical energy is transformed into mechanical energy, which acts on the piston crowns. The reciprocating motion of the pistons and connecting rods creates inertial forces that make the engine block vibrate in various ways. At low engine speeds, the gaseous forces are greater than the inertial forces, while the inertial forces are greater than the gaseous forces at high speeds. The most significant forces arise periodically once or twice per crankshaft revolution, these are called inertial forces of the first and second order. Inertial forces of the first order are completely outweighed by the balanced crankshaft and by the two pairs of pistons 1-4 and 2-3 turning simultaneously in different directions.
Second order forces acting vertically |
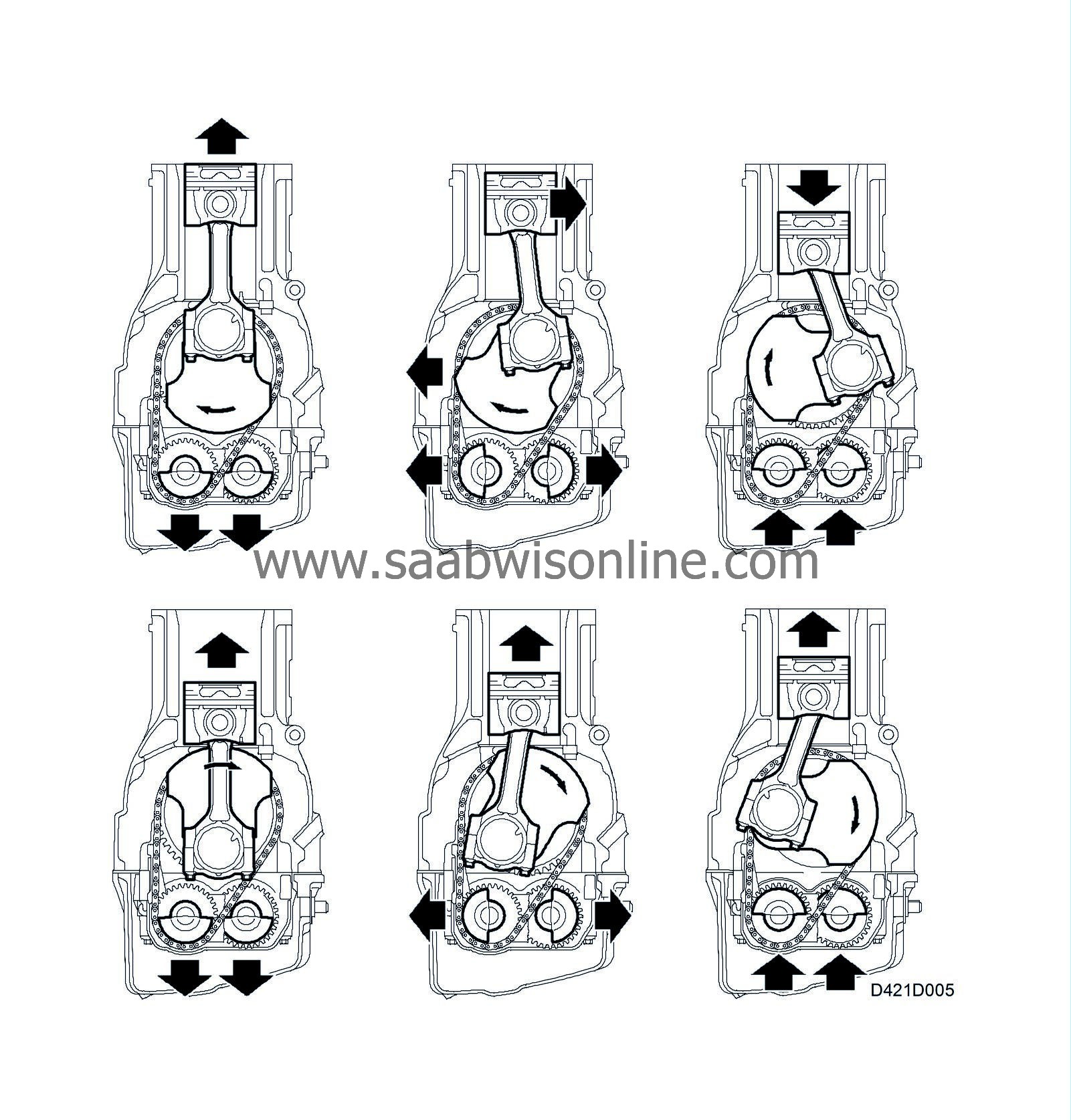
Inertial forces are caused by the fact that both the descending pistons in a 4-cylinder engine at a certain crankshaft angle move a longer distance than both the ascending pistons (the sideways movement of the connecting rod accelerates the descending piston movement but delays the ascending movement). The common centre of gravity of the vertical masses therefore varies, causing vertical forces that vary periodically twice per crankshaft revolution and cause the engine to vibrate vertically.
Second order forces acting laterally |
During the power stroke, the piston is pressed against the cylinder wall due to the angle of the connecting rod in relation to the cylinder bore. At higher engine speeds however, the inertial forces are much greater. Irrespective of the engine speed, the lateral gaseous and inertial forces vary periodically twice per crankshaft revolution and cause the engine to vibrate laterally.
Balancer shaft system |
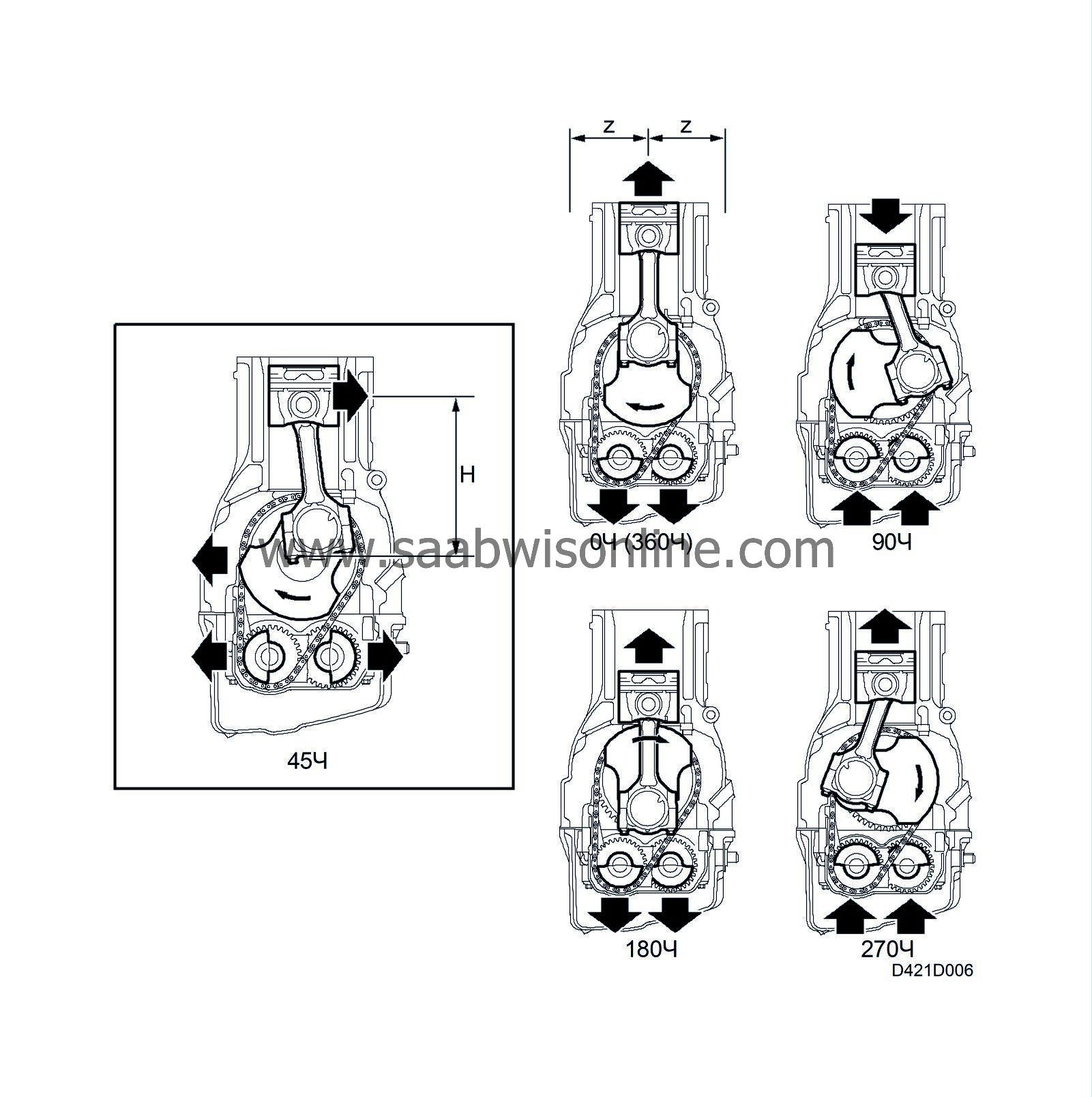
Saab has utilized the principle of balancer shafts to balance the second order inertial forces. Two balancer shafts, placed symmetrically on each side below the crankshaft in the crankcase, have eccentrically placed balance weights on them. One of the shafts is driven by a chain from a sprocket on the crankshaft and the other is driven by a spur gear engaged in the chain-driven shaft. They rotate in opposite directions to each other at twice the speed of the crankshaft.
The balance weights on the shafts are placed so that they reduce the mass forces caused by the movement of the pistons and connecting rods as well as the gaseous forces created during the working cycle.
The balancer shafts are mounted in a cast frame, which also acts to reinforce the crankcase and main bearings.
One absolute condition for the function of the balancer shafts is that they are mounted in exactly the correct position. This means that the crankshaft in the engine must be made fast when cylinder 1 is at top dead centre when work is being carried out on the balancer shafts. The balancer shafts must also be fixed in position with a tool.
Balancer shaft drive |
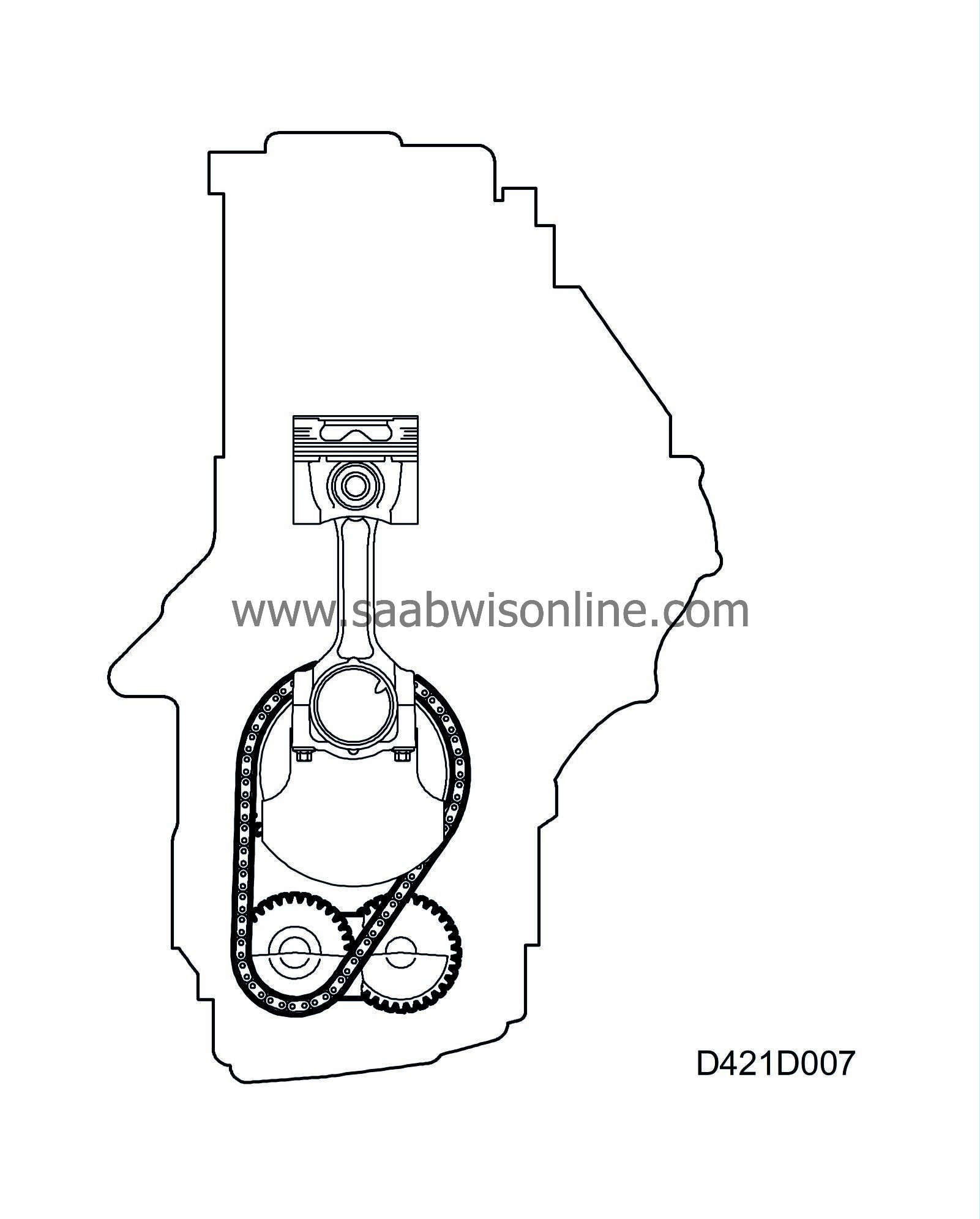
The balancer shafts are driven by the crankshaft via a chain connected to one of the shafts and from there via a spur gear to the other shaft. The gear ratio is such that the speed of the balancer shafts is twice that of the crankshaft. Also, they are designed to rotate in the opposite directions.
The chain is guided partly by a fixed chain guide, partly by a pivoted chain guide that is acted on by a tensioner.
The chain tensioner is spring-loaded and damped by the effect of oil pressure in the opposite direction. This is to reduce chain wear as well as chain noise.