Detailed description
Detailed description |
All the control modules in the car are connected via three buses. Two of these buses are electrical while the third is optical.
The two electrical buses are the P-bus (Powertrain bus) and I-bus (Instrument bus). The P-bus has two leads and the I-bus one lead. The difference in voltage between the two leads (P-bus) or the lead and ground (I-bus) is either 0 V or roughly 5 V. The information is coded so that different combinations of pulses, with the values 0 V and 5 V, have different meanings.
The optic bus is known as the O-bus and has an extremely high capacity. It is primarily used to send audio signals, e.g. from the radio receiver or CD changer to the amplifiers. Digital information is transmitted in a plastic cable by pulsating the sound at low and high intensities to thereby form ones and zeros.
P-bus and I-bus |
The two electrical buses are connected to the Column Integration Module (CIM), Infotainment Control Module (ICM) and data link connector. The buses are electrically isolated. The CIM and ICM are gateways, transferring information between the buses. The CIM relays information between the electrical buses. The ICM makes sure that information is transferred between the O-bus and the electrical buses.
The P-bus has a data transfer rate of 500 kbits/s and the I-bus of 33 kbits/s. The data rate on the P-bus is high to allow the powertrain systems access to information with the shortest possible delay, for example during air mass compensation when the selector lever is moved from N to D or TCS or ESP modulation.
The control modules send out information on the bus whenever the information changes. As a safety precaution, the information is also sent at regular intervals irrespective of whether or not it is new. The time between two transmissions depends on the information being transmitted and varies between 10 milliseconds (engine torque) and 10 second (VIN). When a control module sends information, the other control modules listen regardless of whether or not they use the information.
A bus system means that it is sufficient with one sensor for each measurement function in the car. The number of separate signal leads can also be reduced. For example, the engine management system has a coolant temperature sensor, which means that coolant temperature is always available to all systems. Therefore, the car only needs one coolant temperature sensor. Coolant temperature is used by the main instrument unit to control the temperature gauge, and the ACC to control ventilation fan speed and air distribution when starting from cold.
I-bus, principles of communication
You can think of the bus as a telephone line running between the control modules. The I-bus system does not have a +15 power supply lead, with the exception of for the airbag control module (ACM). With the ignition switched on, communication goes on continuously. The CIM determines the key position from information from the ignition switch module (ISM).
When the key is inserted into the ignition, the CIM wakes the other control modules on the I-bus by briefly sending B+ over the bus. The CIM then sends regular reports over the bus of the key position.
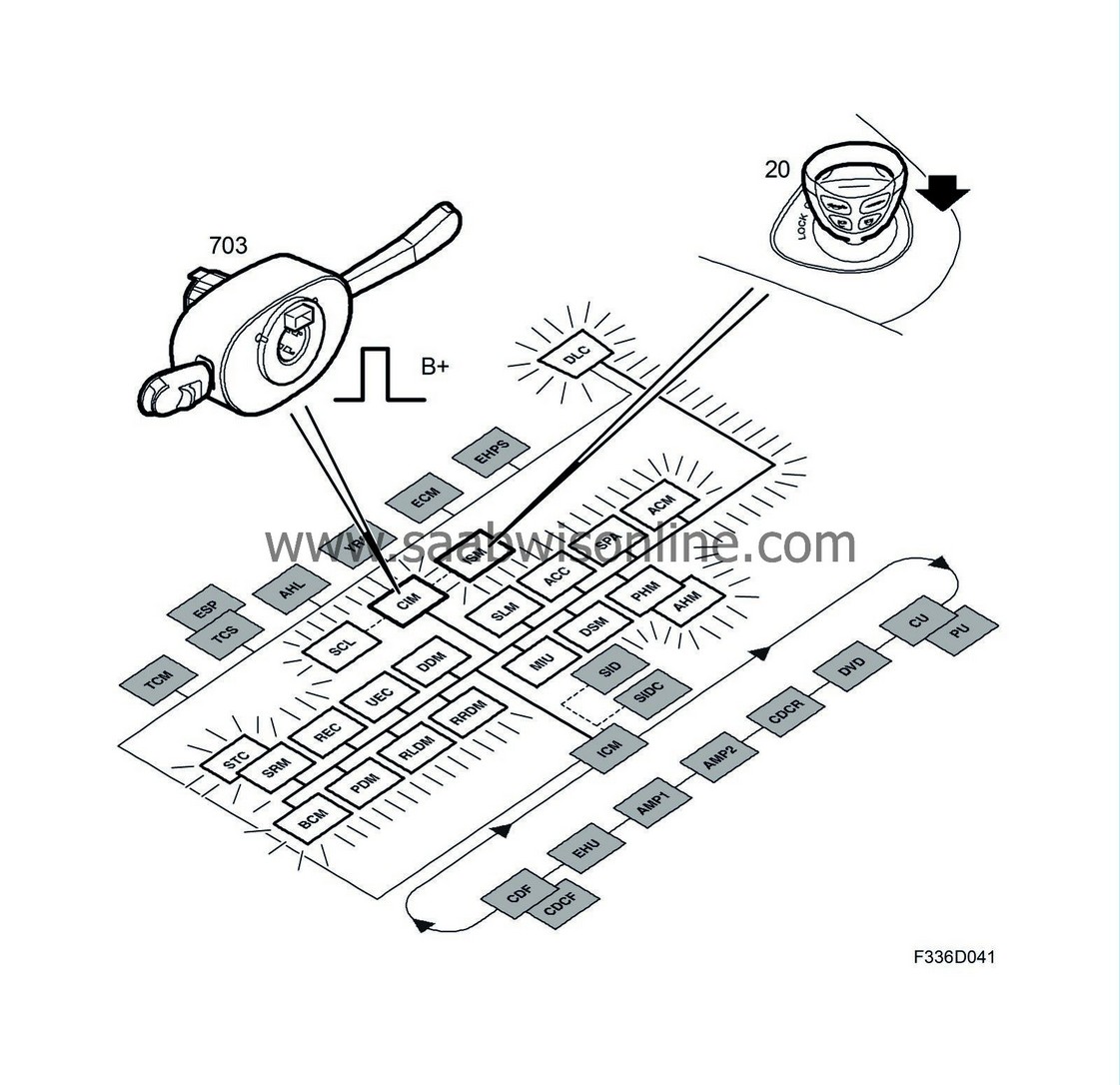
Communication can still be started even if the key has been removed from the ignition switch. For example, if you press the open button on the remote control, the CIM, which receives the signal, wakes the other control modules so that the body control module (BCM) can turn on the interior lighting and the driver door module (DDM), for example, can unlock the door. The control modules go back to sleep when no messages concerning them are sent on the bus.
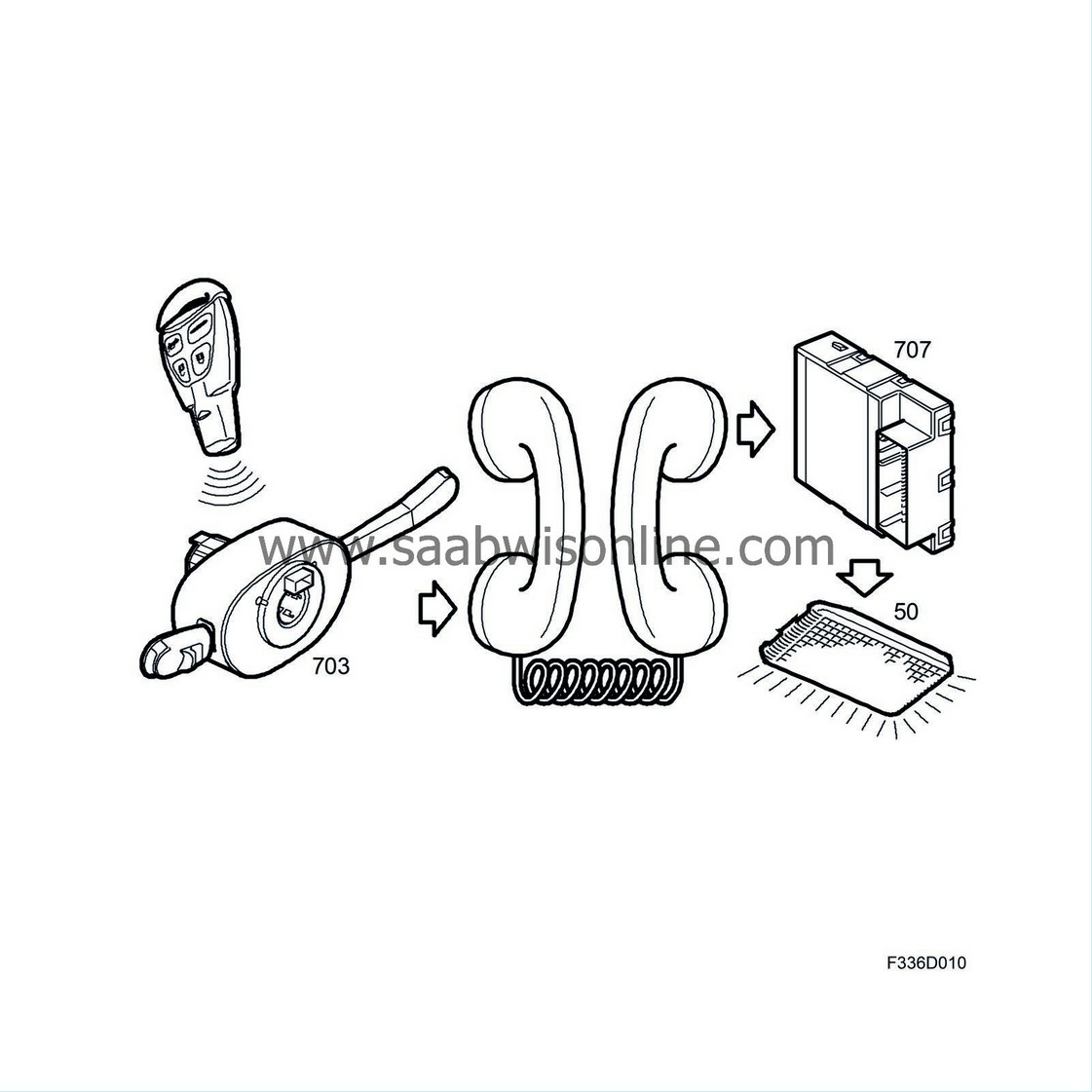
The bus lead is a green cable that is internally grounded in each control module via a 9 kΩ or a 4 kΩ resistor. MIU, BCM, DDM, PDM, CIM, RRDM, RLDM and REC are the control modules grounded internally via a 4 kΩ resistor. To send a zero, the control module raises the bus lead voltage towards 5 V. A potential difference to ground lower than 2.2 V is interpreted as a one, and higher than 2.2 V as a zero. Note that a long series of ones is the same as no message being sent.
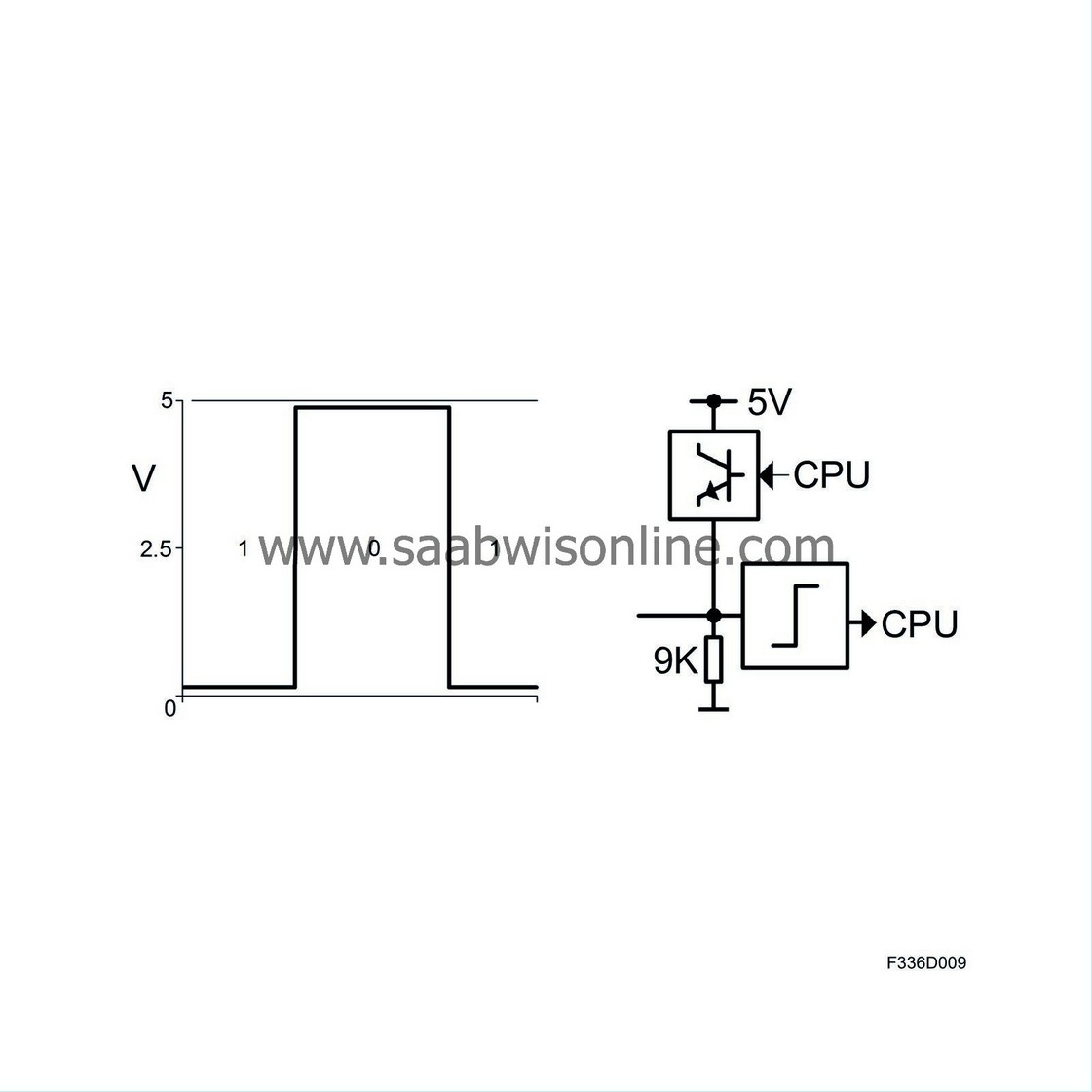
P-bus, principles of communication
The P-bus system has a +15 lead coming directly from the ISM. With the ignition switched on, communication goes on continuously. Communication stops as soon as the ignition is switched off. The P-bus does not have a wake-up function similar to that of the I-bus.

The two bus leads (a green wire for bus + and a white wire for bus -) are fed with roughly 2.5V by each control module. The voltage is created using three resistors connected in series between 5V and ground. The middle resistor means that the voltage on bus + is slightly higher than that on bus - when no message is being sent.
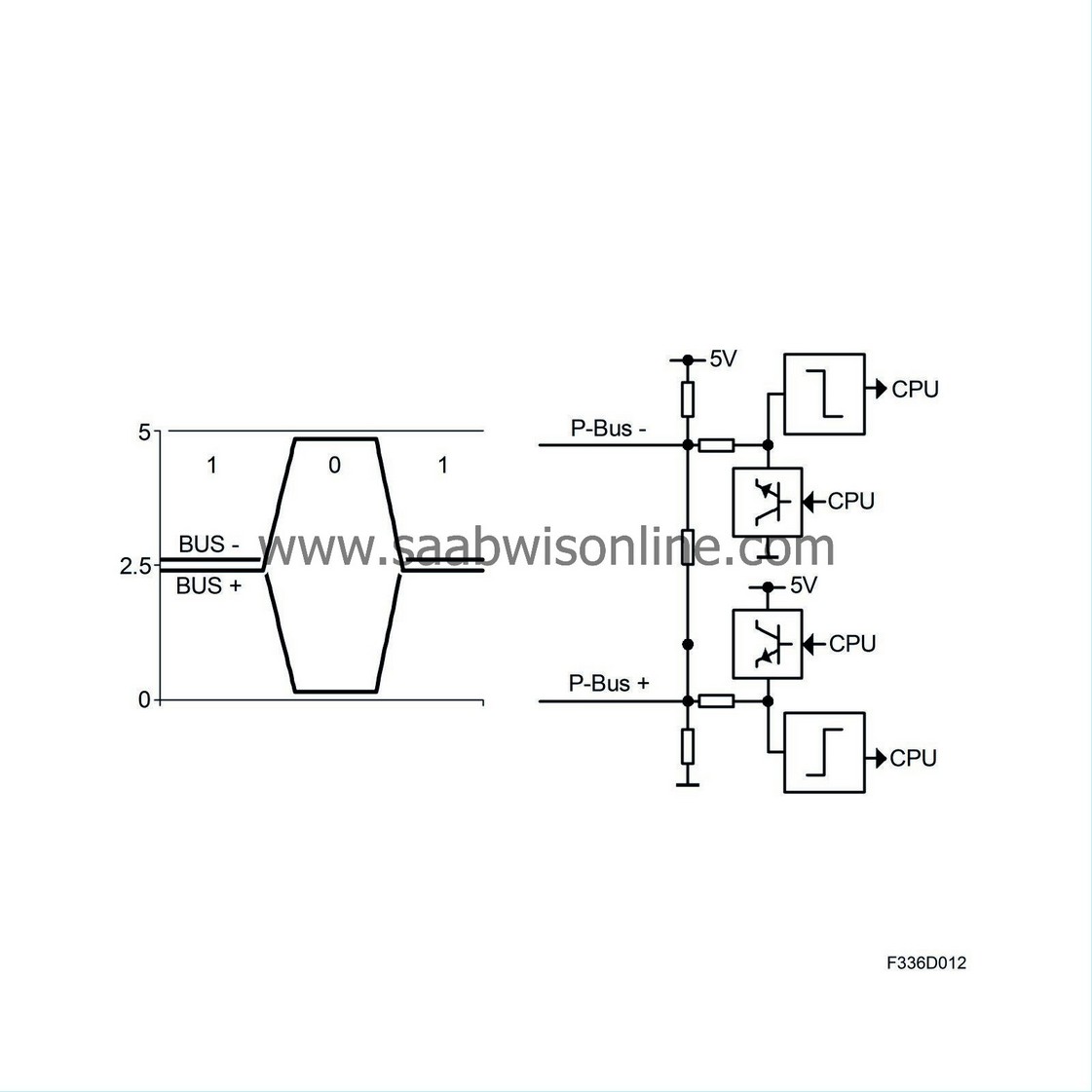
A one is sent when the voltage on both leads is roughly 2.5 V for a certain period of time (2 millionths of a second). A zero is sent when the control module raise the voltage on bus + towards 5 V and lowers that of bus - to ground for the same period of time. A potential difference lower than 1.5 V is interpreted as a one, and higher than 1.5 V as a zero. Note that a long series of zeros is the same as no message being sent.
The P-bus, which has a high data rate, has two wires to reduce its sensitivity to interference. A possible source of interference, such as a relay, will have the same affect on the voltage of both wires. The difference in voltage between the wires will therefore remain the same, and the message will not be affected. The wires are also twisted to further reduce their sensitivity.
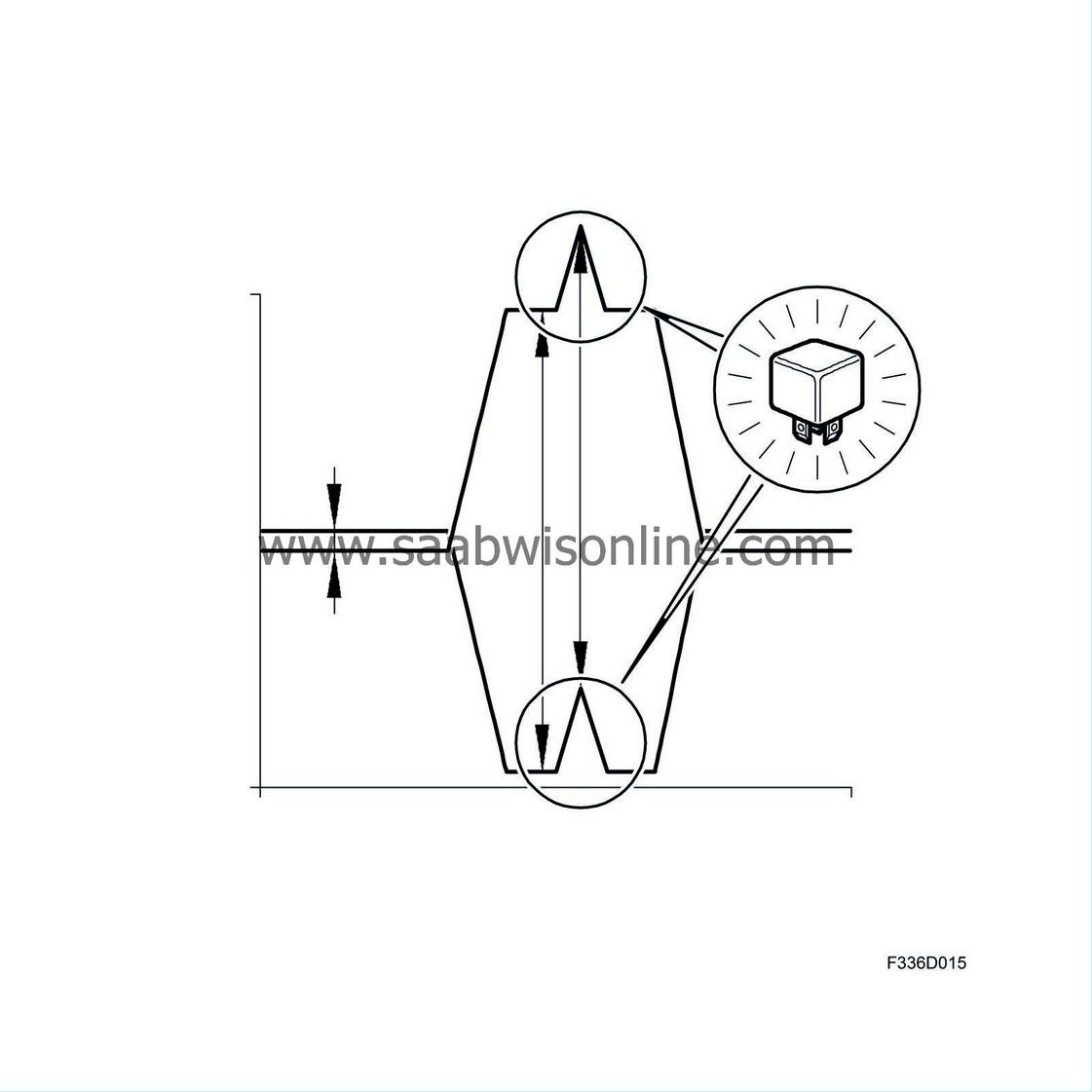
P-bus and I-bus, message transmission and reception
A control module sends a message by sending ones and zeros in a predefined order. The control module only sends a message if no other control module is presently sending. When one control module sends a message, all the other control modules listen, interpreting the combination of ones and zeros. The meaning of the combinations of ones and zeros is predefined so that all the control modules can interpret the information in the same way. The message contains information about what is being sent and the value, for example "Coolant temperature 100°C" or "A/C ON".
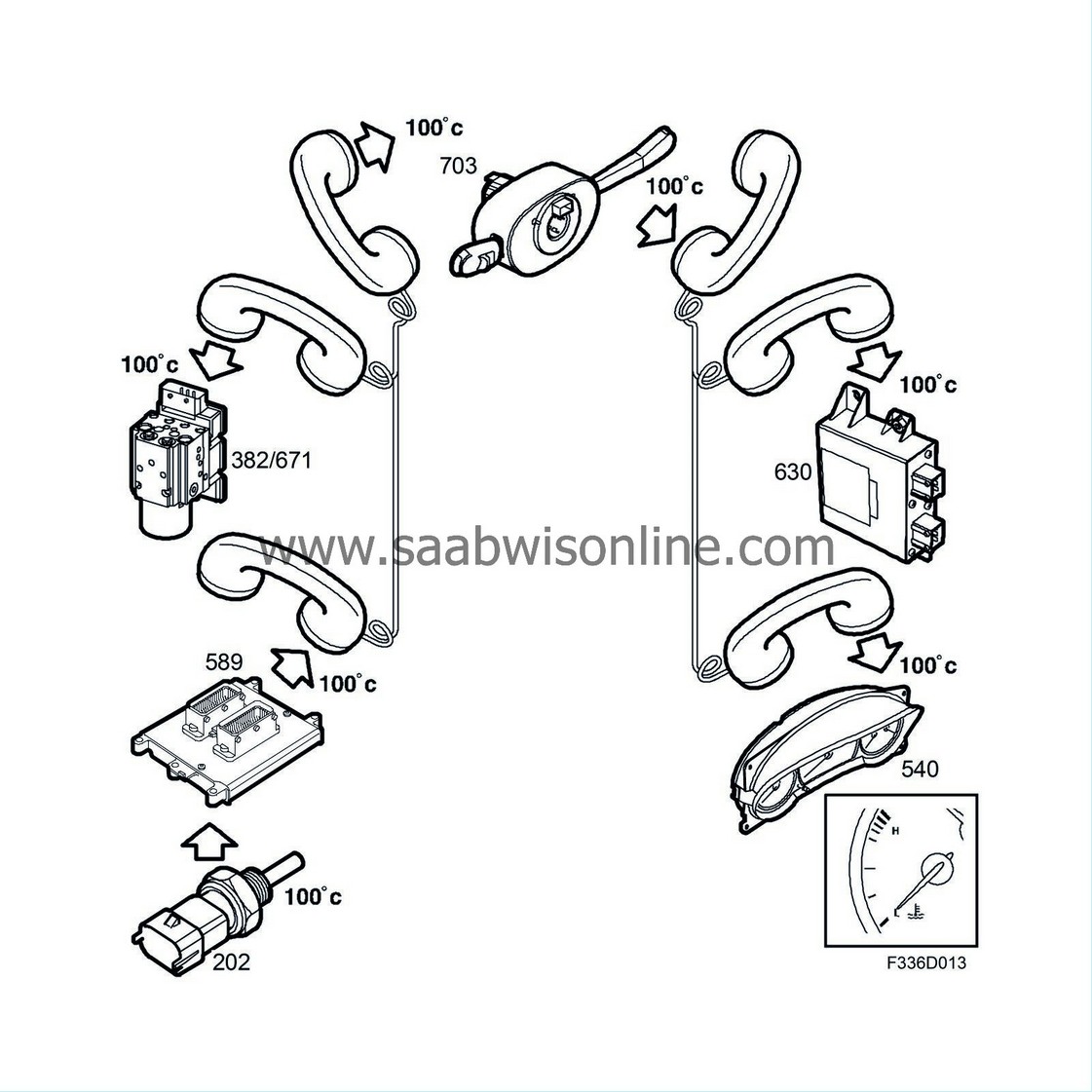
O-bus |
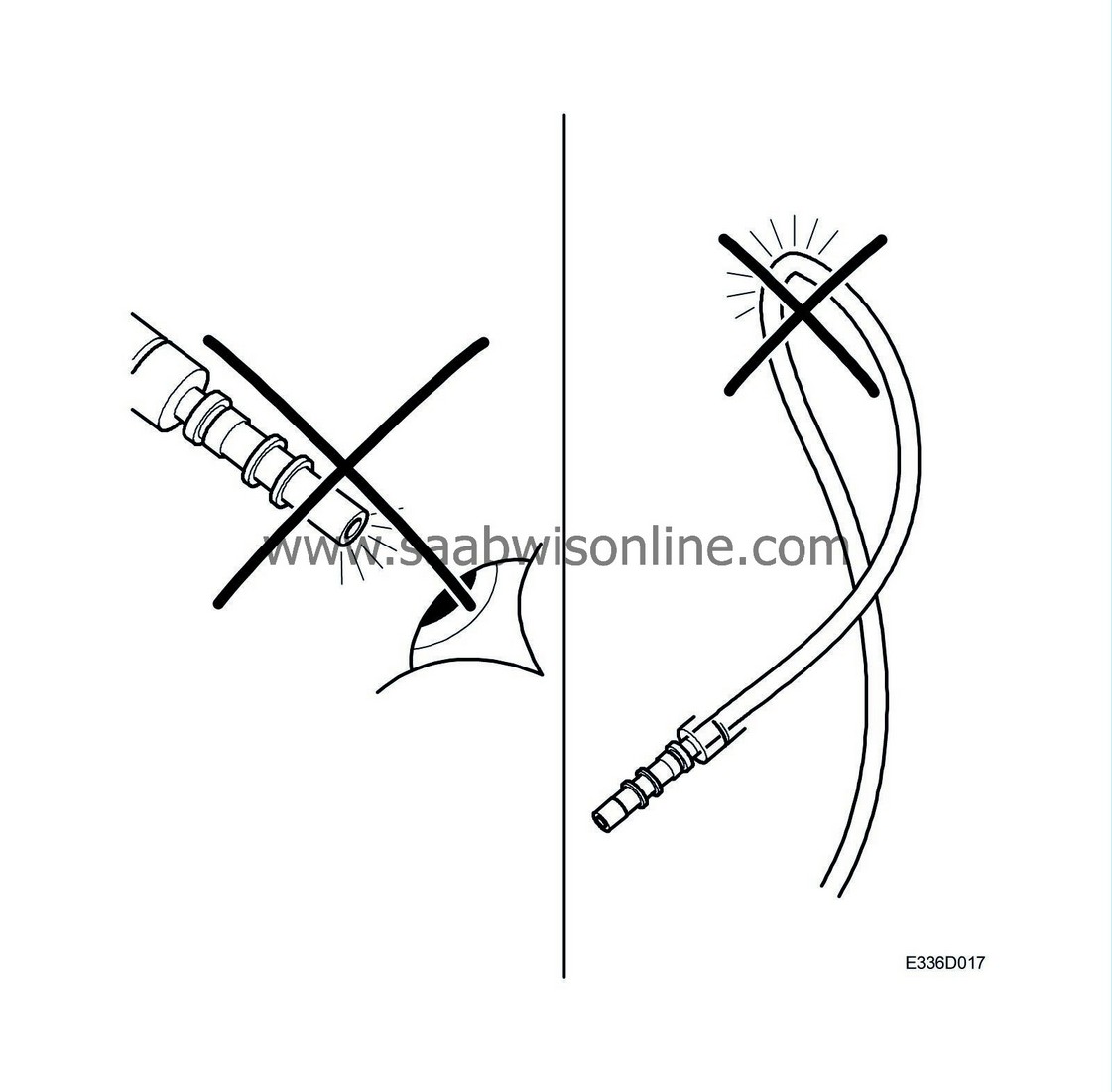
|
The LEDs in the transmitters, though not laser diodes, produce high-intensity light. The light is therefore classed as laser class 1. Do not look directly at the light source (detached fibre of connection). Visual inspection to establish that light is emitted from a fibre is used during fault diagnosis. In such cases, do not point the fibre towards the eyes but shine the light onto a piece of paper or other light object and look at the reflection.
The optical bus consists of an orange 2.3 mm thick plastic cable that looks similar to a standard electrical cable. The optical cable contains a 1.0 mm diameter, transparent, plastic, optical fibre and two protective plastic layers. Each end of the cable has a plastic or brass cable terminal. The purpose of the terminal is to secure and centre the cable on the control module. Each control module is connected to two cables; one for incoming data and one for outgoing data. The bus is a ring bus, which means that messages are sent around the ring by the various control modules.
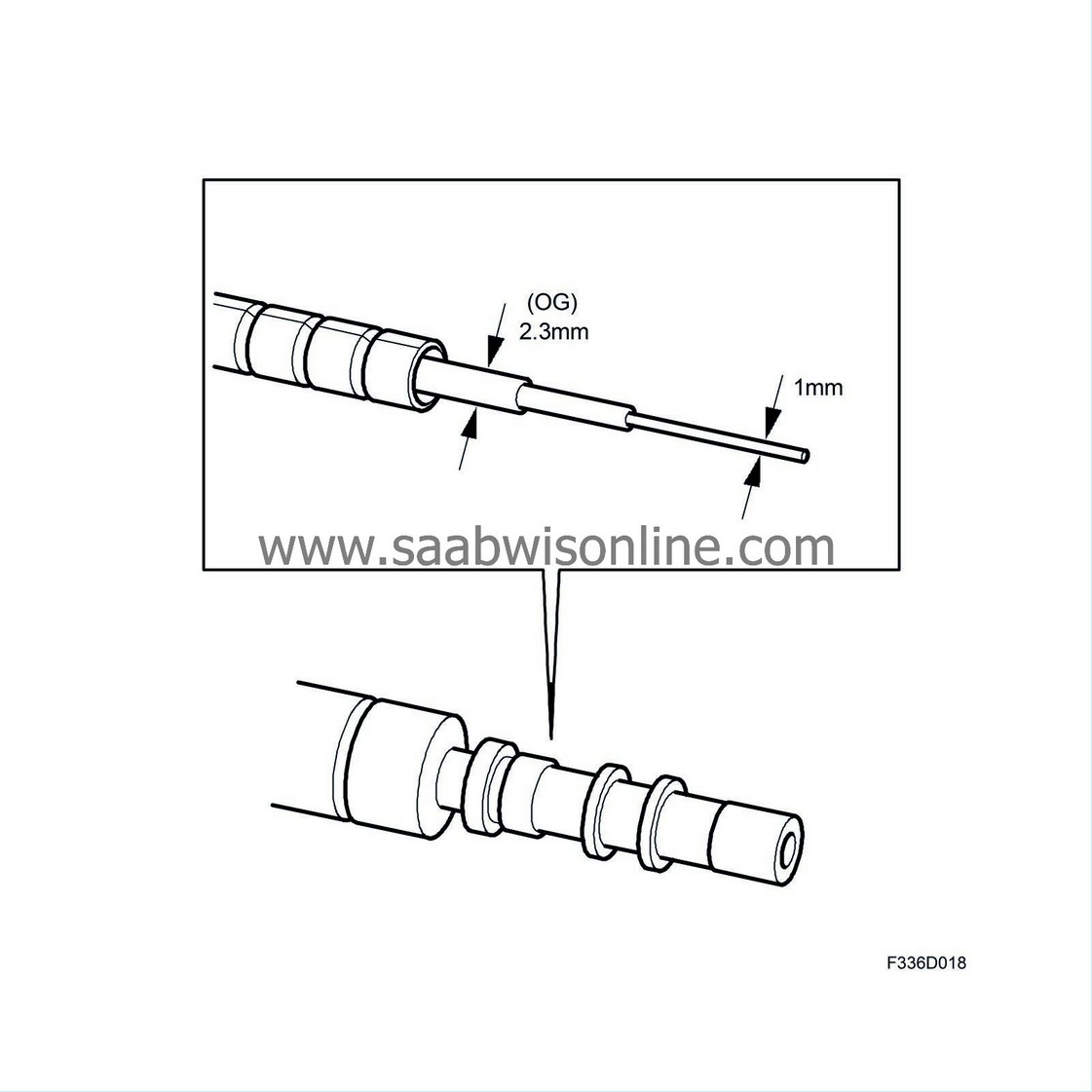
The messages are digital and consist of red light pulses. Each control module converts received messages from optical signals into electrical signals and then back into optical signals for transmission to the next control module.
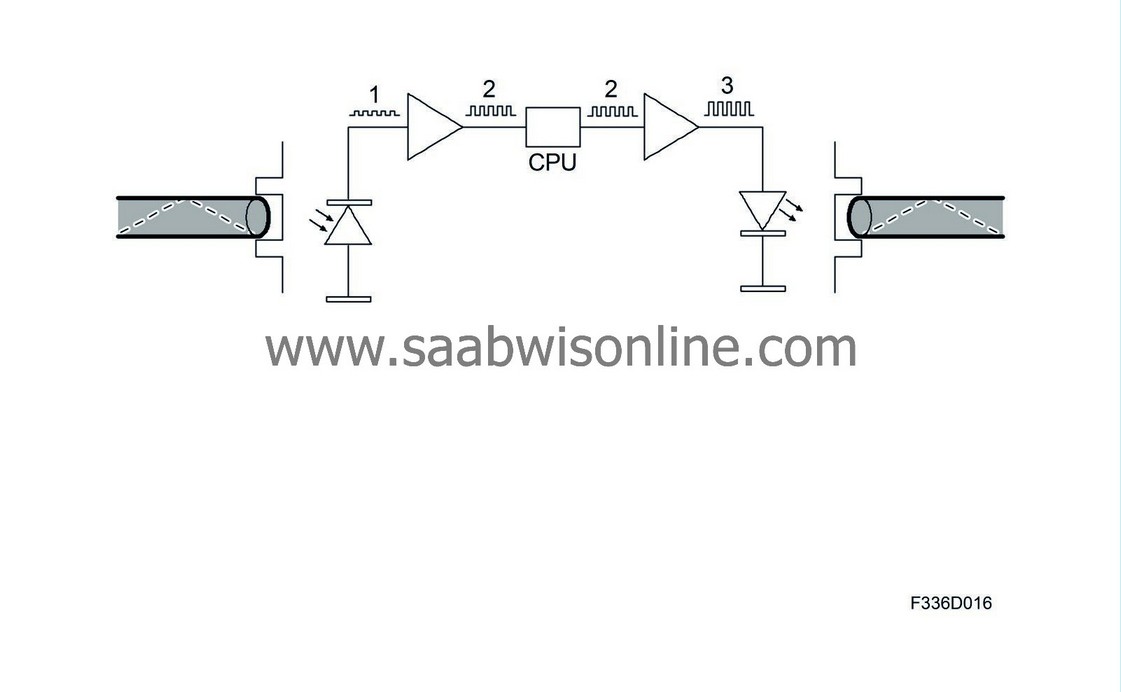
The control module that is the source of a specific type of information modifies the information as necessary each time it passes. The other control modules are free to receive and use any relevant messages.
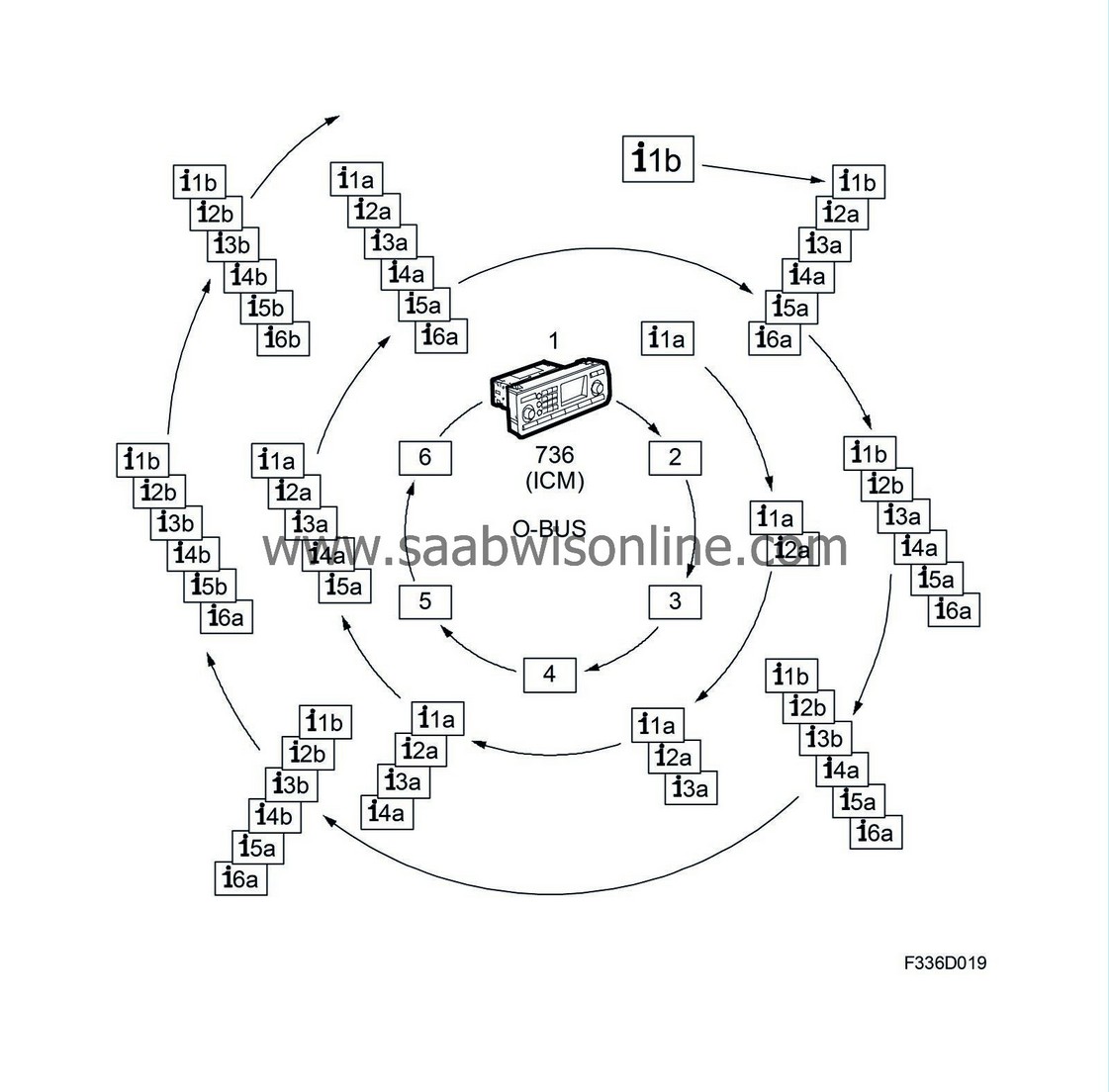
The O-bus has a data rate of 25 Mbit/s. This large capacity means that audio data can be sent in real-time between a playback device or radio receiver and the amplifiers. The P-bus and I-bus are both connected to the ICM. The ICM relays information between the electrical buses and the O-bus.
None of the modules on the O-bus have a +15 lead. All the modules wake up when they receive a light pulse and remain awake so long as a module is communicating. Pressing a button on the ICM is the most reliable way to wake the bus immediately.
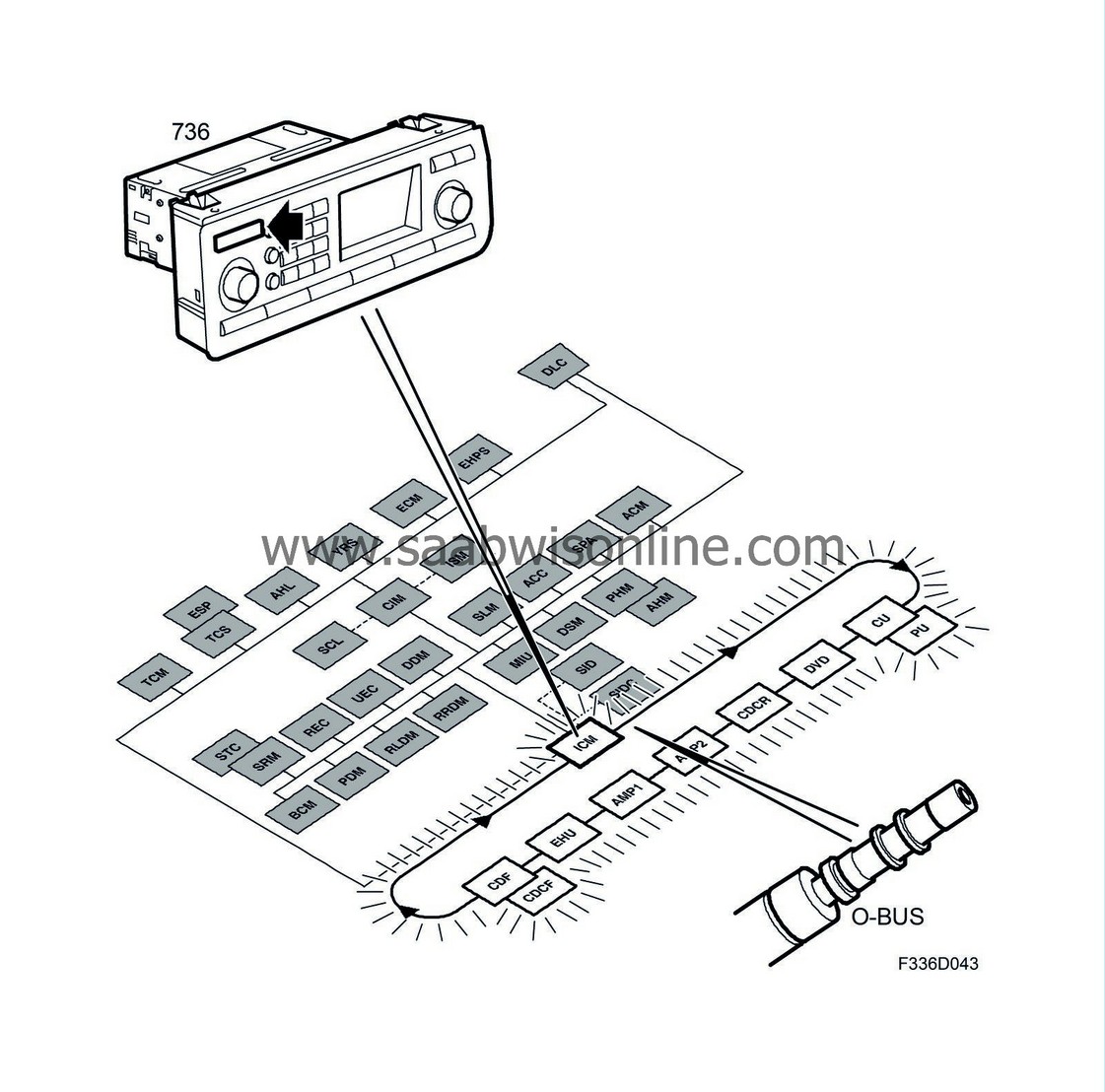
In the most basic model of the car, there are only optical cables behind the dashboard between the ICM and EHU. In other car variants, the optical cables are routed to a CD player or changer in the dashboard, an amplifier under the driver's seat and to the luggage compartment, which can contain other units.
The cable terminals of the cables can be unplugged from the control module connector. It is very important that the two cable in the connector are not confused. Pin 1 receives information and pin 2 sends it. Sending and receiving diodes are located inside the control module connector. Additional control modules can be connected. Each control module must be connected to a specific place in the ring as compensation has been made for the short delays in communication.
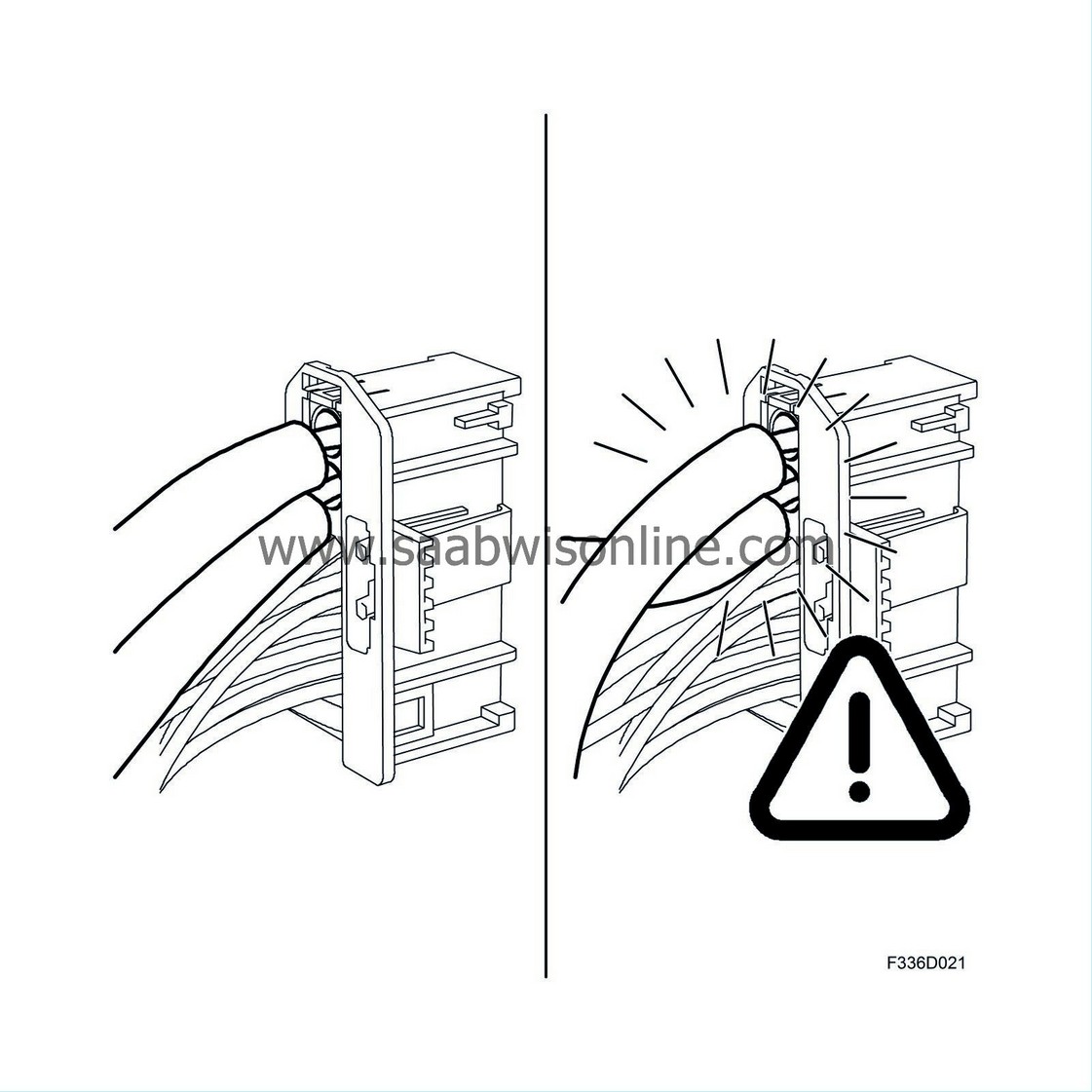
Cables cannot be joined but are supplied in ready lengths. The plastic cable terminals are laser welded to the cable and the brass terminals are pressed on. The cable must not be bent to a radius of less than 25 mm or be subjected to temperatures greater than 85°C. The ends of the cable must not be dirty, but exceptional cleanliness is not necessary. The cable is resistant to small amounts of oil, acid, brake fluid, alcohol and glycol. If the cable is subjected to an impact, the transparent plastic fibre will whiten reducing the light intensity and could cause a break in communication. The cable must not be pulled tight over sharp edges. Although this will not cause permanent damage it will reduce the light intensity. Insufficient light intensity can be experienced as a rattling from the audio system, similar to atmospheric interference.
Diagnostics communication
The P-bus and I-bus are wired to the data link connector. Tech 2 can be connected with an adapter to the data link connector and communicates directly with the various control modules on the P-bus and I-bus. Diagnostics communication with O-bus systems takes place via the ICM, which acts as a gateway.
In a bus system, all units must be able to communicate with each other. For example, the engine cannot be started unless the ECM can receive the immobilization information broadcast by the CIM. Bus faults can be caused by a bus lead breaking. This could result in one or more systems disappearing from the bus concerned, depending on where the break in the wiring harness occurs. If a short circuit occurs in a bus lead, all systems will disappear from the bus concerned (P or I-bus). In the event of a fault in the grounding or power supply to one or more systems, these will cease to communicate. A break in the O-bus or a fault in the grounding or power supply to a control module on the O-bus will cause the entire O-bus to fail, since this is a ring bus. The only O-bus system that can be contacted in the event of a break is the ICM.
In theory, control modules connected to the bus can be considered as one large control module with a number of sensors and actuators. Bus communication is comparable to internal control module communication. This means that it is vital to consider the entire vehicle when diagnosing faults. A fault may not necessarily lie in the system in which it becomes apparent but may be caused by a faulty sensor in another system.
Permanent bus faults
The ICM contains lists of all the control modules on the three busses in the car in question. When you read out DTCs, Tech 2 always starts by contacting the ICM to check which control modules should be present in the vehicle. Tech 2 then checks which control modules in the car are communicating. If a control module is missing, or if an additional control module has been fitted, this is displayed. Nothing is displayed if the numbers of identities agree. If there is a difference, you are given the opportunity to start fault diagnosis or to accept the new control module configuration. You may wish to accept the new configuration if a control module has been fitted or permanently removed. Tech 2 will then update the lists in the ICM so that no warning is displayed in the future. Tech 2 displays if a control module on the bus is missing. This means that if all control modules connected to the buses are communicating correctly, the diagnostic tool does not display a warning. If one of the O-bus systems is missing, the entire O-bus will be down, and in which case there will be a DTC in the ICM. To find out where the break is, disconnect then reconnect the battery cable. All O-bus systems will then be initiated at the same time, allowing the ICM to calculate how many control modules sent a light signal, in other words, how far back along the ring the break is.
Intermittent bus faults
The ECM and TCM continuously check that all the control modules from which they receive information are communicating correctly. In the event of an intermittent fault in bus communication with one of these systems, DTCs will be generated in the ECM and TCM. The reason for the fault may be the bus leads or that the control module in question lacks power.
Fault counter
To facilitate fault diagnosis, the control modules on the I and P-bus have fault counters. A counter counts up each time bus communication with the control module is broken and the module loses contact with all other control modules. If the counter value of only one control module increases, the problem is local and easy to find. If the values of several control modules increase, wiring diagrams must be used to see how the control modules are interconnected. A total short circuit will cause all the control modules on the bus in question to count up. The counters stops at 255 and can be reset with Tech 2. A counter showing 255 must be reset to be of any use. Intermittent faults can be detected by jiggling the wiring harness. Problems with the power supply or grounding will not be counted by the counter, despite a loss of communication, since the control module itself is then out of order.
Note | ||
It is not uncommon and perfectly normal for the value of a counter in a car that has been driven large distances to be 255. |
O-bus ring break position
To find the position of a break on the O-bus, Tech 2 provides a function called "O-Bus Ring Break Position". To diagnose using the “O-Bus Ring Break Position" function in Tech 2, the car must be without electrical power for 4 minutes if it is equipped with AMP2, or 1 minute for all other versions. Interference on the O-bus due to short-lived breaks or excessive dampening in the optical fibres may not be displayed as breaks on Tech 2.
Therefore, all O-bus control modules provide diagnosis and generate a DTC if they receive a corrupt message. All messages received are converted into electrical signals, reconverted into light and retransmitted. The ICM is the bus master and, unlike the other modules, never resends a corrupt message. If a control module receives a corrupt message, the fault must have occurred upstream, somewhere between the control module and the ICM. This means that a fault will generate a DTC for an intermittent bus fault in all the control modules downstream.
Fault diagnosis follows the standard fault diagnosis procedure: check the power supply to the control module and check the optical fibre. To avoid having to remove large parts of the car, use the fibre optic test cable, part no. 86 12 913. Connecting this cable between two control modules allows fault diagnosis to determine whether the optical cable needs to be changed. Also to facilitate fault diagnosis, the O-bus control modules have fault counters. A counter counts up each time bus communication is broken. The counters stops at 255 and can be reset with Tech 2. A counter showing 255 must be reset to be of any use. Intermittent faults can then be detected by jiggling the harness. This means that a fault will cause all the control modules downstream to count up.
Note | ||
The counters are very sensitive and generally show 255, even after a short period of time. Starting the engine and the activation of the O-bus when the radio is turned on usually cause the value of the counters to increase a couple of digits. |
C-cable |
A C-cable is a communications lead, which in actual fact is a single-wire bus for slow communication between two modules. Such a lead has a maximum transfer rate of 10 kbit/s. Communication is serial and bi-directional. The diagnostic tool is connected to the bus, as are all control modules. All the same, there are a number of C-cables.
Most often, one or both of the modules use a pull-up resistor to raise the voltage on the lead to close on B+. Transmission and reception then take place in accordance with a predetermined protocol. Component manufacturers use the protocol as a standard for message structure to avoid misunderstandings.
Examples of C-cables
The BCM communicates with the alarm siren module (ASM) and alarm sensor via a C-cable.
The CIM communicates with the ignition switch module (ISM) and steering column lock (SCL) via C-cables.
The ACM and front and side sensors communicate over C-cables.
The ICM communicates with the SID and SIDC via C-cables.
Diagnosis of C-cables
The control module that is connected to the bus expects data on the C-cable under certain conditions. If the control module does not receive any data it generates a DTC. The fault may not necessary lie in the lead, it may be that the sending module is not energized or grounded.
Function chains |
A large number of function chains can be identified in the bus system. Described below are four examples of important chains.
1. Vehicle speed
The TC/ABS or ESP control module measures vehicle speed with the help of a Hall sensor at each wheel. The sensor supplies the control module with alternating current, the amplitude and frequency of which increase with increasing wheel speed. The ECM calculates the average speed of the two non-driven wheels, correcting this value for the type of tyre. The ECM sends this value for vehicle speed over the bus making it available to other systems.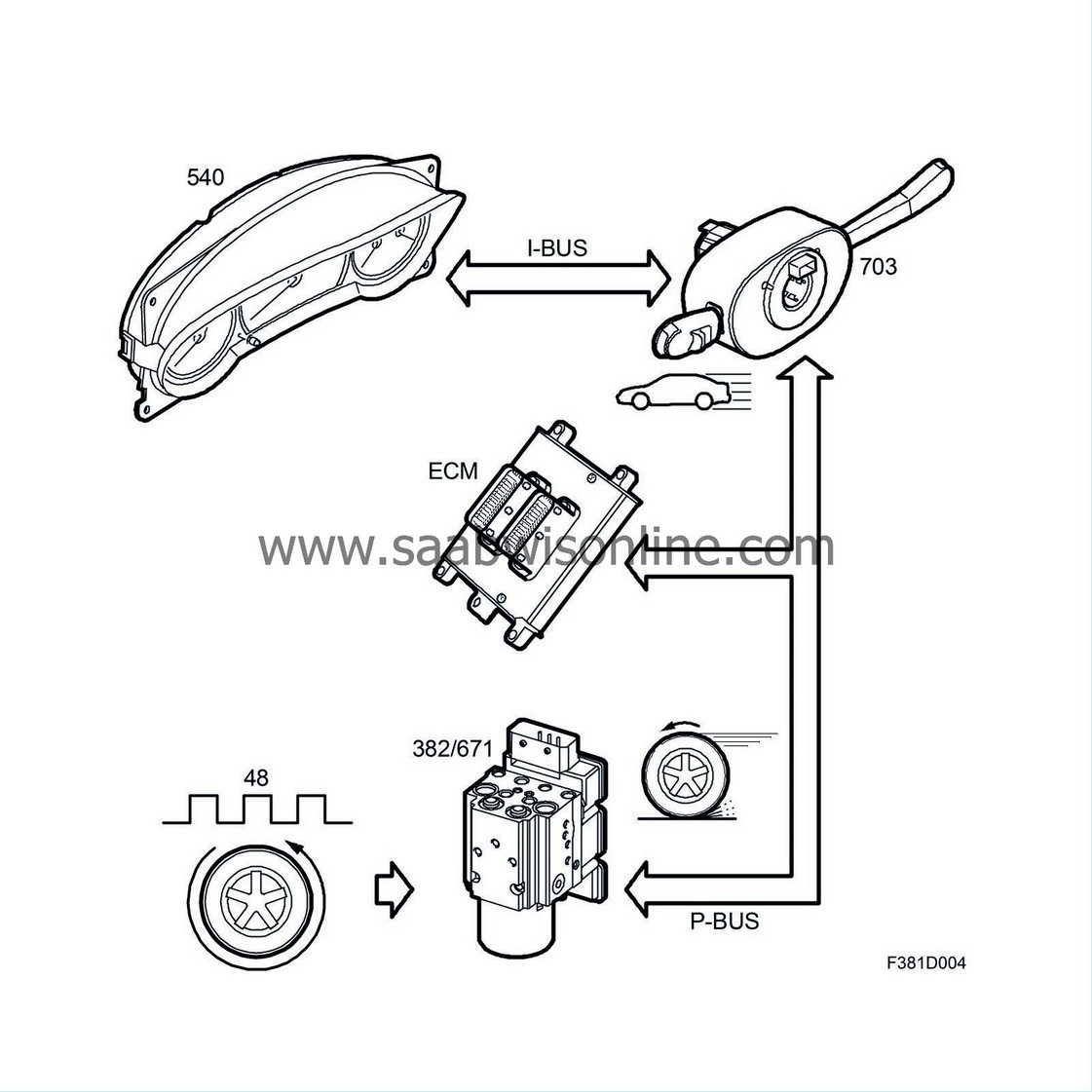
In the table of bus messages, you can see that the ECM sends the value for vehicle speed and that the majority of other control modules use this.
Examples:
- |
The ECM itself uses vehicle speed for cruise control, idle speed control and a number of diagnostic functions. Pulling off (certain markets only).
|
- |
The MIU uses the value for the speedometer.
|
- |
The ICM uses the value for trip computer functions.
|
- |
The CIM uses the value for the steering column lock.
|
- |
The ACC uses the value for activating recirculation at high temperatures and low speeds, to reduce the fan speed at high speeds, and to calculate the cabin temperature.
|
- |
The audio system uses the value for increasing the volume at high speeds.
|
- |
The BCM uses the value to automatically lock the doors after pulling off (certain markets only).
|
2. Immobilization
When the ignition is switched on, the CIM checks that the correct key is inserted in the ignition switch. A circuit built into the remote control part of the key sends a code by means of inductance to a coil in the ISM. The code is passed on via a C-cable to the CIM, which checks that it is correct. The CIM also checks that the right MIU, BCM and PDM are fitted in the car. These are all part of the car's "immobilizer environment" and continuously send an ID number over the bus. If the key and control module ID numbers are OK, the CIM will send a message for "Immobilizer OFF" on the bus. The ECM acts on this information by cancelling fuel shut-off, which is always activated whenever the ignition is turned on.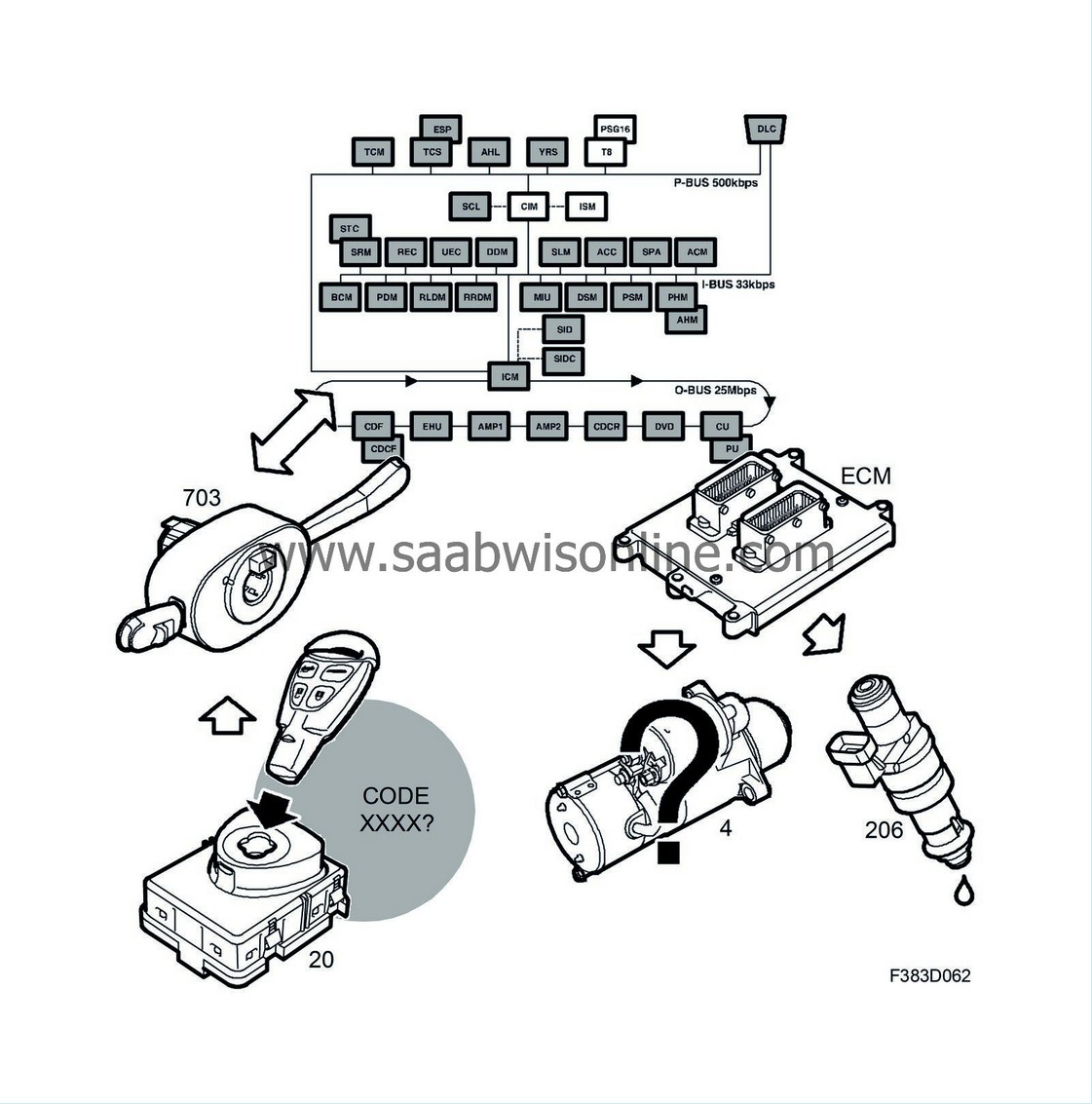
3. Steering column lock
Turning the ignition OFF locks the steering column. The CIM first checks that vehicle speed does not exceed 5 km/h. The problem here is that the TC/ABS or ESP and ECM provide the value for vehicle speed. These control modules are connected to the P-bus and there is no communication on the P-bus when the ignition is switched OFF. To solve this problem, there is a direct lead from the TC/ABS or ESP providing a wheel speed signal. The TC/ABS or ESP can read the wheel sensor values and transmit a speed signal since it has a separate +X feed (battery voltage with ignition switch ON or OFF).
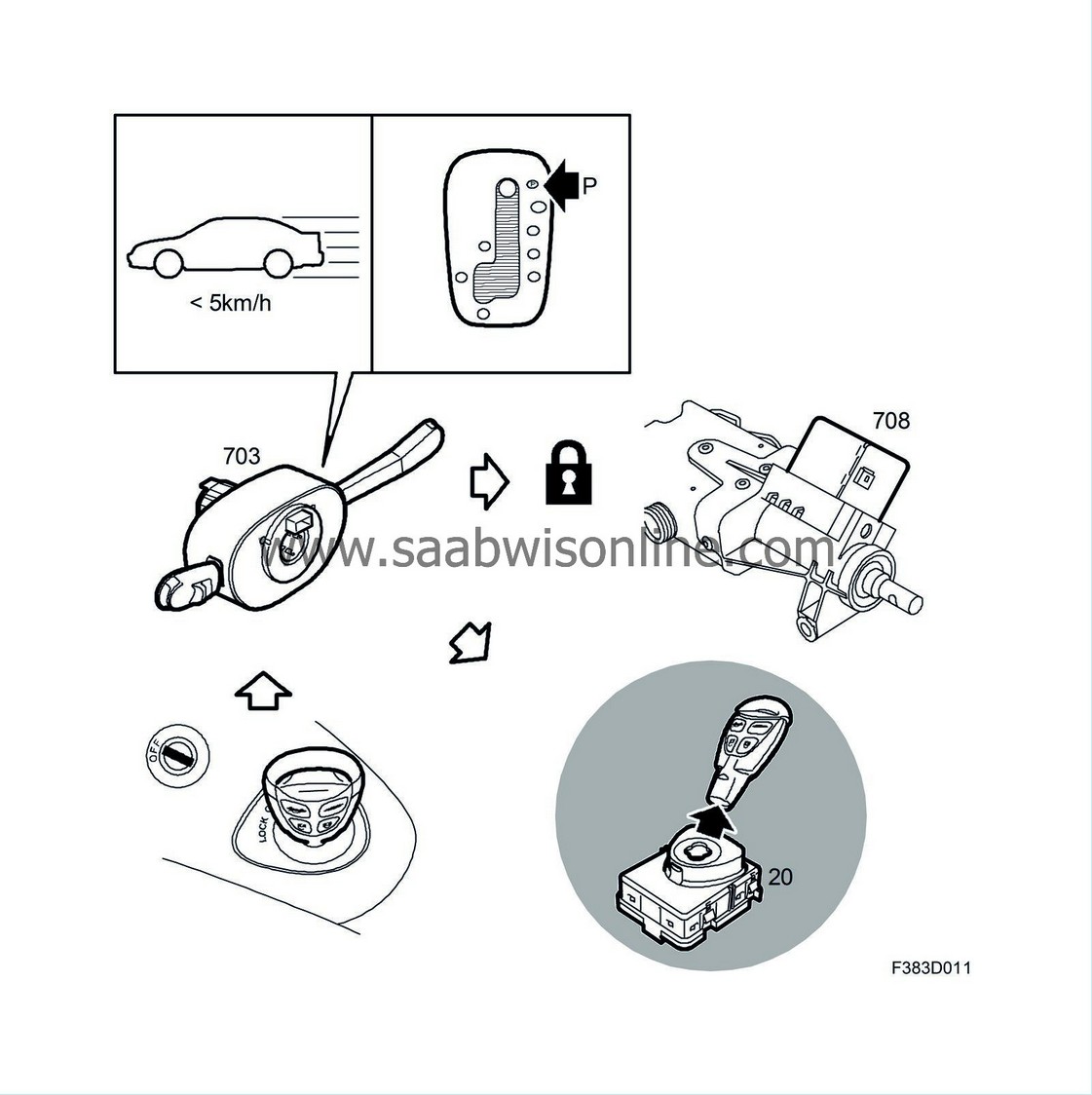
As well as checking that vehicle speed does not exceed 5 km/h, the CIM checks that the selector lever in cars with automatic transmission is in position P (I-bus from SLM). When these conditions are fulfilled, the CIM sends a signal on a C-cable to the ISM to release the key. The key can now be turned to LOCK and removed. Only now is the steering column locked.
When the key is inserted into the ignition switch, the steering column lock is released if the transponder is approved. If the car is parked in such a way that the steering shaft bears against the lock bolt, it may not be possible to release the lock. The CIM will in this case send a message on the bus that the ICM, via the SID, can instruct the driver to remove the key, turn the steering wheel and reinsert the key.
4. Central locking system
BCM contains all logic for the central locking system. When the unlocking button on the remote control is pressed, CIM receives the radio signal. CIM then activates the other I-bus control modules and transmits which button was pressed and how it was pressed (e.g. single press). BCM transmits the unlock command on the bus, at which time the four door modules (DDM, PDM, RRDM, and RLDM) unlock their respective door. The Rear Electronic Module (REM) unlocks the boot lid/tailgate and BCM unlocks the fuel filler flap.
4D
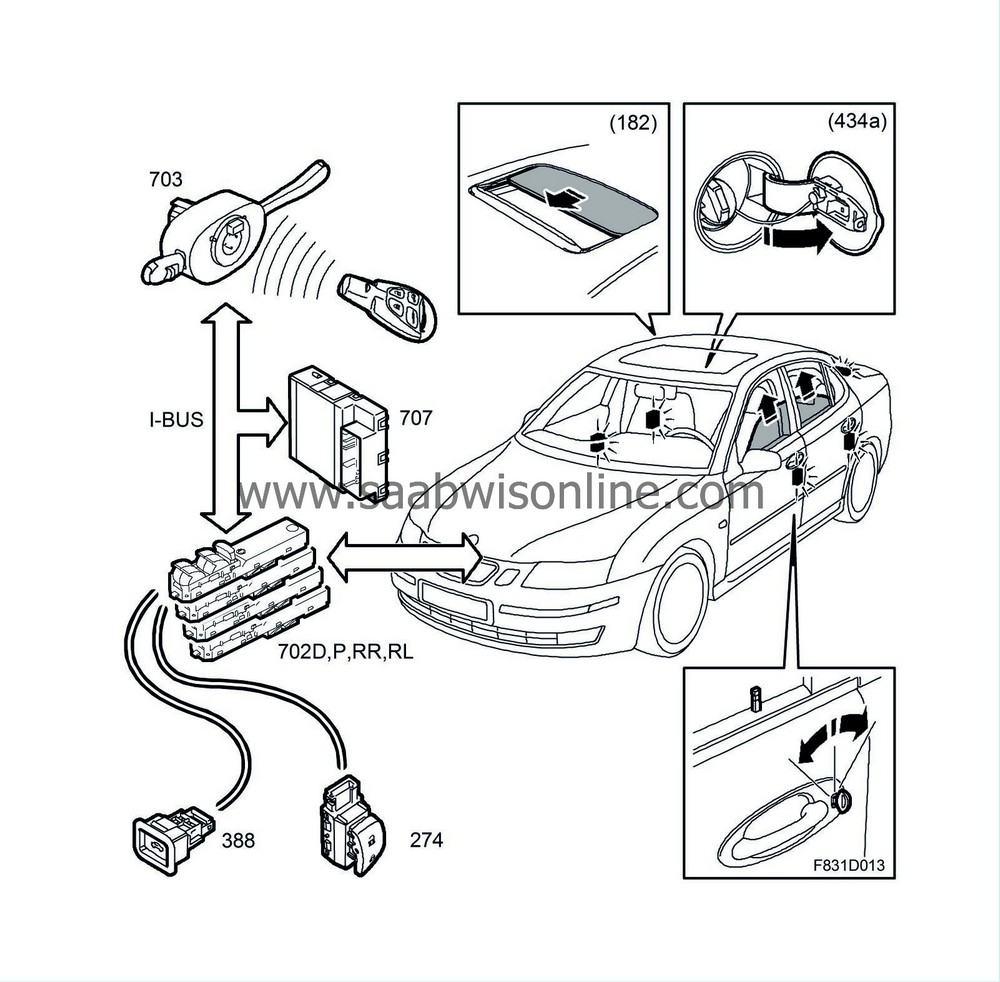
CV
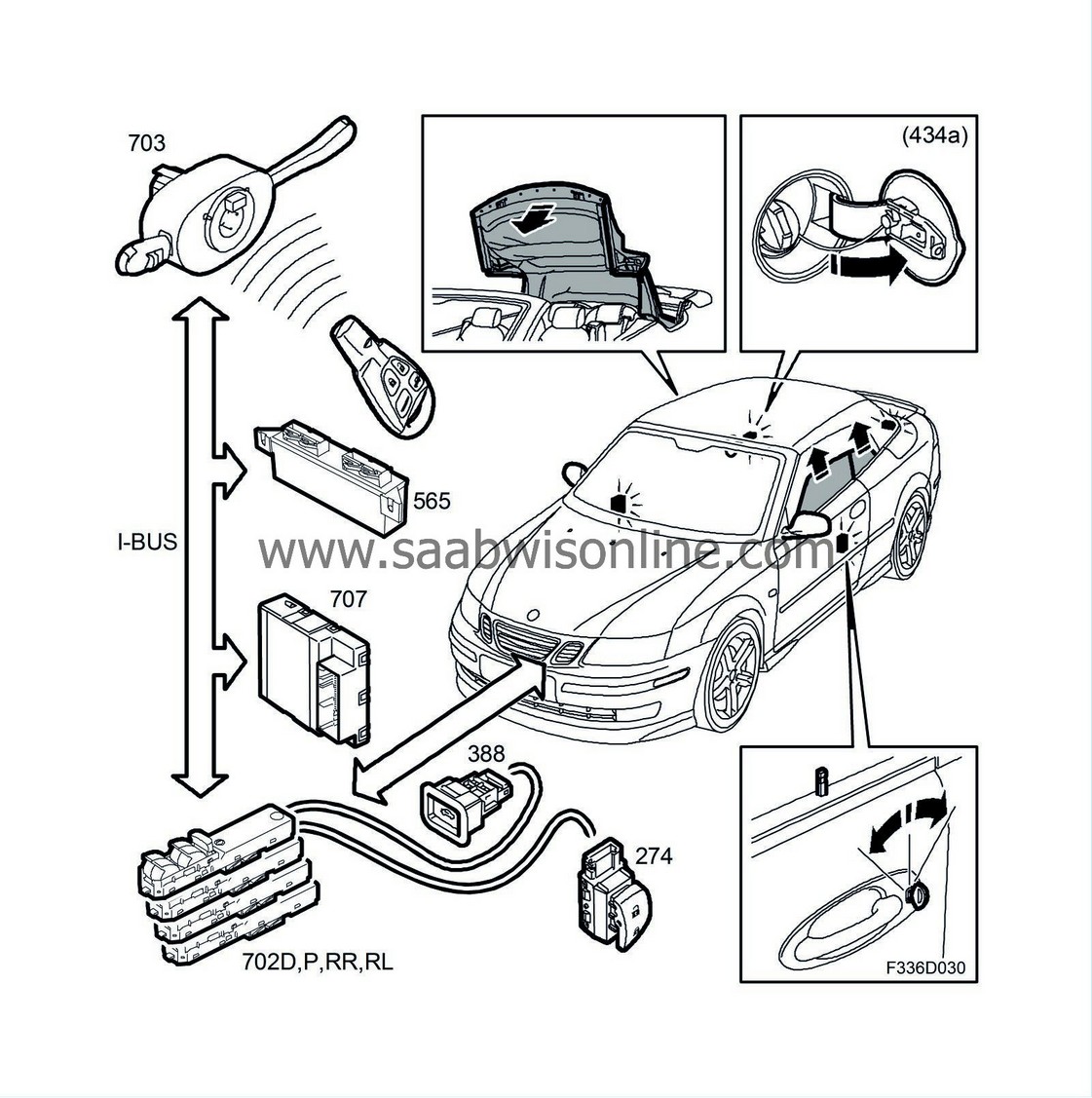
The BCM contains the central locking logic and can be programmed to unlock only the driver's door and fuel filler flap if the unlock button is only pressed once.