Detailed description, engine management function
Detailed description, engine management function |
Engine torque |
General
Torque control is used to make sure the engine delivers the right engine torque. ECM regulates the engine torque by regulating the injected fuel quantity.The following functions can request engine torque:
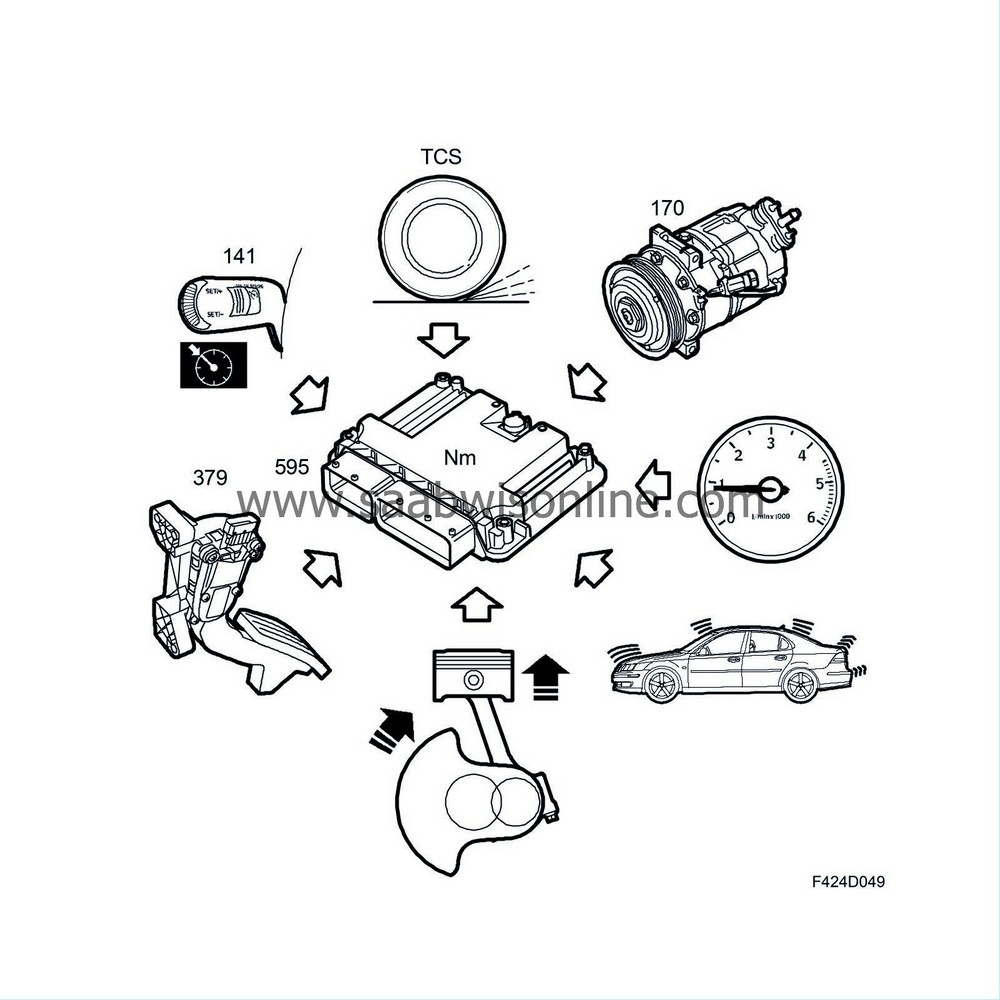
• |
Pedal request
|
• |
Cruise control
|
• |
TCS/ESP
|
• |
A/C and generator compensation
|
• |
Idling
|
• |
Active surge dampening
|
• |
Internal engine friction
|
But it is not always that the requested engine torque can be attained. This can be due to the maximum permitted engine torque for the engine speed in question has already been attained or that TCS/ESP has requested a reduction in torque. The following functions can limit engine torque:
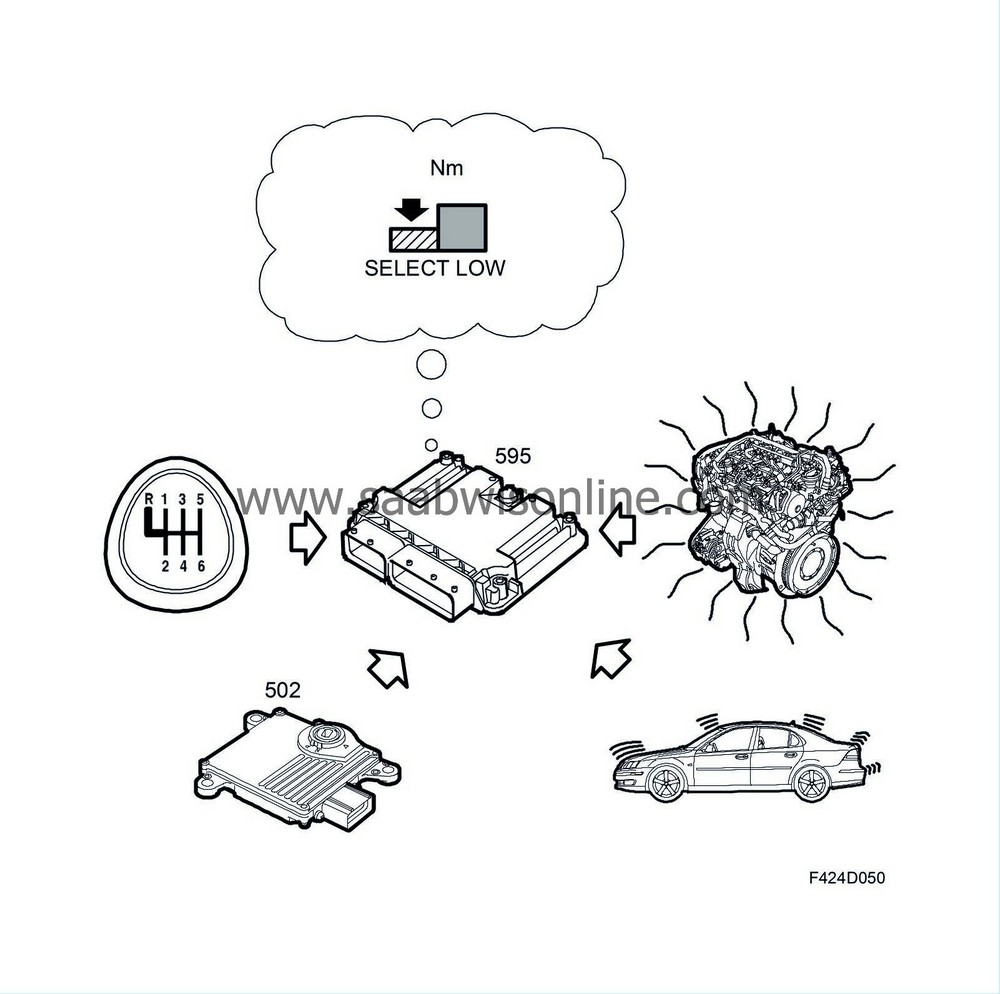
• |
TCM
|
• |
Manual gearbox
|
• |
Engine protection function
|
• |
Active surge dampening
|
• |
Brake
|
• |
Internal engine friction
|
These are coordinated to one common driving torque request, the function is used once the engine has started. To start the engine, there is a starting torque request. The resulting starting or driving torque request is converted to a fuel quantity request.
Pedal request
GeneralTwo potentiometers are integrated in the accelerator pedal bracket. Potentiometer 1 provides ECM with information on the driver's torque request in the form of a voltage signal 0-5V.
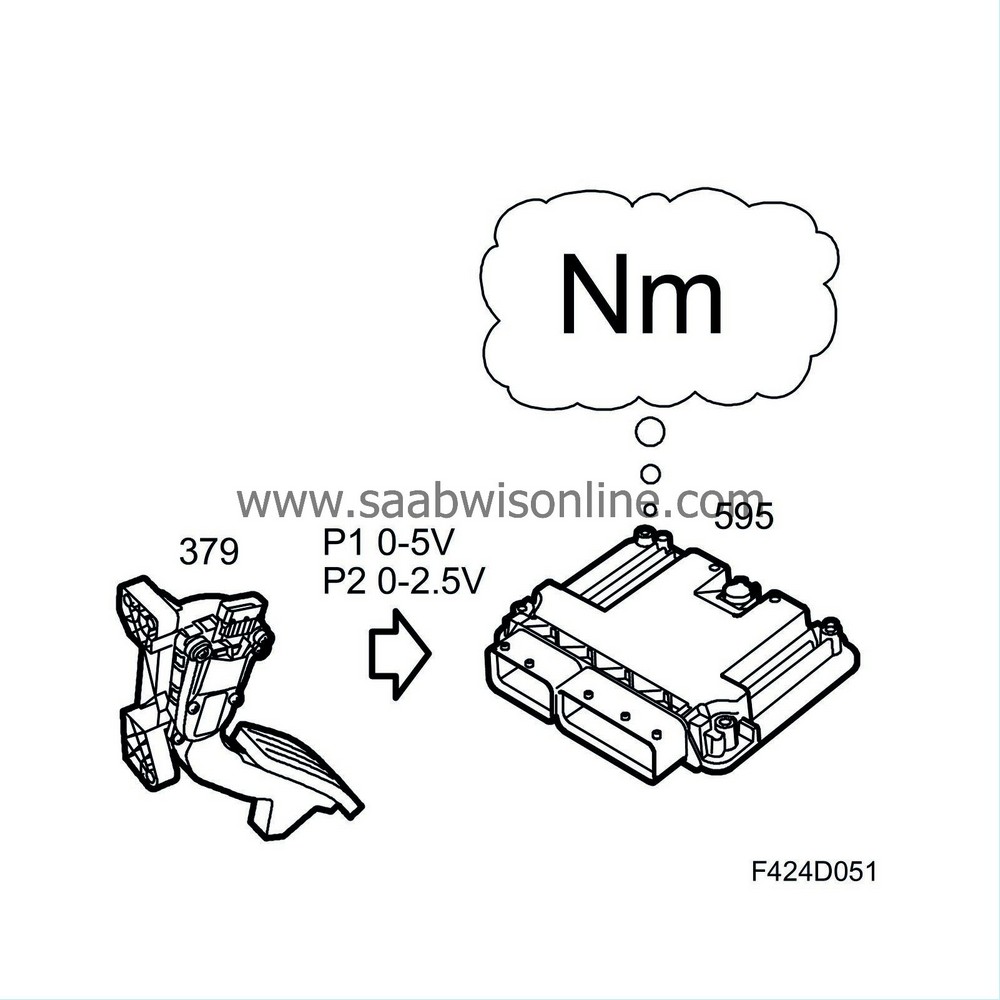
Potentiometer 2 is a safety potentiometer that provides ECM with information on the pedal position in the form of a voltage signal 0-2.5V. This voltage is used to ensure that information from potentiometer 1 is reliable.
Function
Pedal potentiometer 1 provides ECM with information on the drivers torque request. The pedal position together with the engine speed gives a requested torque using a matrix. The torque request varies between 0 Nm (idling) and a value that is somewhat greater then the maximum torque allowed for the engine.
Request from TCS/ESP
In case of wheelspin, TCS can request a reduction in engine torque (negative request) to counteract it. Likewise, ESP can request a reduction in engine torque if the car skids. TCS, but above all ESP, can request an increase in engine torque (positive request) to counteract a skid, for example.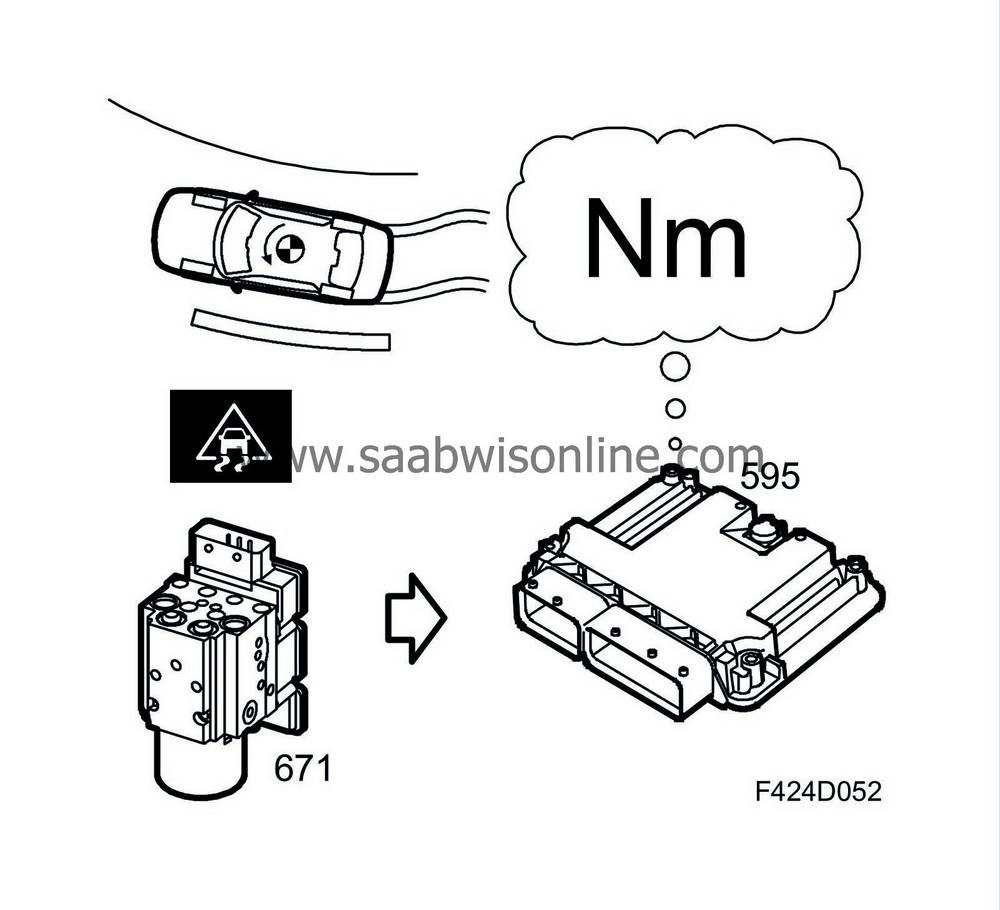
Request for A/C and generator compensation
Torque can be requested from this function in order to keep the specified engine torque independent from the prevailing load from the A/C compressor and generator. Consequently, this is a positive request.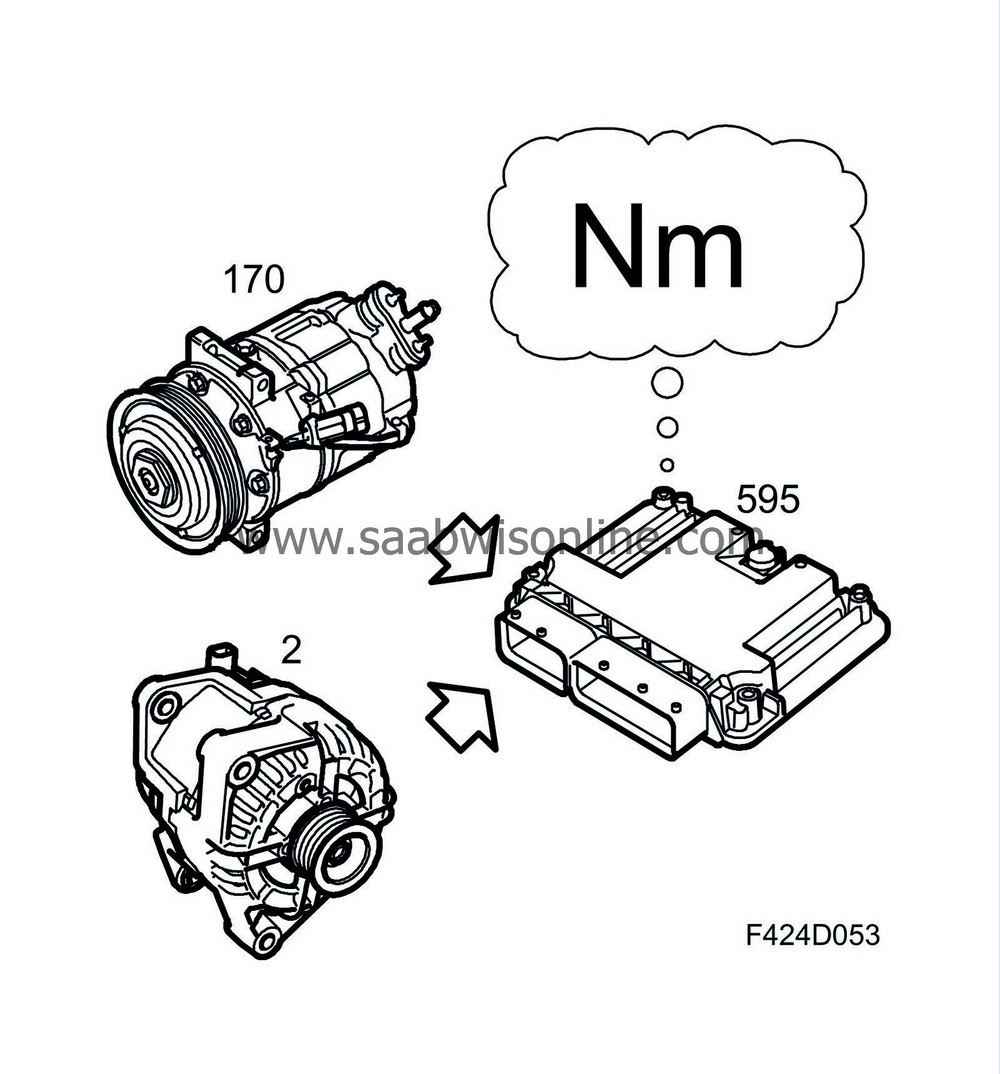
Compensation for AC
The relay for the A/C compressor is controlled by ECM, which also reads the prevailing pressure in the A/C system via pressure sensor (620). In this way, ECM can calculate the torque that must be added to compensate for the torque taken by the A/C compressor.Compensation for generator
The generator informs ECM of the prevailing load through a wire from generator connection L. In this way, ECM can calculate the torque that must be added to compensate for the torque taken by the generator.
Idle speed control
Idle speed control is used to regulate the engine torque so that the balance between the torque developed by the engine and the torque required to keep the engine and its auxiliary equipment running is maintained. Nominal idling speed with warm engine is 850 rpm.Function
With an idling speed exceeding the nominal, there will be an excess of engine torque and the idling function will then request a lower value until the nominal idling speed has been attained. When the idling speed is below the nominal value, there will be a torque deficiency and the idling speed will have to be increased to attain nominal idling speed.
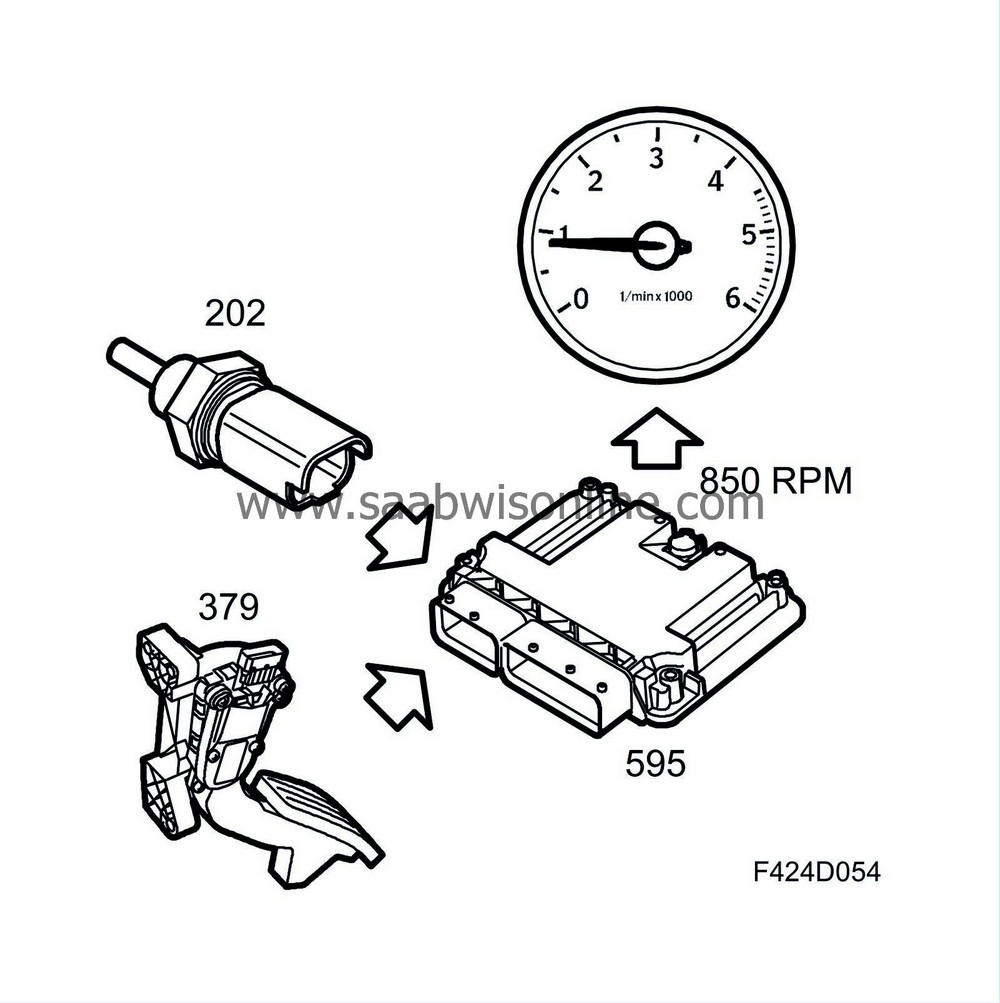
The nominal idling speed is dependent on the coolant temperature. The idling speed is higher for a cold engine.
Idle speed control is active when the accelerator pedal is not pressed.
Active surge dampening
A certain surging(oscillation) can occur during acceleration/deceleration. This is caused by sudden increases of engine torque in combination with a certain elasticity in the drive line and engine mountings.Function
The anti-surge function detects fluctuations in engine speed and dampens them by requesting an increase or decrease in torque. This will reduce or eliminate surging.
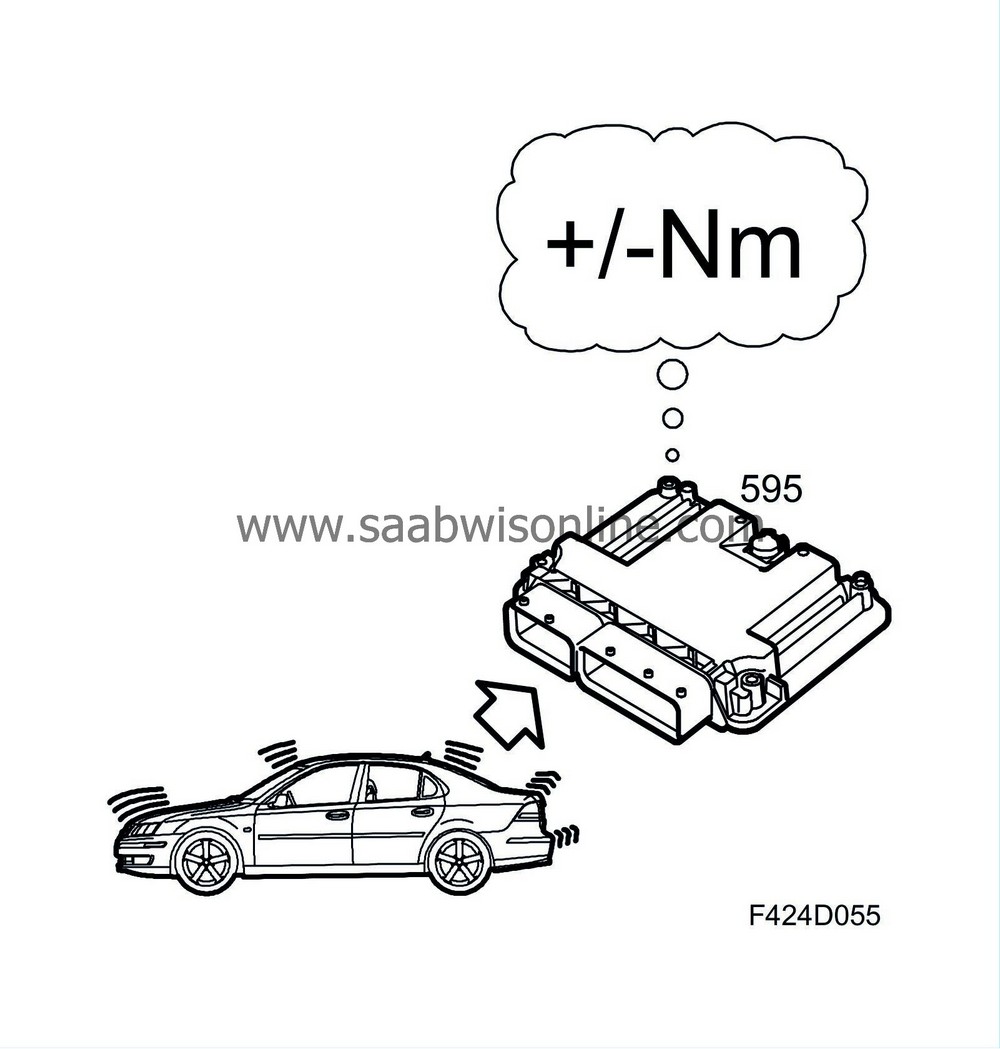
Internal engine friction
The engine has its own torque consumption that principally comprises its internal friction and pump losses. To compensate for this, the function will usually request torque.Function
The engine's internal torque consumption is mainly calculated from:
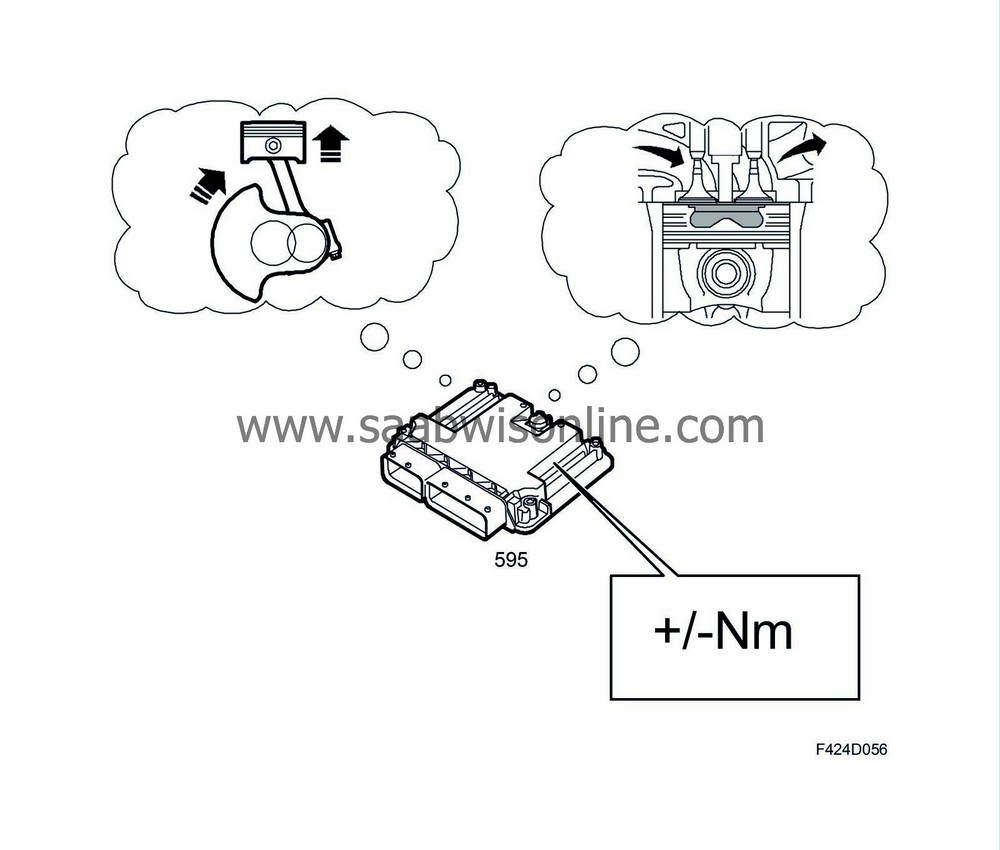
• |
Coolant temperature
|
• |
Oil temperature
|
• |
Engine speed
|
• |
Pressure drop across particle trap
|
• |
Calculated exhaust mass flow
|
The first three are principally engine friction, while the last two represent pump losses.
Torque limitation TCM
Engine torque must be limited occasionally to ensure smooth gear changing. In some cases, torque must be limited for reasons of strength/safety.Function
TCM determines the maximum engine torque that is permitted. For reasons of comfort, the engine torque will often be reduced when changing gear. Torque can also be limited for strength reasons. To protect the gearbox when stalling, TCM sends the maximum engine torque it allows on the bus.
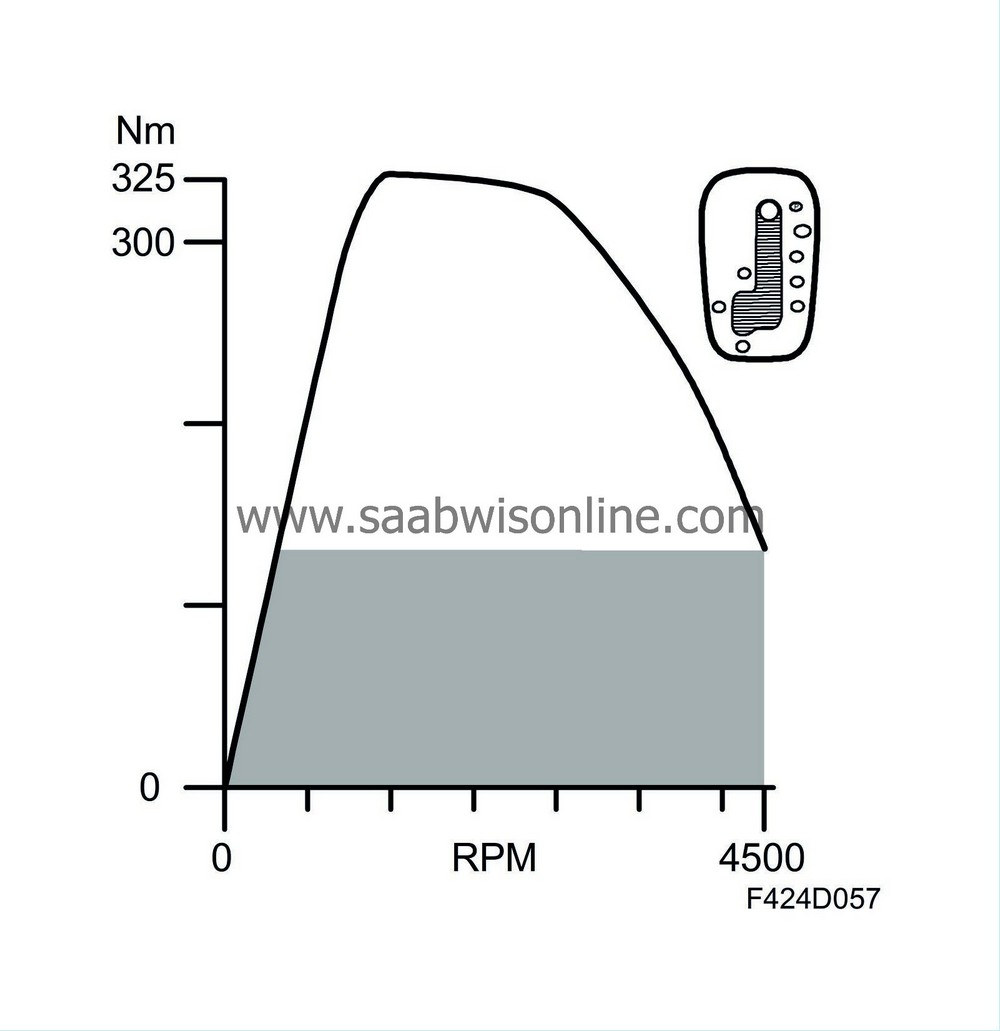
Torque limitation, manual gearbox
Engine torque is limited when reverse gear is engaged.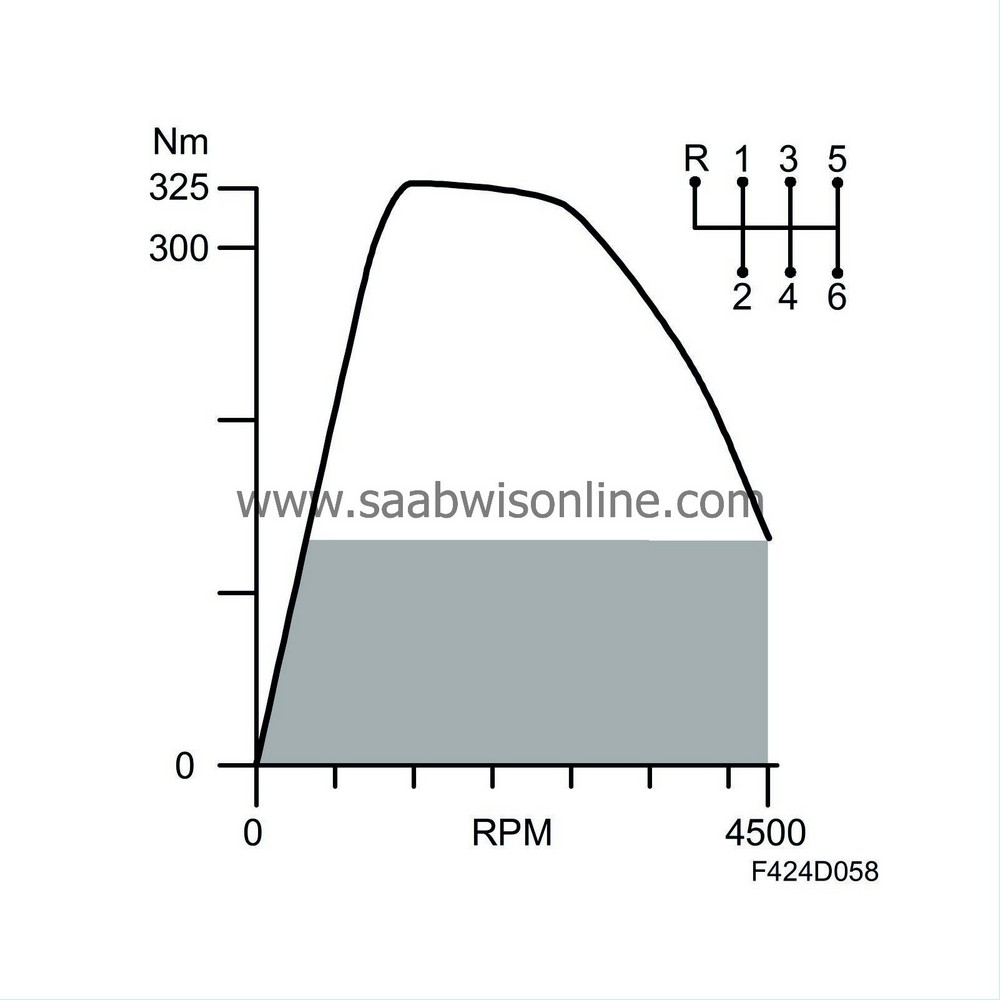
Torque limitation, braking
Maximum permitted engine torque must be limited when the brake pedal is depressed for reasons of durability.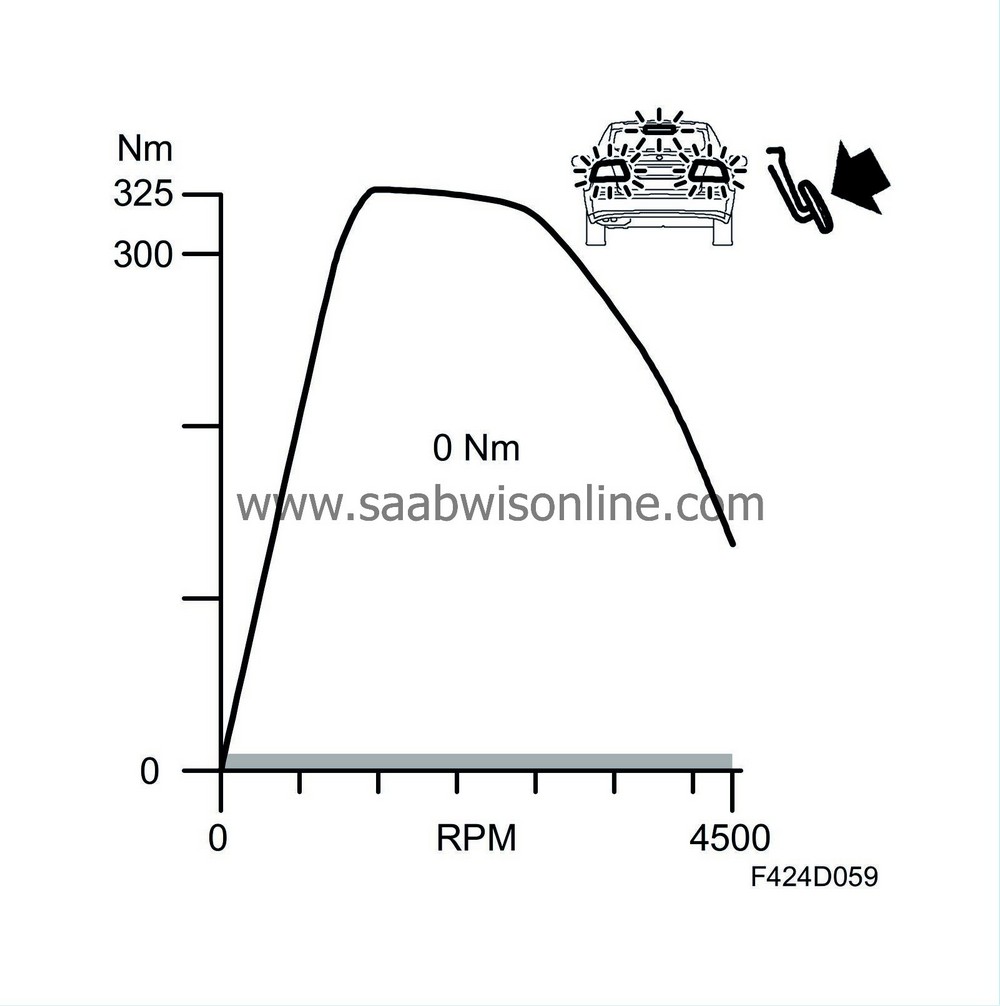
Fuel |
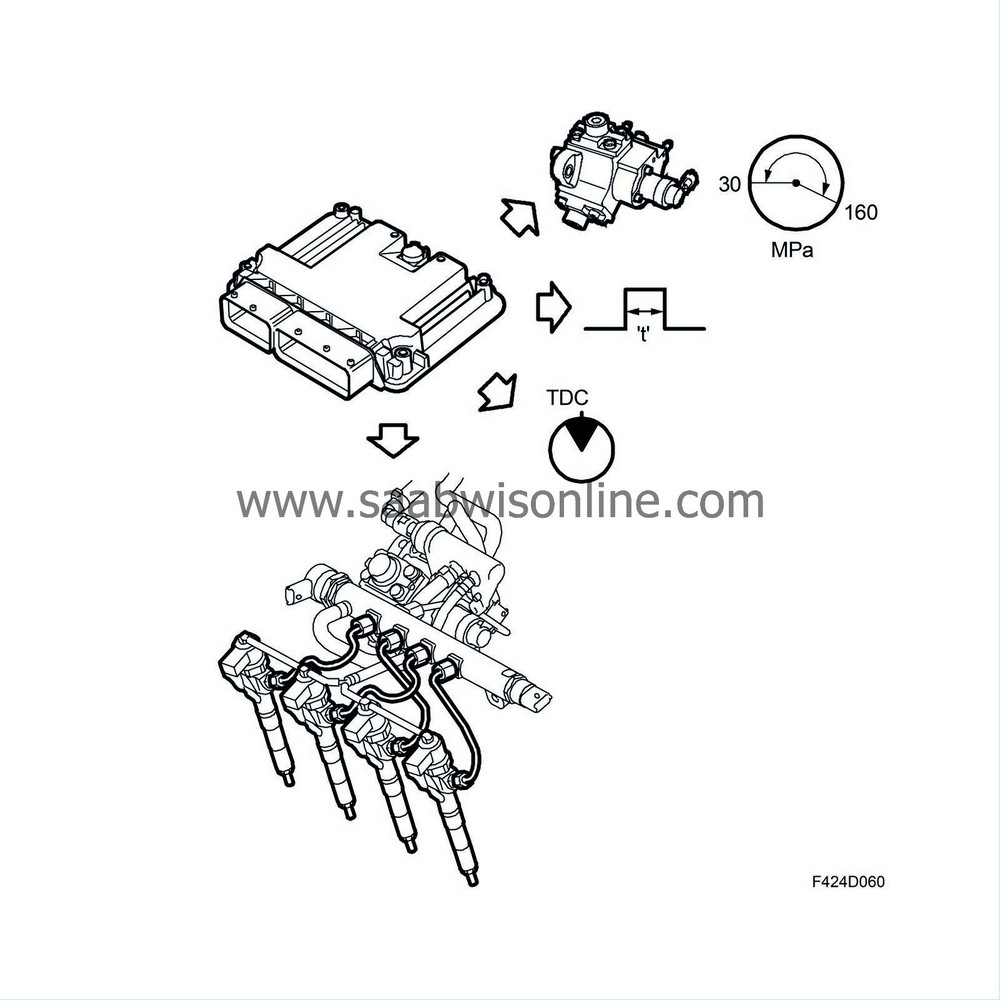
Requested engine torque is converted to requested injection timing, injection duration and fuel pressure for the four injectors.
But first, the requested engine torque must be converted to a fuel mass.
Injection time
Converting engine torque to fuelECM calculates the fuel mass corresponding to the requested engine torque using matrices and tables. By measuring the temperature of the fuel, ECM will correct for the difference in density between warm and cold fuel.
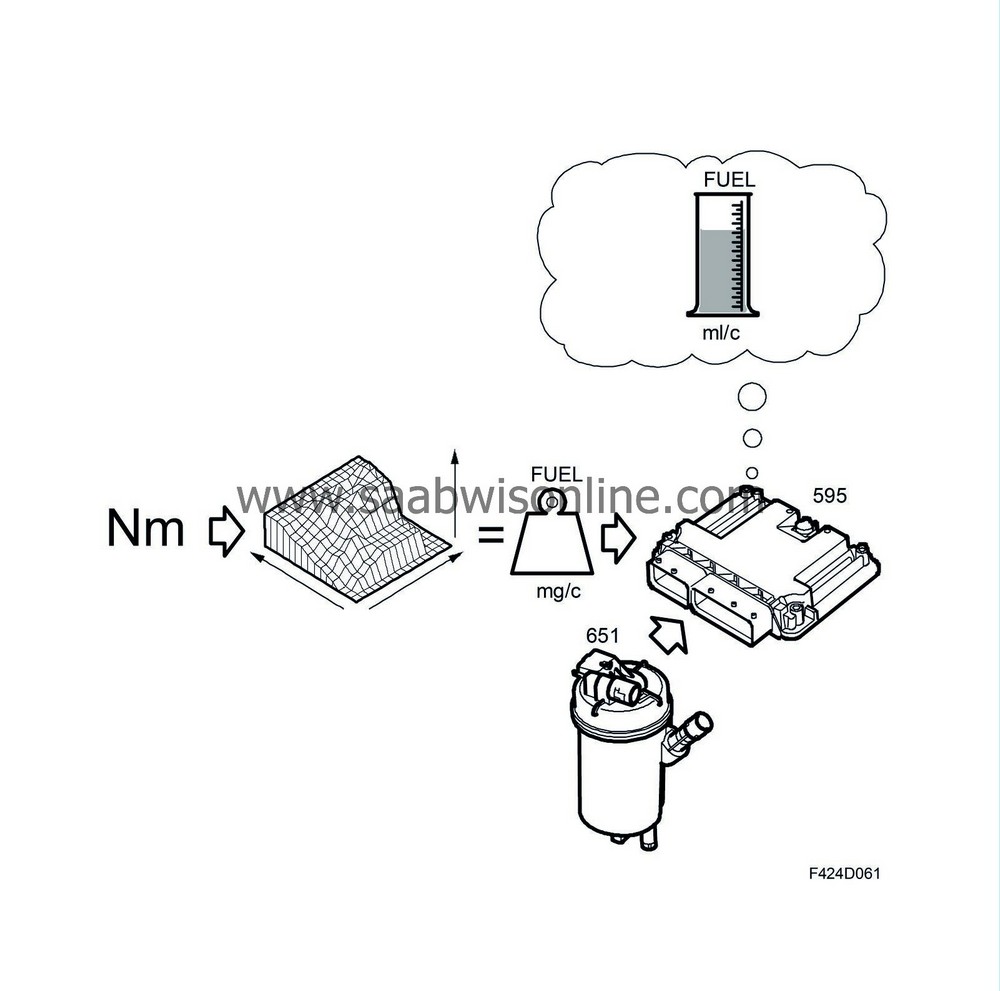
So this is the fuel mass to be added to the engine per combustion. The value is converted from fuel mass to fuel quantity (fuel volume).
This value is then transferred to the cylinder balancing function where it is compensated by adding or subtracting fuel.
Cylinder balancing
GeneralThe objective of the cylinder balancing function is to balance the combustion pulses from each cylinder so that the engine will run smoothly and consequently reduce vibration. This is done by adding or subtracting fuel.
Function
When idling, as the injected fuel quantity is relatively small, this is done to compensate for the differences in the amount injected into each cylinder and for the differences in the efficiency of each cylinder. When running above idling speed, compensation is made mainly due to the difference in efficiency of each cylinder. This is done by calculating and changing the injected amount for each cylinder individually.
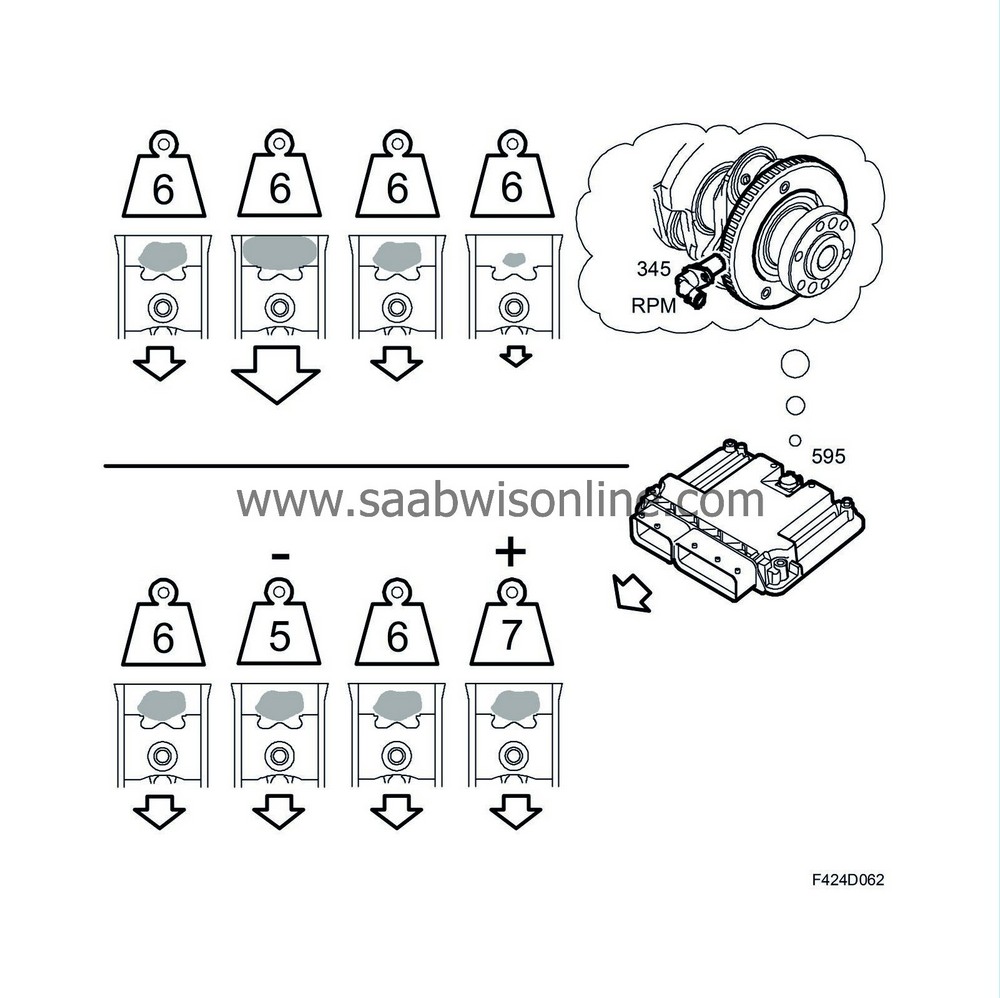
ECM measures the crankshaft motion after each power stroke and if it is accelerating more vigorously after ignition in e.g. cylinder 2, the fuel quantity in this cylinder will need to be reduced. When ignition is to take place next in this cylinder a calculation will be ready for a compensation quantity, in this case negative. This compensation quantity is adjusted so that later combustion will give the same power pulse after combustion as the other cylinders.
The total value is sent to the smoke limitation function.
Smoke limitation
GeneralThe objective of the smoke limitation function is to determine the maximum fuel quantity that can be injected without exceeding the smoke limit. Smoke limitation will begin when there is not enough air mass to obtain a smoke free combustion.
Function
Based on engine speed and air mass per combustion, the maximum fuel quantity is calculated that can be injected without exceeding the smoke limit. This value will act as the upper limit for the fuel quantity that can be injected.

If the value for the fuel quantity from the conversion from engine torque exceeds the smoke limitation function fuel quantity, the fuel quantity will be limited. This involves a limitation of engine torque. The value is sent on to the shut-off function.
Shut-off function
GeneralThis function can set the fuel quantity to 0, which will stop the engine. This is done if +15 is missing or if a safety critical fault occurs. During normal running, this function will only send the value on to the calculation for injection timing.
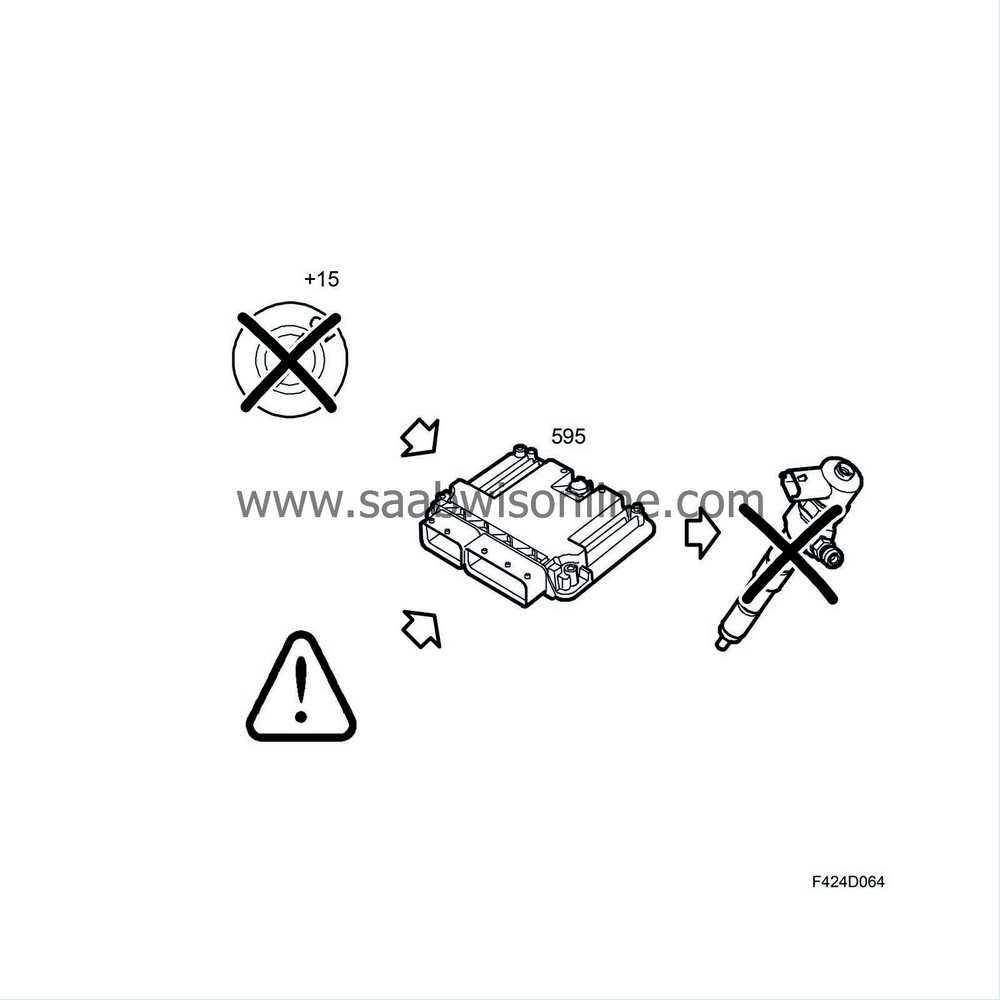
Injection
Injector opening duration, basic durationFuel volume/combustion is converted to time during which the injector must be open depending on the injector flow at the prevailing differential pressure.
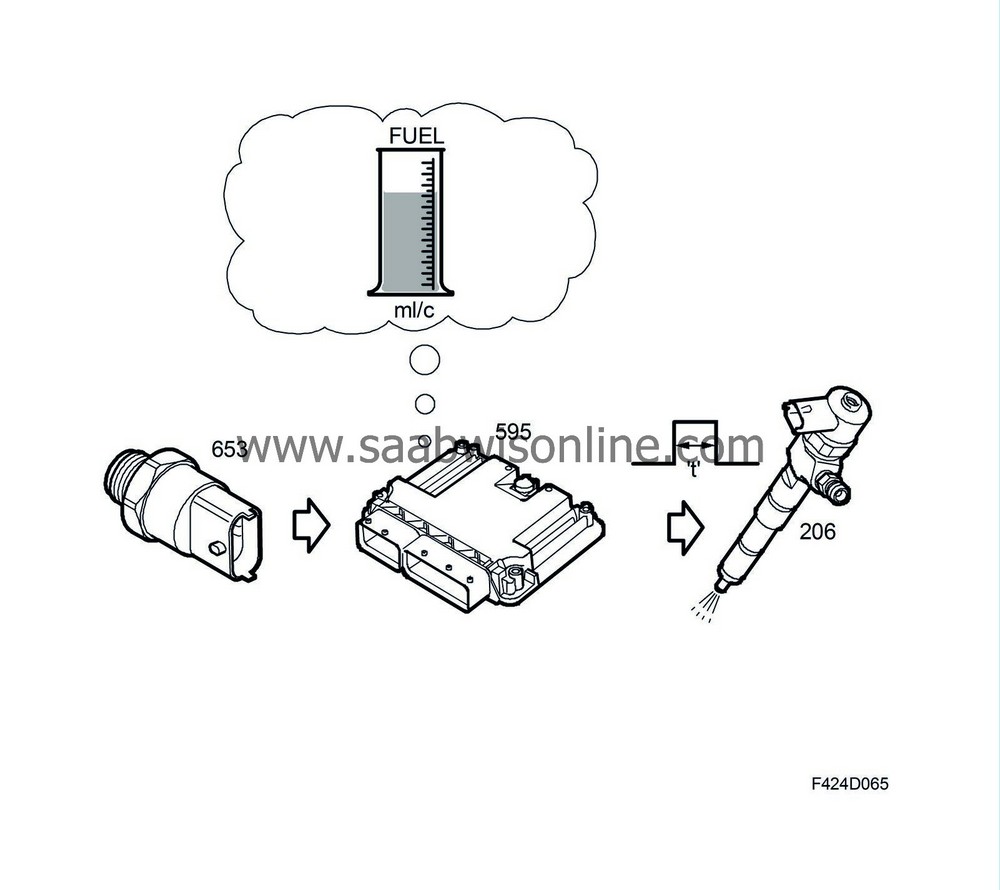
The pressure in the fuel rail is measured by the fuel pressure sensor (653).
Injection request from other functions
A request for injection can also come from the pilot injection and regeneration of particle trap functions.
Pilot injection
To reduce engine noise, "diesel knocking", at low coolant temperatures, the pilot injection function is used. This means that a small amount of fuel is injected just ahead of the main injection. The function is active when the coolant temperature is below +60°C. It will be turned off at high engine speeds.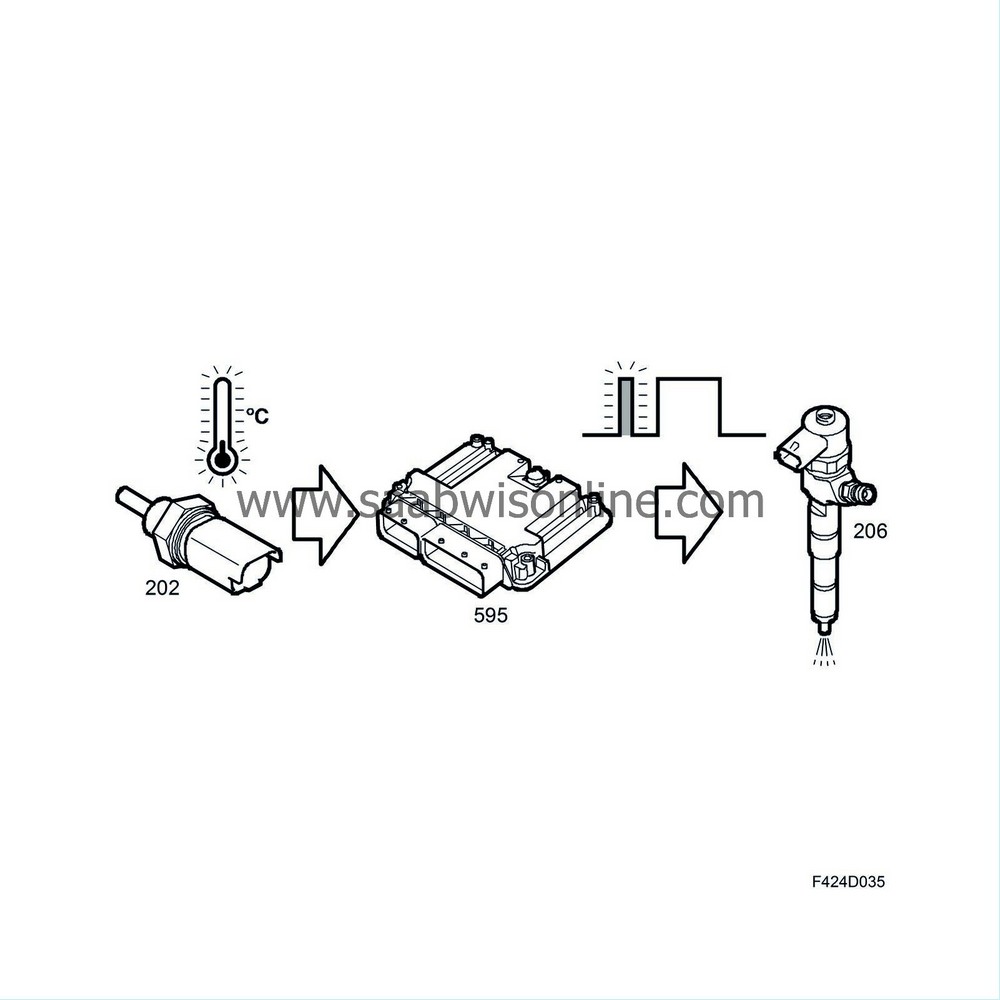
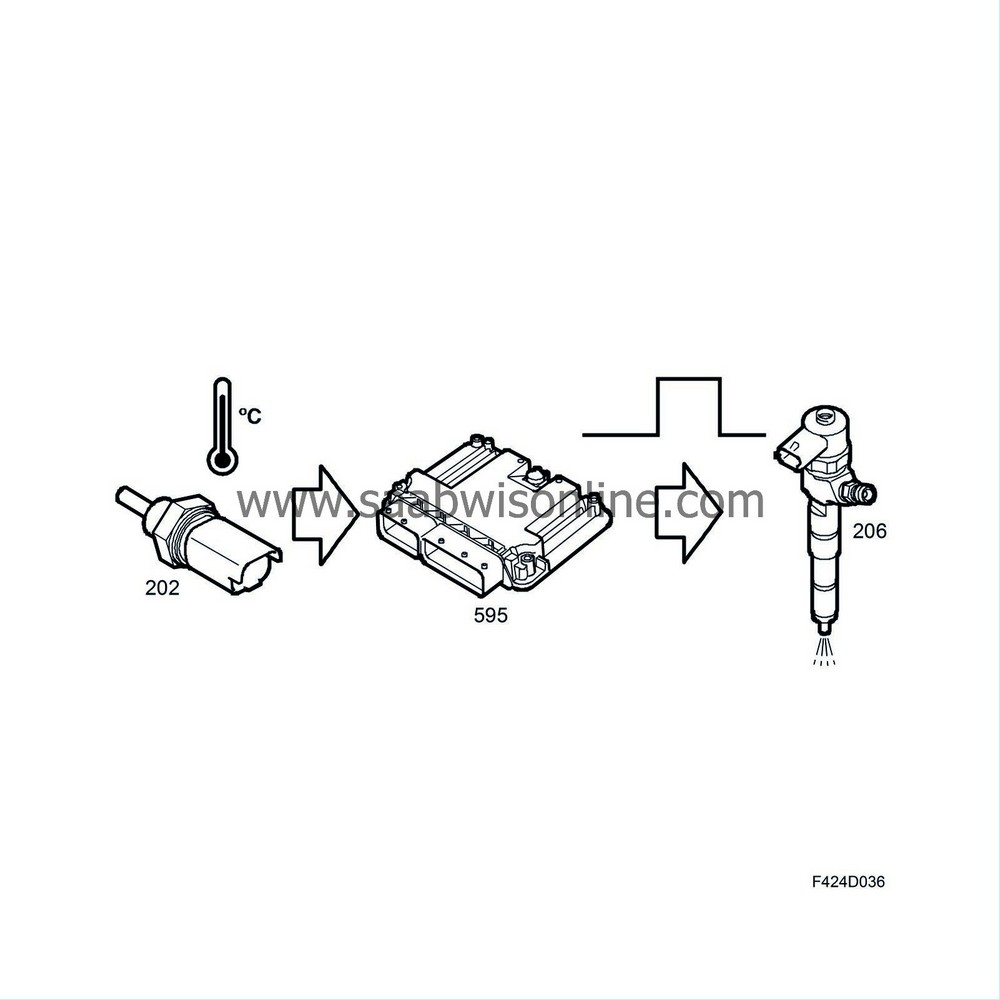
Diesel knocking arises when the injected fuel is ignited rapidly. The time between the fuel being injected into the combustion chamber and ignition is called ignition lag. In principle, the ignition lag should be kept as short as possible and is mainly dependent on the cetane number of the fuel, the temperature in the cylinders and how well the fuel is distributed during injection. A long ignition lag means a relatively large amount of fuel will be injected into the cylinder before the ignition. This gives rise to a violent pressure increase in the cylinder, resulting in noise and rough engine running.
Fuel with high cetane number consequently gives a shorter ignition lag as well as high temperatures in the combustion chamber during the injection. A good distribution of fuel is achieved through a combination of nozzle type and the high fuel pressure.
When the engine is running with low coolant temperature, heat losses from the cylinders to the surroundings are high. This means the temperature of the air at the time of injection is not that high. The result is a long ignition lag and more "diesel knocking".
By injecting only a small amount of fuel that ignites just before the main injection, the temperature in the combustion chamber will rise considerably. When the main injection then starts, there will only be a short lag. This gives less engine noise.
Regeneration of particle trap
When regenerating the particle trap, its internal temperature must rise to at least +550°C for the soot to burn. At around 160 degrees after top dead centre, a small amount of fuel will be injected into the cylinder. As this fuel is injected so late (the piston is almost at bottom dead centre and the exhaust valve is open), this fuel will not contribute to the torque. The exhaust temperature will not increase appreciably either as it is simply enriched with HC (hydrocarbon). This will start a reaction in the front catalytic converter so that the temperature rises. Once the hot gases enter the particle trap, they will react with the catalytic converter in the particle trap, whereby the temperature will increase further. The soot in the particle trap can now be burned.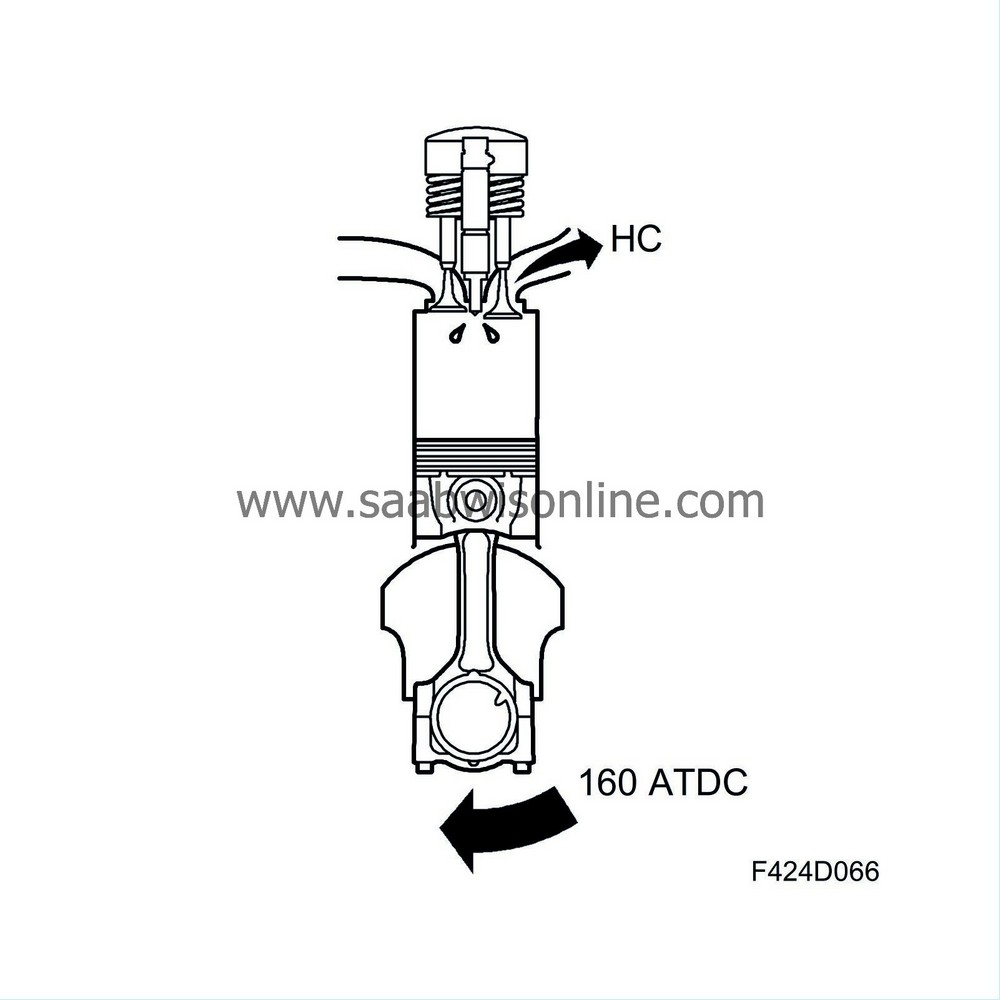
Compensation for delay in injector
Compensation must be made for the time from when the power stage in ECM has been activated until the injector opens and fuel is injected.
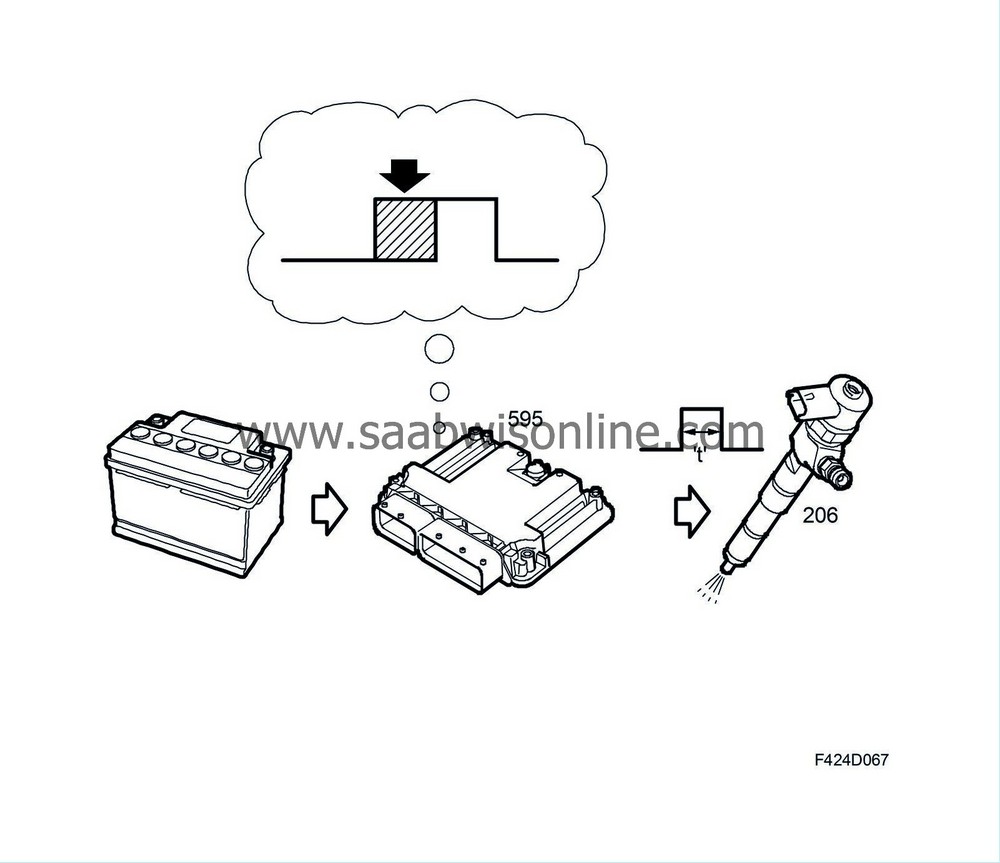
Delay time is system dependent.
Compensation for shock wave
As the injectors open, a shock wave forms in connecting pipes and fuel rail. ECM must compensate for this phenomenon or the wrong amount of fuel will be injected.
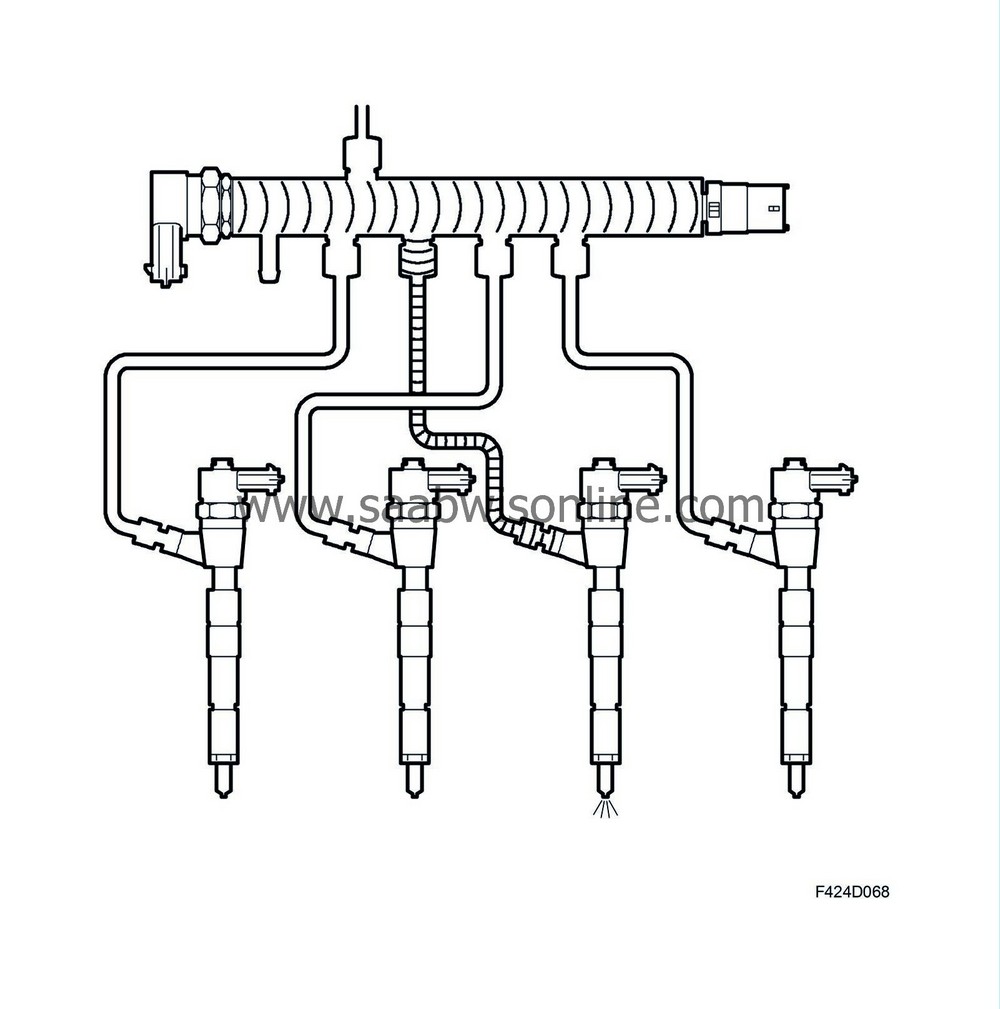
Compensation is individual for each cylinder and mainly takes into account the pressure and temperature of the fuel.
Activating the injectors
ECM activates the injector in question at the calculated time and keeps it open for the calculated injection timing.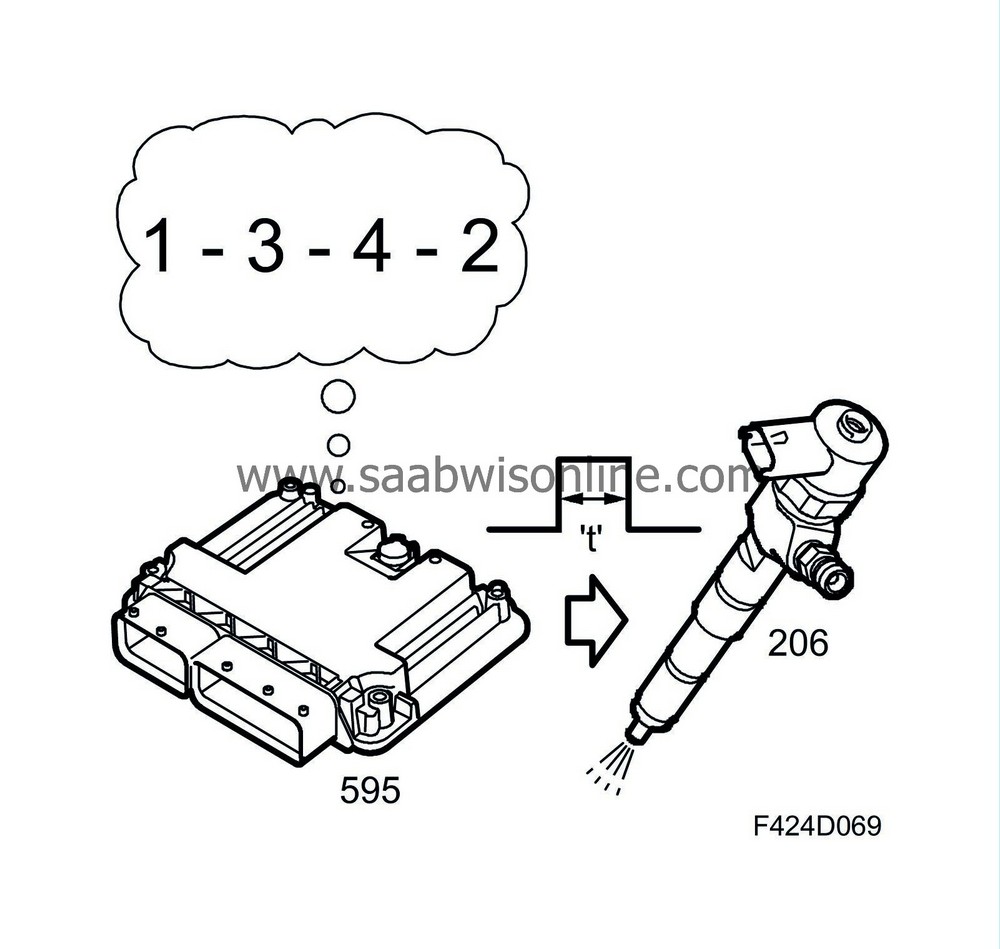
Injection duration
Injection duration is regulated depending on the engine speed and load. The objective of this regulation is to attain the right build-up of the combustion pressure.
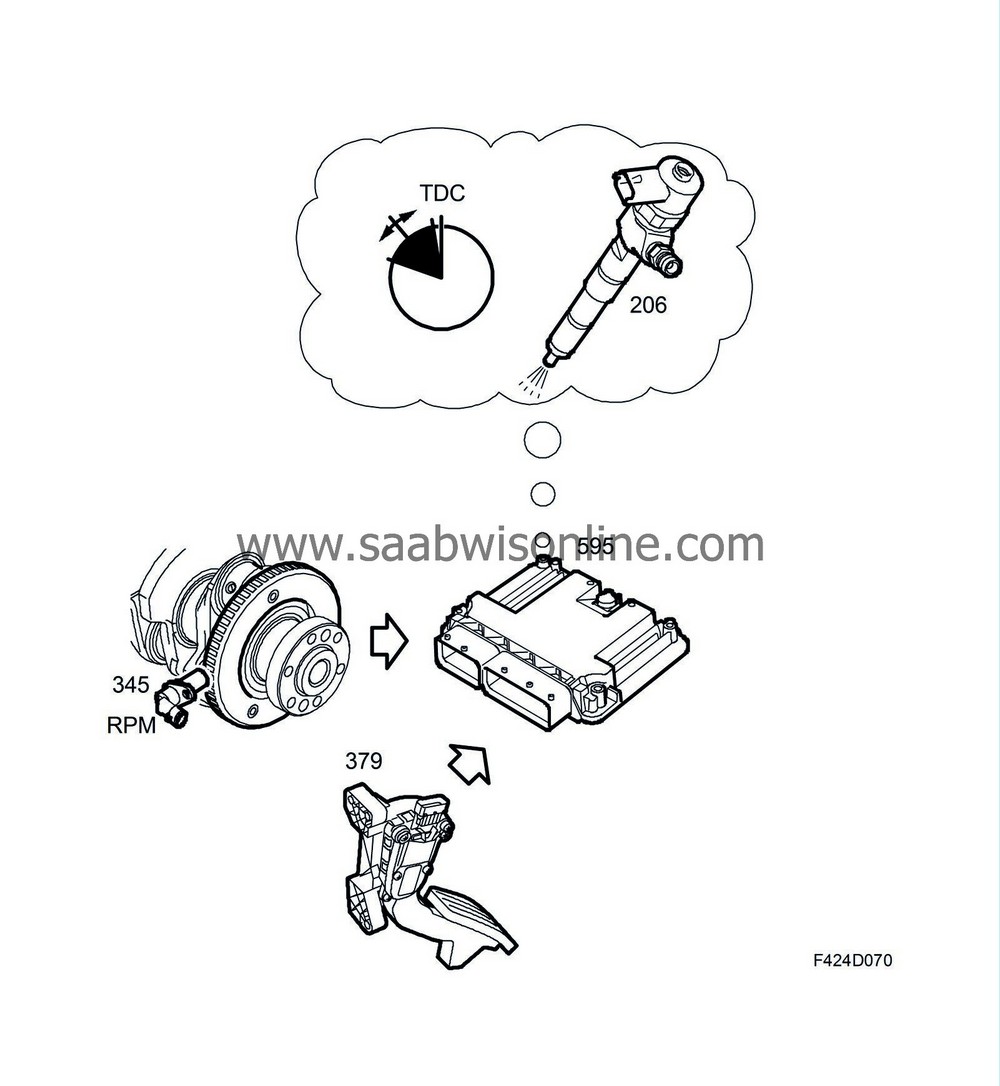
The injection duration indicates the duration of the injection in crankshaft degrees, not to be confused with the injection timing.
Fuel pressure
GeneralFuel pressure varies between 40 MPa and 160 MPa (400-1600 bar) depending on the prevailing conditions. The pressure is regulated using two valves, one on the high-pressure pump and one on the fuel rail. ECM checks that the requested pressure is attained using a fuel pressure sensor mounted on the fuel rail.
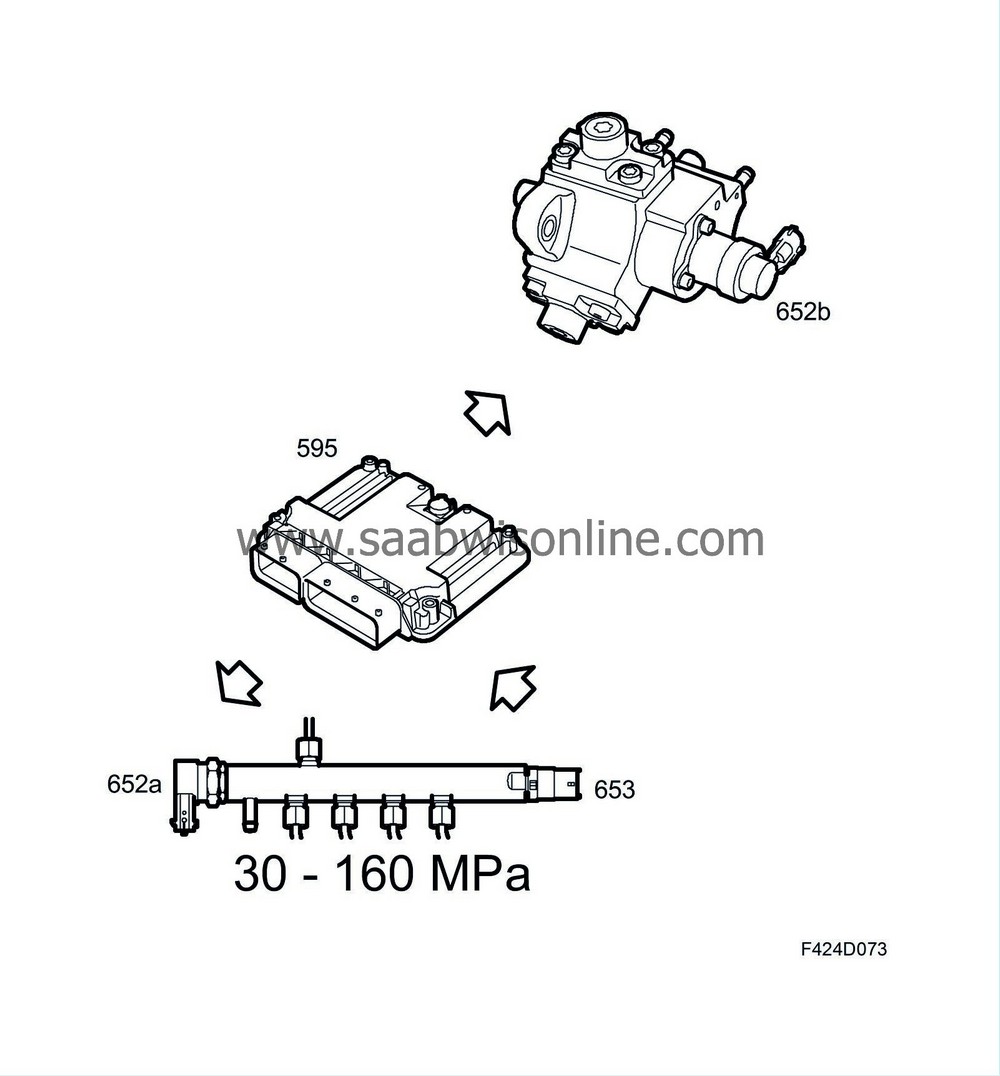
General function
As the engine's fuel requirements change over a large range, the fuel pressure delivered by the high-pressure pump to the fuel rail must be regulated. This is done by the fuel quantity control valve (652b) and the fuel pressure control valve (652a) and is measured by the fuel pressure sensor (653).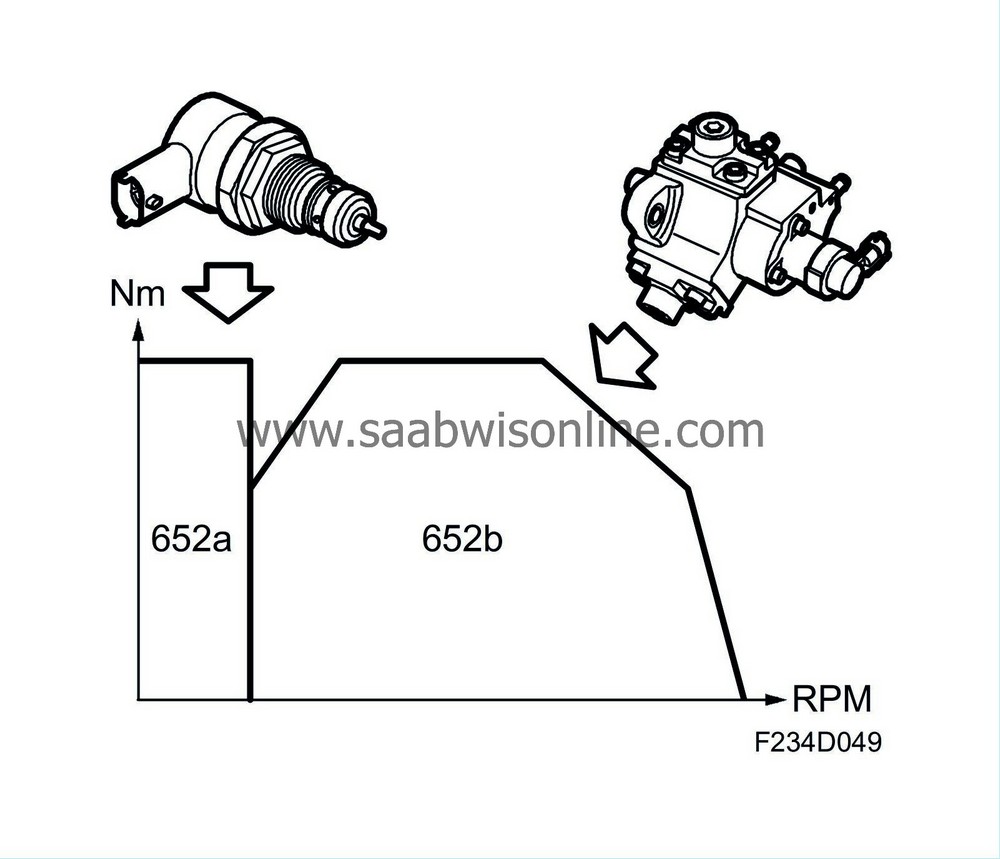
Function when starting and low engine speed
When starting the engine, the high-pressure pump is allowed to deliver as much as it can to ensure quick and reliable starting. The fuel control valve (652b) is then fully open and fuel pressure regulation is then handled by the fuel pressure control valve (652a).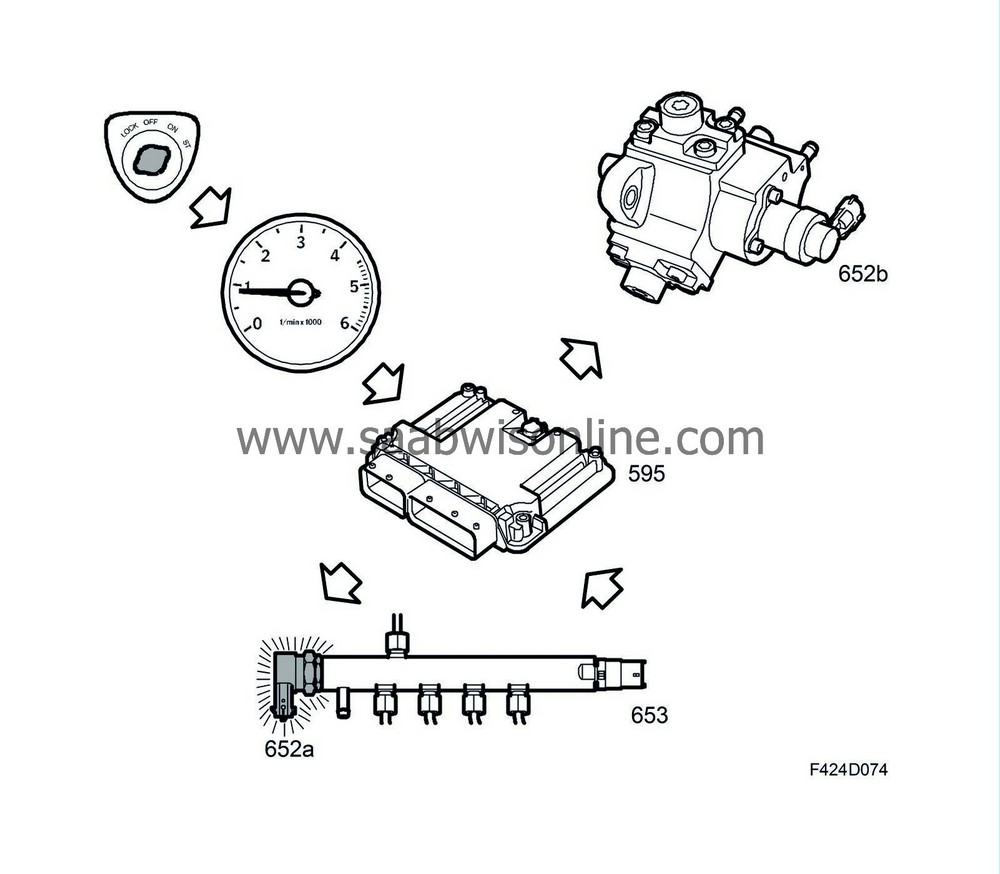
Function if engine speed just above idling
When the engine is running just faster than idling, the fuel pressure is regulated with the fuel quantity control valve (652b) and the fuel pressure control valve (652a). By allowing both valves to work it is possible to prevent pulsations caused by uneven fill factor in the high pressure pump element. The pump is allowed to work at a relatively high fill factor and the fuel pressure control valve (652a) dumps fuel so that the correct fuel pressure is attained.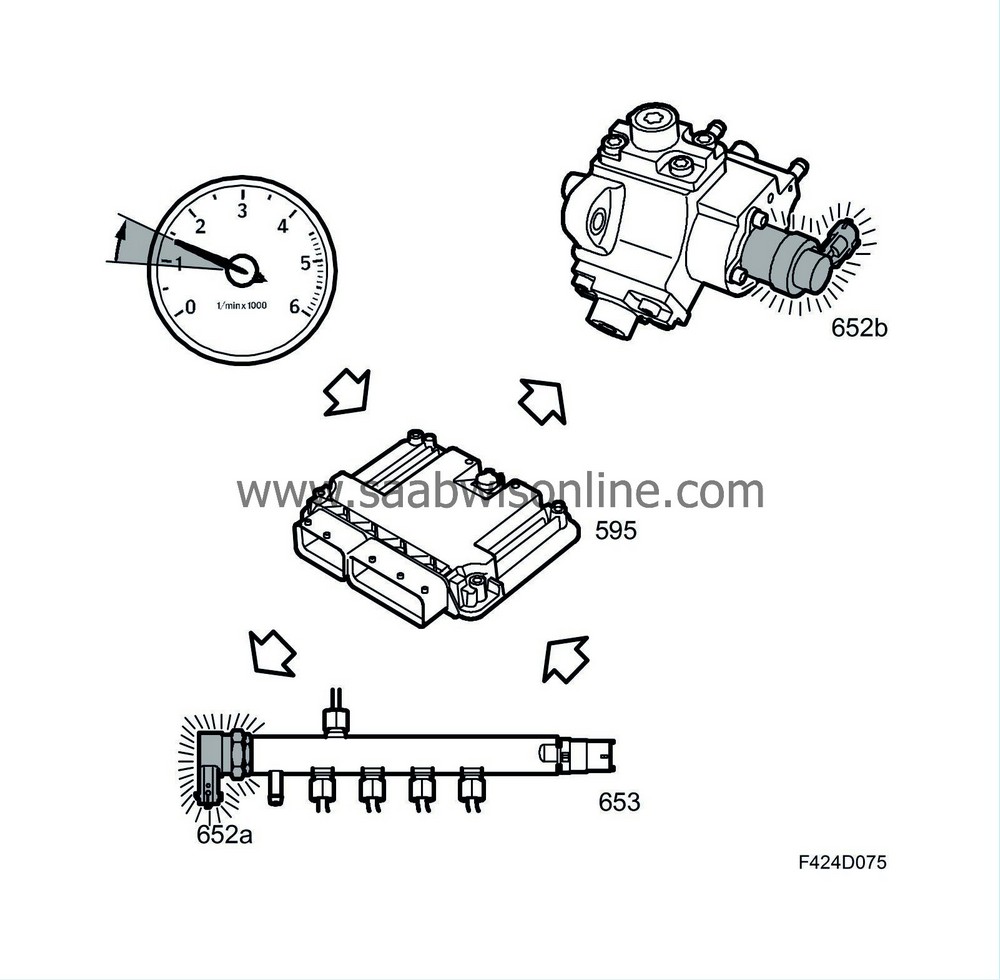
At a slightly higher engine speed fuel pressure regulation is handled by the fuel control valve (652b). By not allowing the pump to run at full fill factor, the torque requirement for the high-pressure pump will be reduced. A reduced torque requirement gives a lower fuel consumption as the load on the engine is lower. If rapid drops in pressure are required, the fuel pressure control valve (652a) will dump fuel to reduce pressure quickly. Depending on the driving conditions, the fuel pressure can go up to 160 Mpa (1600 bar).
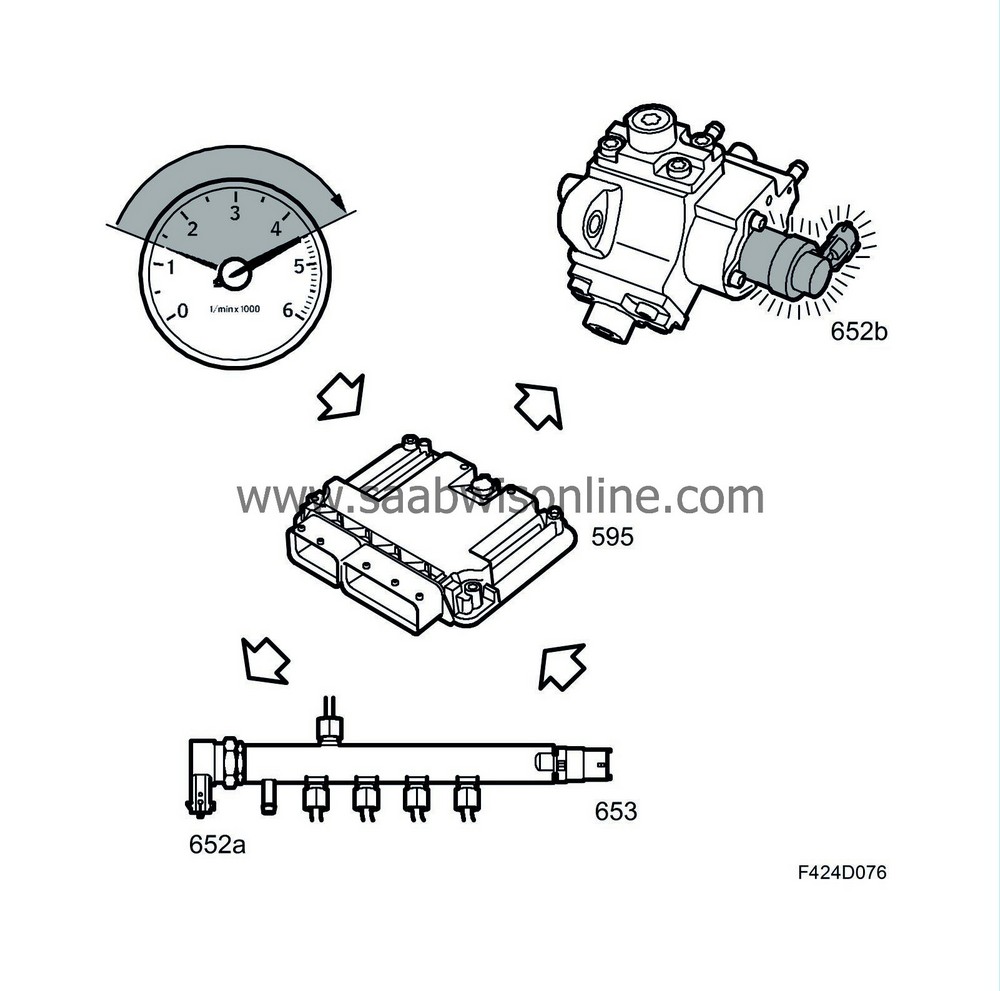
Calculating fuel consumption, general
The volume is accumulated for each combustion and the value sent on the bus. The main instrument unit uses the value to correct the tank gauge and the information display uses it to calculate the petrol consumption.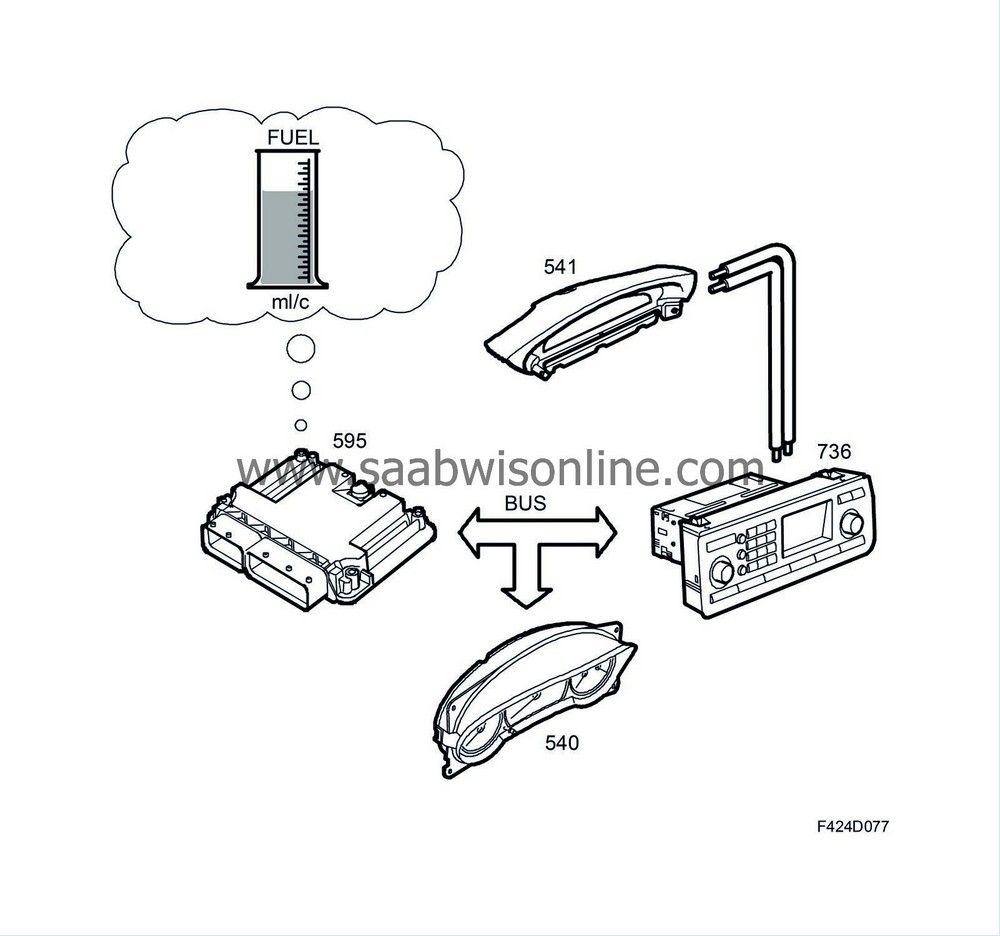
Air |
General
The function is used to coordinate the engine's air requirements. The following sensors are used primarily for this purpose:
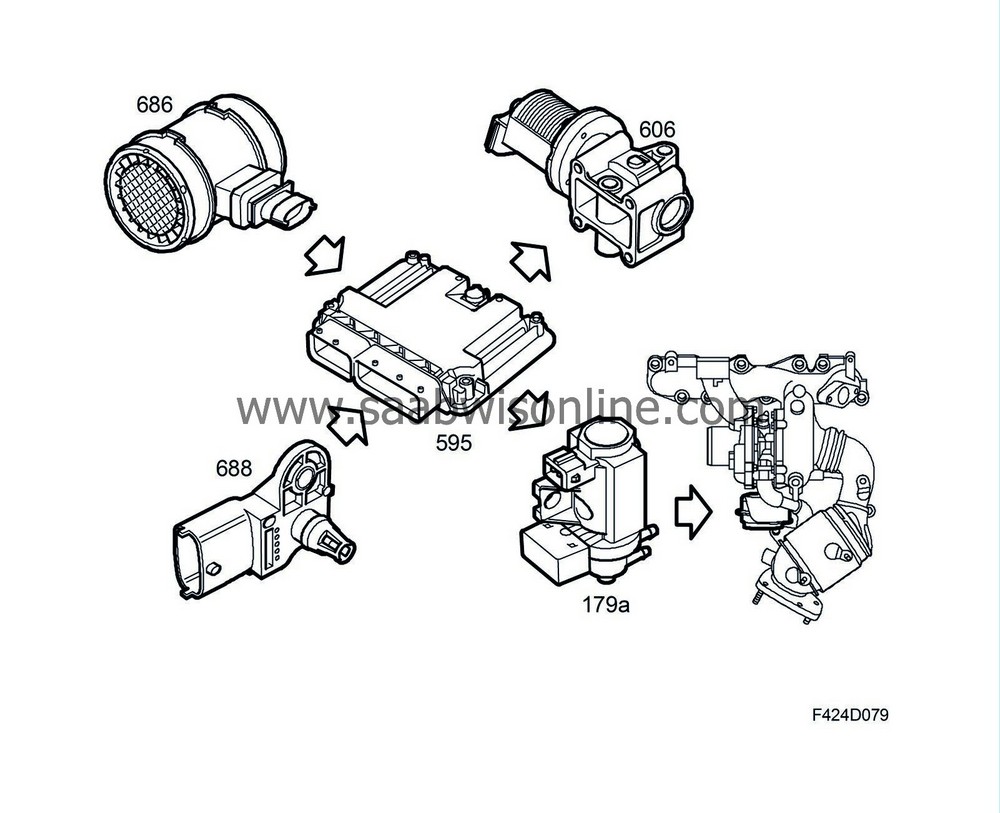
• |
Mass air flow sensor (686) to measure the intake air mass and the temperature of the air .
|
• |
Intake air sensor (688) to measure the pressure and temperature of the charge air.
|
ECM uses the following actuators to affect the engine's air change rate:
• |
Boost pressure control valve (179a)
|
• |
EGR valve (606)
|
Calculation of air mass requirement
The air function calculates the air mass per combustion that is required for the prevailing driving conditions. This is mainly based on the requested fuel mass and engine speed.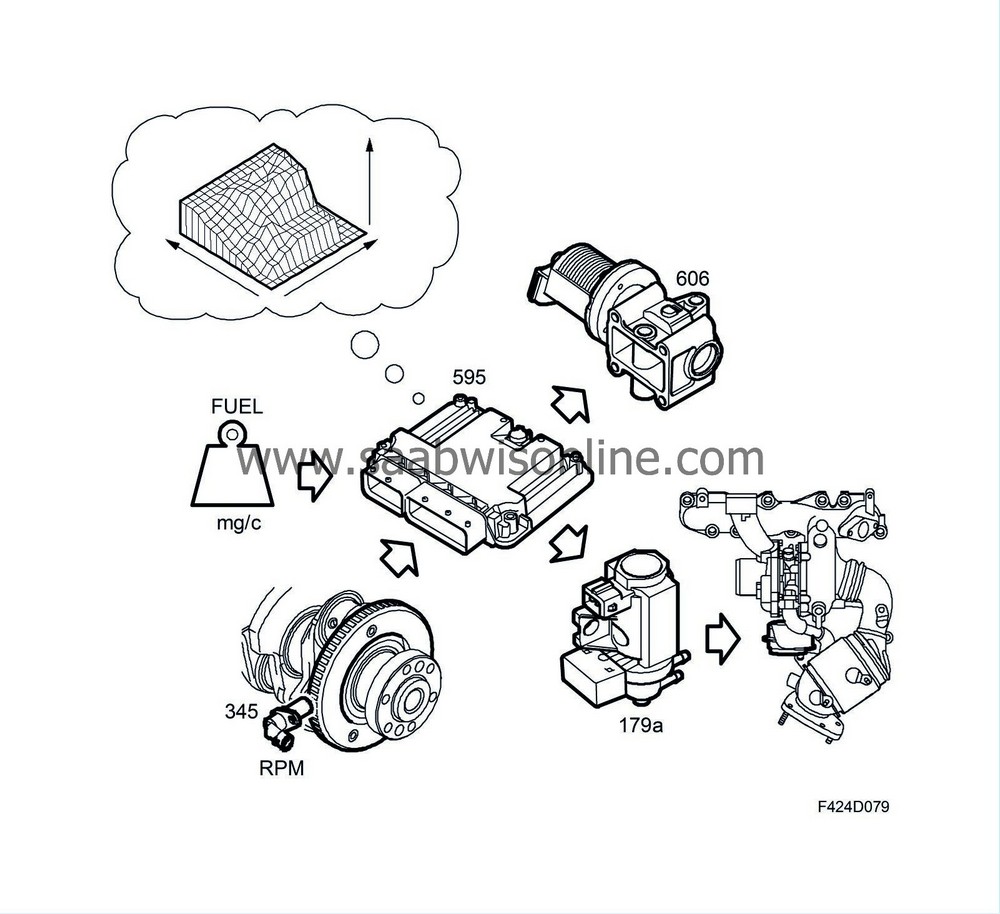
Regulation of air mass requirement
When the air mass per combustion required for the given fuel mass has been calculated, ECM has two ways of executing this air mass request. This is done with turbo control and EGR regulation.Using turbo control will increase engine aspiration; increased pressure of the charge air gives increased air mass through the engine. The EGR function works conversely; air mass is replaced with exhaust gas. ECM measures the current air mass using the mass air flow sensor (205). This is converted to air mass per combustion and compared with a requested value. If the values are different, turbo control and EGR regulation will make a correction. The value from the mass air flow sensor is corrected for the inertia of the air in the induction system, i.e. in the pipes and charge air cooler.
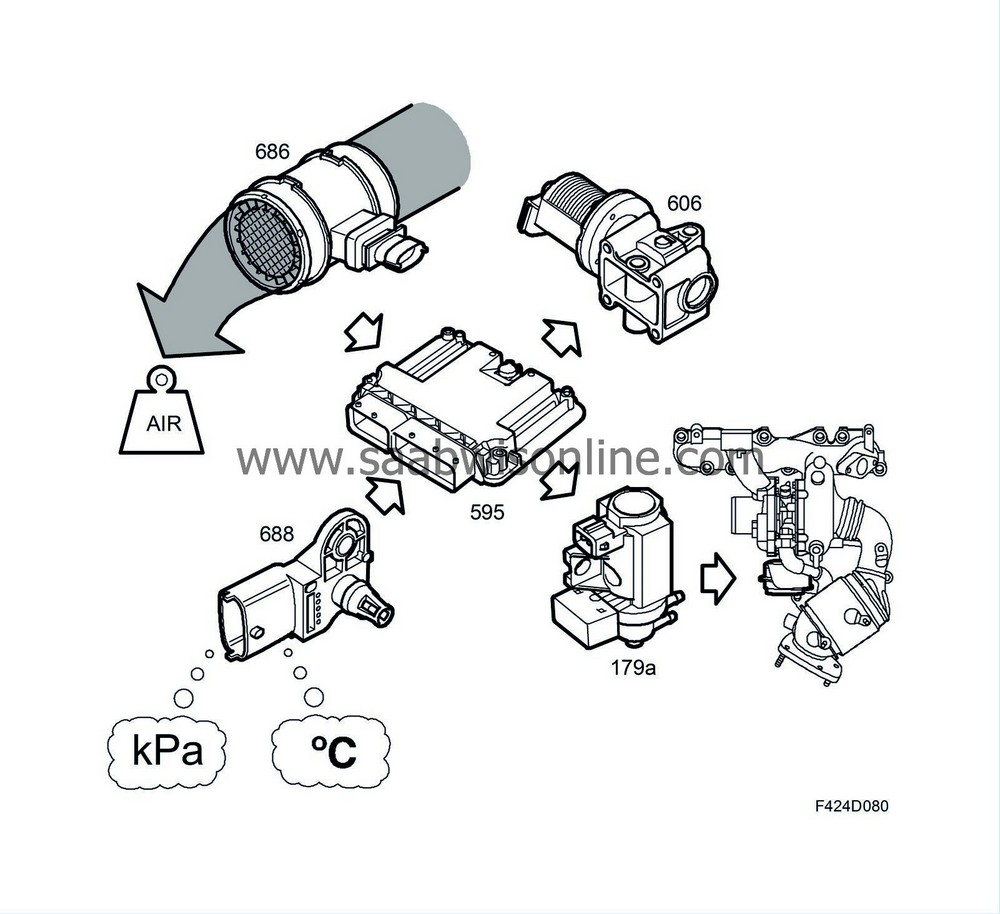
Turbo adjustment
The requested air mass per combustion is achieved by regulating the boost pressure.ECM calculates the boost pressure (desired value) required to obtain the requested air mass per combustion. The desired value is mainly calculated using the following parameters:
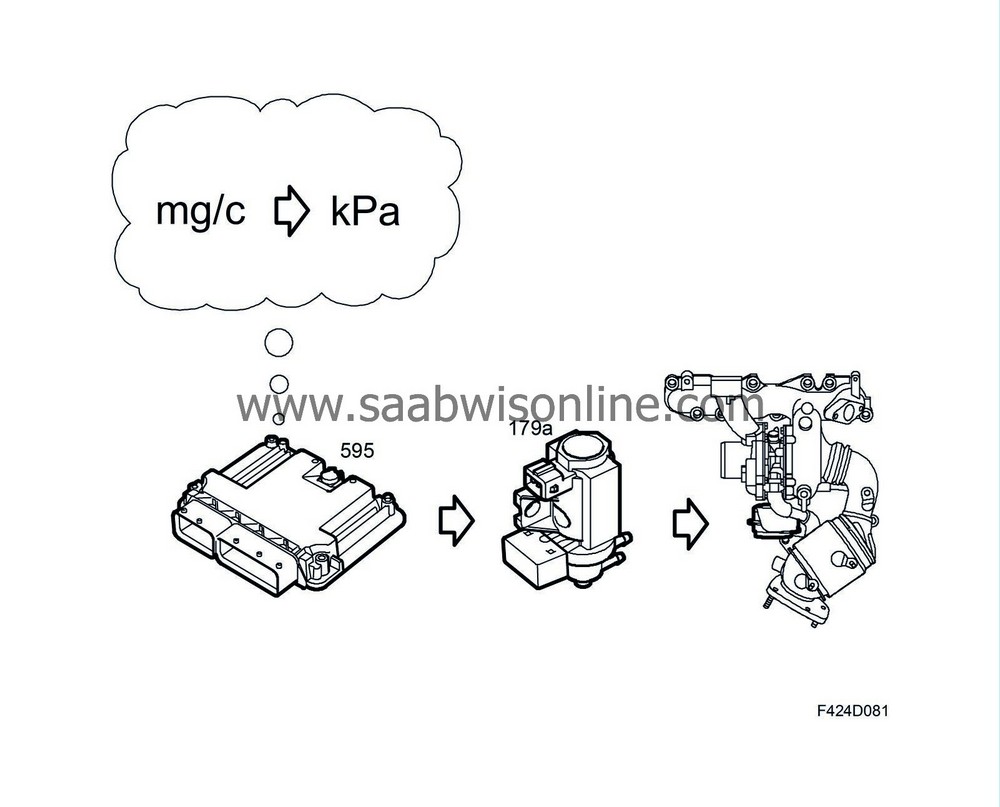
• |
Engine speed
|
• |
Fuel quantity
|
• |
Prevailing boost pressure
|
The result is a PWM signal that controls the charge air control valve (179a). This valve regulates the vacuum to the turbocharger vane regulator. ECM compares the current boost pressure and corrects the PWM signal accordingly. Turbo control is adaptive.
EGR control
EGR control affects the air mass per combustion, see Exhaust gas recirculation, EGR .
Glowing |
General
The main task for the glow function is to preheat the combustion chamber so that a fast and reliable start of the engine is assured at low temperatures. Glowing can also be activated in conjunction with regeneration of the particle trap. The glow function has five different subfunctions.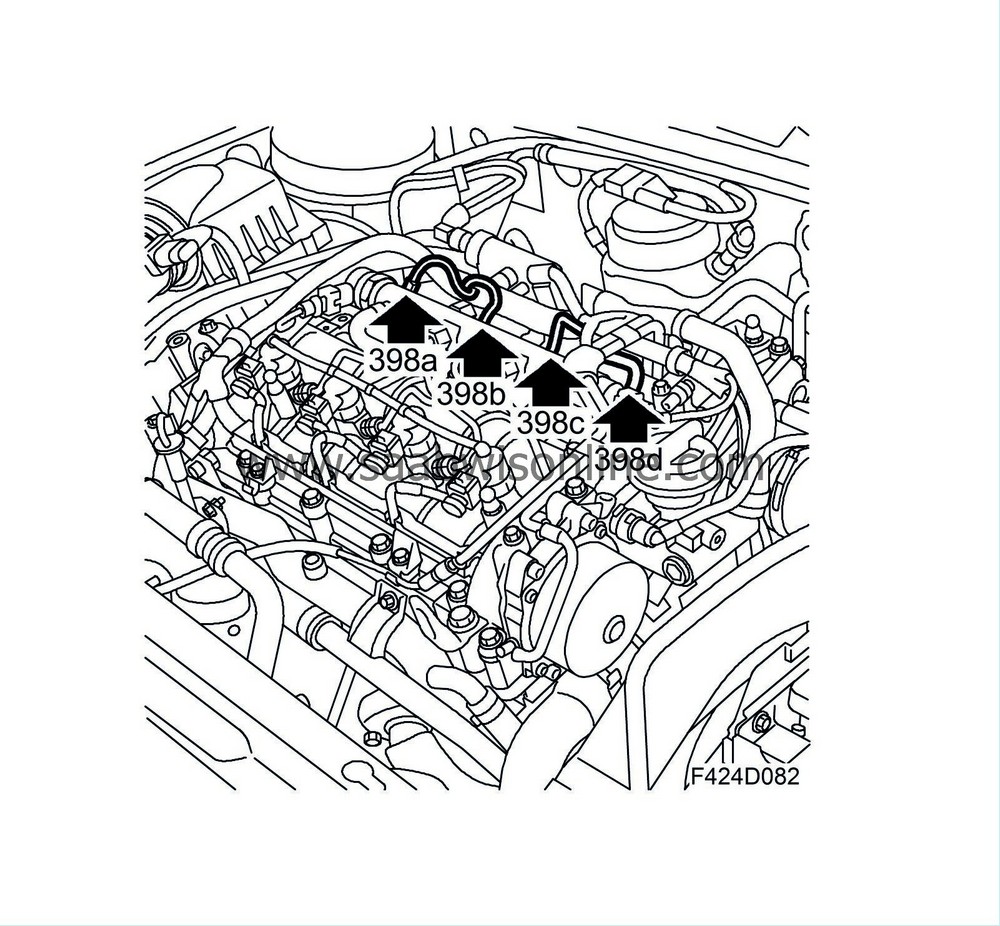
• |
Preheating
|
• |
Starting preparation glow
|
• |
Starting glow
|
• |
Afterglow
|
• |
Intermediate glowing
|
The temperature generated by the compression must be high enough to ignite the injected fuel. The compression leakage and thermal losses when starting a cold engine are greater than when starting a warm engine. This can mean that the fuel will not reach its ignition point and the engine will not start.
Mounted in the cylinder head are the glow plugs (398), one for each cylinder. When the glow function is activated, the glow plugs will heat up, especially the top protruding into the combustion chamber. This will heat the fuel to the temperature required for ignition. As the power consumption of the glow plugs is very high, they are controlled by ECM via a glow plug control module (596).
The glow plugs can be activated to increase the engine load for regeneration. Their power consumption will increase the load on the generator, which in turn requires a higher torque to drive. ECM will compensate for this increase in torque requirement by increasing the injected fuel quantity. The result will be increased exhaust temperature and increased exhaust flow in the particle trap.
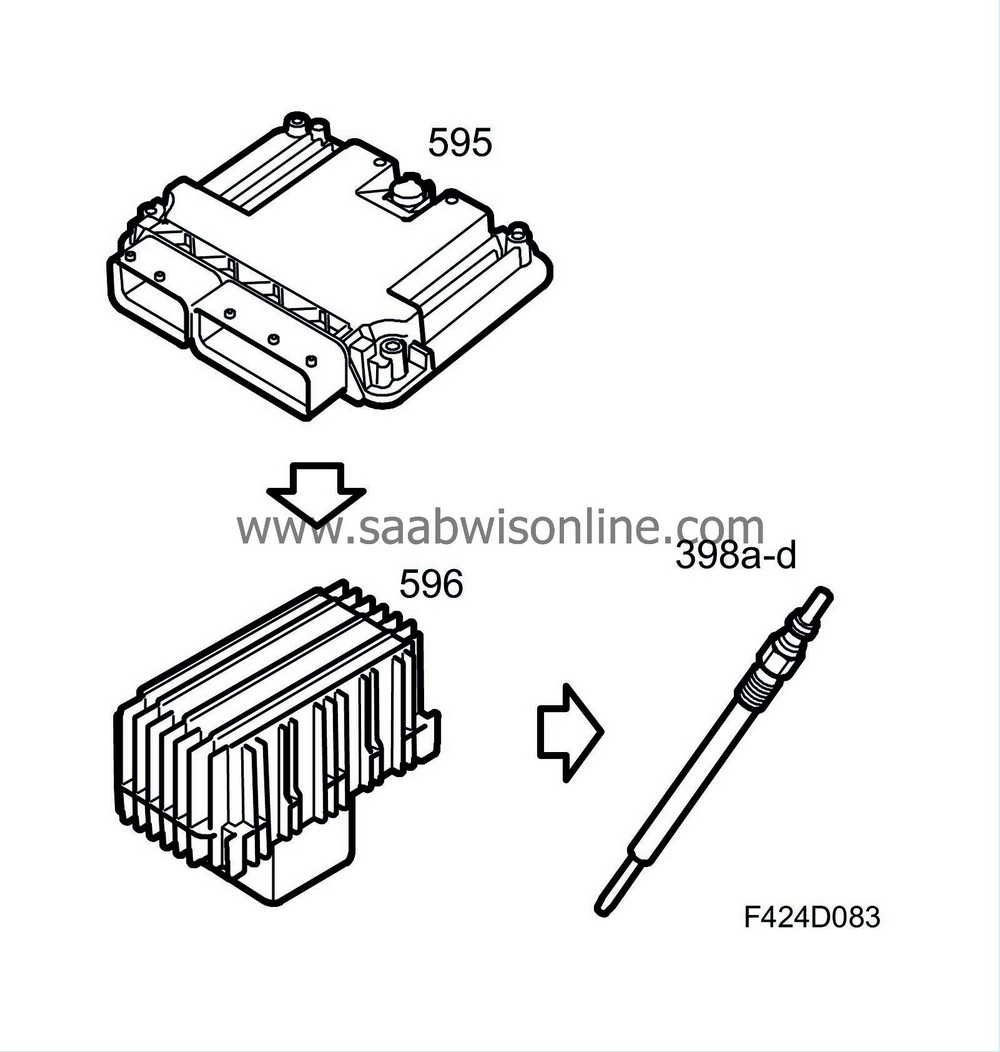
Preheating
Preheating starts once the ignition key has been turned to ON. The glow duration is dependent on coolant temperature and is 0 for a warm engine. Meanwhile, information that preheating is active is sent on the P-bus, which is read by the main instrument unit. This will turn on the preheating indicator lamp.
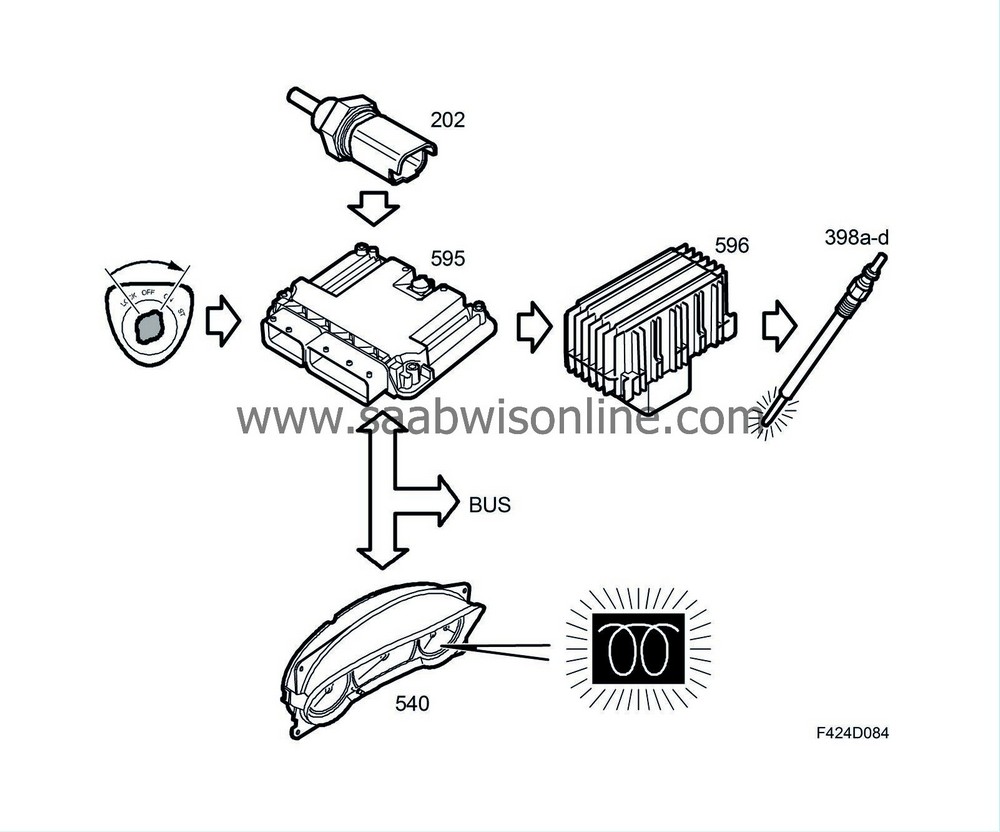
Preheating is turned off after a certain period. It is then replaced with start readiness glow. If the engine has started it is replaced with starting glow.
Starting preparation glow
Once preheating is completed, start readiness glow will commence. It is used to keep the glow plugs warm waiting for start. Start readiness glow is turned off after a certain period. If the engine has been started, it is replaced with starting glow.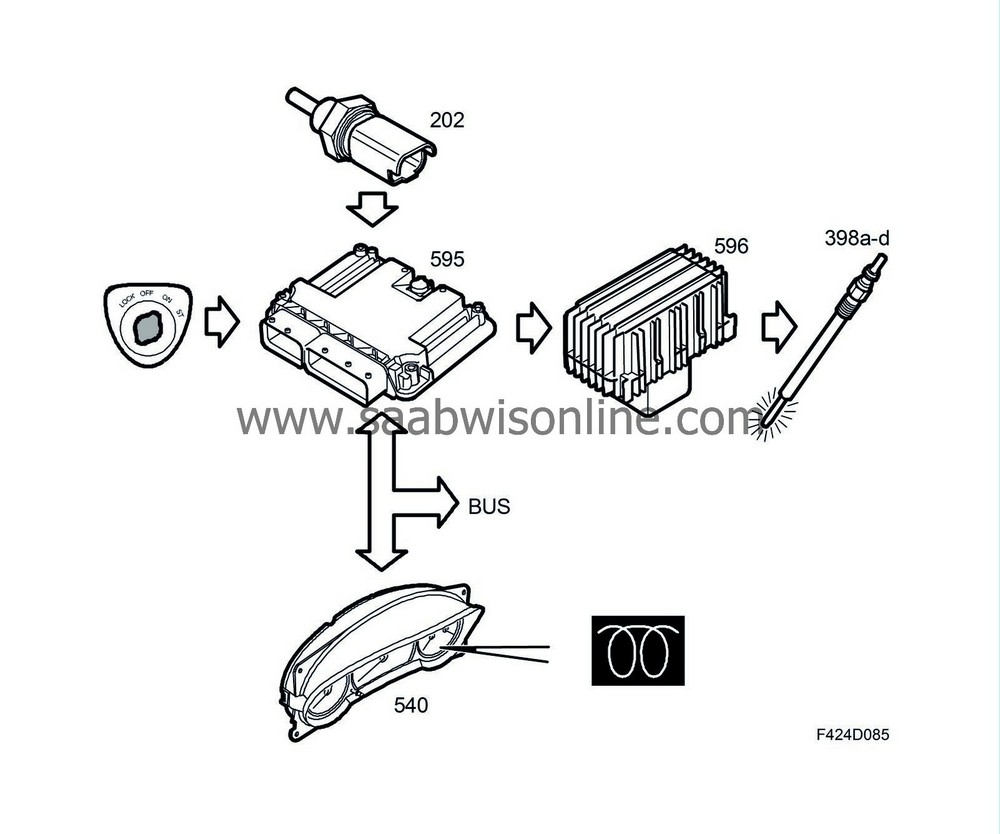
Starting glow
Starting glow is activated once the engine has started and the coolant temperature is low. It is turned off when the engine is assumed to be running and is then replaced with afterglow.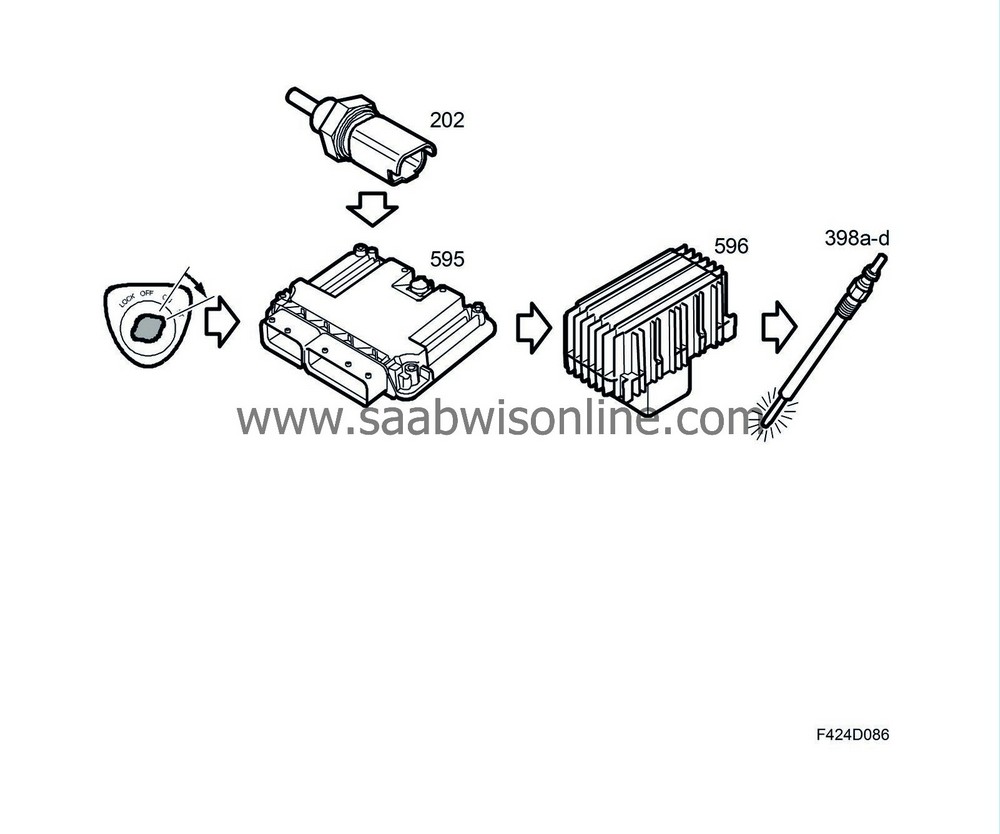
Afterglow
Afterglow takes over from starting glow when the engine is assumed to be running. This is to reduce misfiring and give smoother running by making sure the combustion chamber is being heated while combustion is not yet generating sufficient heat to provide a reliable ignition of the fuel. Afterglow is turned off after a period that is dependent on the coolant temperature. It is also turned off when the engine speed or injected fuel quantity exceeds limits. Should the engine speed or injected fuel quantity again drop below limits, afterglow will be engaged again provided the period dependent on the coolant temperature has not expired.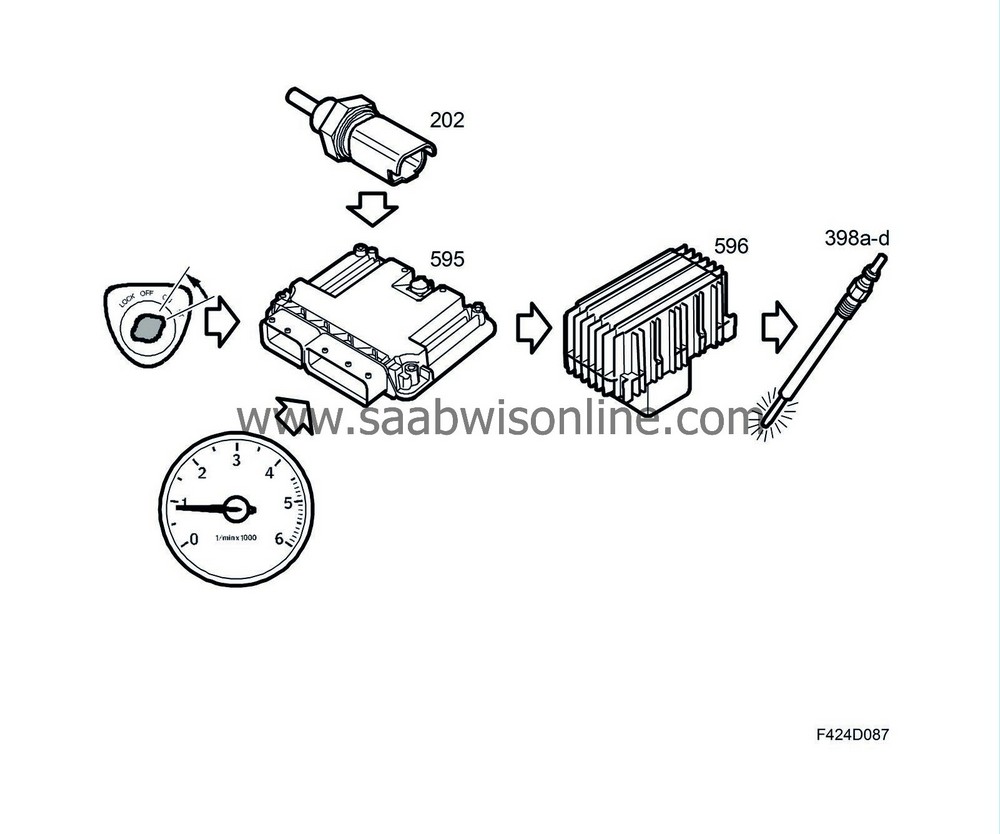
Intermediate glowing
To reduce cooling of the combustion chamber when fuel quantities are low or during engine braking (fuel quantity = 0), the intermediate glow function can be activated. This will reduce blue smoke when accelerating again.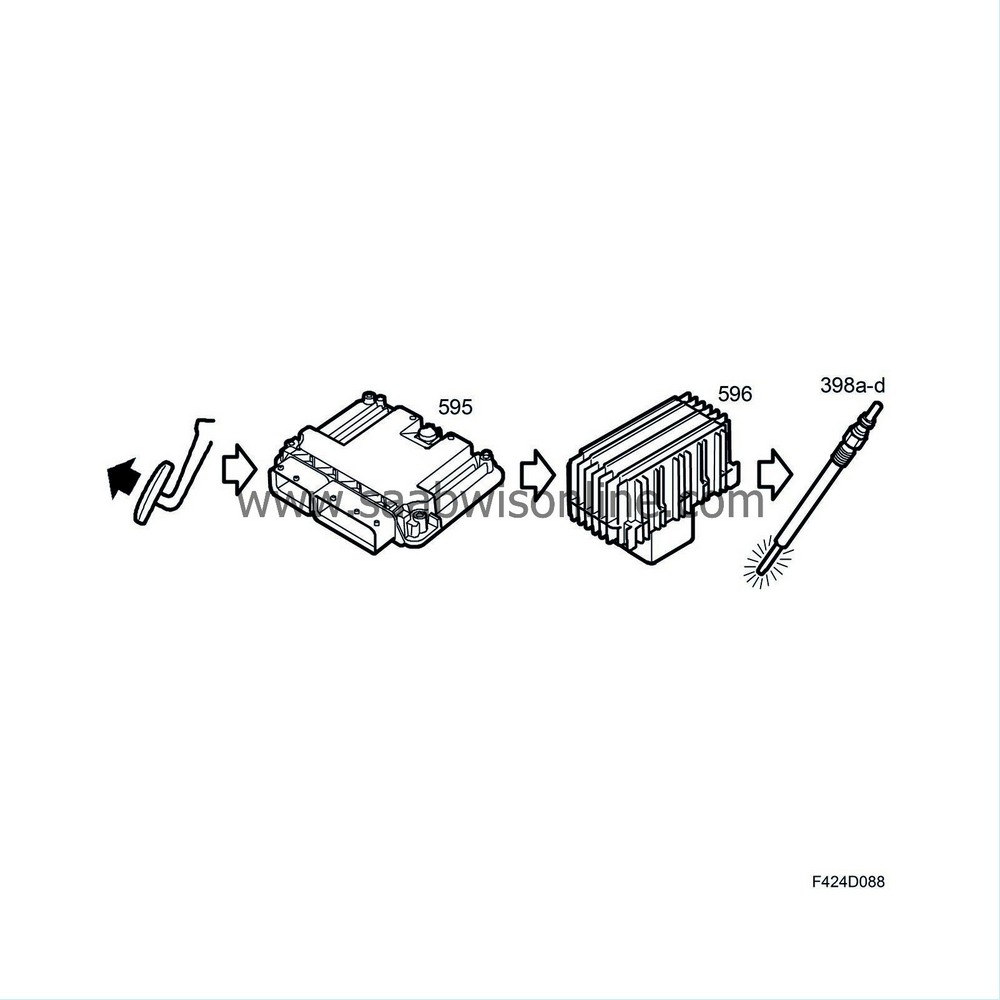
The intermediate glow function can also be activated when the particle filter is regenerated and under driving conditions when the engine load is relatively low. The high power consumption of the glow plugs increases the load on the generator, which in turn demands more torque from the engine to drive it. ECM will compensate for the increased requirement of torque by increasing the injected fuel quantity. The result is increased exhaust temperature and increased exhaust flow into the particle trap.
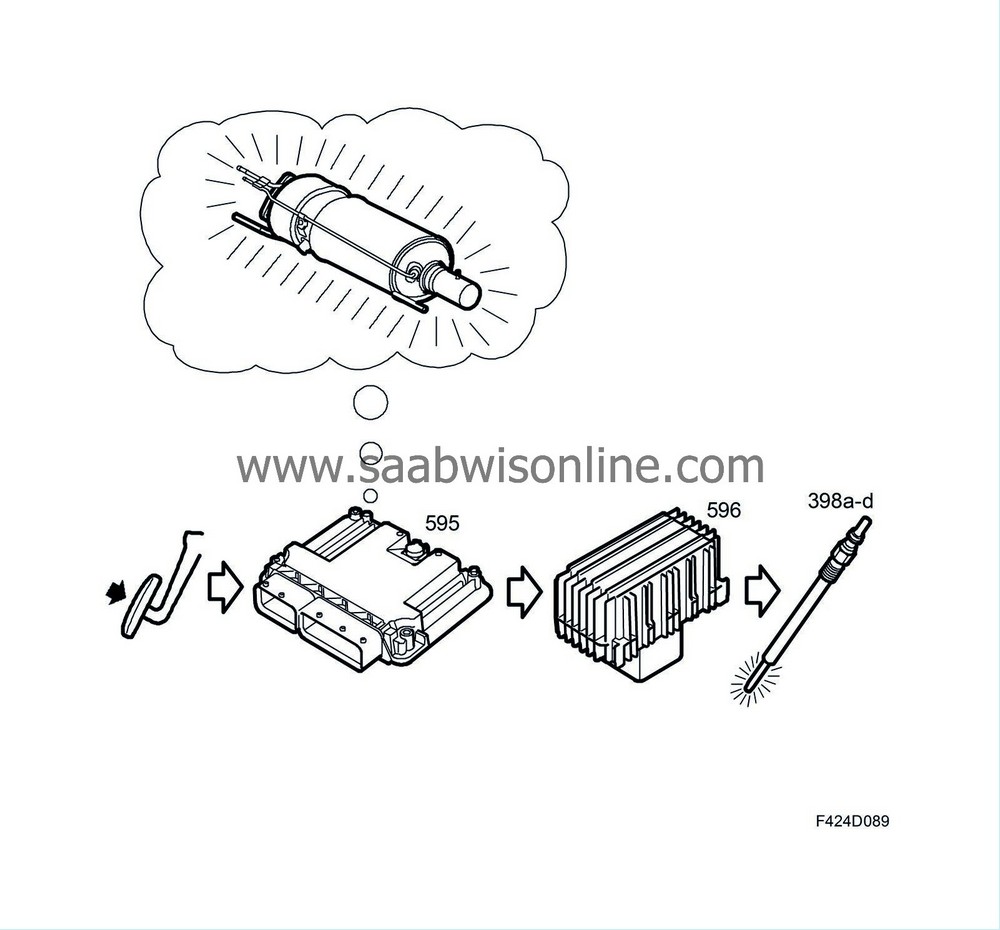
The intermediate glow function will not be activated for regeneration when the engine load is high.
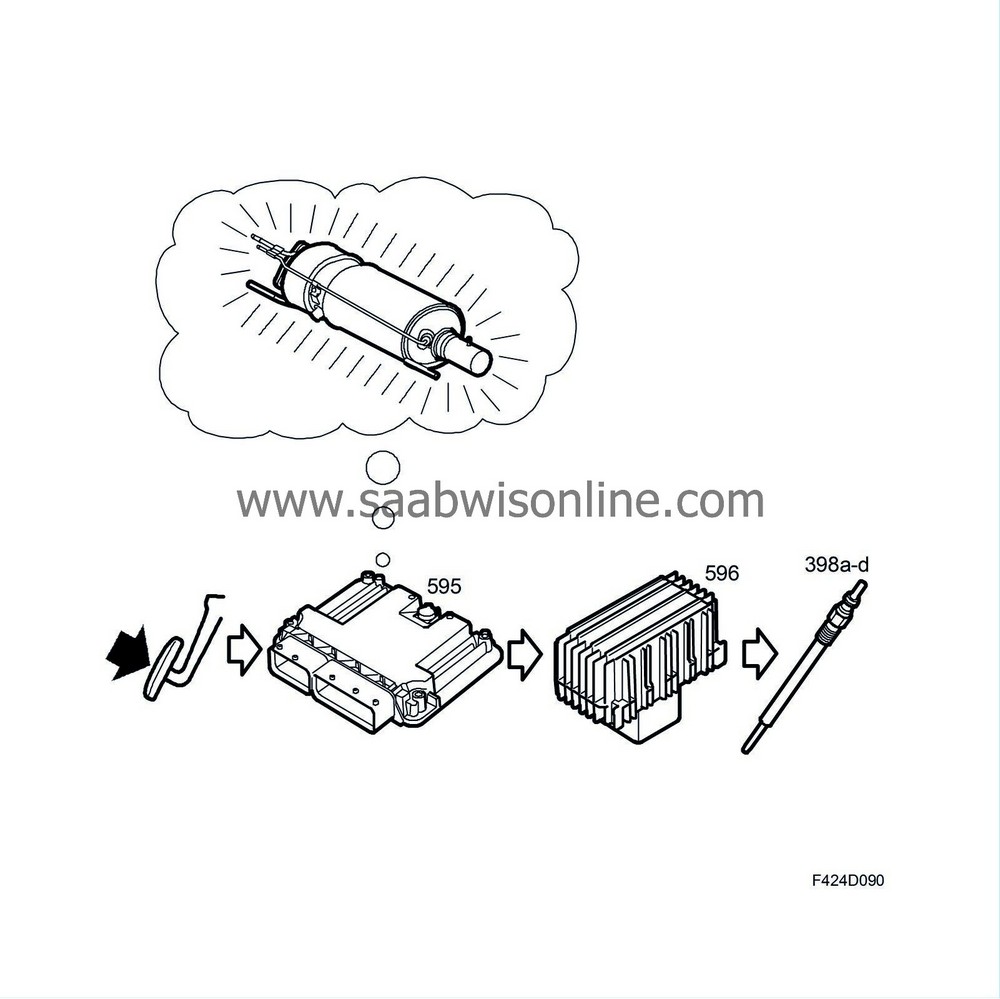