Short description
Short description |
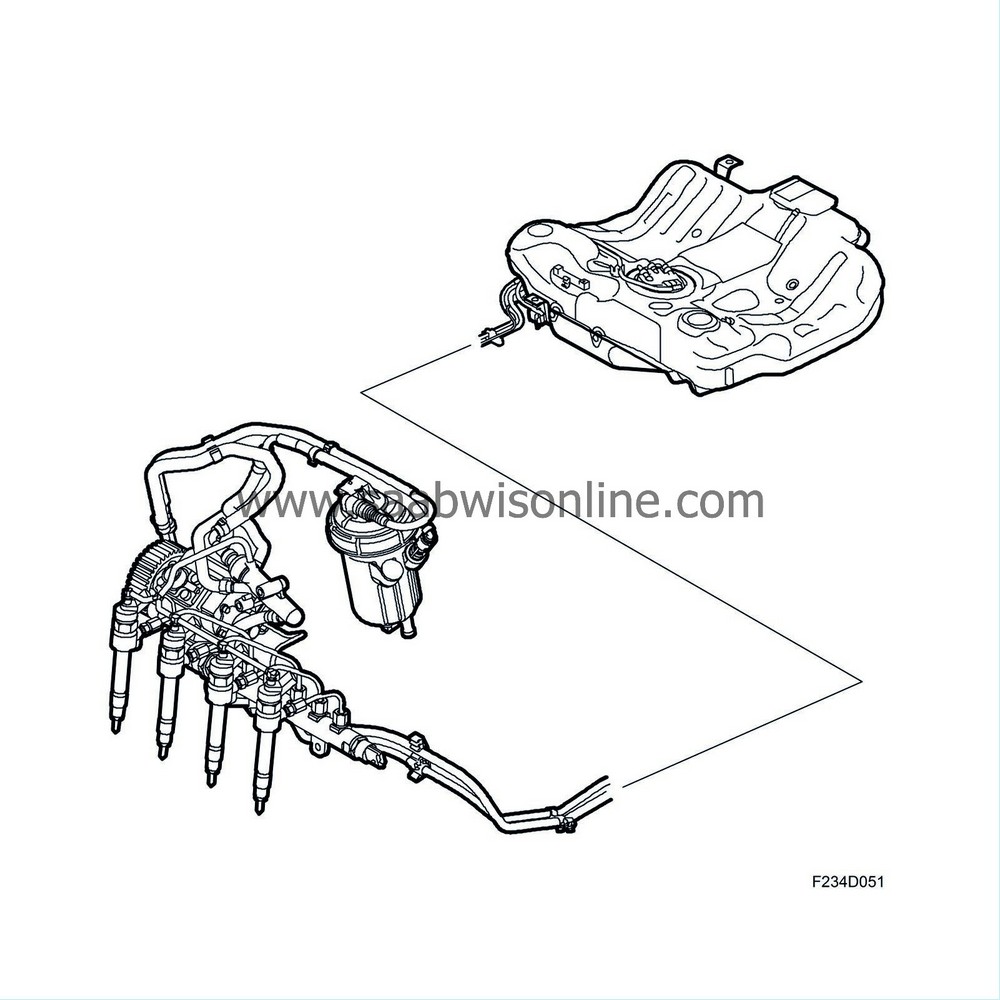
Important | ||
Be very thorough in terms of cleanliness when working in the fuel system. Malfunctions can also occur due to very small dirt particles. Prevent dirt from entering the fuel system by cleaning the hoses and plugging the pipes and lines upon removal. Store the components so that contaminants cannot enter. |
||
• |
Fuel tank
|
• |
Feed pump integrated in fuel tank
|
• |
Fuel lines
|
• |
Fuel filter
|
• |
High-pressure pump
|
• |
Fuel regulator valve
|
• |
Fuel rail/reservoir
|
• |
Fuel pressure regulator valve
|
• |
Fuel pressure sensor
|
• |
High-pressure pipe
|
• |
Injectors
|
• |
Fuel return hoses/pipes
|
• |
Return fuel container
|
Description |
The fuel system is of direct injection common rail type. The 58-litre fuel tank contains a feed pump that delivers fuel to the high pressure pump via a fuel filter. The feed pump pressure is 4 bar, while the high pressure pump delivers a pressure of up to 160 MPa (1600 bar), depending on the prevailing running conditions. This ensures that the injected fuel is well atomized. The pump supplies a fuel rail that also acts as a reservoir.
A steel pipe runs from the fuel rail to the respective injector. The injectors on the Z19DT have six fuel jets and on the Z19DTH seven. To regulate the injection pressure, there are two valves and one pressure sensor. The injection timing and duration is controlled by the ECM. To achieve as optimum an injection as possible, ECM can inject fuel up to five times per power stroke. This is divided into
a. |
Pilot injection (1)
|
b. |
Main injection (3)
|
c. |
Regeneration injection (1).
|
To give an idea of the precision required of the injection process, the maximum injection timing is 1.1 milliseconds (1.1 thousands of a second).