Torque control
Torque control |
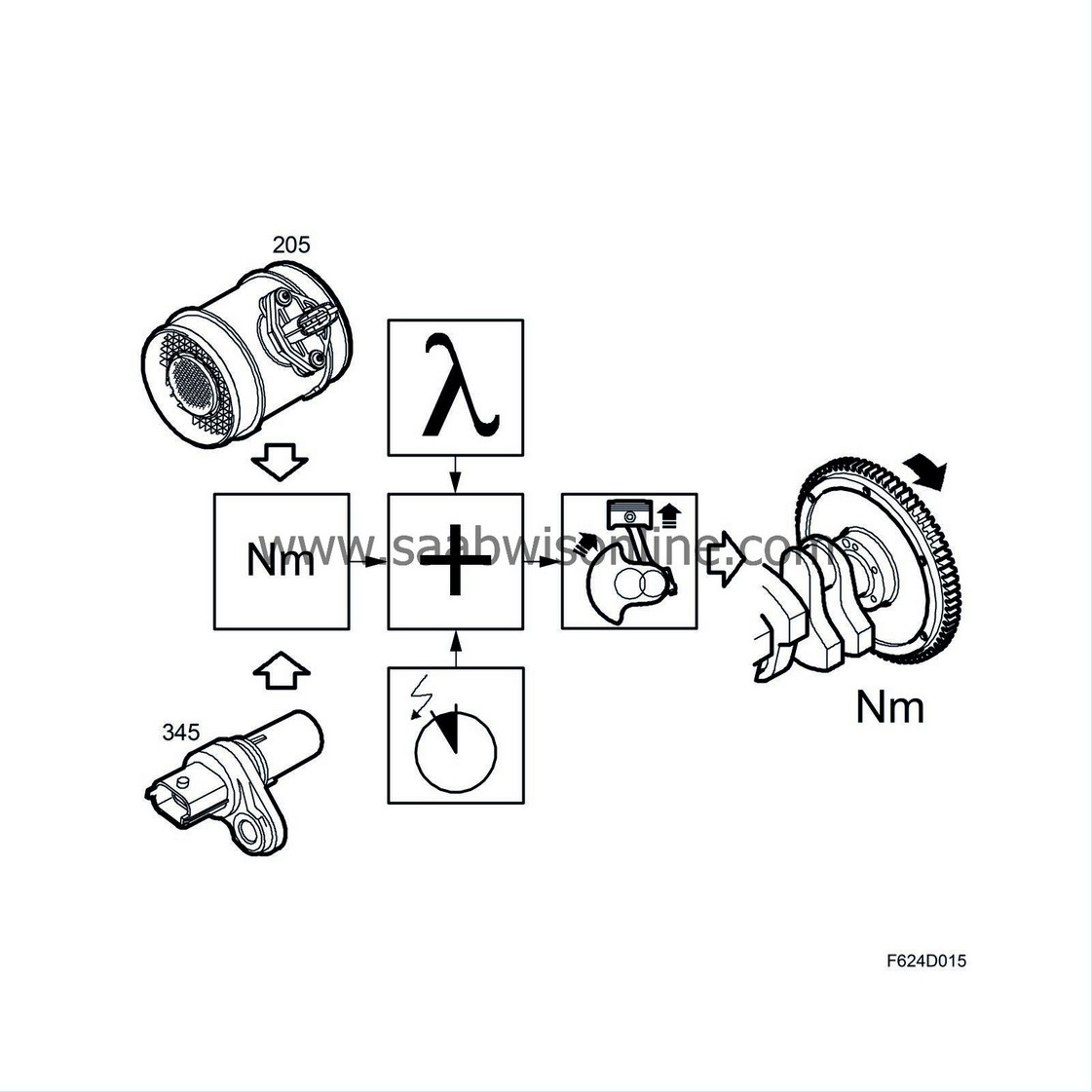
General
Engine torque control is used to ensure the correct engine torque is supplied by the engine. ECM controls engine torque by regulating the air mass per combustion (cylinders' capacity) and also by regulating the ignition timing.The maximum engine torque allowed for the engine is stored as a table in the control module memory. The table specifies the highest torque the engine is allowed to generate at various engine speeds.
Engine torque is primarily calculated using air mass per combution and engine speed. But, ignition timing and current lambda value also affect the torque calculation. Retarded ignition timing generates lower engine torque. This is the case in knock control. As regards the lambda value, there is an optimal lambda value for each operating point. If the engine runs richer or leaner than the optimal value, engine torque reduces.
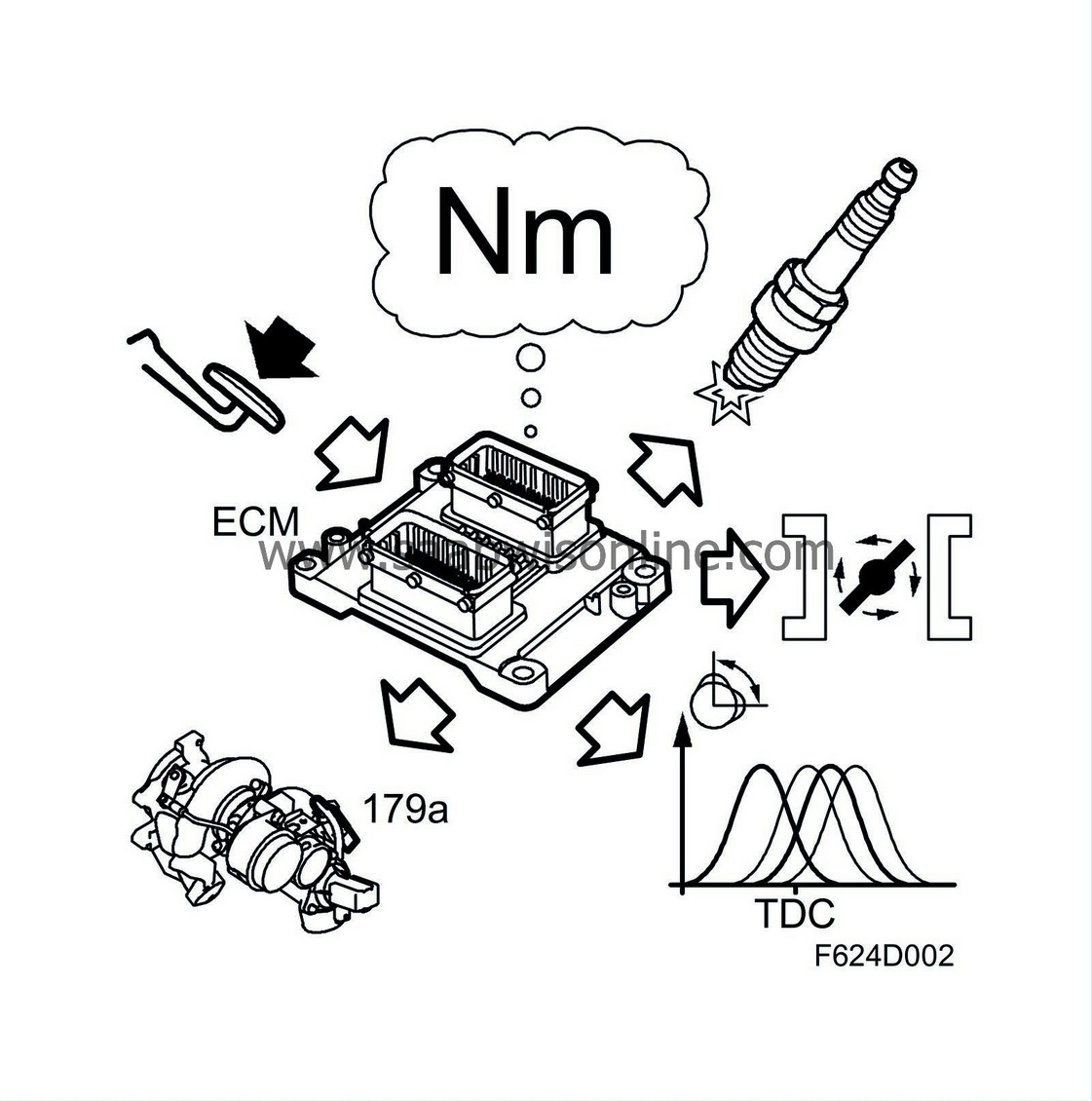
Note that a lambda value lower than the optimal value (richer mixture) produces lower torque.
The calculation also takes the engine's own torque consumption, i.e. internal friction, into consideration. The following values are used for this calculation:
• |
Air mass
|
• |
Engine speed
|
• |
Coolant temperature
|
• |
Idling torque
|
Fast engine torque control, increasing load
The fast method of control is used when the engine load changes rapidly, e.g. idle when turning the steering wheel rapidly so that the power steering pump puts a load on the engine. The increased torque requirement from the engine must then be compensated by a rapid increase in engine torque or the idling speed will drop. This fast compensation is done using previous ignition timing, giving higher torque.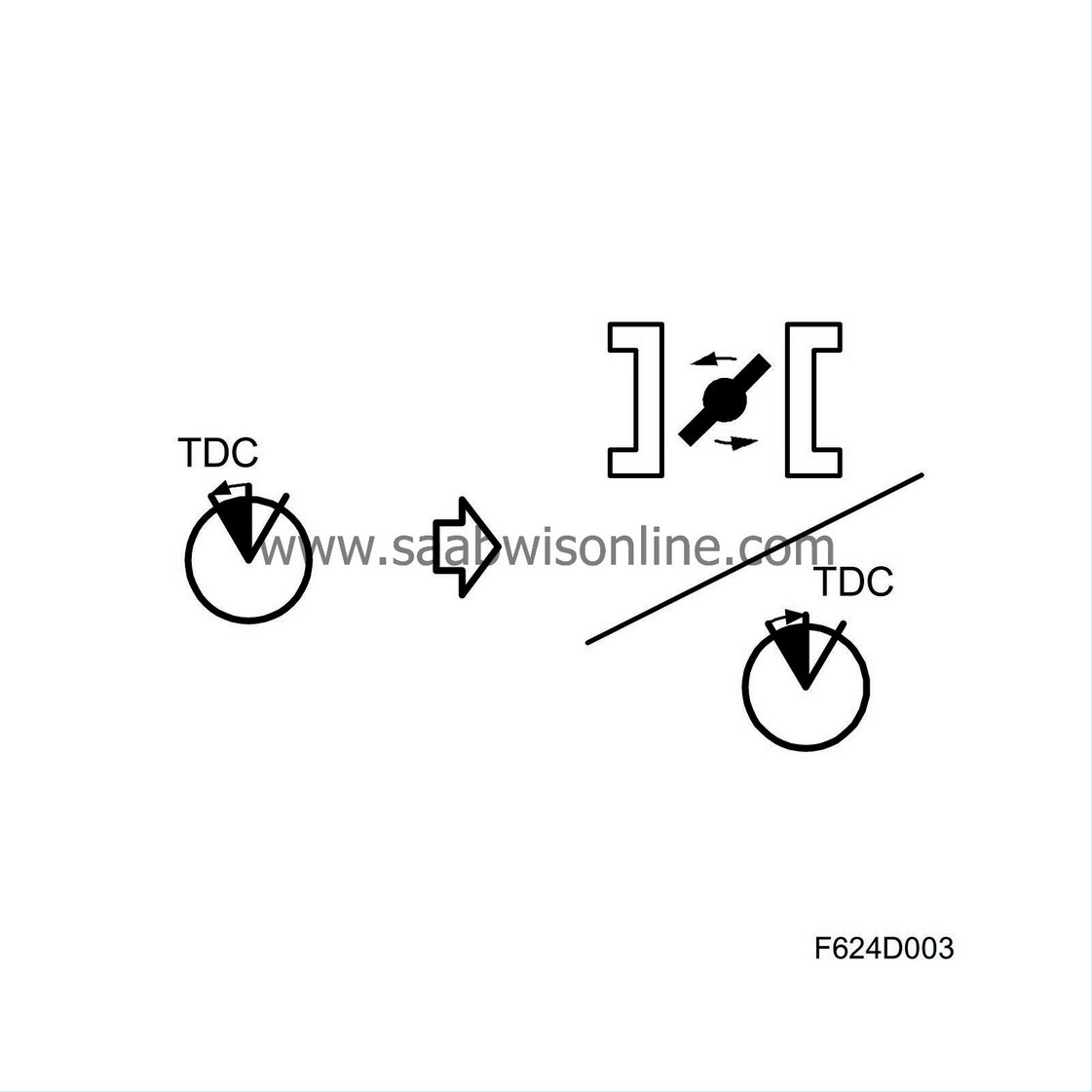
After the fast compensation, ECM will gradually increase the throttle area in order to get more air mass into the engine while the ignition is retarded slightly. This allows ECM to maintain a torque reserve so that it can again perform fast compensation for changed engine loads.
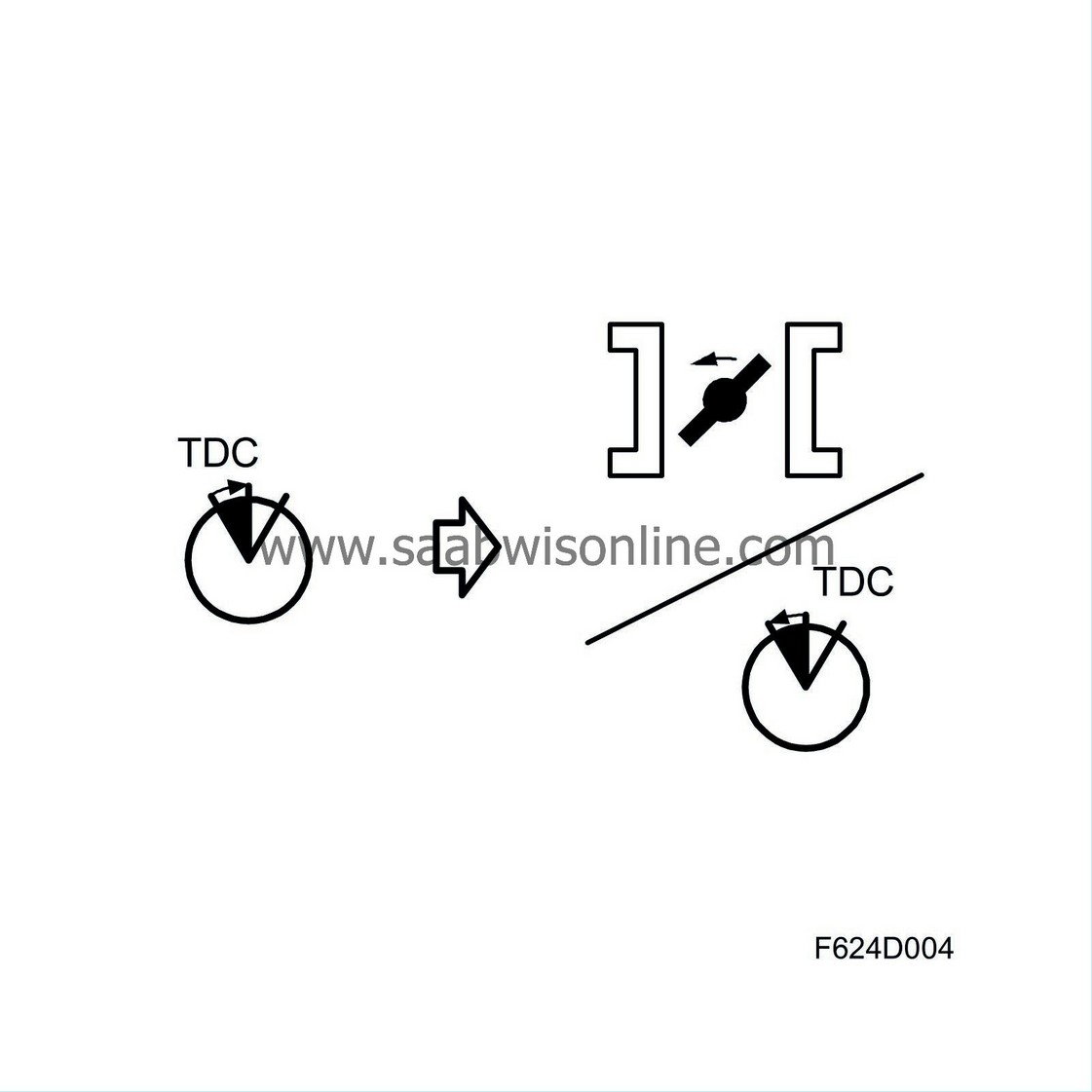
Slow torque control, load change
Slow engine torque control is used when driving under constant load, i.e. when the load does not vary or varies slowly. In this case, ECM operates mainly with throttle area to regulate the engine torque.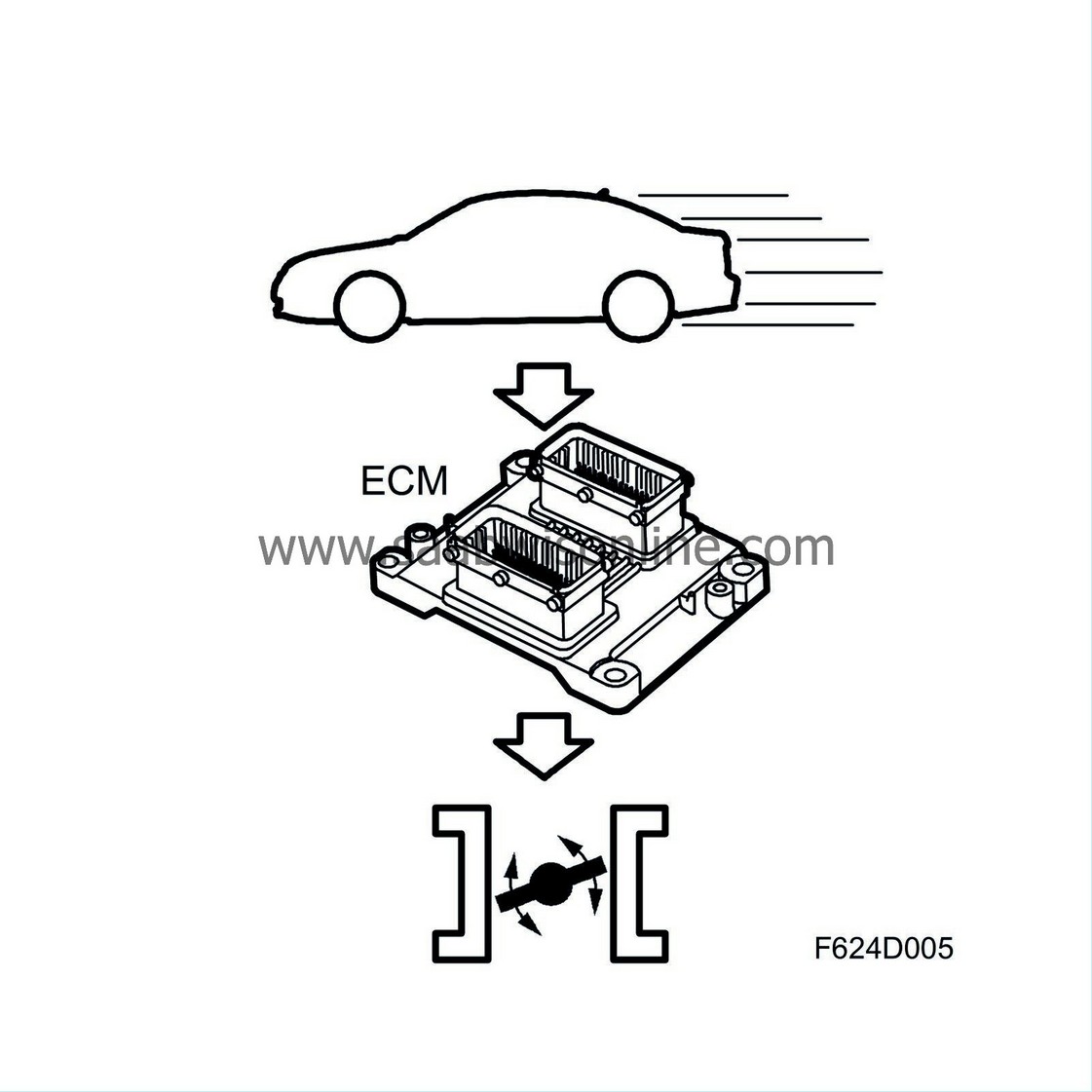
For higher torque requirements, turbo control will also be used to increase the air mass in the engine so that it produces the requested engine torque.
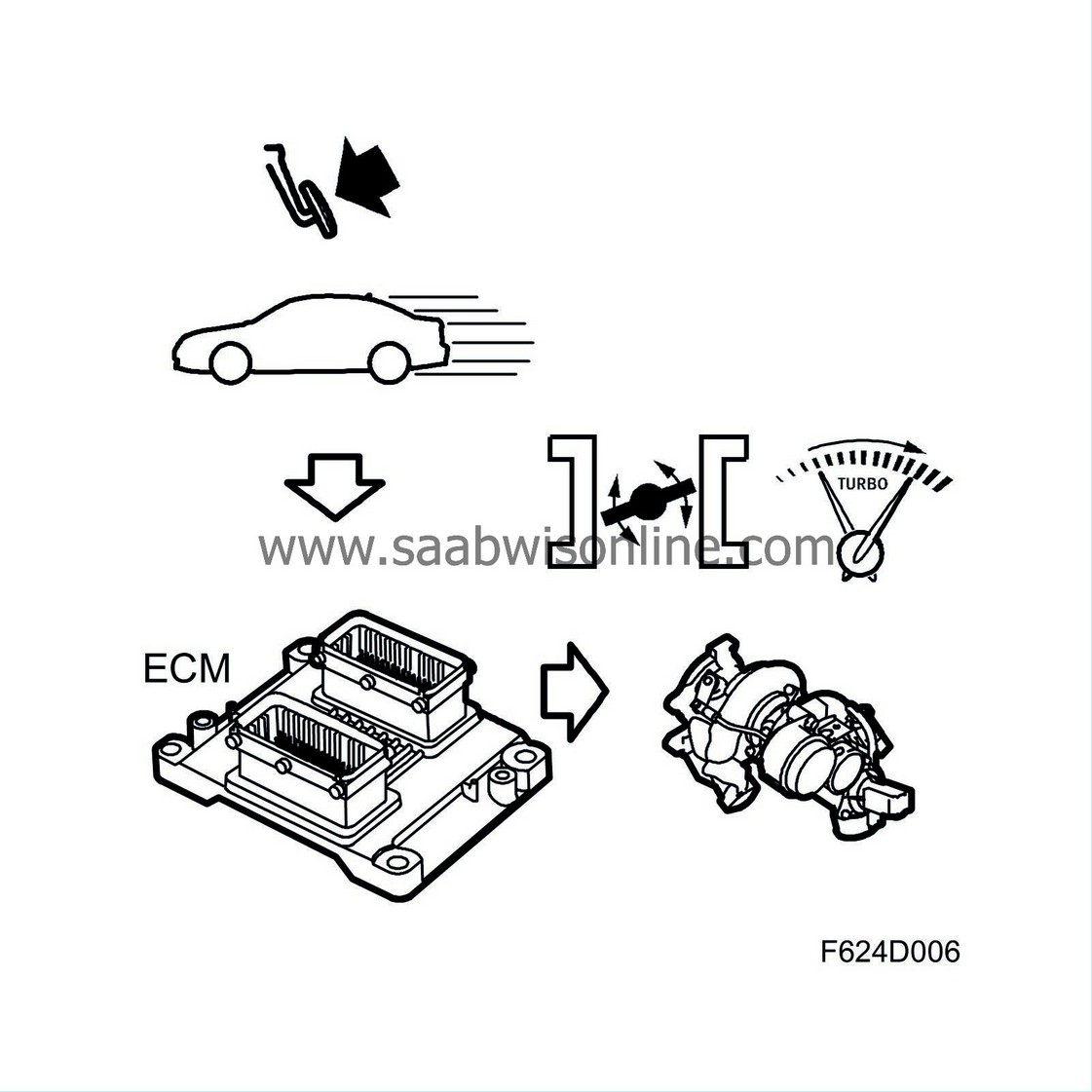
Idle speed control |
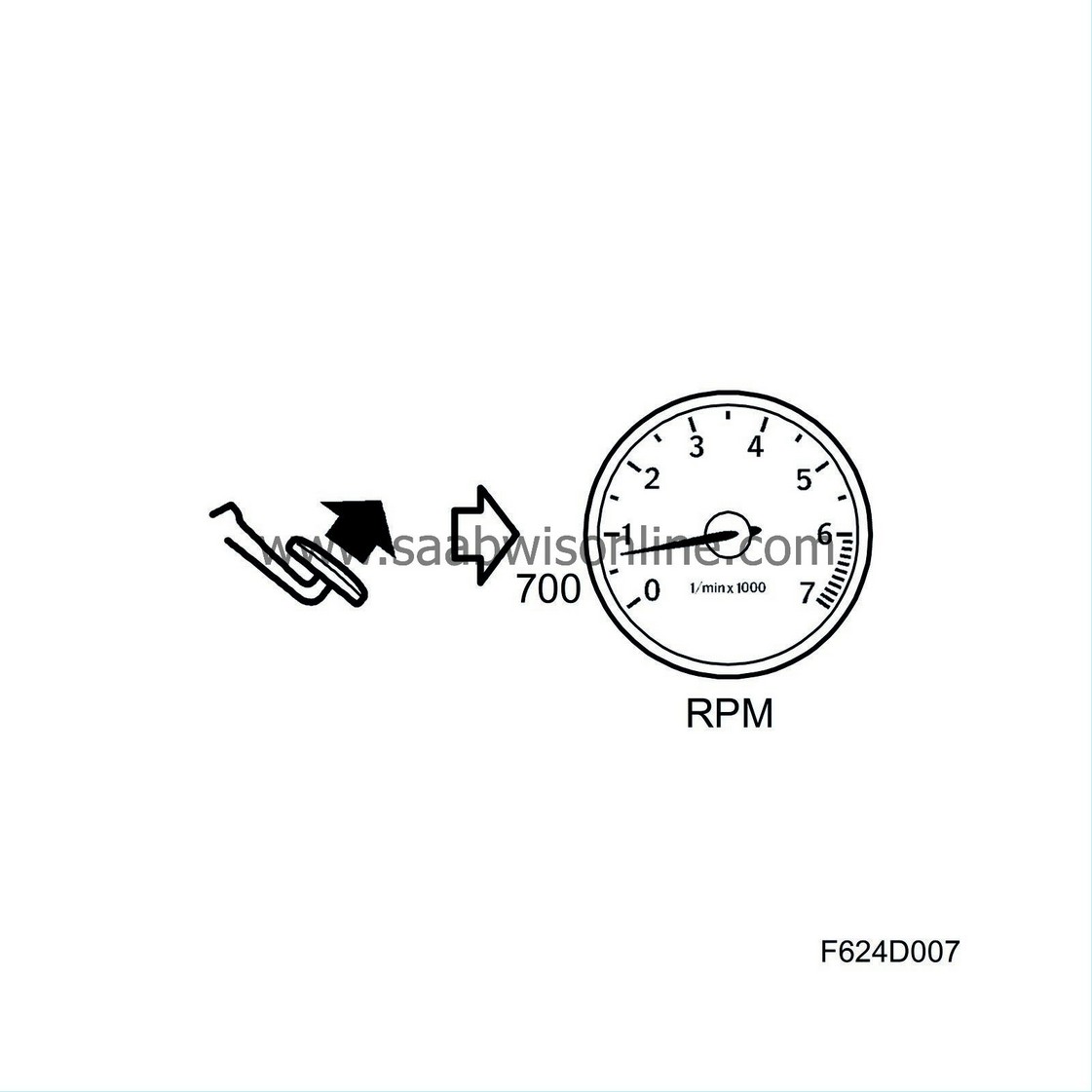
General
Idle speed control is used to regulate the engine torque so that the balance between the torque developed by the engine and the torque required to keep the engine and its auxiliary equipment running is maintained.The nominal idling speed of a warm engine is 650 rpm. The engine speed is higher just after starting, especially if the engine is cold. Nominal idling speed also depends on coolant temperature.
Idle speed control is active when the accelerator pedal is released and the vehicle speed is 0.
Torque control
The principle of idling control is that the engine works with a "torque reserve". Since ignition timing is retarded compared to that which would generate the best torque, engine torque can quickly increased by setting engine timing earlier. Slow changes are handled by throttle control.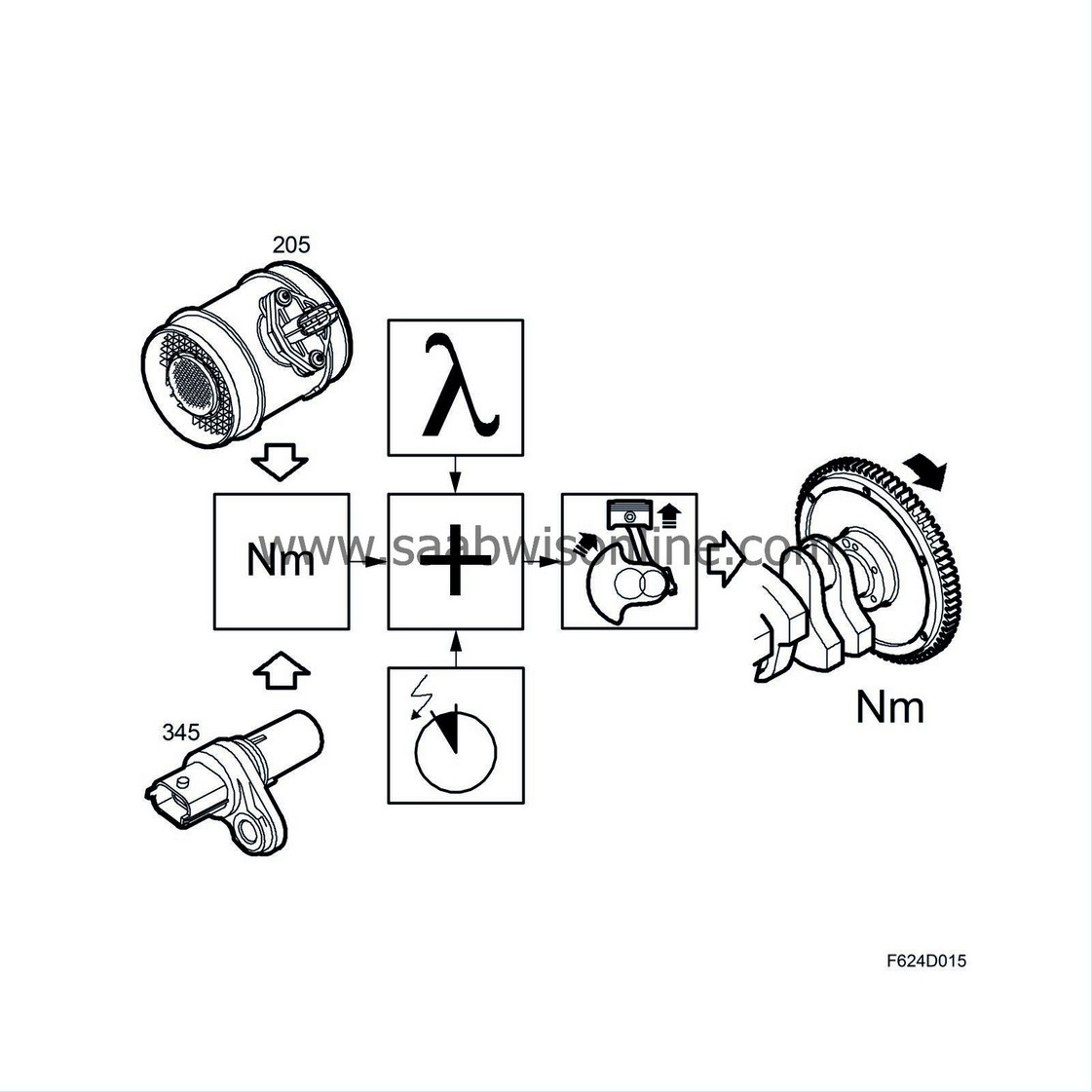
With an idling speed exceeding the nominal, there will be an excess of engine torque and the idling function will then request a lower value until the nominal idling speed has been attained. When the idling speed is below the nominal value, there will be a torque deficiency and the idling speed will have to be increased to attain nominal idling speed.
ECM reads the value for the torque (Nm) necessary to keep engine speed at the requested value from its memory. This value is also an indication of the engine's internal friction and is used for correction during torque calculation.
Torque request |
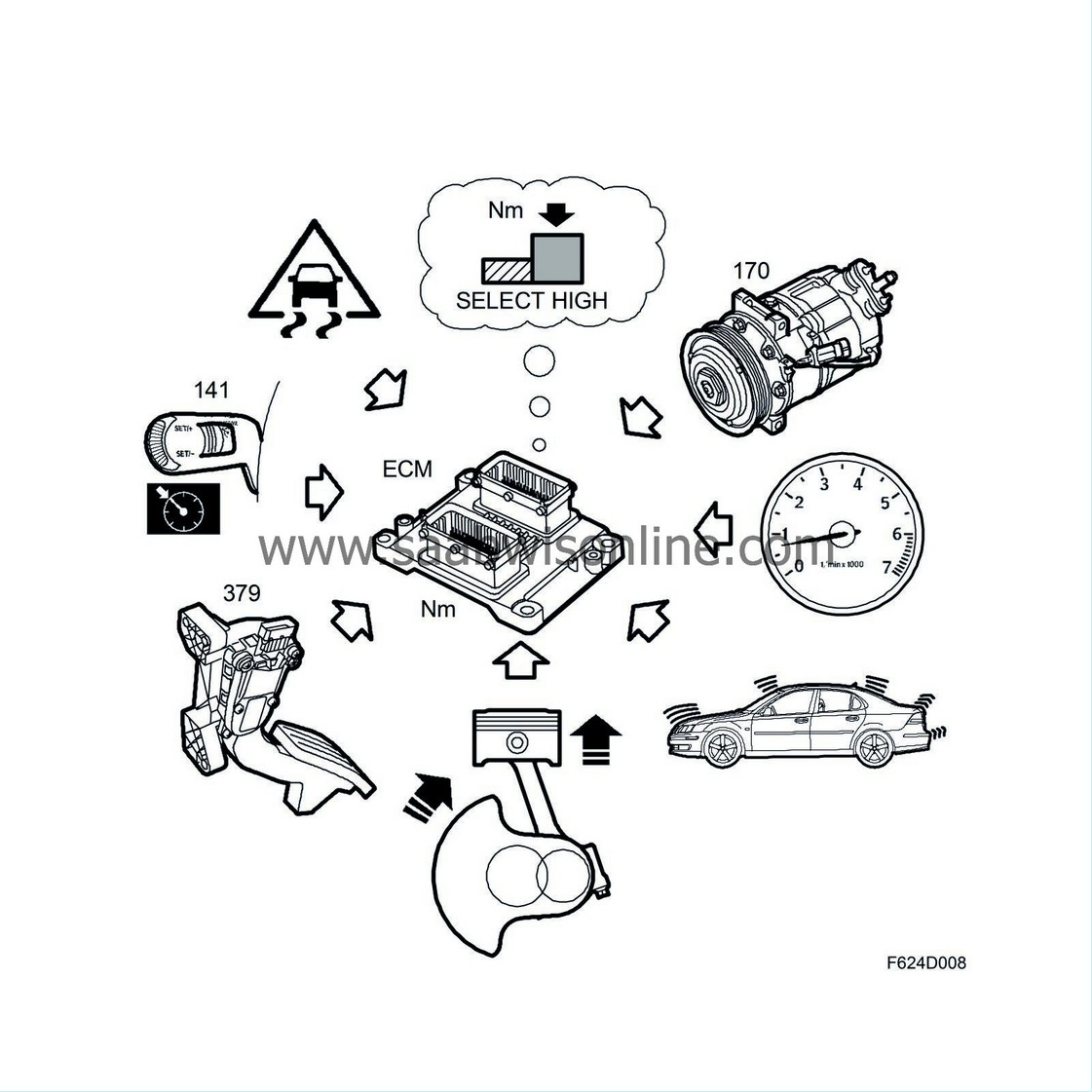
General
Several different functions, whether they be external or internal control module functions, can request engine torque. This request can be either positive or negative (limitation). ECM combines these sometimes opposing requirements.The following functions can request positive engine torque. The highest value is selected and sent on to "limitations."
• |
Pedal request (from driver)
|
• |
Cruise control
|
• |
TCS/ESP
|
• |
Idle speed control
|
• |
Compensation for A/C, generator
|
• |
Active surge dampening
|
But it is not always that the requested engine torque can be attained. This can be due to the maximum permissible engine torque for the engine speed in question has already been attained or that TCS/ESP has requested a reduction in torque. The following functions can limit engine torque:
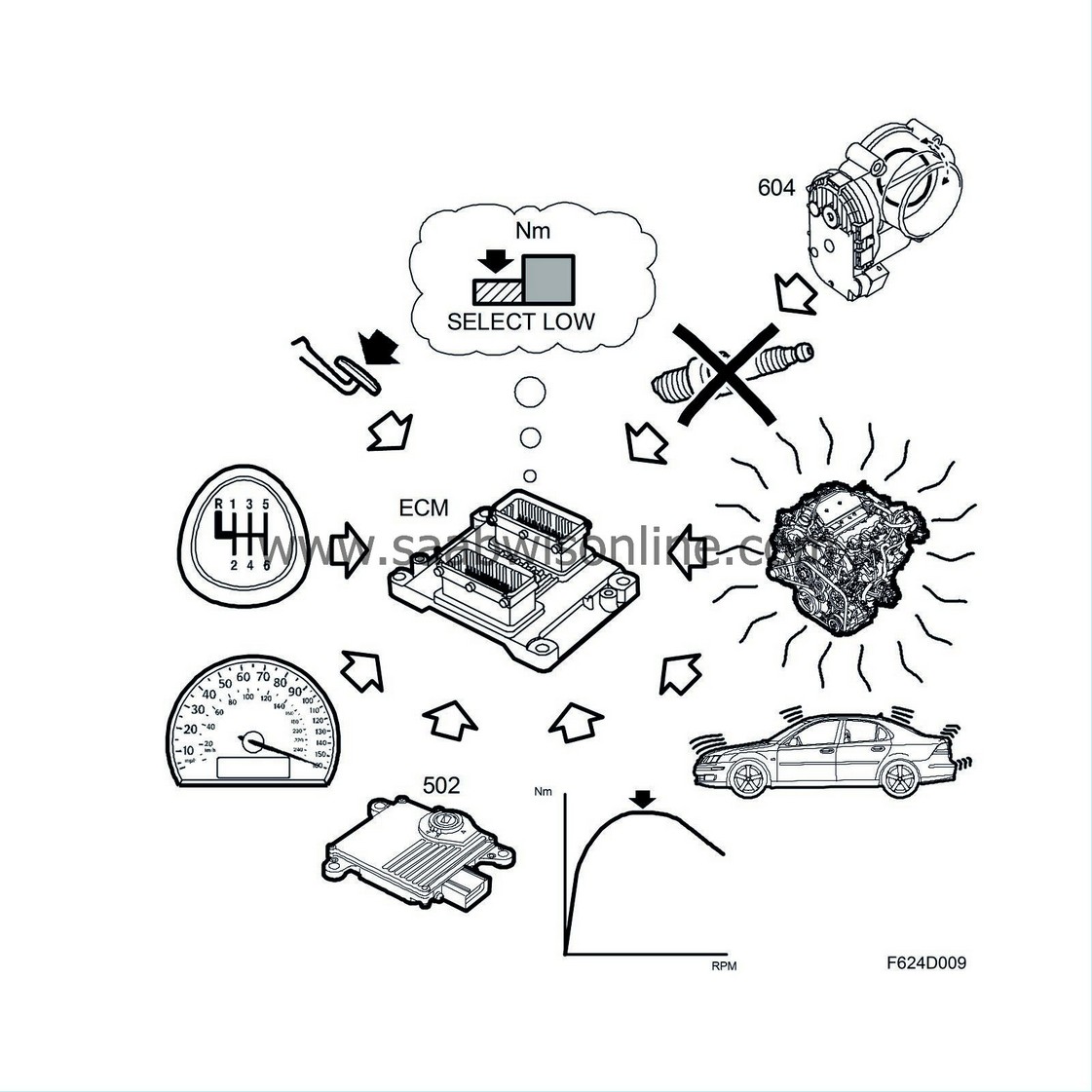
• |
Maximum permissible engine torque
|
• |
TCM
|
• |
Manual gearbox
|
• |
Engine protection function
|
• |
Brake
|
• |
Safety-critical fault in throttle control.
|
• |
Misfiring
|
• |
Emission limitation
|
• |
Active surge dampening
|
• |
Maximum permissible vehicle speed
|
Once the engine has been started, all torque requests are combined into a joint driving torque request. When starting the engine, there is a starting torque request that is selected by upon start of the engine. The result - a starting or driving torque request - is sent on to be converted to an air mass request.
Pedal request |
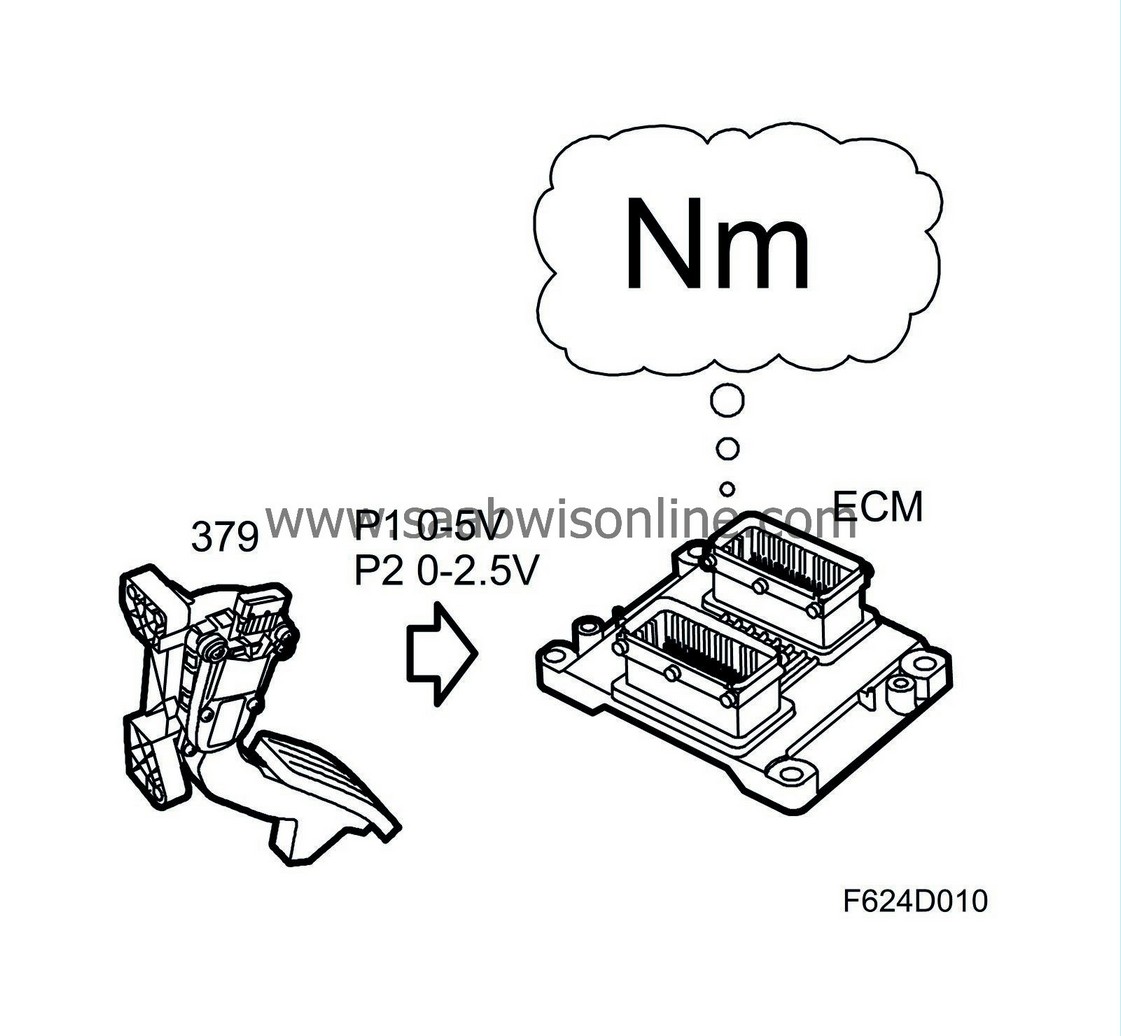
General
Two potentiometers are integrated in the accelerator pedal bracket. Potentiometer 1 provides ECM with information on the driver's torque request in the form of a voltage signal 0-5V.Potentiometer 2 is a safety potentiometer that provides ECM with information on the pedal position in the form of a voltage signal 0-2.5V. This voltage is used to ensure that information from potentiometer 1 is reliable.
If the information from the potentiometers does not agree, one of them must be malfunctioning. The engine throttle control will then go into limp-home mode.
Function
Pedal potentiometer 1 provides ECM with information on the drivers torque request. The pedal position together with the engine speed gives a requested torque using a matrix. The torque request varies between 0 Nm (idling) and a value that is somewhat greater then the maximum torque allowed for the engine.To obtain good driveability and response to the pedal position, a given pedal position will give a higher torque at lower engine speeds and lower torque at higher engine speeds.
The torque request finally results in a requested air mass per combustion so that the engine can attain the requested torque.
Adaptation of pedal position
When the pedal is completely released, potentiometer 1 adapts the voltage value for the released pedal. This constitutes the idling position of the pedal. the lowest voltage value for potentiometer 1 is defined as a completely released pedal. Adaption occurs each time the ignition is switched on.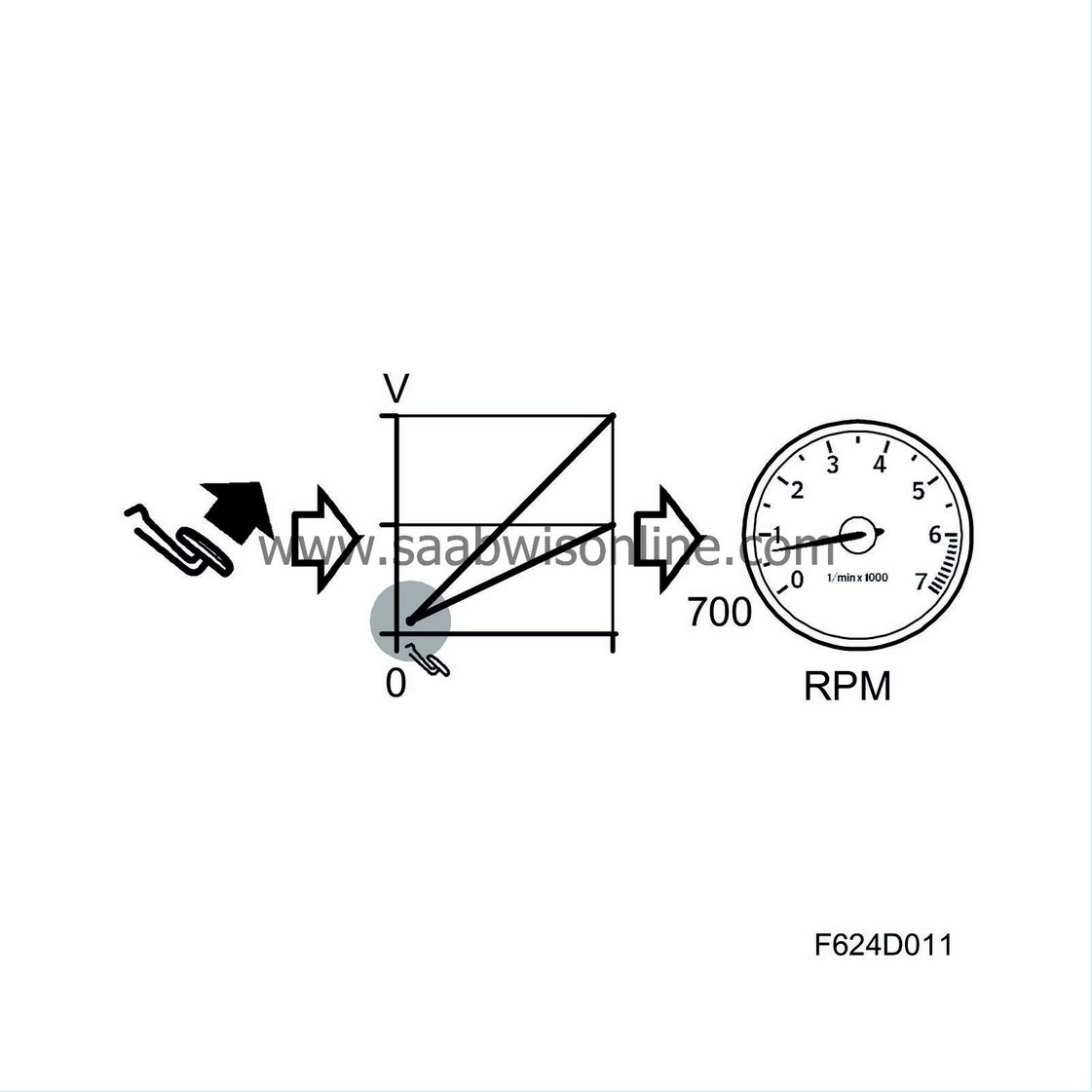
TCS/ESP |
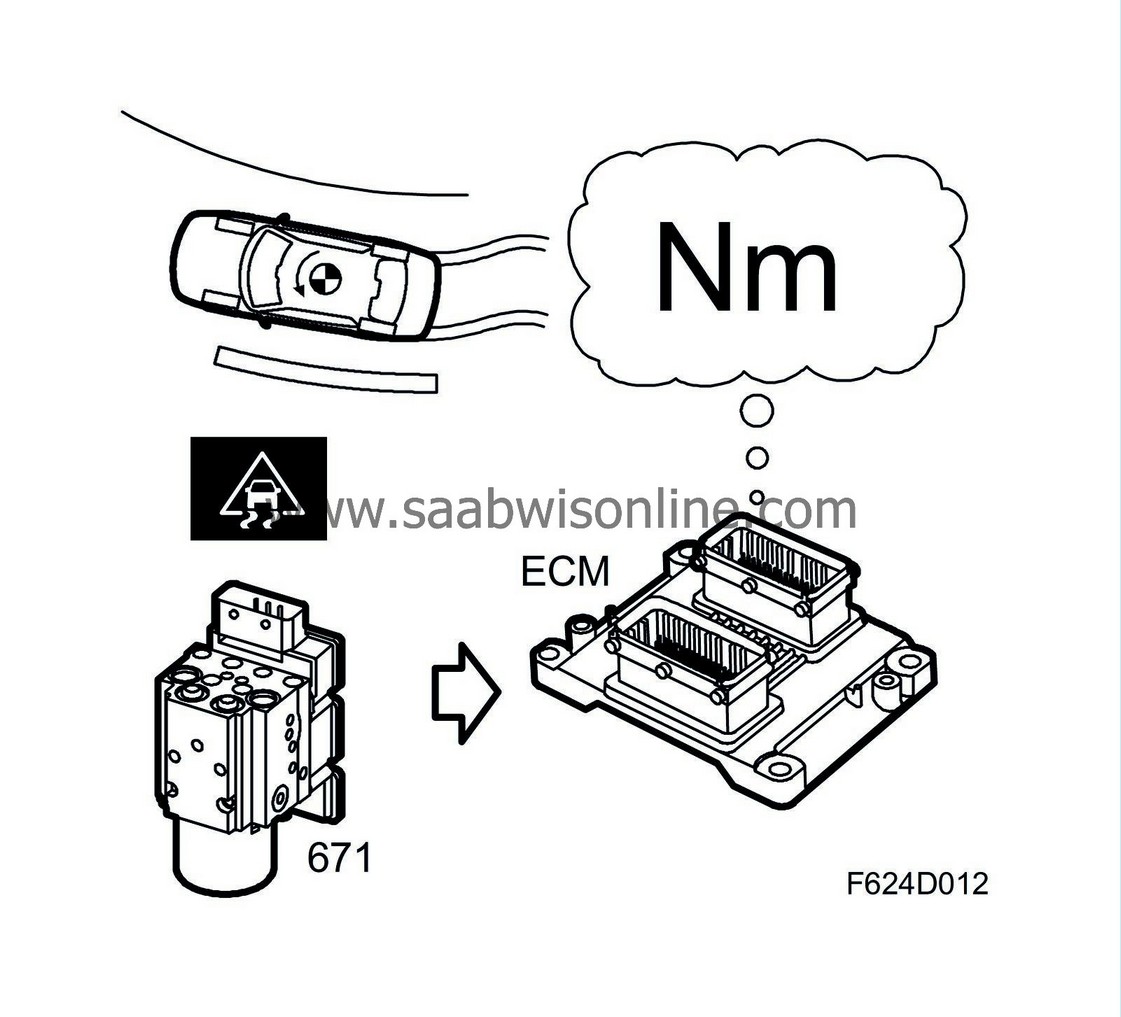
TCS/ESP request, general
In the event of wheel spin, TCS can request a limitation of engine torque (negative request) to counteract it. Likewise, ESP can request a limitation of engine torque if the car skids. TCS, but above all ESP, can request an increase in engine torque (positive request) to counteract a skid, for example.Function principle, torque limitation during TCS/ESP control
ECM works with the throttle area and ignition timing control to reduce engine torque during TCS/ESP control. In the event of large limitations, turbo control will also be actuated to reduce engine torque.Ignition timing control generates quicker torque changes, while regulating the throttle area is slower. Turbo control is the slowest.
Compensation for A/C compressor and generator |

General
Torque can be requested from this function in order to keep the specified engine torque independent from the prevailing load from the A/C compressor and generator. Consequently, this is a positive request.Compensation, A/C
The relay for the A/C compressor is controlled by ECM, which also reads the prevailing pressure in the A/C system via the pressure sensor (620). In this way, ECM can calculate the torque that must be added to compensate for the torque taken by the A/C compressor.Compensation, generator
The generator informs ECM of the prevailing load through a wire from generator connection L. In this way, ECM can calculate the torque that must be added to compensate for the torque taken by the generator.Maximum permissible engine torque |
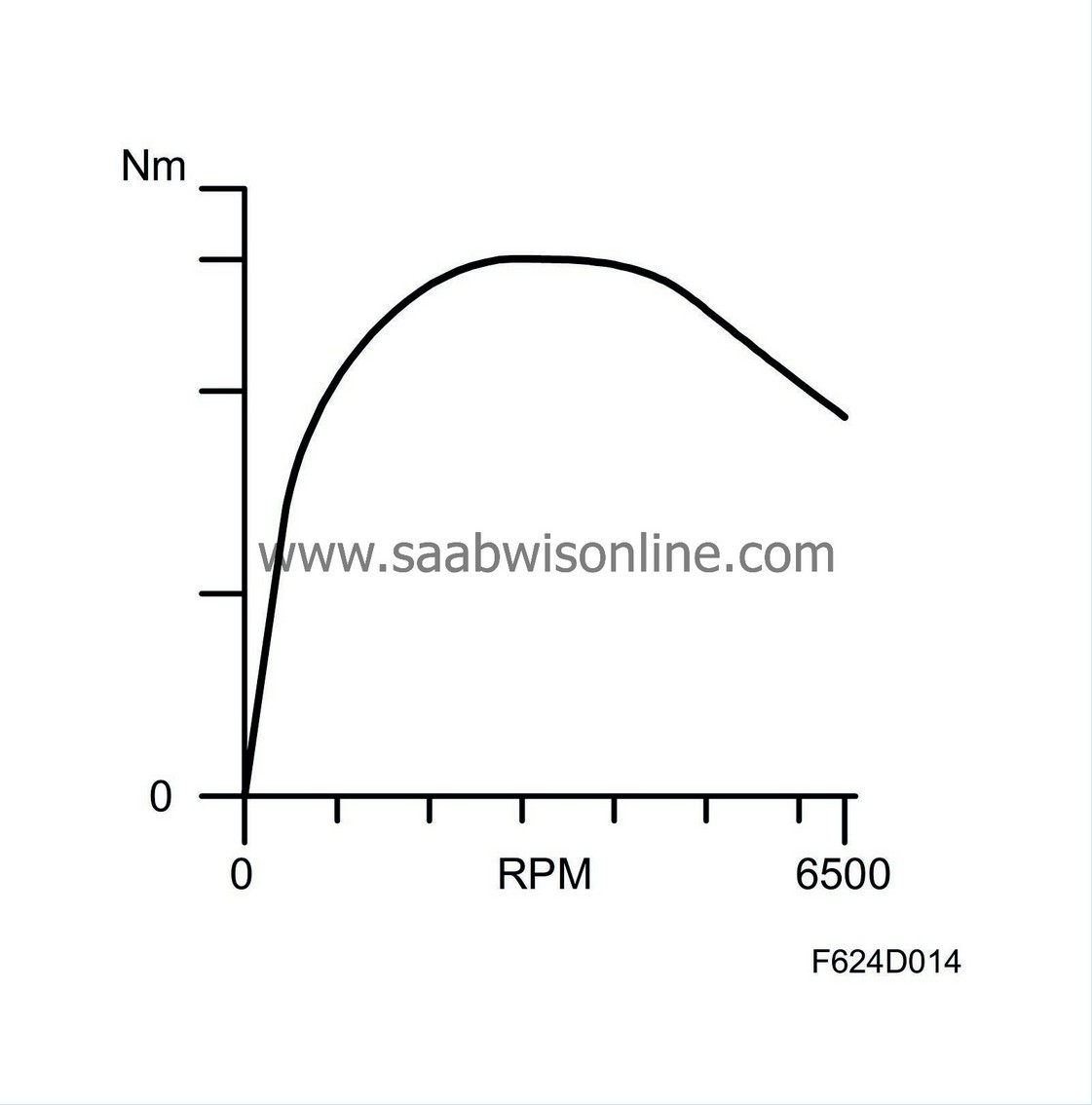
General
The maximum engine torque allowed for the engine is stored as a table in the control module memory. The table specifies the highest torque the engine is allowed to generate at various engine speeds.Calculation, engine torque
Engine torque is primarily calculated using air mass per combution and engine speed. But, ignition timing and current lambda value also affect the torque calculation. Retarded ignition timing generates lower engine torque. This is the case in knock control. As regards the lambda value, there is an optimal lambda value for each operating point. If the engine runs richer or leaner than the optimal value, engine torque reduces.Note that a lambda value lower than the optimal value (richer mixture) produces lower torque.
The calculation also takes into account the torque used by the engine itself, i.e. the internal friction. Values for air mass, engine speed, coolant temperature and idling torque are used for this calculation.
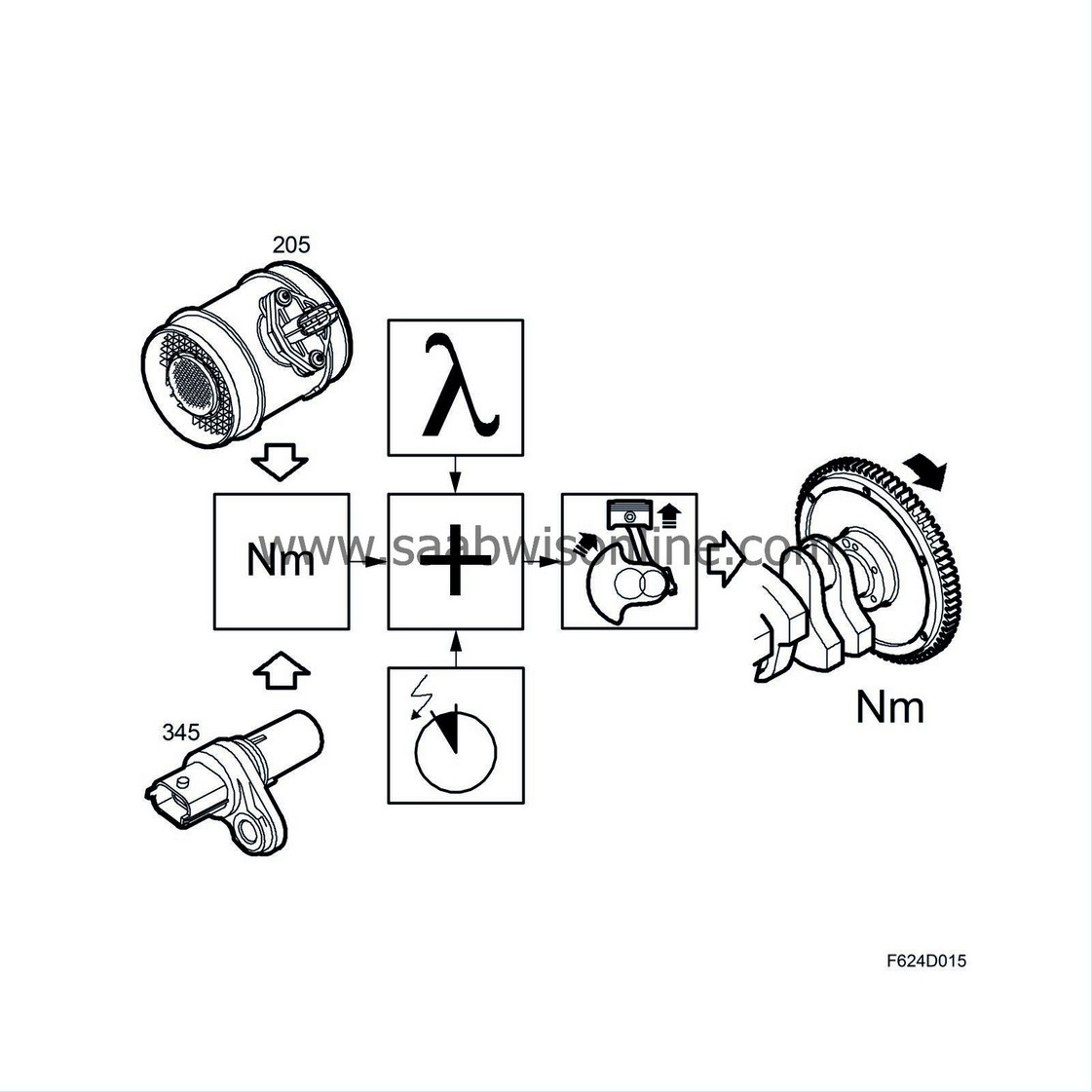
TCM |
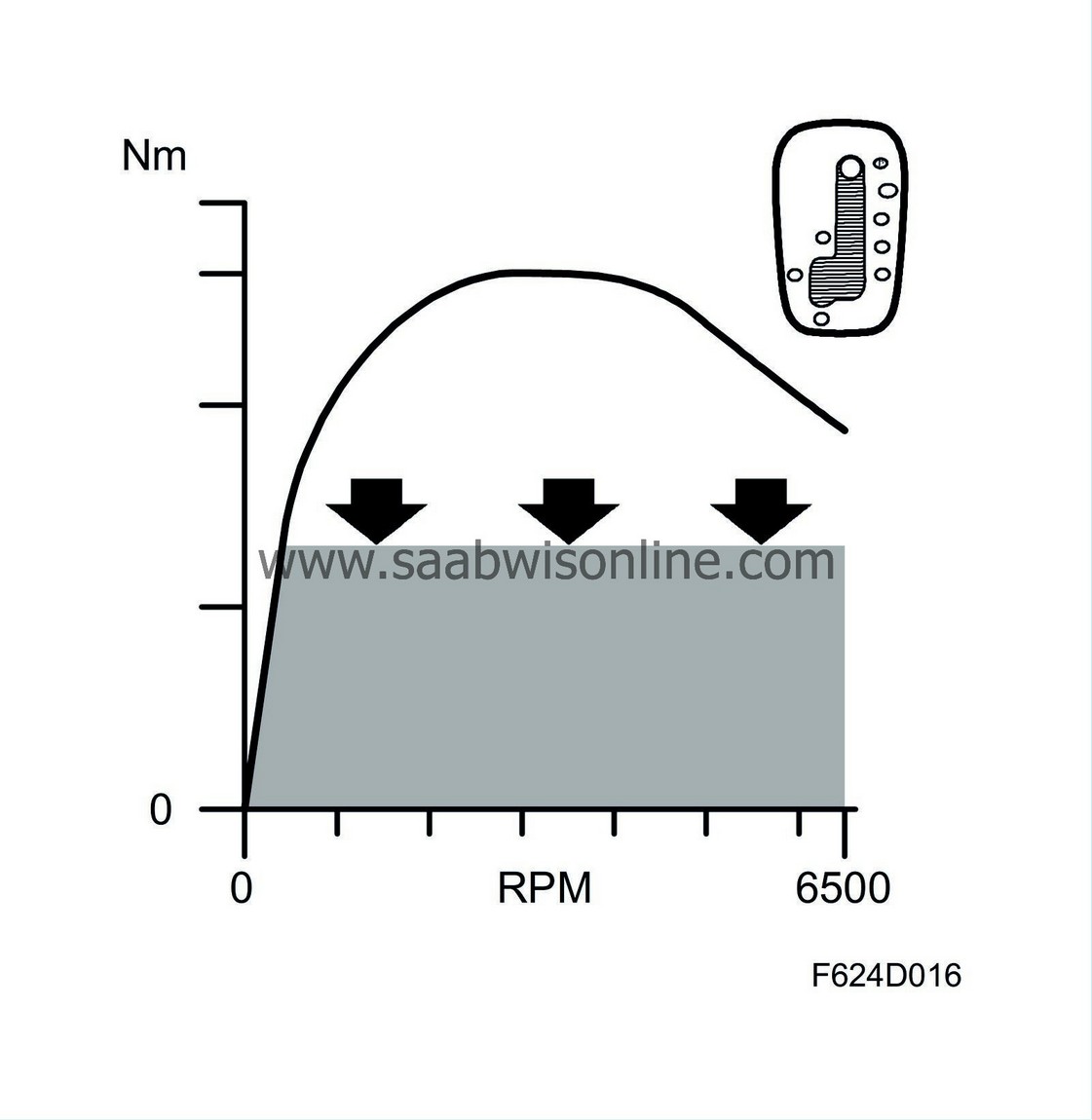
Torque limitation, automatic gearbox
Engine torque must occasionally be limited for the sake of comfort in gear changing and in certain cases also for reasons of durability.Engine torque limitation, bus from TCM
TCM determines the maximum engine torque to be allowed. During gear changing, engine torque is often reduced somewhat for comfort. Torque can also be reduced for reasons of durability.Engine torque limitation, stalling
Engine torque for a stalling gearbox is limited to 200 Nm to protect the gearbox.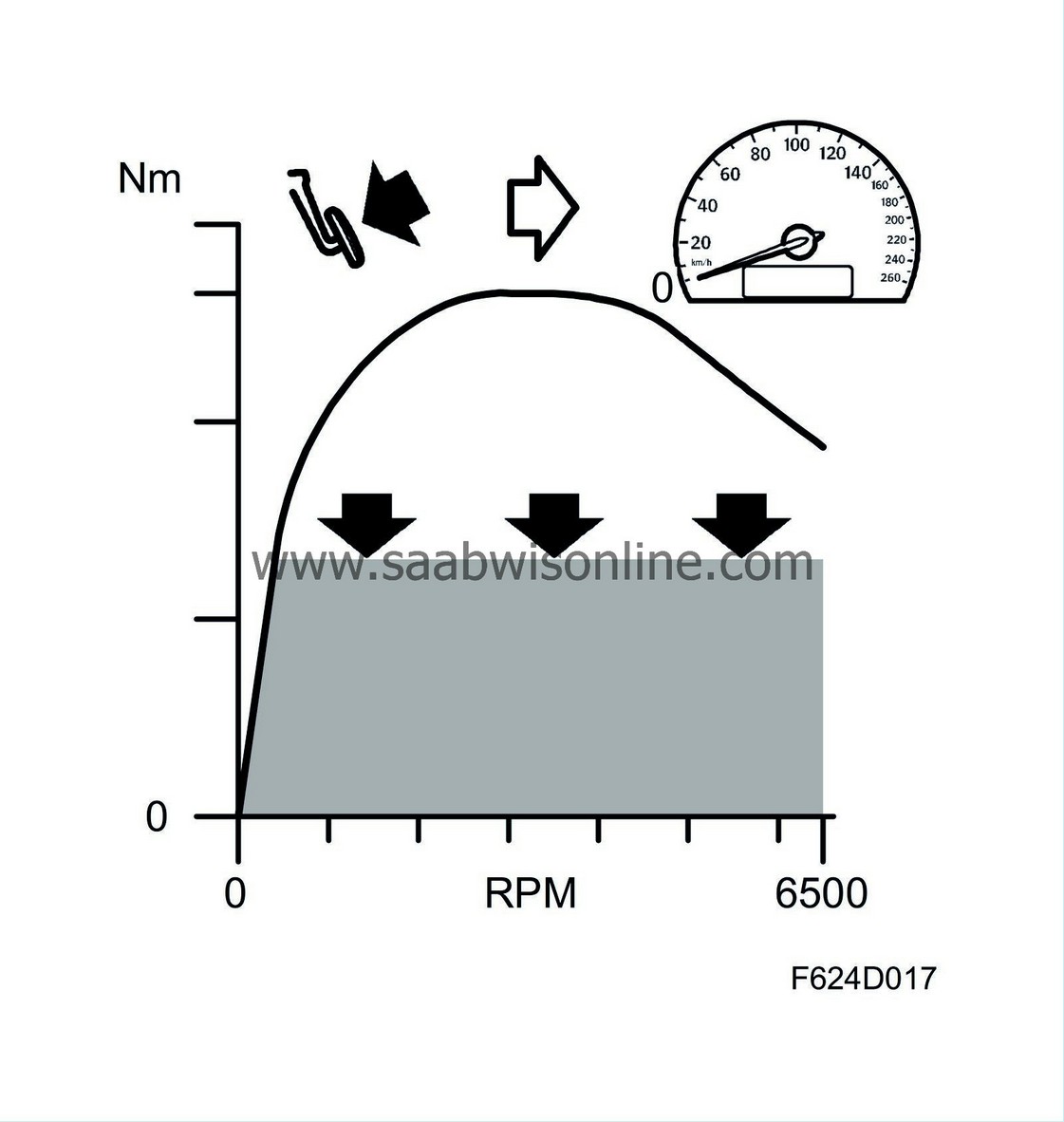
Manual gearbox |
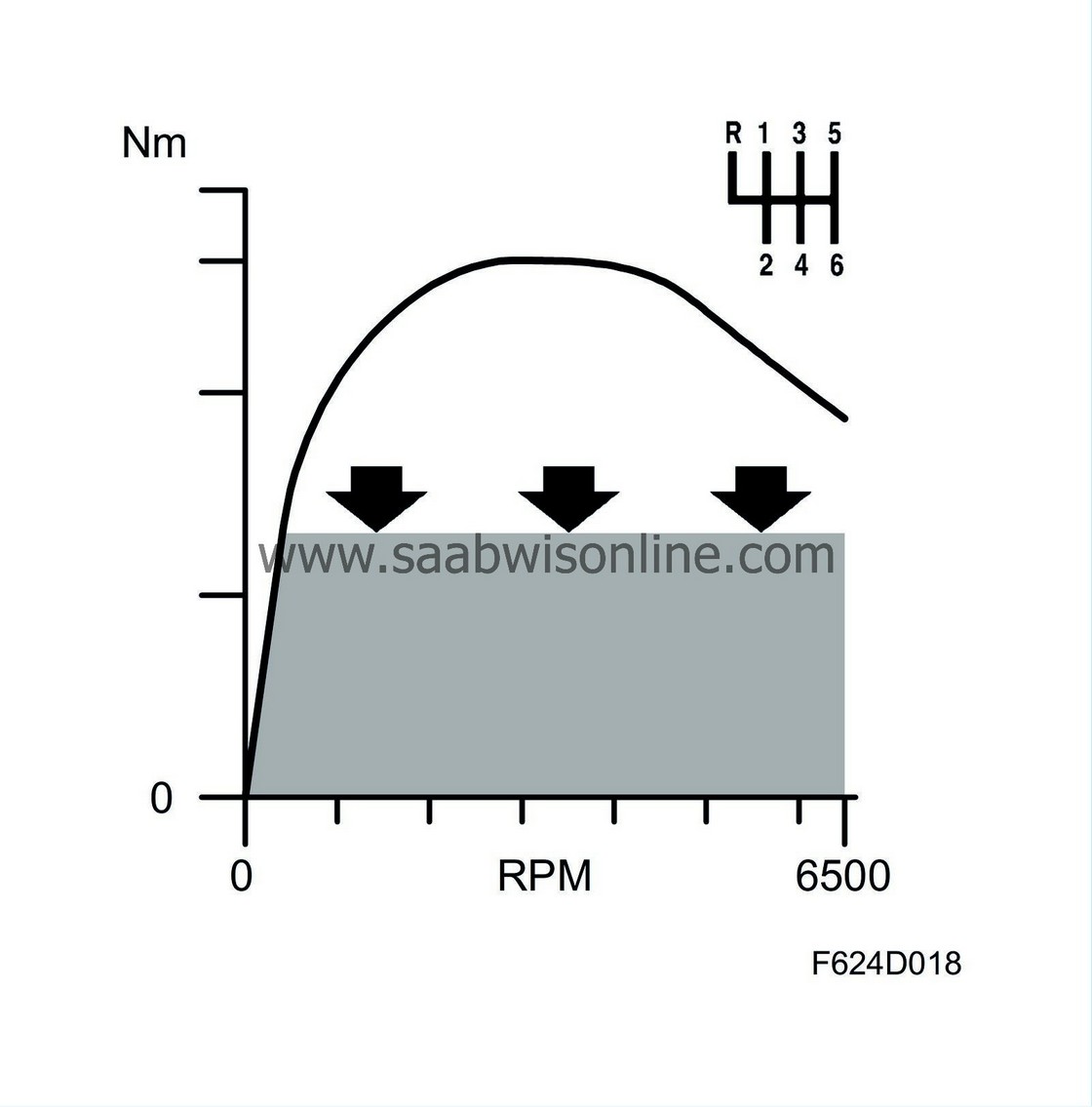
Torque limitation, manual gearbox
ECM calculates the current gear via vehicle speed and engine speed. The following gears are subject to torque limitation:• |
1st gear
|
• |
Reverse gear
|
Other limitations |
Engine protection function
Under certain operating conditions, engine torque must be limited to prevent damage. Examples of protective functions: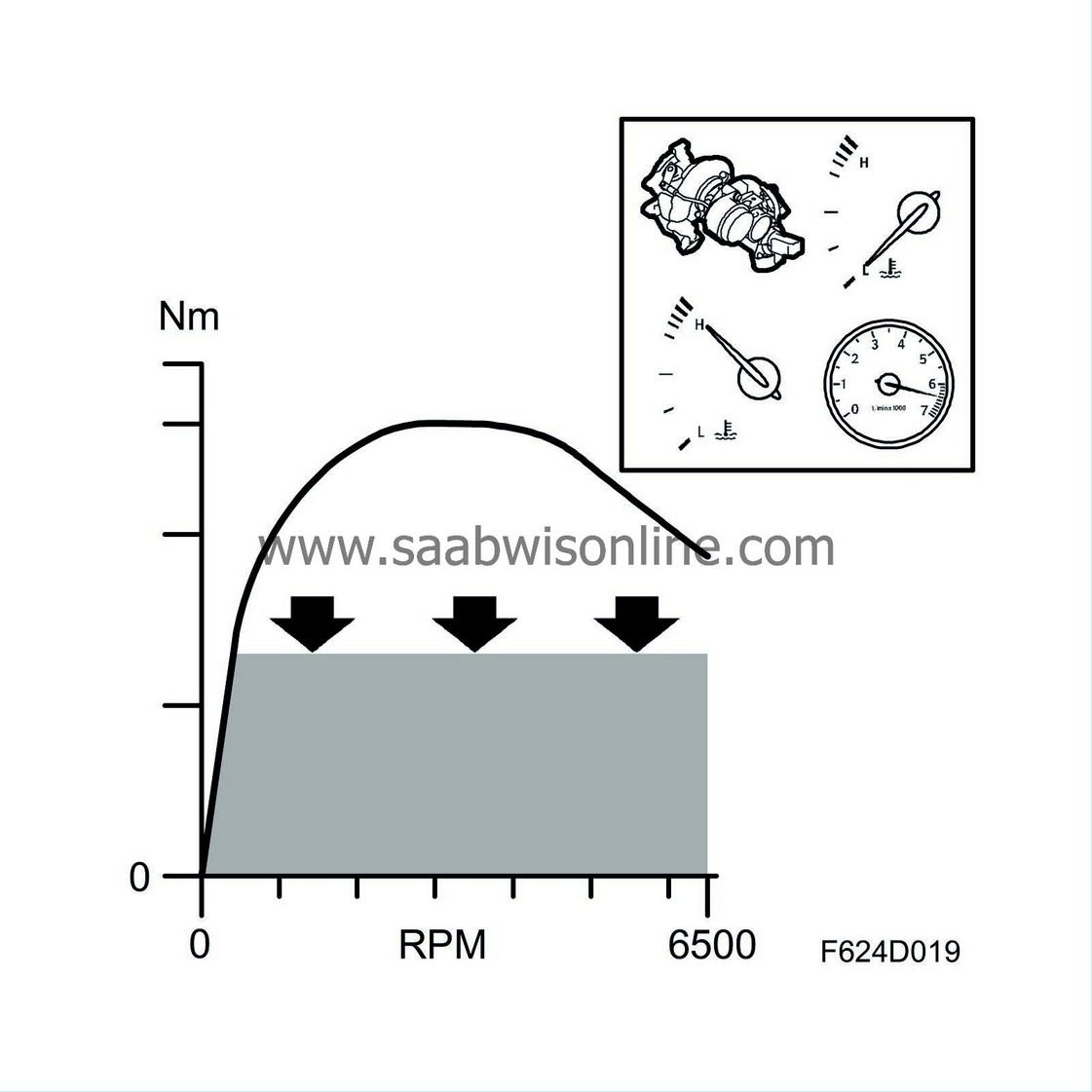
• |
When driving at high altitudes, engine torque may be limited to prevent the turbocharger from overrevving.
|
• |
When the engine is cold, engine torque is limited to prevent engine damage.
|
• |
If there is a risk of overheating, engine torque is limited by restricting air mass and through fuel cut-off.
|
• |
Limitation of maximum permissible engine speed.
|
Torque limitation in the event of a diagnostic trouble code
Certain diagnostic trouble codes cause torque to be limited in order to prevent damage.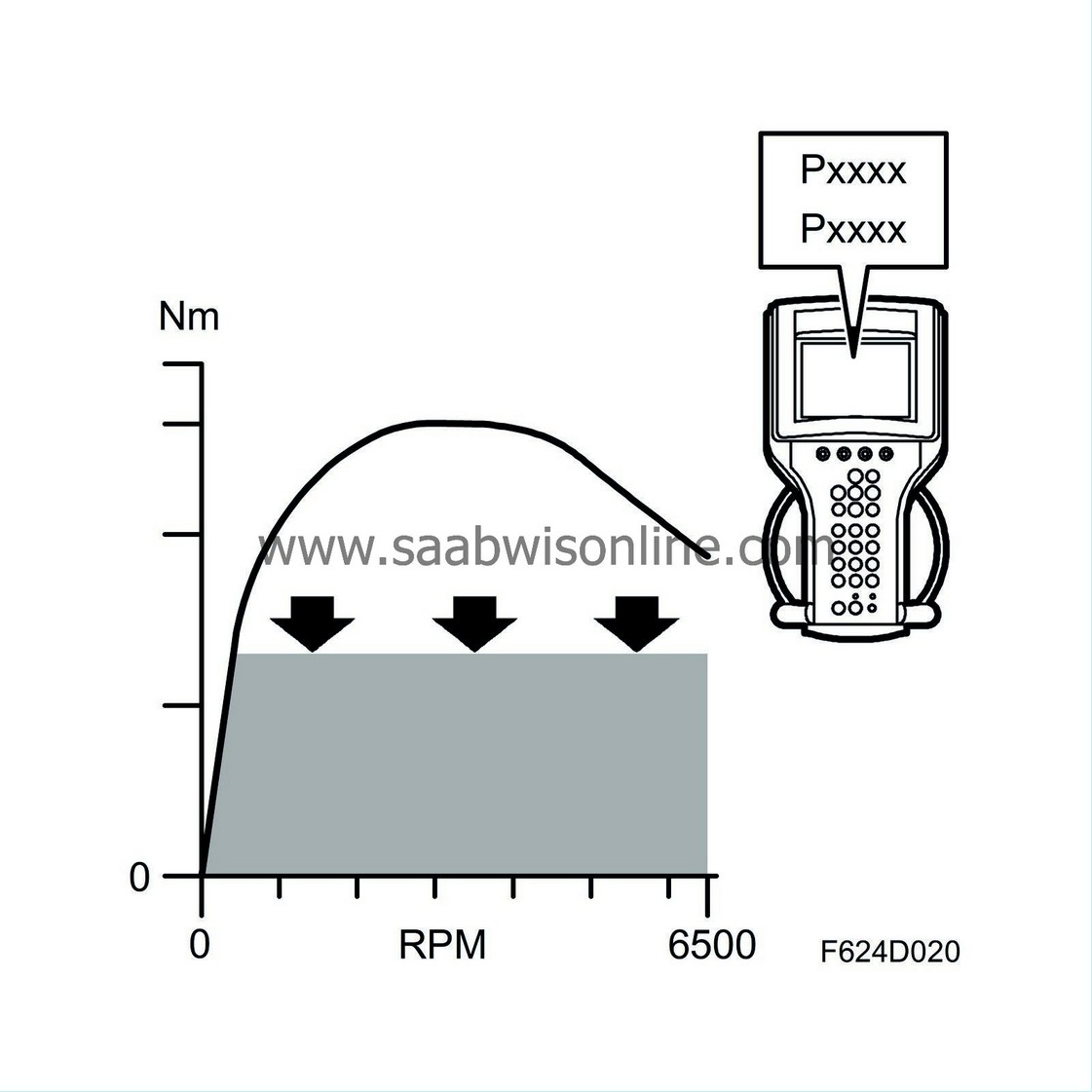
Brake
Maximum permissible engine torque must be limited when the brake pedal is depressed for reasons of durability.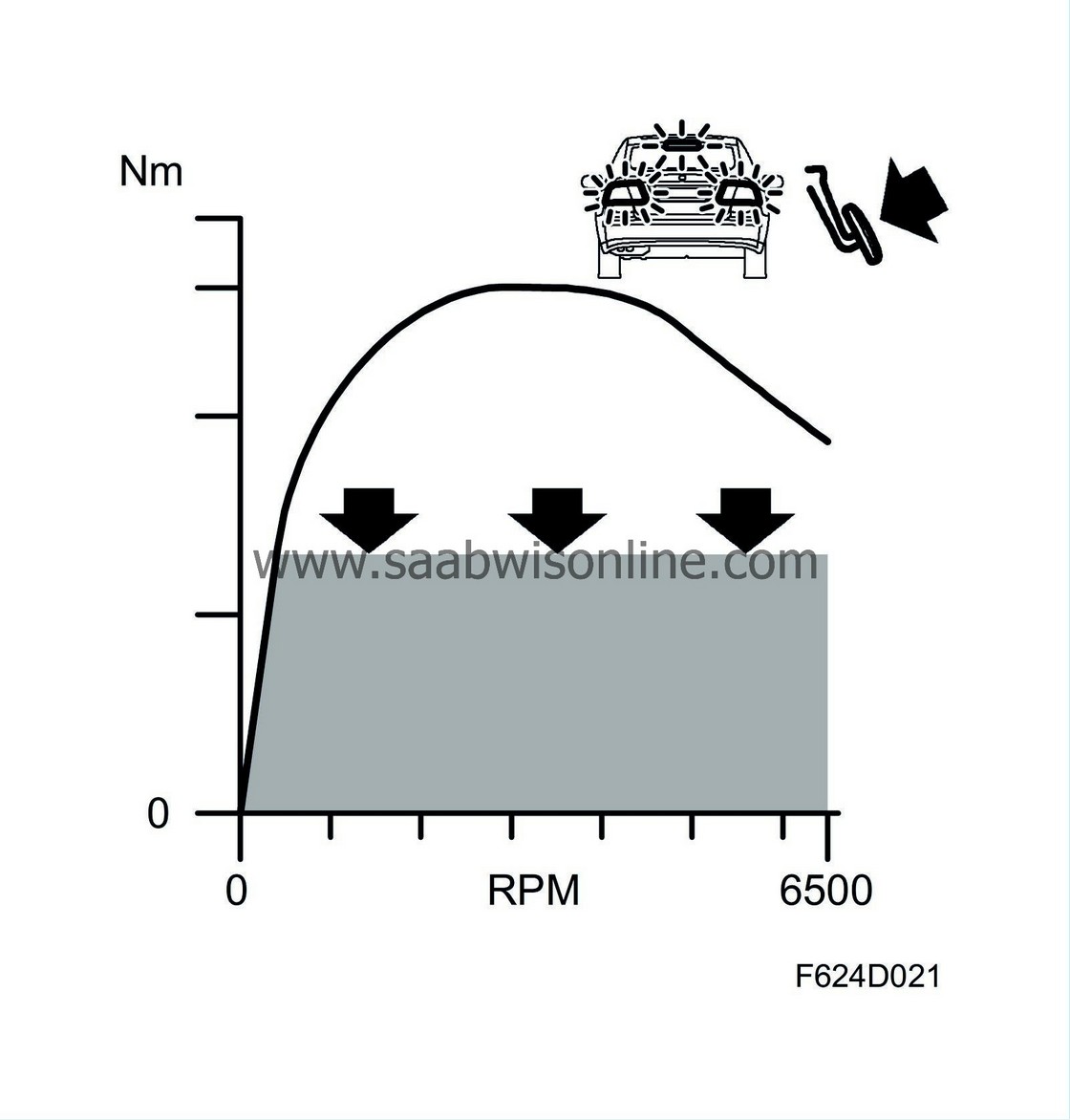
Safety-related fault in throttle control.
If there is a safety-related fault in the throttle control, throttle control is in limp-home mode or pedal sensor is in limp-home mode, the engine's maximum torque is limited.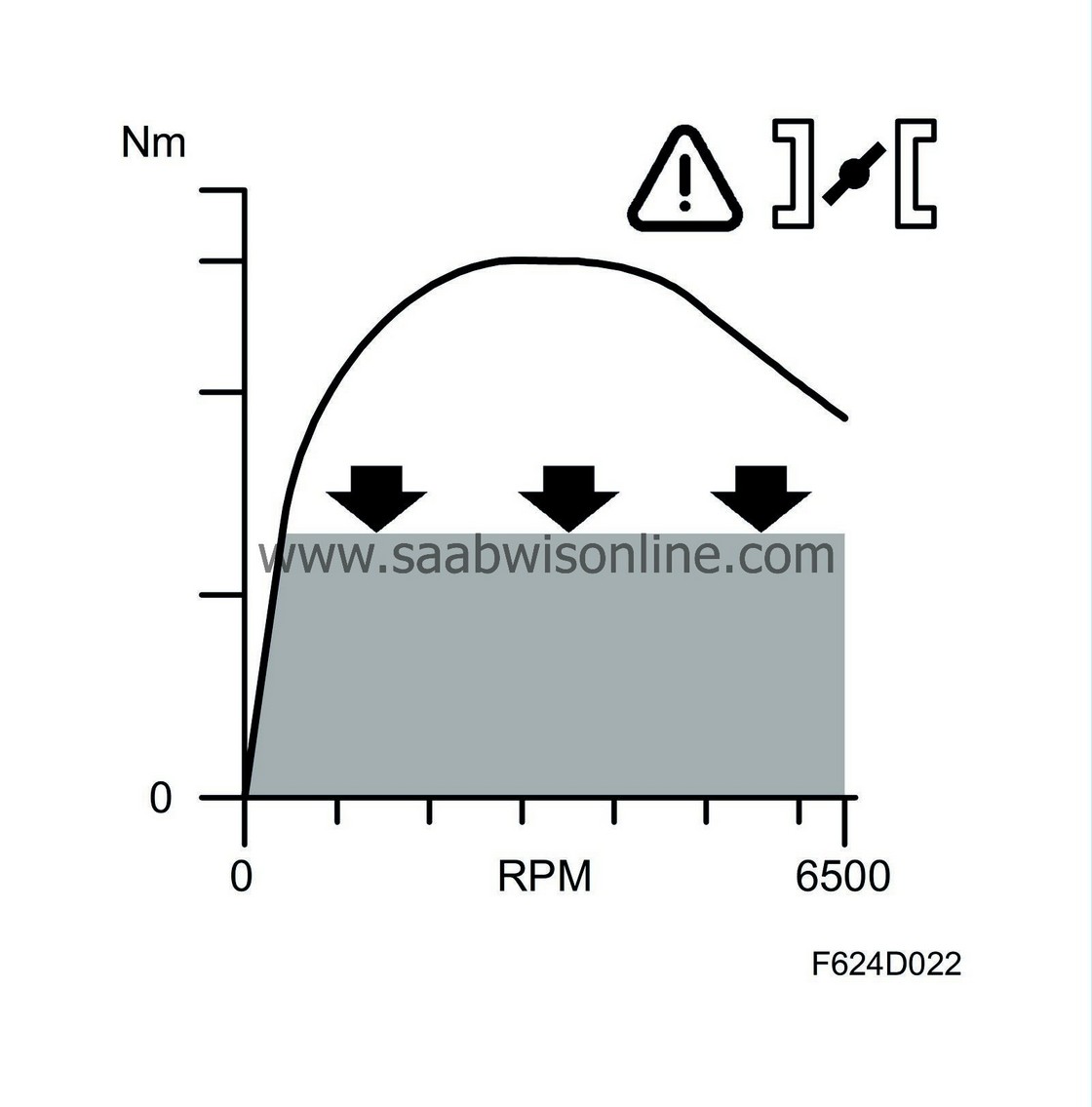
Misfiring
To protect the turbocharger and the catalytic converter in the event of misfiring, engine torque is limited if there is a risk of overheating. The degree of misfiring that is allowed without engine torque limitation depends on the current operating point, engine speed and load.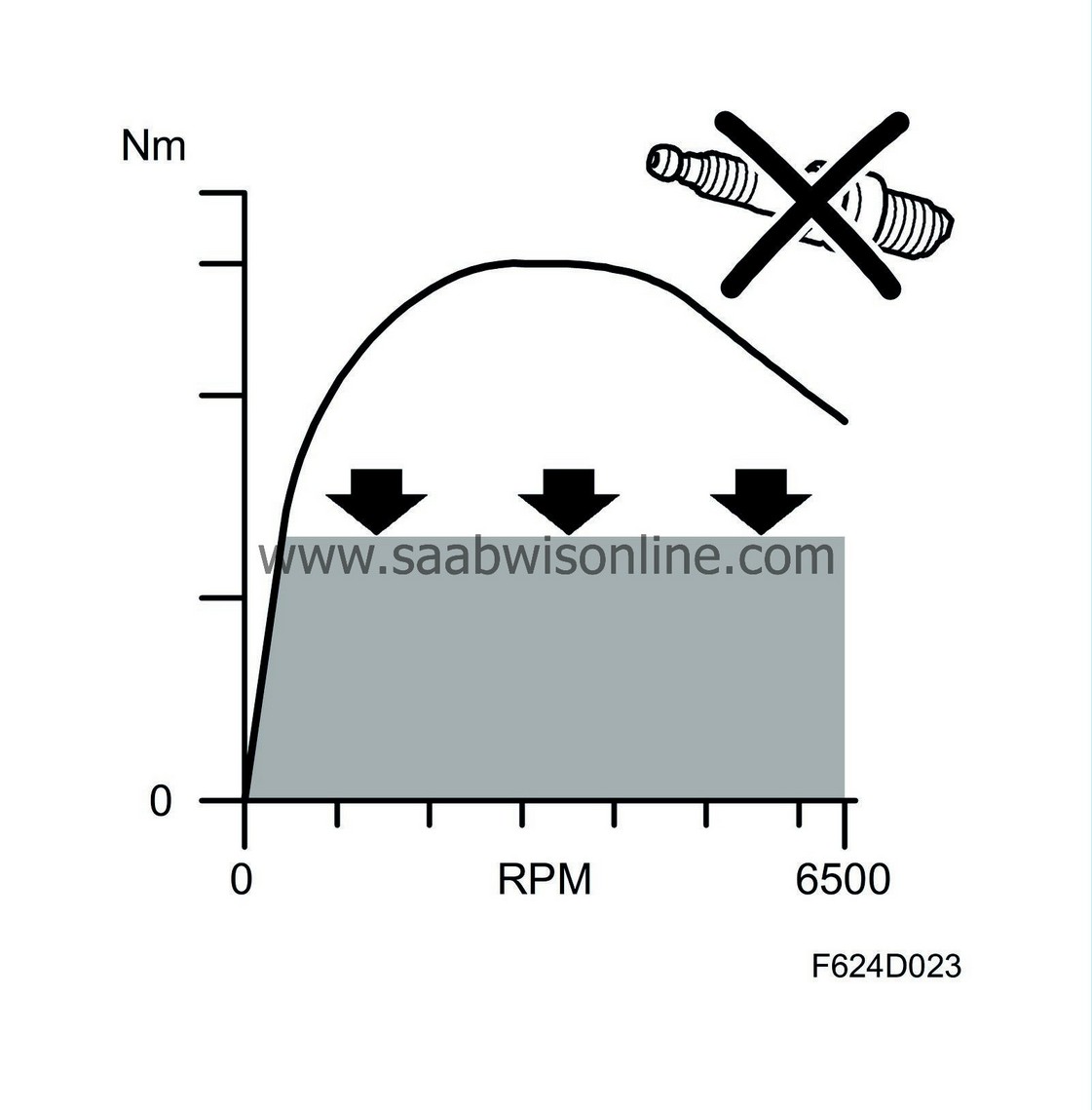
Emission limitation
Increases in engine torque can be limited in order to reduce emissions. A rapid increase in torque requires relatively high fuel enrichment, giving higher exhaust emissions.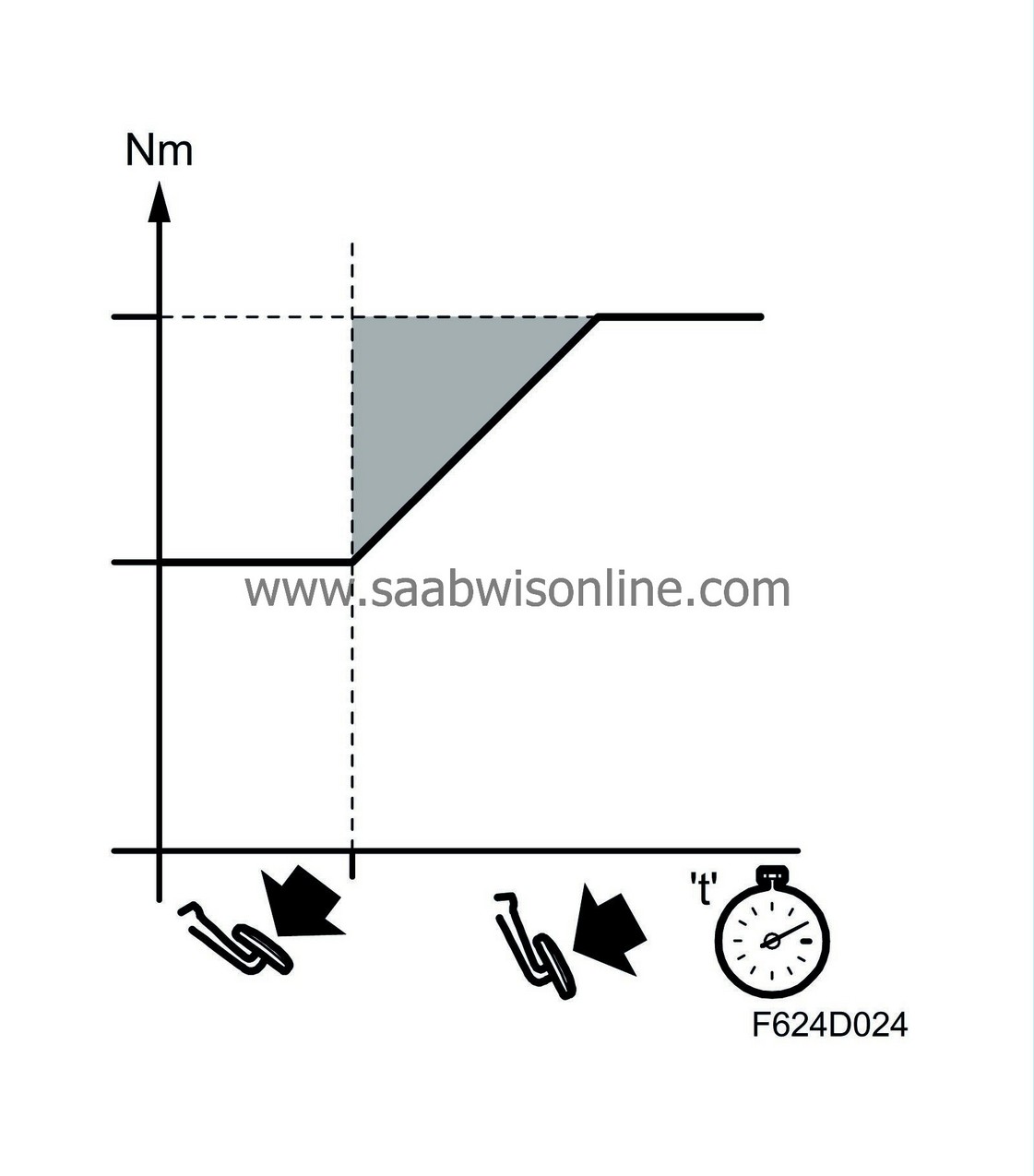
Active surge dampening
Surges (variations) may occur during acceleration. These are caused by sudden increases in engine torque combined with a certain elasticity in the power train and engine mountings. Through compensation, these variations can be reduced or eliminated completely.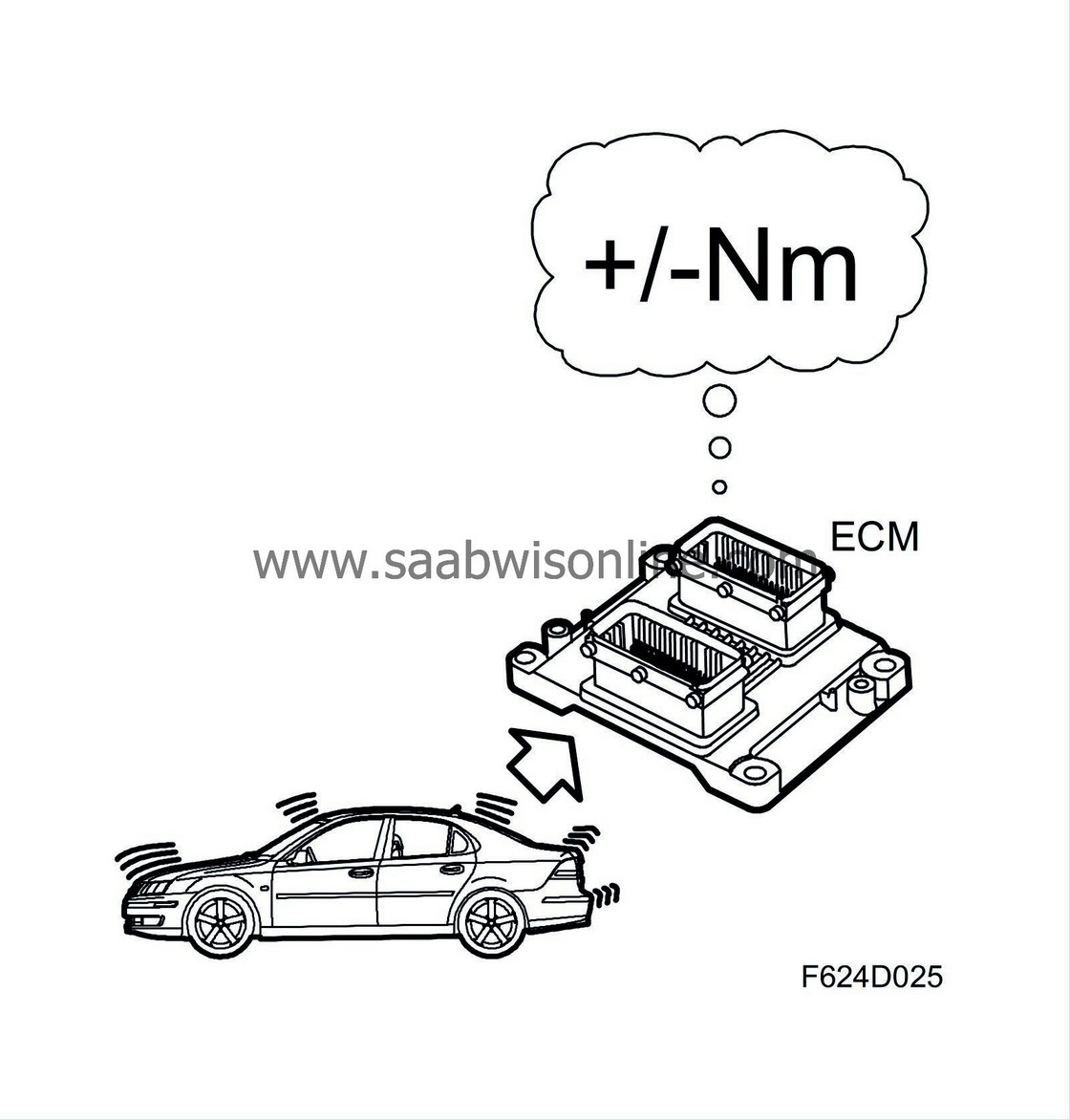
The anti-surge function detects variations in engine speed and dampens them by changing engine torque via ignition timing, which is usually retarded.
Maximum permissible vehicle speed
If vehicle speed exceeds the programmed value for speed limitation, the function limits engine torque, thus limiting the car's maximum speed.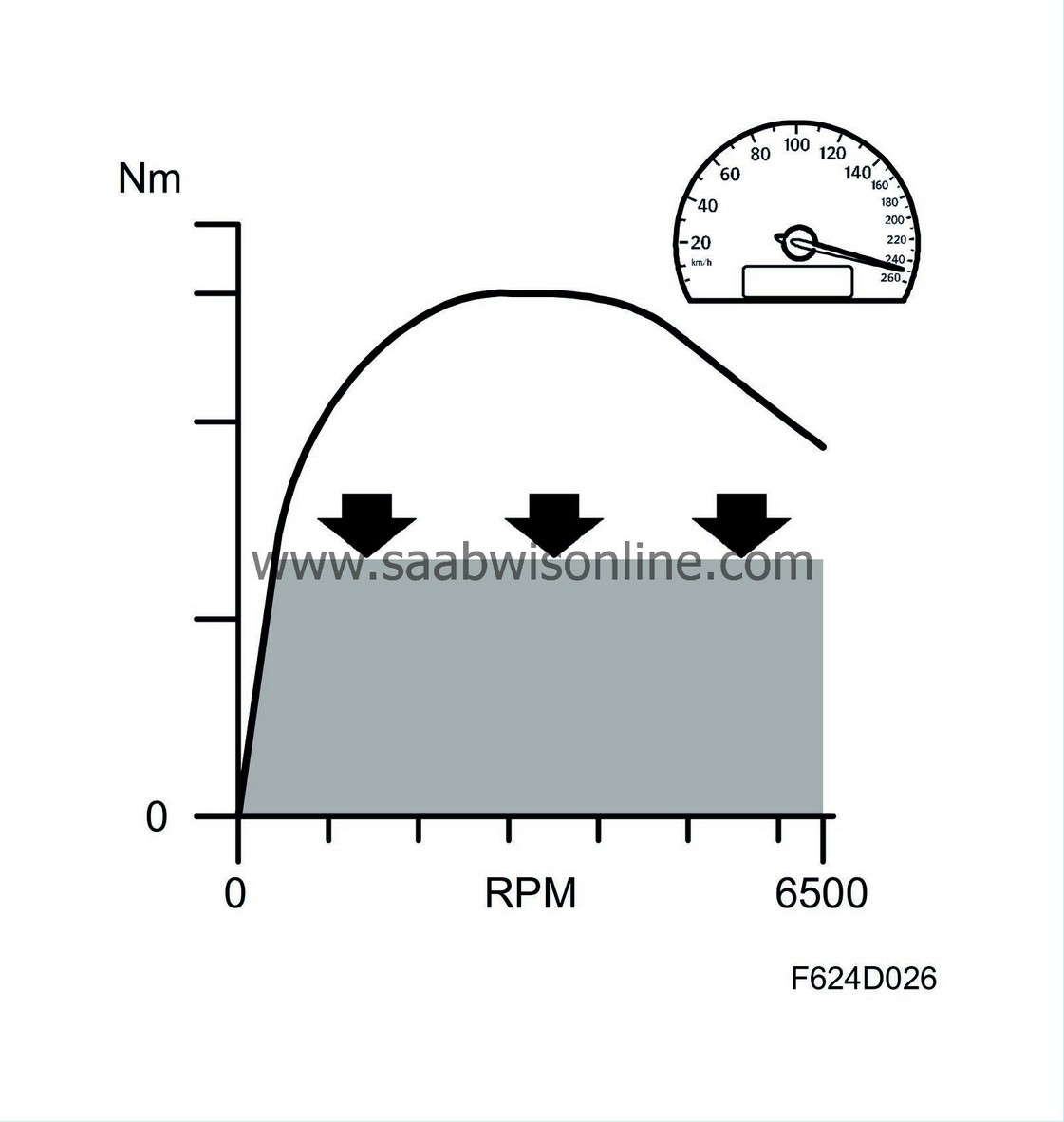
Torque request from the system |
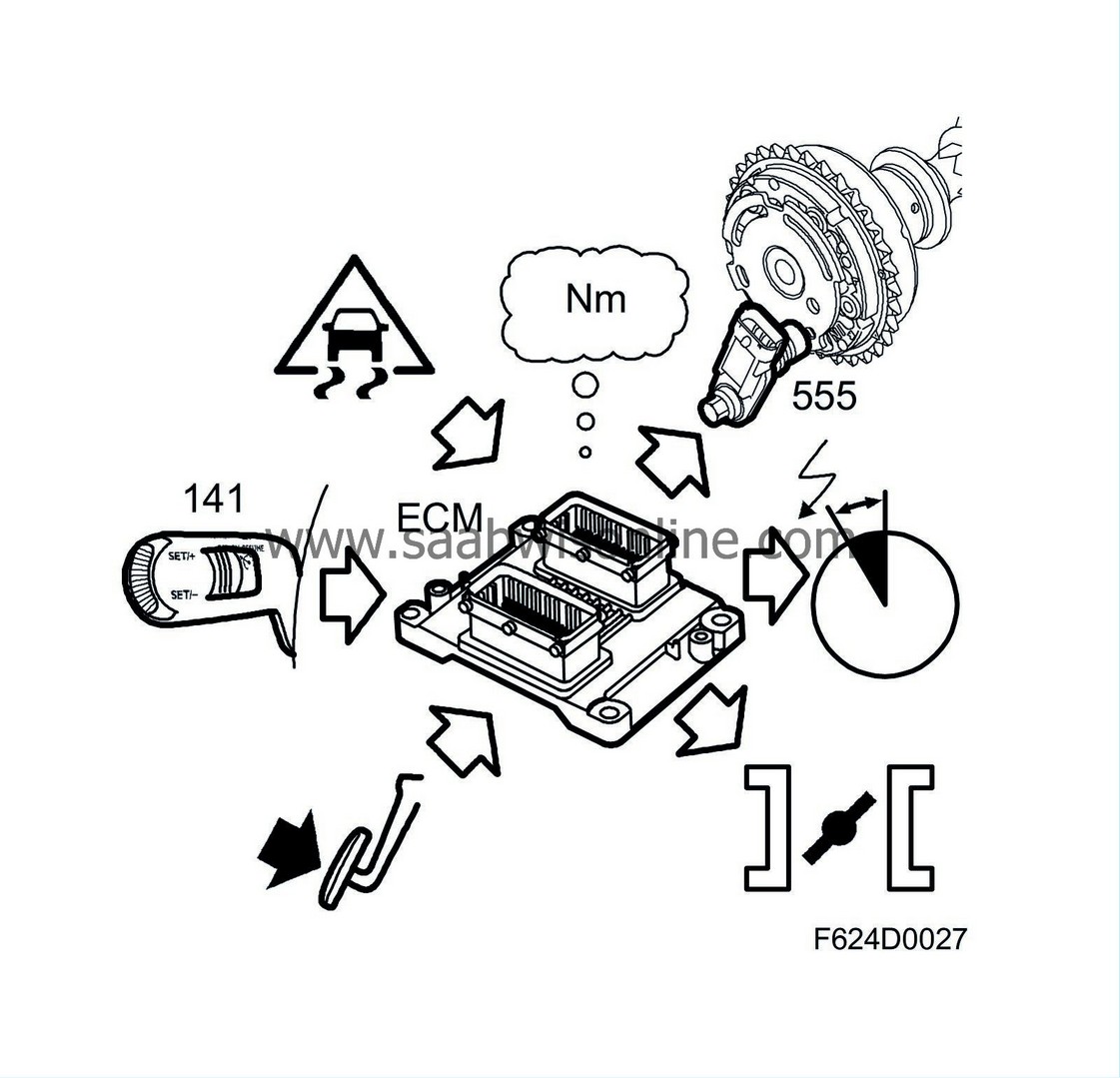
General
The highest value is chosen from among the functions that can limit torque, e.g. acclerator pedal 400 Nm. This value is sent on to the function for limitations, at which time the lowest value is selected. It is usually "maximum permissible engine torque" that is the limiting function. This value may change as it is dependent on engine variant. Let's say the value is 350 Nm. The driver requests 400 Nm via the accelerator pedal, but the system only allows 350 Nm for this engine variant. The value 350 Nm is the one chosen by the system.If the engine begins to knock due to poor fuel, "knock control" limits torque to 300 Nm, for example, to prevent engine damage. In this case "knock control" is lower than "maximum permissible torque", thus "knock control is selected.
The system's torque request is sent on to the sub-functions:
• |
Throttle adjustment
|
• |
Ignition
|
• |
Turbo adjustment
|
• |
CVCP control
|
Throttle adjustment, general
The throttle is turned by a DC motor via a reduction gear. ECM supplies the motor a PWM signal from pins 15(A) and 31(A). ECM can turn the throttle disc in either direction, i.e. in a closing or opening direction. A spring strives to keep the throttle in a slightly open position, which is its rest position.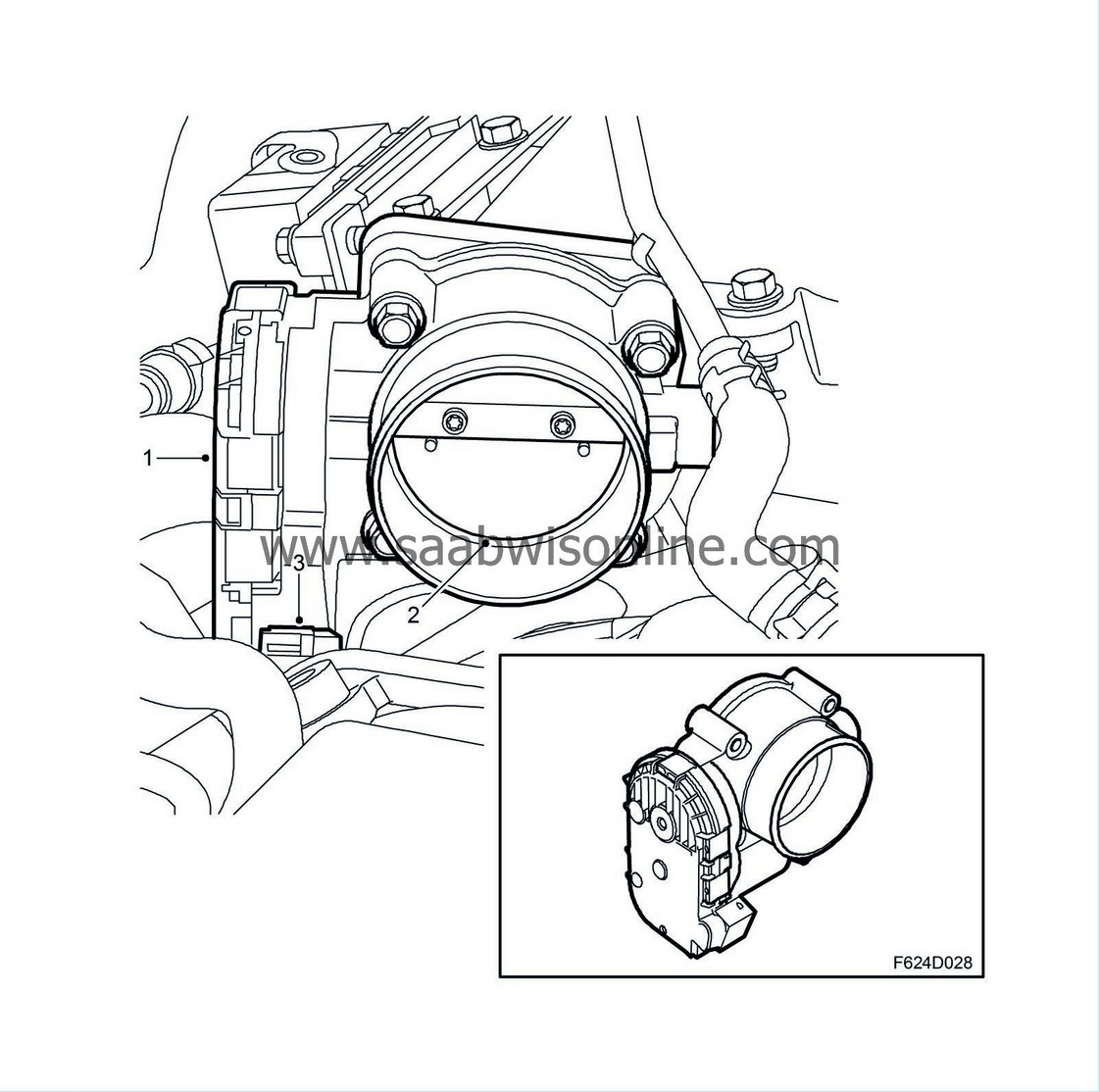
During limp-home in the throttle control, it is this position that provides the throttle area and thereby controls the air mass/combustion that can enter the engine. Cylinder cut-off (fuel cut-off) and ignition timing are used as regulating instruments to control engine torque. Idling speed is about 900 rpm. The engine runs unevenly at low load due to cylinder cut-off. The car can be driven, but with greatly reduced performance.
Two throttle position sensors are conencted to the shaft. The sensors comprise potentiometers that are supplied 5 V from ECM pin 54(A) and are grounded in ECM pin 39(A).
The voltage from potentiometer 1 is connected to ECM pin 55(A) and increases as the throttle opening (area) increases. Voltage from potentiometer 2 is connected to ECM pin 8(A) and reduces as the throttle opening (area) increases. Thus, the total of the voltages is always 5 V.
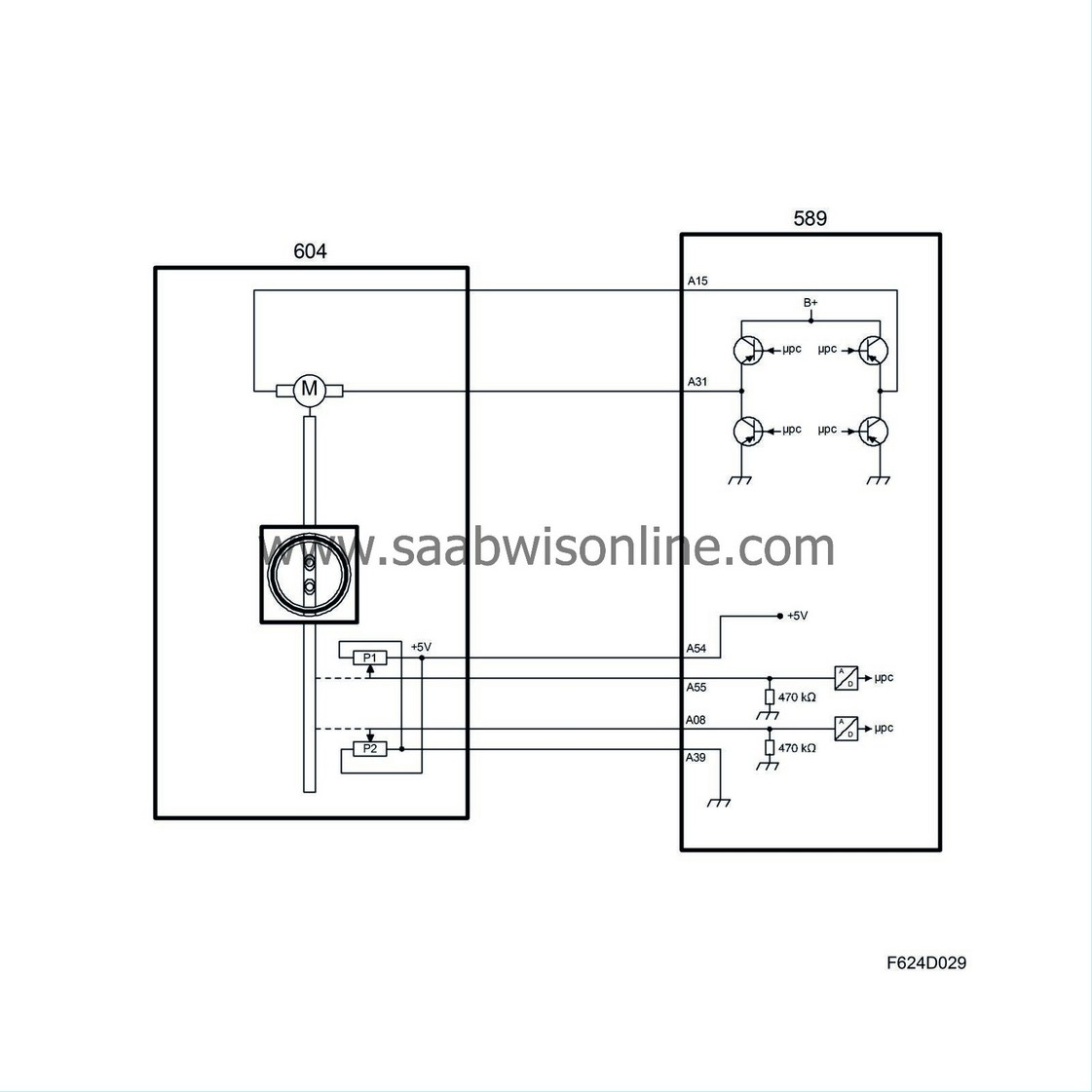
ECM uses the value from potentiometer 1 to detect the current throttle opening (area).
Throttle control, principle
The value from torque control is converted to air mass/combustion. Throttle control converts this to a specific requested value for throttle position sensor 1 and compares the requested value with the actual sensor value. The difference (deviation) gives rise to a throttle motor PWM of a magnitude and polarity that will turn the throttle until the desired value (area) is obtained. If there is a major fault in throttle control, it is deactivated and the throttle disc assumes its rest position, which is controlled by a spring. At this time, engine torque can only be regulated through cylinder (fuel) cut-off and ignition timing.
When the system's total requested air mass/combustion (engine torque) has bee calculated it is realized by the throttle and, if necessary (high engine load) turbo control. CVCP control works in parallel with the throttle and turbo control.
Requested air mass/combustion is corrected with the density of the charge air (air before throttle). Thinner air (lower density) gives a greater throttle opening angle (larger area) so that the same air mass/combustion is obtained as with normal air density.
Air density is calculated using the charge air absolute pressure and the temperature.
This value is converted to a certain requested value for throttle position sensor 1. The requested value is compared to the current value of the sensor. The difference (deviation) gives rise to a throttle motor PWM of a magnitude and polarity that will turn the throttle until the desired value (area) is obtained.
The PWM value is finely adjusted if necessary so that the requested position agrees with the current one, i.e. zero deviation.
If the requested air mass/combustion is too high to be treated (attained) by throttle control only, the excess (difference) is handled by turbo control.
In the event of a safety-related fault in throttle control, it will go into limp-home mode. The Check Engine symbol will illuminate immediately. A message appears in SID to indicate that engine performance is limited.
Note | ||
It is entirely normal if the throttle is not completely open when the accelerator pedal is completely depressed. |
Turbo adjustment
The airflow from the turbocharger is regulated by a solenoid valve, which controls the exhaust turbine wastegate pneumatically.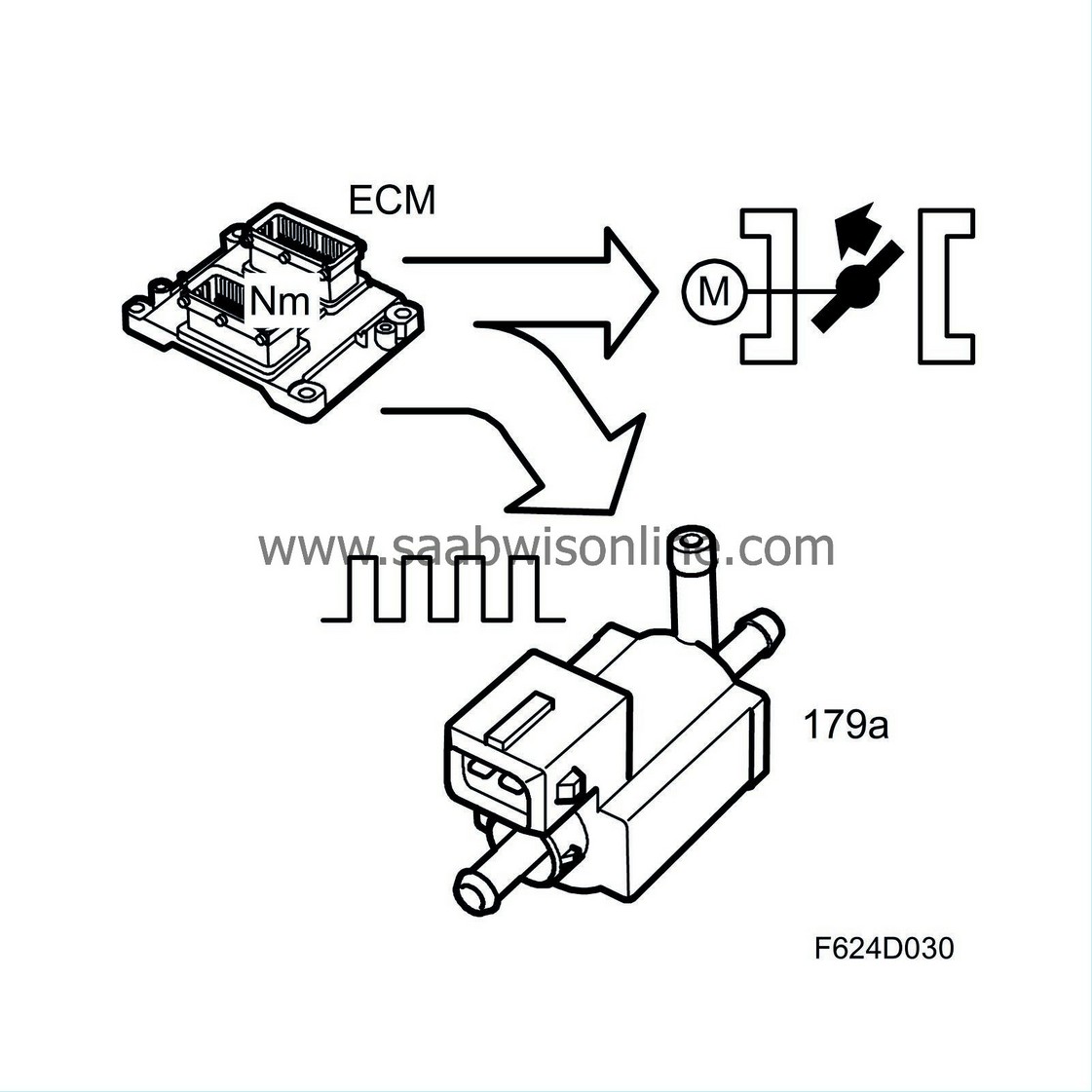
The solenoid valve (179a) is supplied voltage from the main relay (229) and is grounded from control module pin 14(A) with a 32 HZ PWM. The wastegate valve goes opposite the closing direction when the pulse ratio increases, thus increasing compressor flow.
When the requested air mass/combustion (torque) is too great to be regulated by the throttle alone, the turbo control must satisfy the excess requirement. The excess is converted to a PWM that controls the charge air control valve.
ECM calculates the necessary (requested) boost pressure to achieve the desired engine torque.
The values for atmospheric absolute air pressure and intake air temperature are used to correct the conversion. At low atmospheric pressure or when the intake air temperature is high, a greater PWM ratio is required to obtain the same engine torque.
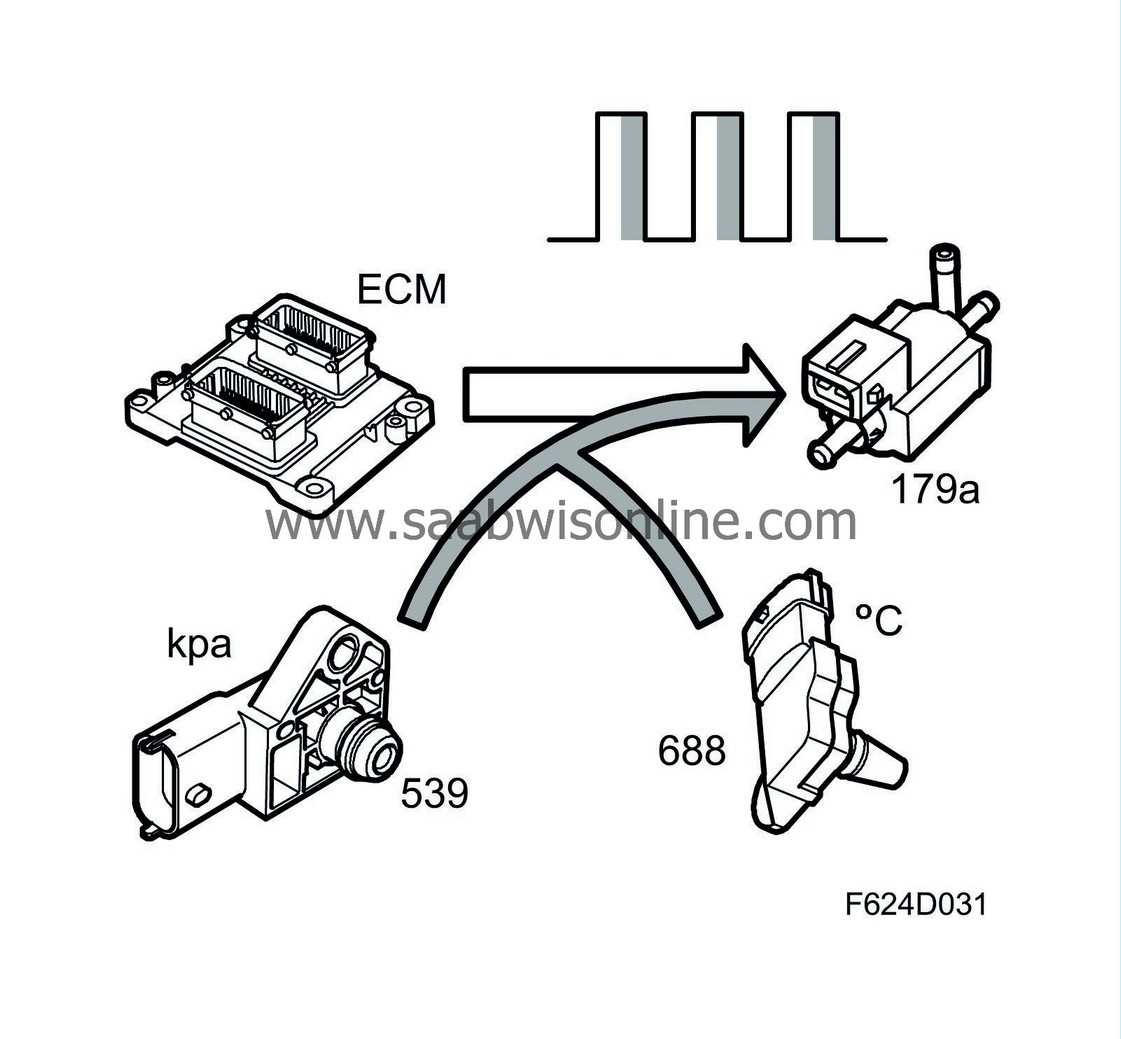
The control module checks that the actual boost pressure agrees with the requested one. If necessary, the PWM ratio is fine-tuned by being multiplied by a correction factor.
The correction factor (adaptation) is stored in the control module memory and is always included in the calculation of the PWM ratio.
The purpose is to make actual torque and request torque the same as soon after a load change as possible.
CVCP control
ECM regulates camshaft position based primarily on engine speed and load. A number of other values are used for minor compensations. Based on these values, ECM calculates requested camshaft position, converts it to the necessary PWM value and sends it out to the valves. A Hall sensor reads the position of the aperture discs and thereby the current position of the camshafts. ECM compares the requested and actual positions. If there is deviation, the PWM voltage to the valves is corrected.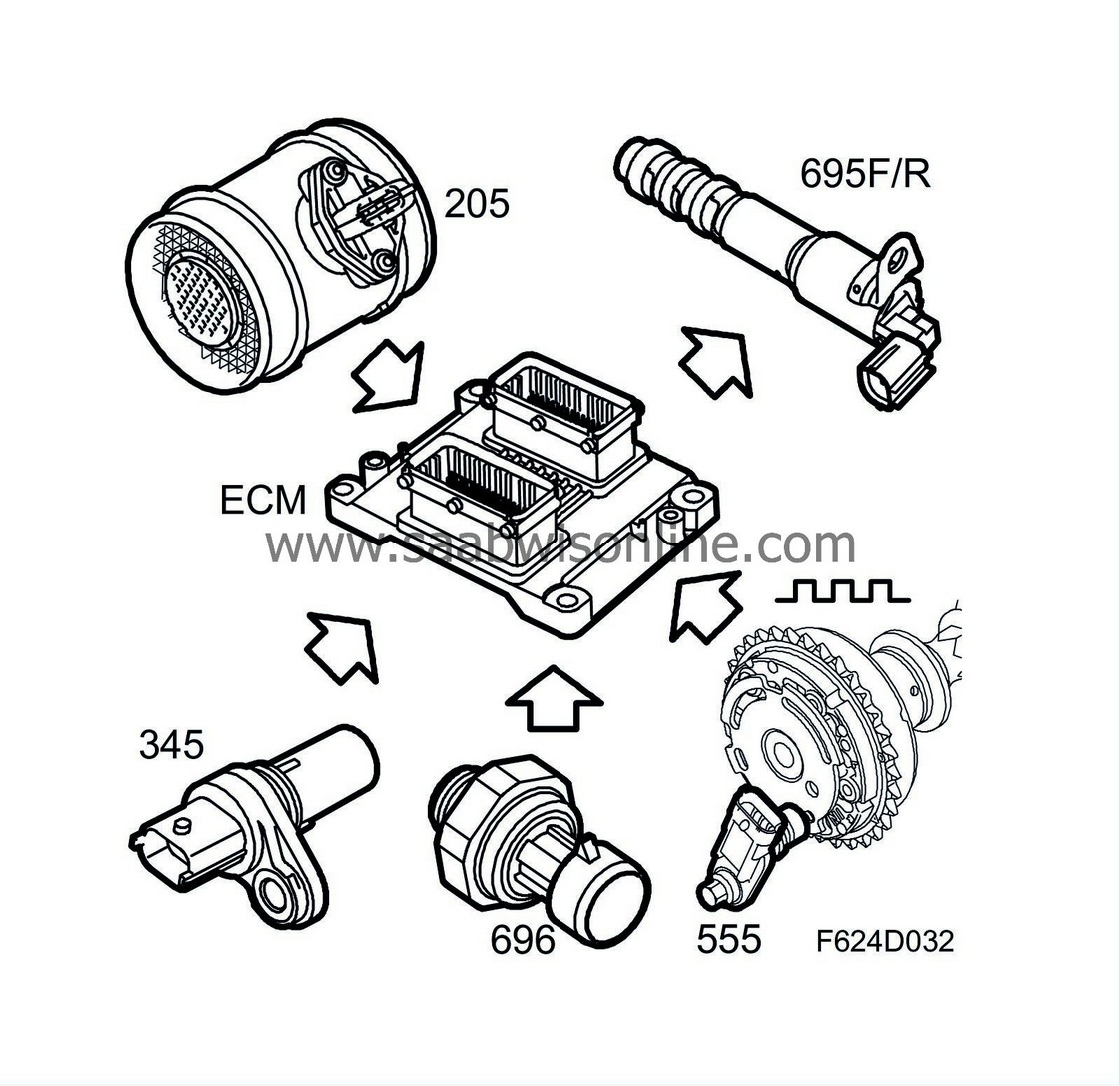