System function
System function |
Bus communication |
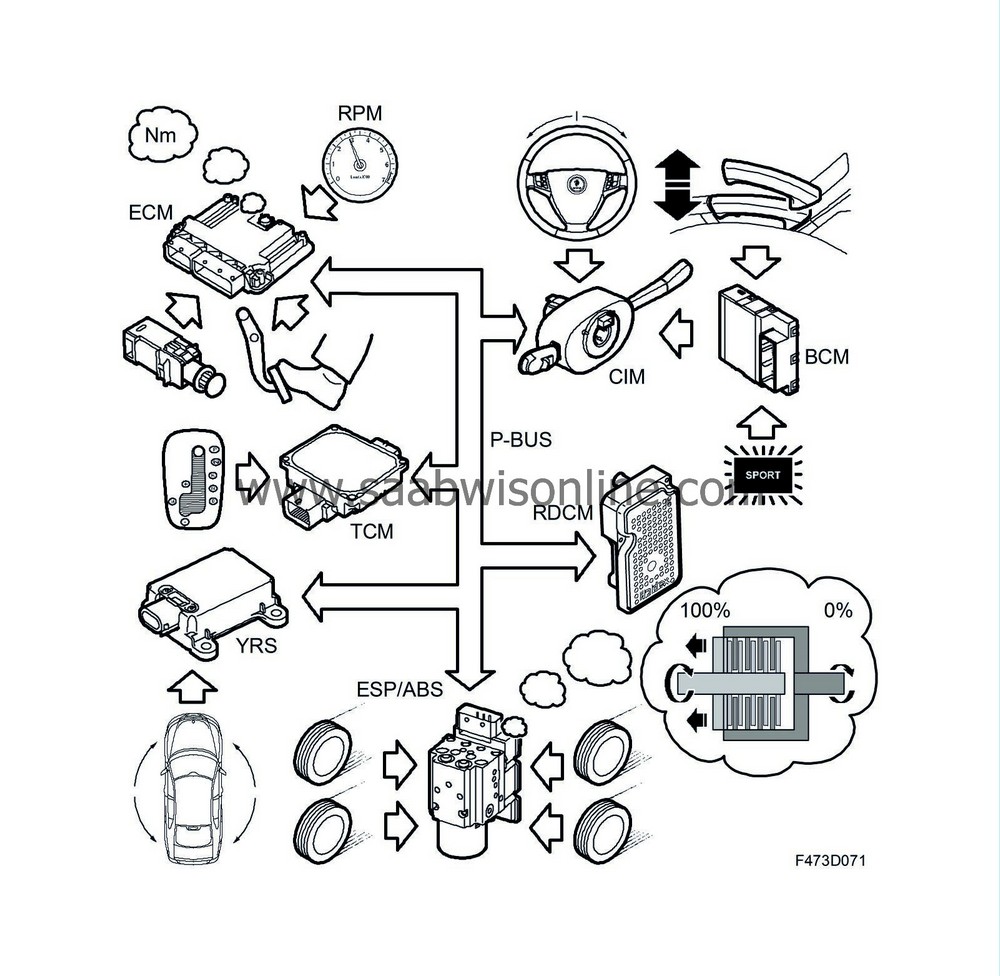
The XWD control module, abbreviated to RDCM, is connected to the vehicle's P-bus. Its bus messages are used to determine the operating/driving conditions for the vehicle, and accordingly how much drive torque should be transferred to the rear wheels. The control module and control valve are calibrated together, and they must be replaced together without exception.
The software in the control module can be updated with SPS.
The XWD control module uses information, amongst other things, from the following systems:
• |
ECM
: Requested (accelerator pedal position), current and maximum drive torque, engine speed, activated brake pedal
|
• |
YRS
: Yaw rate, lateral and longitudinal acceleration
|
• |
ESP
: Wheel speed of the four wheels
|
• |
CIM
: Steering wheel angle
|
• |
TCM
: Current gear
|
• |
BCM
: Handbrake activated, SPORT mode activated.
|
Pump motor control |
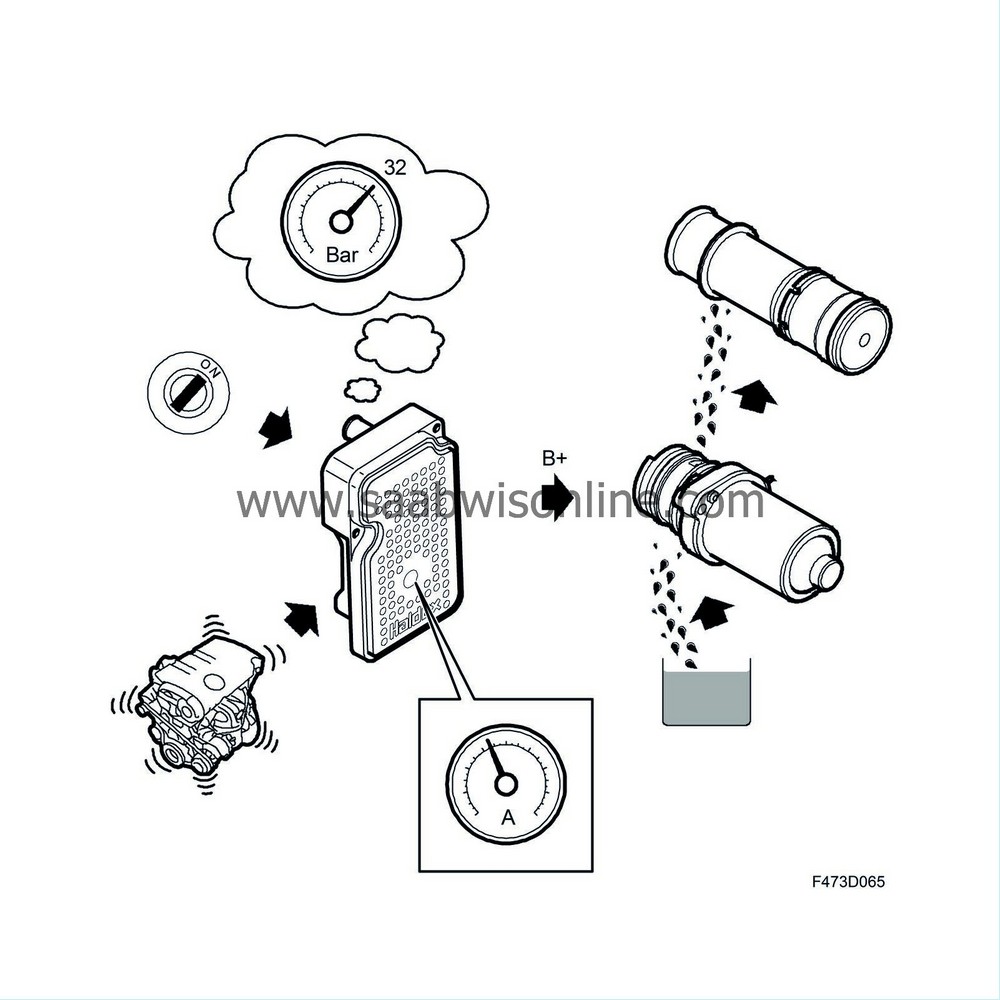
The control module activates the output to the hydraulic pump as soon as the following conditions are fulfilled: "ignition ON" and "engine started". The output is active until the calculated pressure is approx. 32 bar. The pressure is calculated by means of the control module measuring electric motor power consumption. The higher the pressure, the greater the resistance there is for the electric motor to drive the pump itself, and the higher the current becomes. When the pressure in the system amounts to approx. 32 bar (fully charged accumulator) the accumulator piston exposes the unloading holes and the pressure does not increase further.
The current to the motor does not increase any further but remains constant, the control module now knows that full system pressure has been reached and shuts down the pump. Restart takes place when the calculated pressure is below approx. 27 bar.
Controlling the differential clutch |
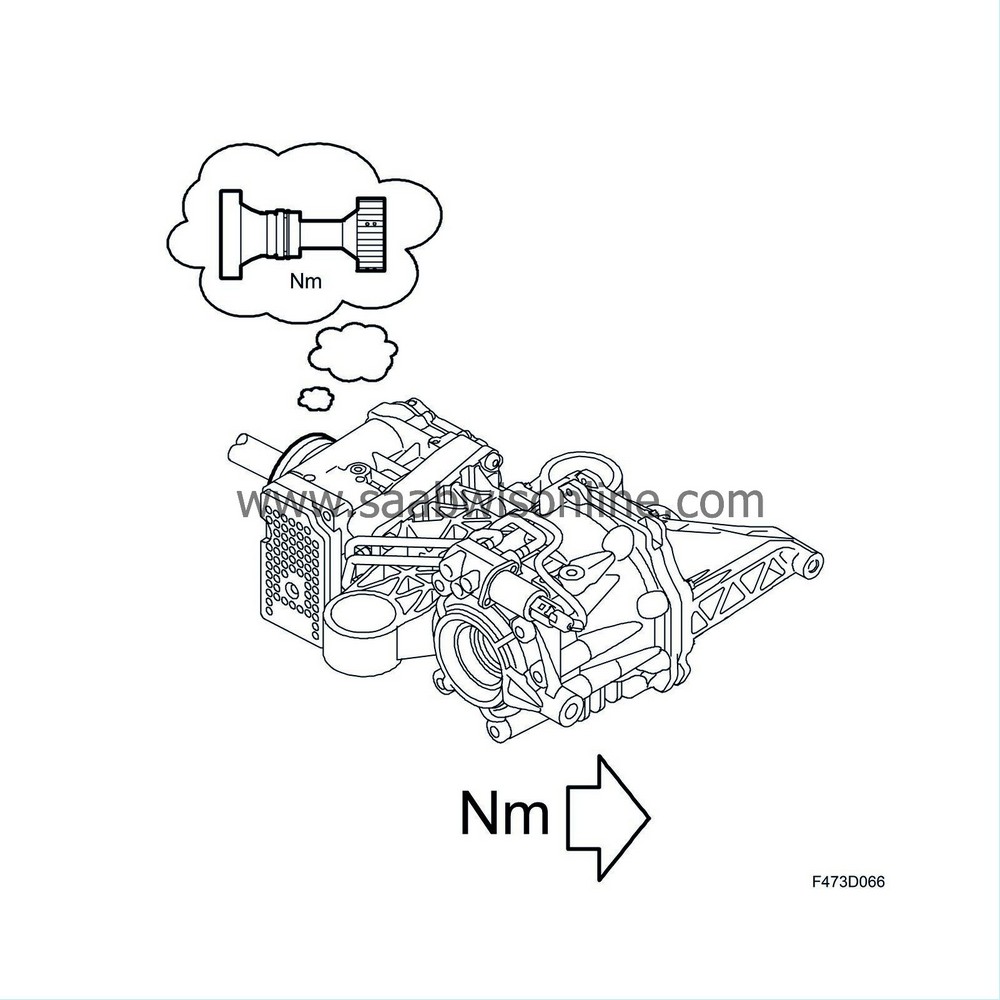
The control module controls torque transfer to the rear wheels by using the pressure control valve to control the hydraulic pressure to the differential clutch.
The amount of torque to be transferred to the rear wheels depends on a number of different factors. The control module takes care of all the calculations required for all-wheel drive and retrieves the information it needs on the bus. Other systems such as ESP may, under certain conditions, request that the differential clutch is opened.
When driving off, the differential clutch is applied to provide optimum acceleration for the prevailing road conditions. As vehicle speed increases the torque distribution to the rear wheels decreases to around 5-10% for motorway driving at constant speed.
During acceleration from a constant speed the differential clutch will be applied further, i.e. immediately transfer a greater proportion of torque to the rear wheels. This takes place very quickly as clutch reaction time is around 80 ms, which is a considerably shorter time than it takes for the engine to build up the torque. Consequently the clutch is ready to handle the increased torque from the engine before the engine delivers the increased torque.
Temperature calculation |
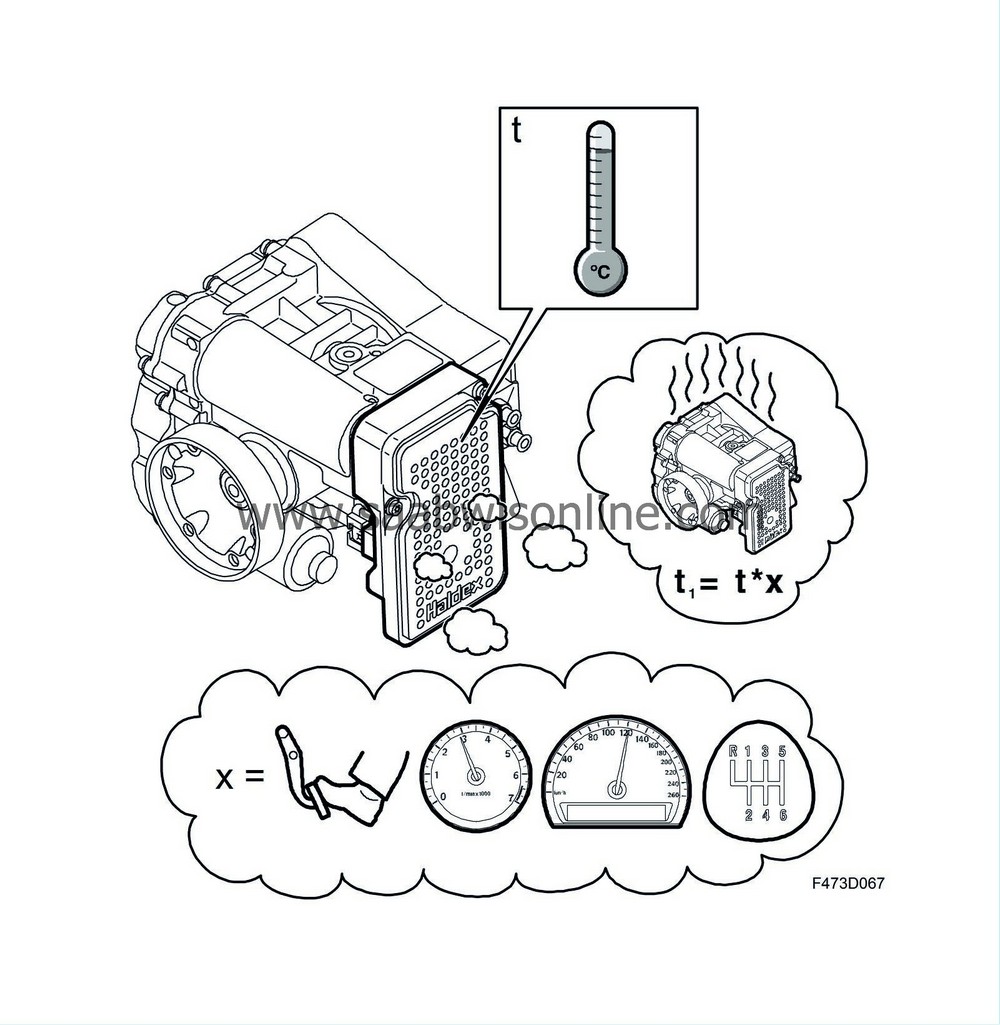
There is a temperature sensor on the control module's circuit board and the value from this, together with information on prevailing driving conditions, is used in a formula to calculate the temperature of the fluid in the differential clutch. The temperature inside the clutch pack itself is also calculated.
If the temperature of the differential clutch fluid reaches critical values then all-wheel drive is switched off, this protects against further temperature increase.
Fluid viscosity (thickness) varies with temperature, because of this the current to the pressure control valve must be compensated. In principle it takes a longer time to apply the clutch at low temperature compared to when the fluid is at normal operating temperature.
Wheel size adaptation |
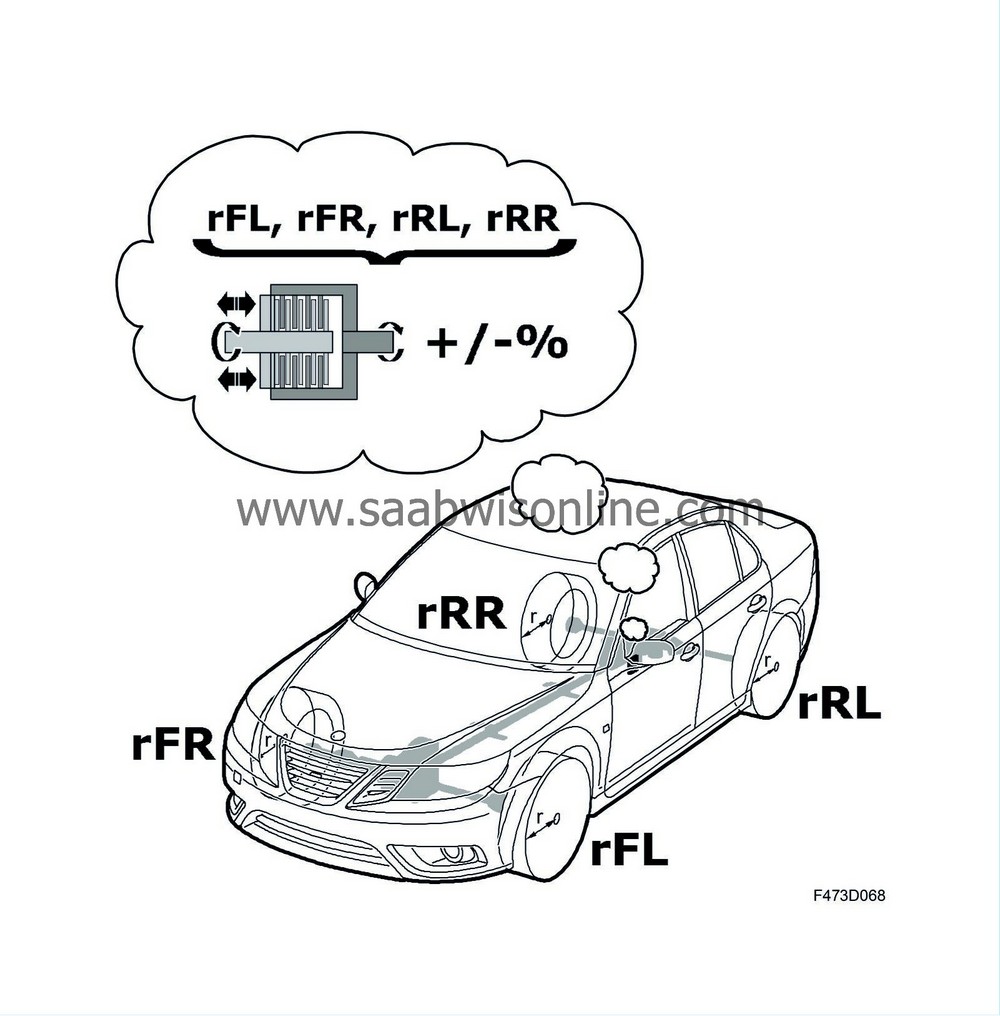
In order that correct torque should be transferred to the rear wheels the application of the differential clutch must be compensated for in terms of the existing difference in rolling radius between front and rear wheels.
If the rolling radius of the rear wheels is greater than that of the front wheels then a certain given application provides more torque to the rear wheels than if the rolling radius of the front and rear wheels was the same. Consequently the current to the pressure control valve must be reduced slightly (lower current results in lower hydraulic pressure = less torque to the rear wheels).
By measuring wheel speed the control module can detect whether any wheel has a deviating rolling radius. Adaptation of wheel size takes several minutes, the value is stored in the control module. If wheels have been changed to another rolling radius, e.g. swapped front/rear wheels then the drive torque to the rear wheels will be incorrect before adaptation has taken place. This may be perceived a small jerk/tug when driving off.
If one wheel deviates more than a certain given value then the control module assumes that a compact model spare wheel has been fitted and switches off rear-wheel drive.
Failsafe mode |
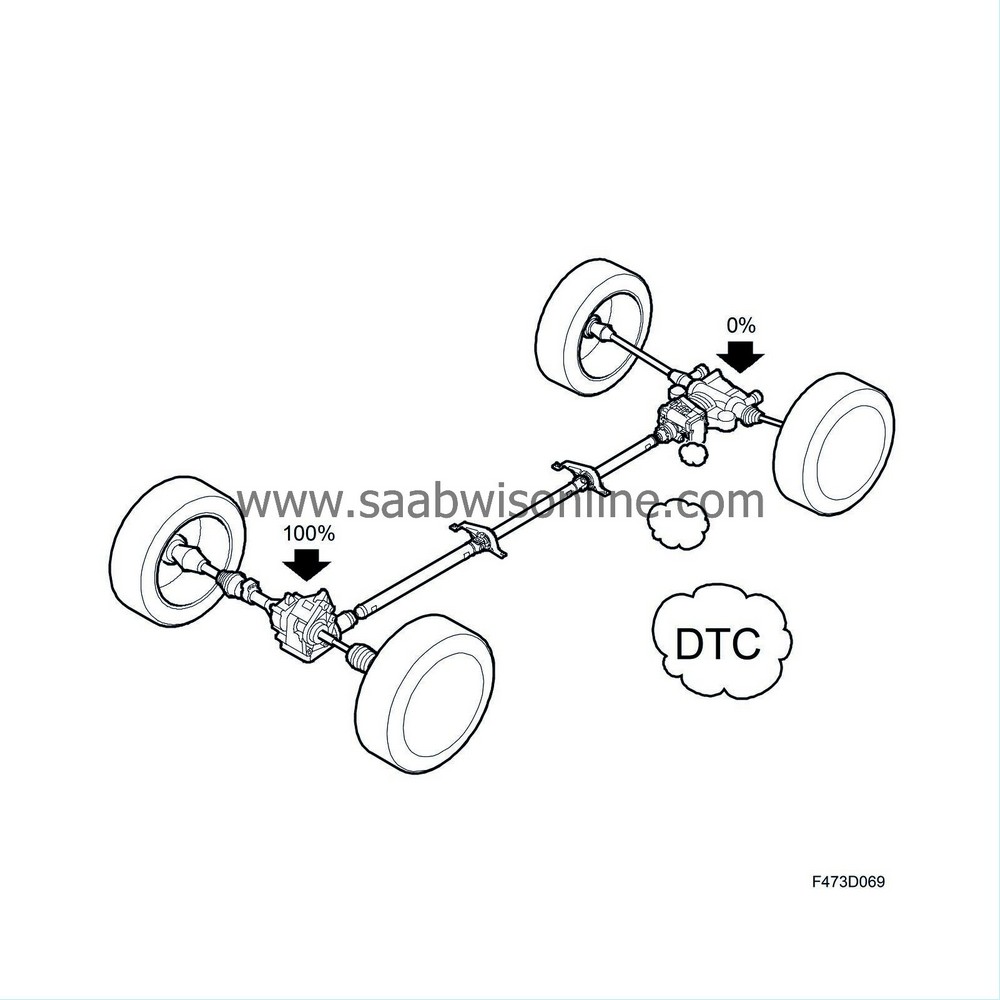
Most diagnostic trouble codes are generated as a result of the control module switching off all-wheel drive or the limited slip differential clutch (if fitted) in order to protect the system from damage or aggravated damage. A message is shown in the SID display.