Fuel pump
Fuel pump |
|
To remove |
Important | ||
The car should be standing level. If the tank is full and the back of the car is raised while the pump is being removed, there is a high risk that fuel will leak out. |
||
Lay down protective paper and possibly a receptacle to protect the carpets when the pump is being removed as there is risk for fuel spill. |
||
1. |
Lift up the rear seat cushion and the carpet.
![]() |
2. |
Undo the cover over the fuel pump.
|
3. |
Unplug the top connector as illustrated.
|
5. |
Remove the screw ring. Use the special tool (part no. 83 94 462).
![]() |
6. |
Lift up the pump until the top of it is approximately 50 mm above the fuel tank. Then rotate the pump approx. 80° and carefully remove it. Have some paper or a rag ready to catch fuel spill.
![]() |
7. |
Lift the pump over to a suitable vessel and pour out the fuel.
|
To fit |
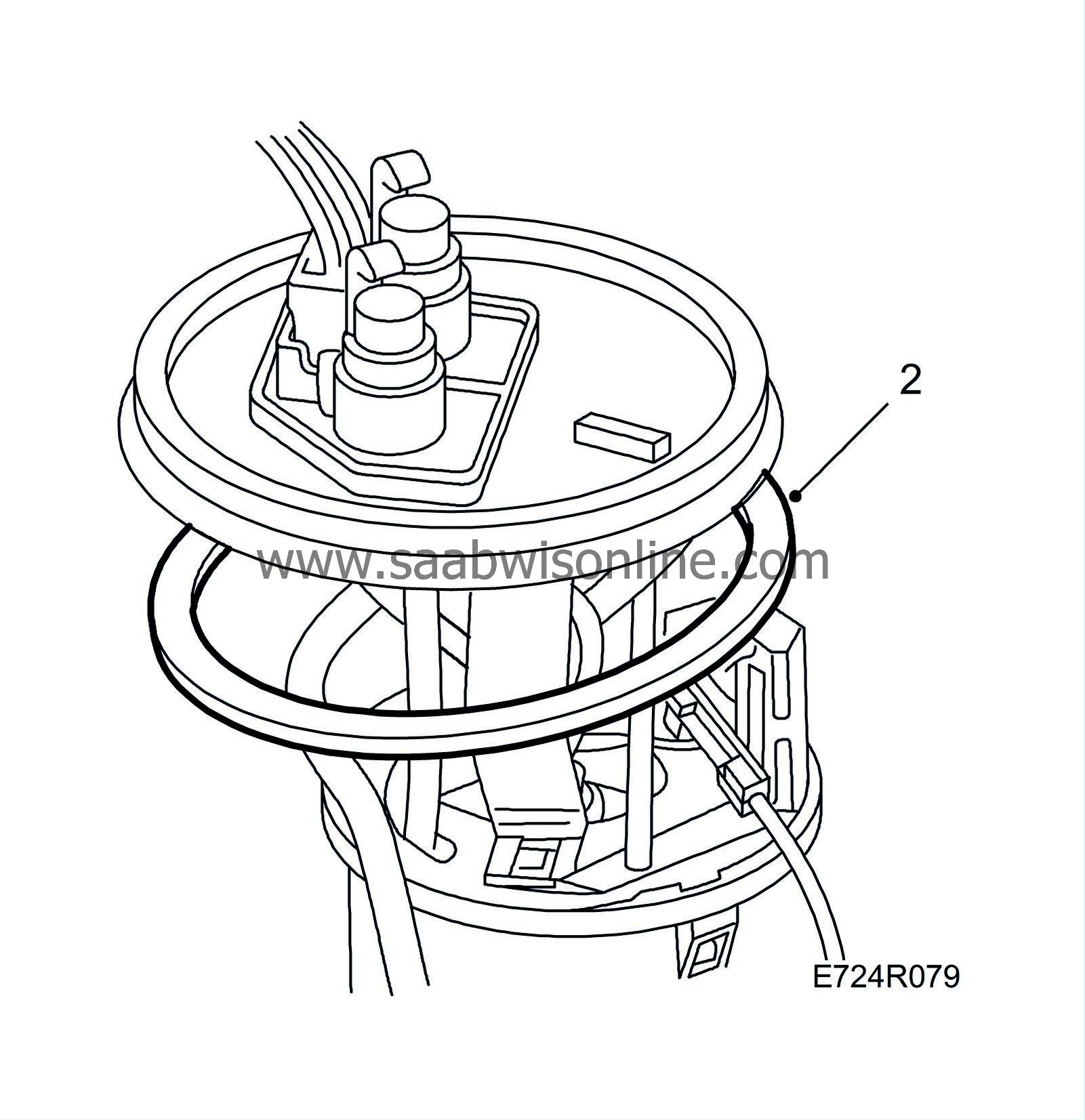
1. |
Clean the sealing surfaces.
|
2. |
Fit a new O-ring into the groove in the tank mounting.
|
3. |
Carefully lower the pump into the correct position. Make sure the index marks on the tank and the fuel pump are aligned. Press down the pump carefully.
![]() |
4. |
Lubricate the thread on the screw ring and the top of the pump with acidic-free vaseline to prevent the pump from rotating while the screw ring is being tightened.
|
5. |
Fit the screw ring and tighten it with the special tool (part no. 83 94 462).
Tightening torque 75 Nm (55 lbf ft). |
6. |
Check and lubricate the O-rings on the fuel line connectors with acidic-free vaseline and fit the connectors to the pump. Watch out for fuel spill.
![]() |
7. |
Make sure the yellow catches have snapped over the connections.
|
8. |
Plug in the connector and spray with contact spray, Kontakt 61 (part no. 30 04 520).
|
9. |
Check the operation and integrity of the pump.
|
10. |
Fit the cover and replace the carpets and seat cushions.
|
Checking the check valve |
2. |
Activate the fuel pump with the diagnostic tool.
![]() |
3. |
Run the pump manually until the pressure gauge reading stops rising.
|
4. |
Read the pressure gauge. Stop the pump. Residual pressure after 20 min. should be 2.3 bar (33 psi).
|
5. |
If the residual pressure is too low, inspect the check valve by detaching it from the pump outlet to see if it is leaking.
|
6. |
Remove the special tool (part no. 83 93 886).
|
Changing the check valve |
Important | ||
If the check valves on both the delivery and return lines are changed, it is important to make sure the correct valve is fitted to the correct line. |
||
1. |
Expose the check valve.
![]() |
2. |
Cut the fuel delivery line with a razor blade or sharp knife at the pump nipple as illustrated.
|
3. |
Fit tool 83 95 329 onto the fuel line. The end of the fuel line should project a short way.
![]() |
4. |
Fit the O-rings onto the new check valve, lubricate the check valve with acidic-free vaseline and position it in the fuel line. Make sure it is pointing in the right direction as it cannot be rotated once fitted and the hose is too rigid to twist.
|
5. |
Press in the check valve with the tool. Move the special tool gradually so that there is always just a short distance between the tool and the check valve connecting nipple.
|
6. |
Plug in the connector and spray with Kontakt 61 (part no. 30 04 520). Apply acidic-free vaseline to the O-rings on the check valve. Connect the fuel lines. Make sure the catches secure the delivery line properly.
|
7. |
Start the engine and make sure there are no fuel leaks.
|
Checking the position of the fuel gauge float arm |
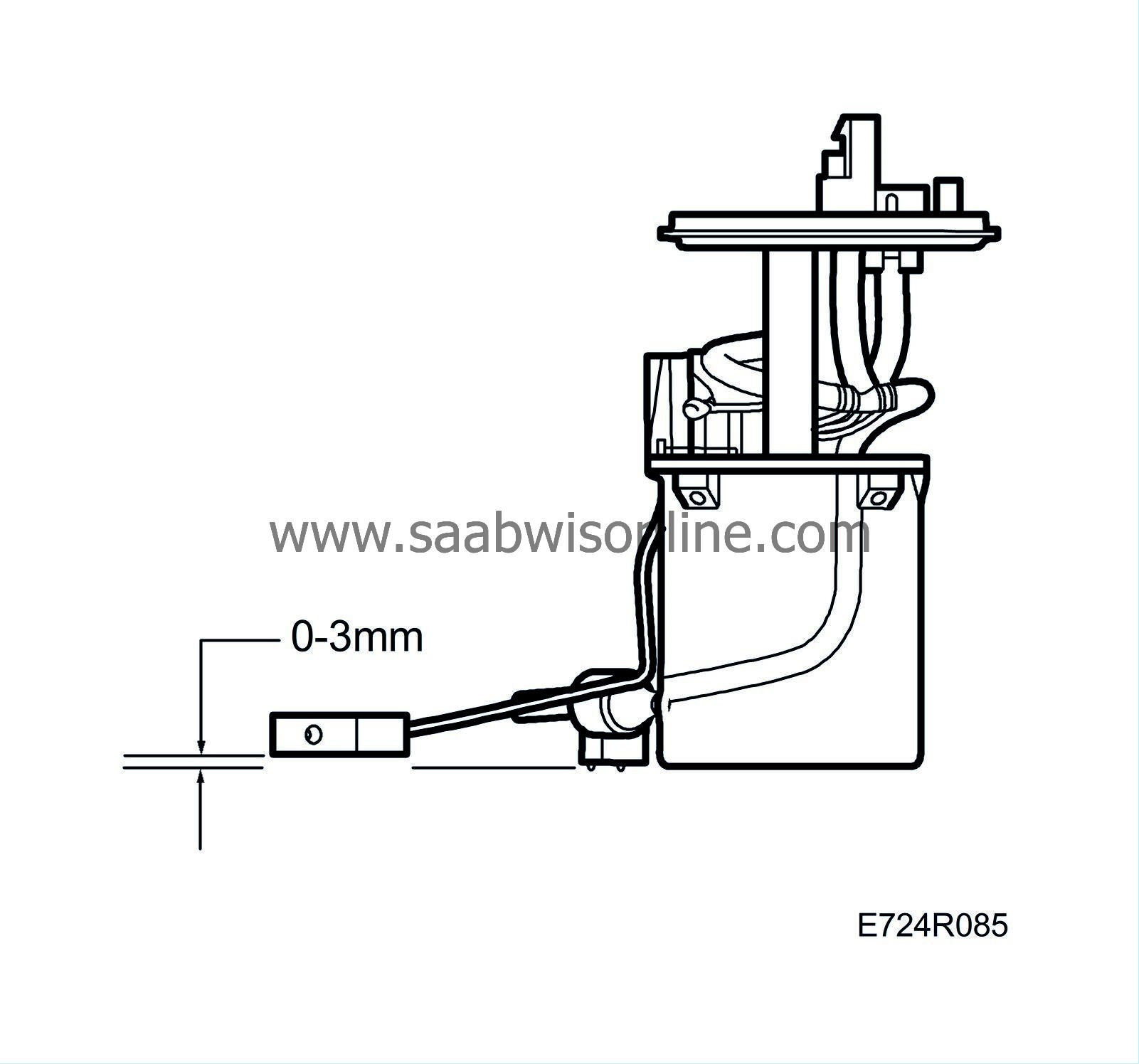
With the pump placed on an even surface, the distance between the surface and the bottom of the float should be 0-3 mm.
The resistance in the sensor should be:
• |
Empty tank, float in bottom position: 50±1.5 Ohm.
|
• |
Full tank, float in top position: 425±6.5 Ohm.
|