Power steering pump
Power steering pump |
In addition to pump elements, the pump incorporates a control valve for regulation of the pressure and flow.
|
Pump operation |
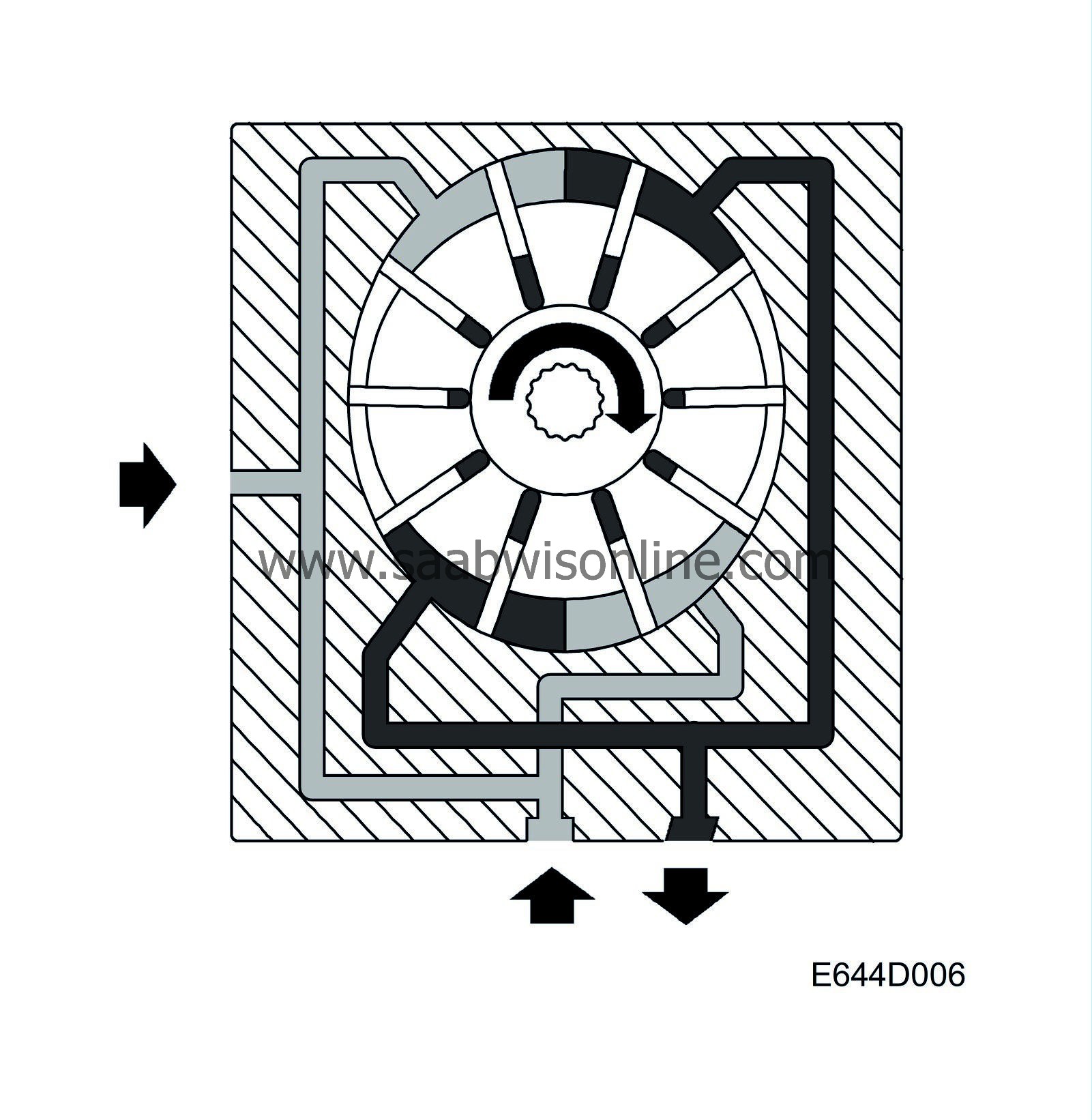
The pump element consists of a rotor containing a number of slots, a vane for each slot, a pump casing and two end plates with inlet and outlet ports for the power steering fluid.
Due to the oval shape of the pump casing, the volume between the vanes increases and decreases twice during each revolution of the rotor. Inlet ports lead to the areas in which the volume increases and outlet ports lead from those in which the volume decreases, thereby producing a pumping effect. Apart from being forced outwards by centrifugal force, the vanes are also pressed outwards against the pump casing by the pressure of the fluid. The fluid is directed into the slots inside the vanes.
Pressure and flow control |
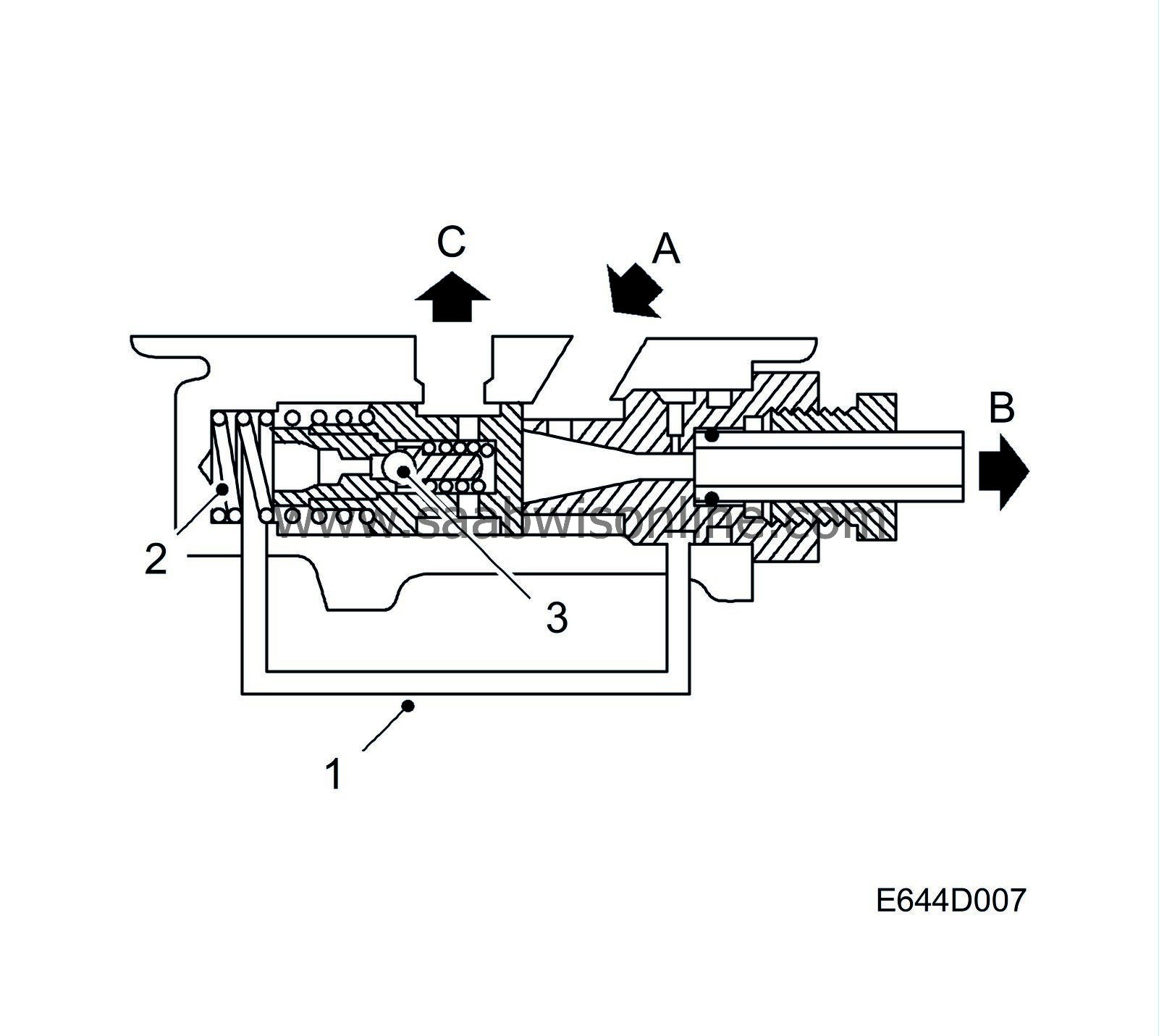
The purpose of the control valve is to regulate the flow from the pump so that it remains constant, regardless of engine pump rpm.
One side of the control valve is in direct communication with the delivery side of the pump (A). The outlet (B) from the pump incorporates a restriction from which a connecting passage (1) leads to the other side of the valve, which is fitted with a spring (2). When not actuated, the valve is pressed against the outlet side.
Inside the control valve is an overflow valve (3) which, when the pressure exceeds a certain limit, is actuated by the pressure of the power steering fluid on the spring-loaded side of the control valve.
For the control valve to operate, a certain amount of power steering fluid must circulate through it continuously at (A) and (C), although not when the steering wheel is at full lock.
The pump delivers a maximum pressure of about 120 bar and a maximum flow of about 7.2 litres per minute.
Steering and parking at low engine rpm |
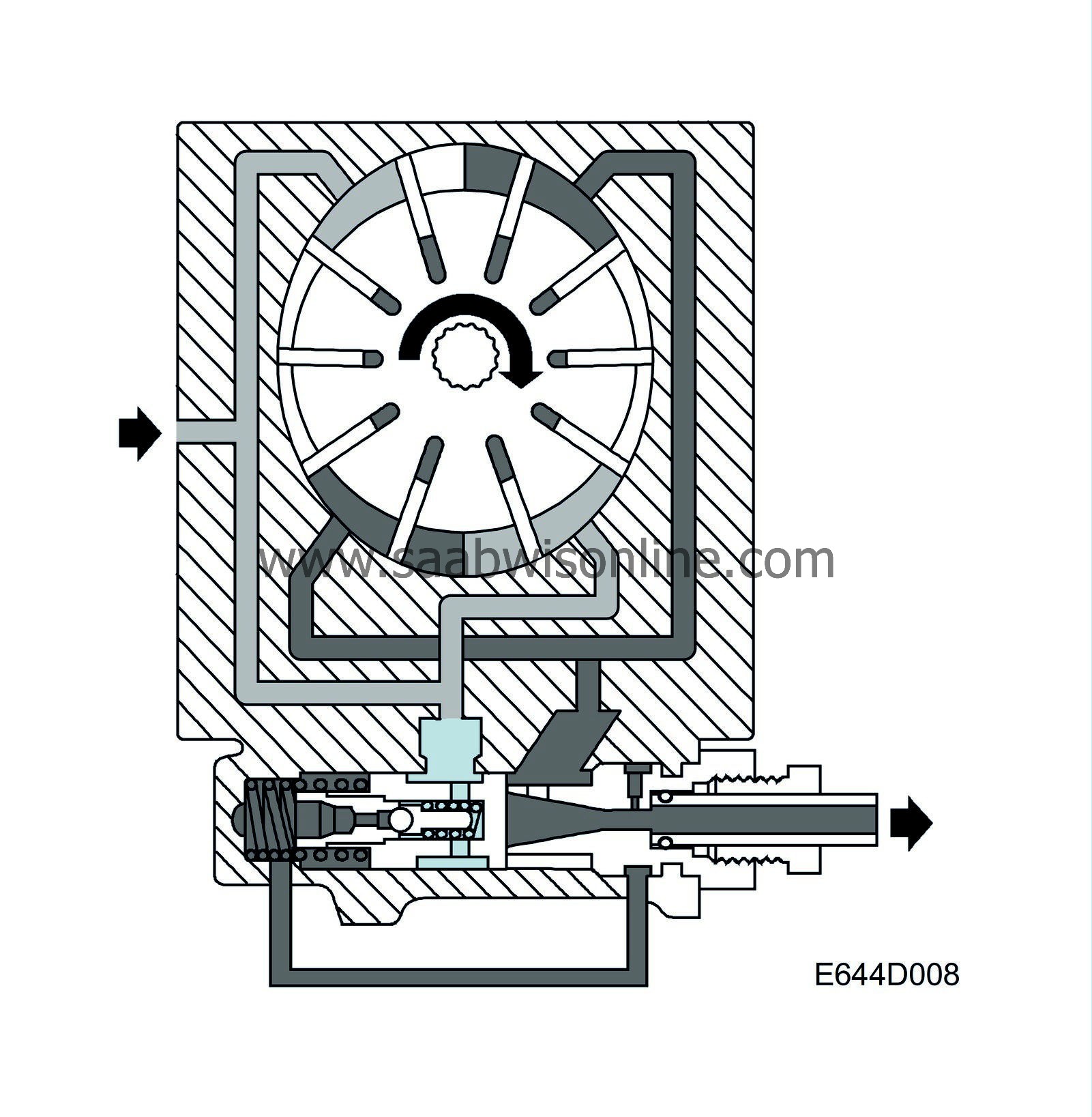
The pressure raised by the pump (shaded portion) is reduced slightly by the restriction in the pump outlet.
This reduced pressure is also communicated to the spring-loaded side of the control valve, creating a small pressure difference across the valve. Owing to the low speed of the pump, however, the difference in pressure is insufficient to overcome the force of the spring and actuate the valve.
Steering at high engine rpm (pump in flow control mode) |
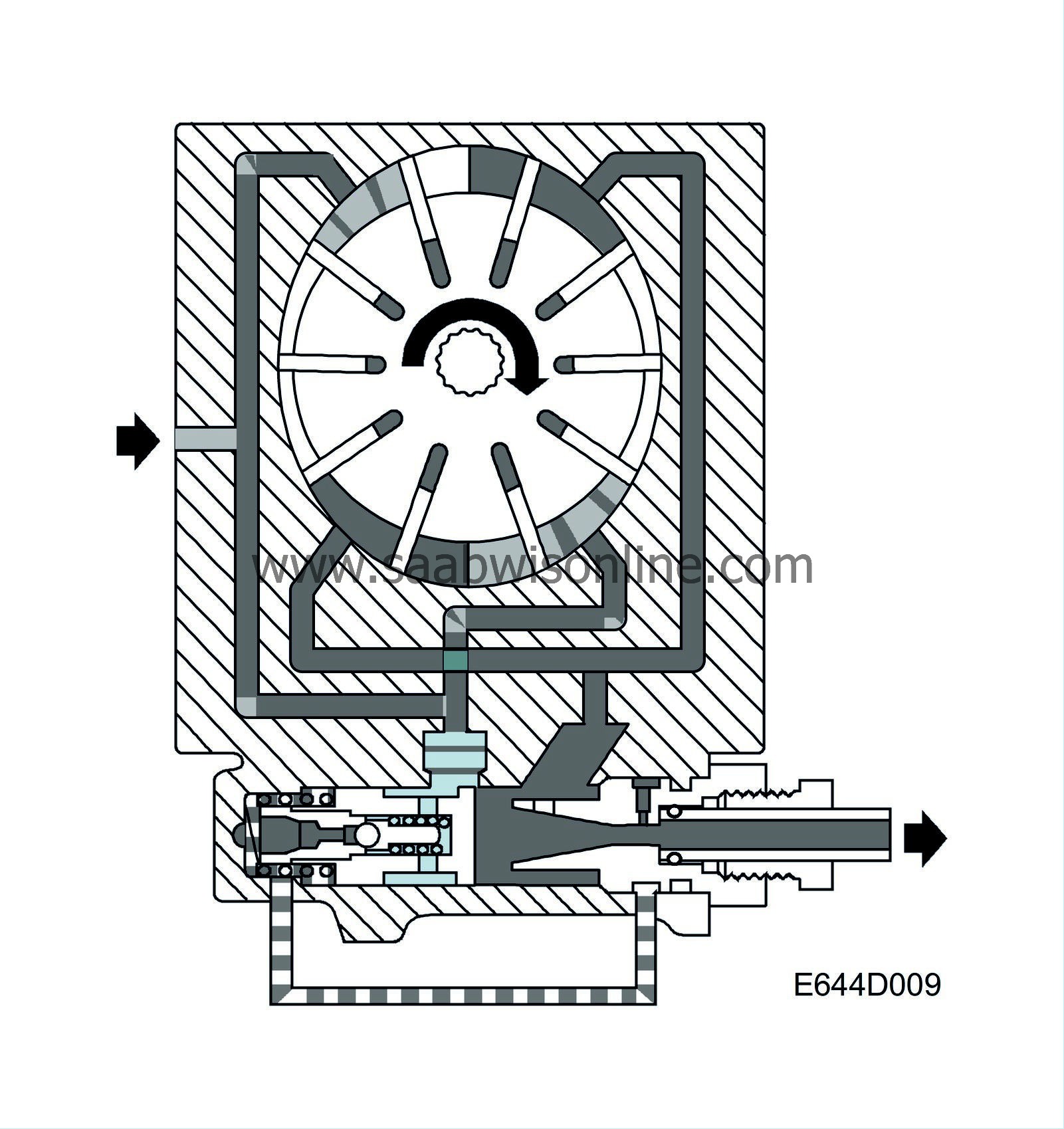
The flow of power steering fluid inside the pump increases with increasing engine rpm and owing to the restriction in the pump outlet the flow velocity also increases. This reduces the pressure in the connecting passage, with the result that the pressure on the spring-loaded side of the control valve will be lower than that acting on the outlet side of the valve. The valve therefor overcomes the force of the spring, opening a port to the suction side of the pump and allowing a certain amount of internal recirculation of the fluid to take place so that the flow from the pump is maintained at a constant rate, regardless of engine pump rpm.
Steering wheel turned to full lock |
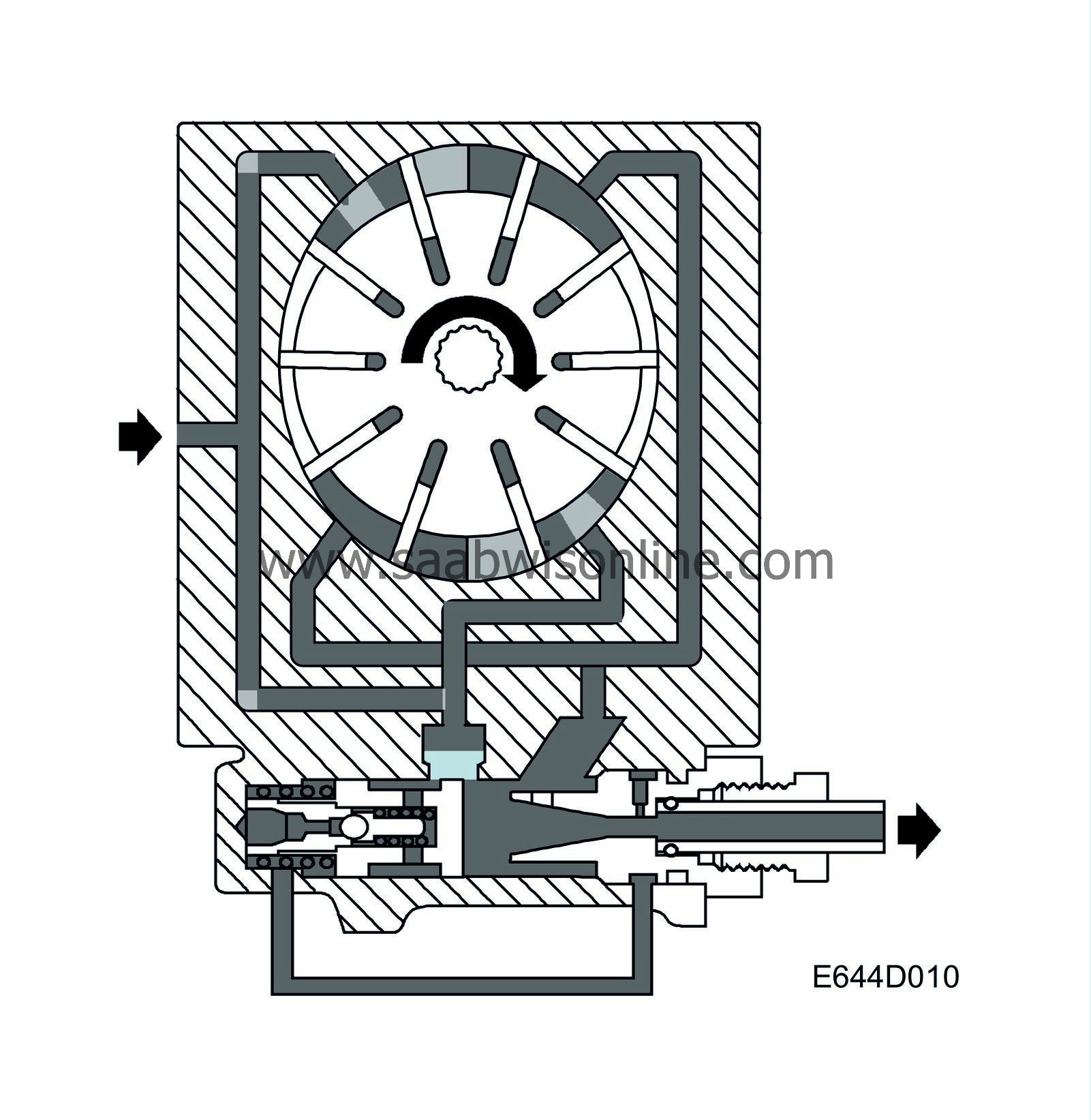
Pump speed in this case is often low. When the steering wheel is turned to full lock the control valve of the steering gear closes. The flow of fluid from the pump will then be zero.
The resulting high pressure is directed via the connecting passage to the spring-loaded side of the control valve. The pressure opens the overflow valve and allows the fluid to pass to the inlet side of the pump. The pressure difference across the control valve forces it to move against the spring and so open the port for recirculation of the full delivery flow from the pump.
The predetermined maximum pressure is maintained as long as the control valve remains closed.