SRS control module
SRS control module |
The control module incorporates an electromechanical safety sensor of magnetic reed type, a microprocessor, three backup power sources, one voltage converter and an accelerometer.
The purpose of the safety sensor is to arm the front airbags if sudden retardation is detected. This happens when a spring-loaded magnet reaches the reed element and closes the detonation circuit.
Since this sensor is connected in series with the detonation circuits for the front airbags, the fact that the microprocessor is all set to activate the front airbags will not alone suffice. For activation of the front airbags, two basic conditions must be satisfied:
1. |
The safety sensor must be closed.
|
2. |
The microprocessor must have found that the necessary conditions obtain for activation of the front airbags.
|
An acceleration sensor which senses acceleration and retardation of the car in its direction of travel is provided to enable the control module to recognize a collision situation. When the car's retardation exceeds a certain limit, the processor starts to process the signal from the acceleration sensor with greater precision.
If retardation continues to increase and exceeds the values defined for a collision, the processor will send a pulse to one of the electric detonators and cause the seat-belt tensioners to be activated first. If the collision is sufficiently severe, the front airbags will also be activated.
The seat-belt tensioners can also be activated by a rear-end collision, acceleration.
The control module has the capacity to activate six different detonation circuits:
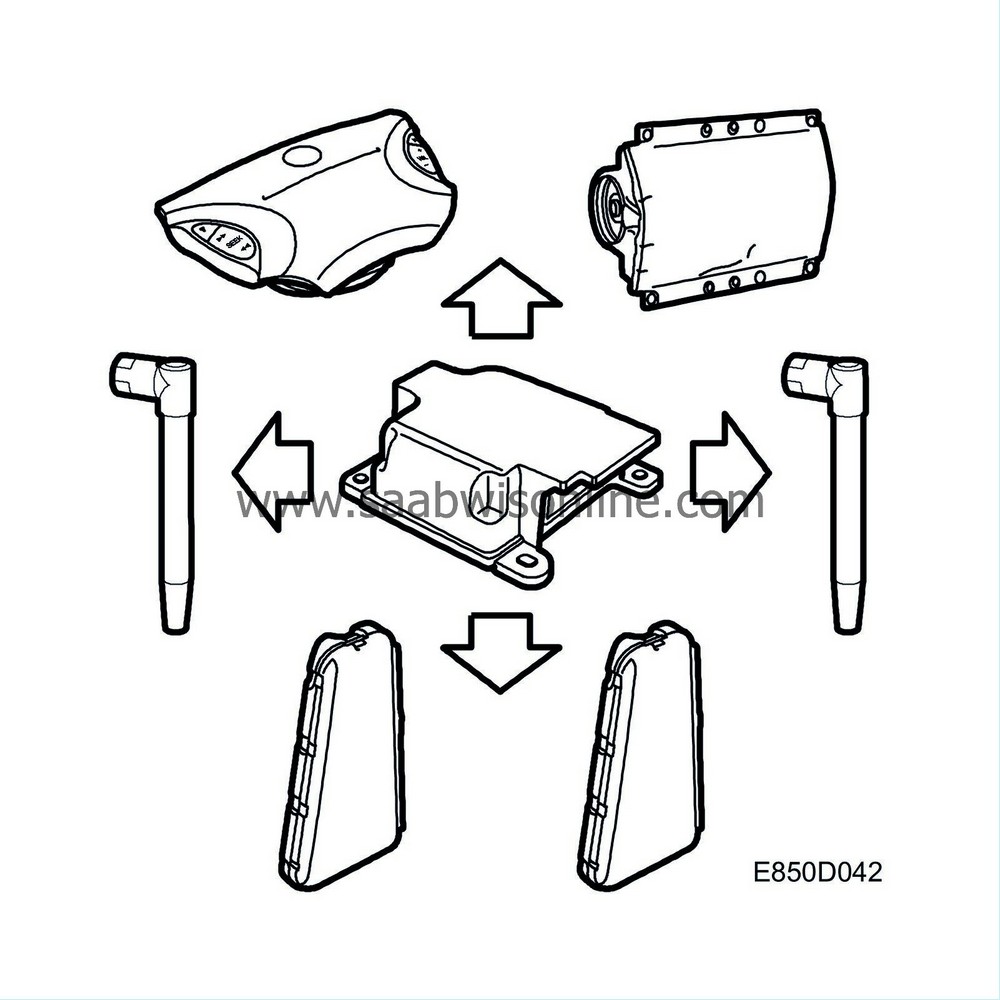
• |
driver airbag
|
• |
Passenger airbag
|
• |
Seat-belt tensioner, left
|
• |
Seat-belt tensioner, right
|
• |
side airbag, driver
|
• |
side airbag, passenger.
|
The activation times in a collision may be different for the different circuits.
In a side collision, the side impact sensor registers the pressure change in the front doors. If the pressure build-up per unit time coincides with the limits that have been defined as constituting a collision, crash information is supplied to the control module which then activates the side airbag on the side of the car affected by the collision.
Backup power |
The control module has three backup power sources. Two of them enable the front airbags to be activated for a minimum of 150 milliseconds after the regular power supply has failed and the third backup power source keeps the processor going for 150 milliseconds after the regular power supply has failed.
On-board diagnostics |
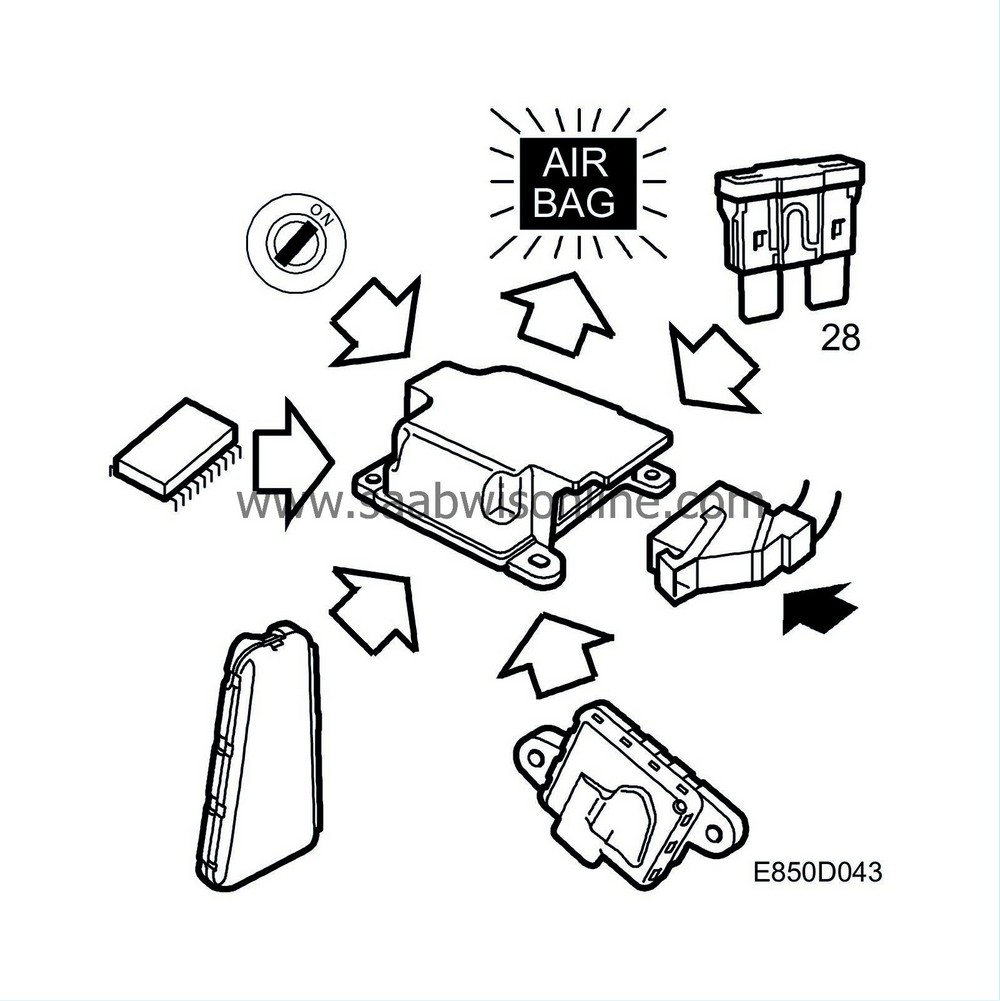
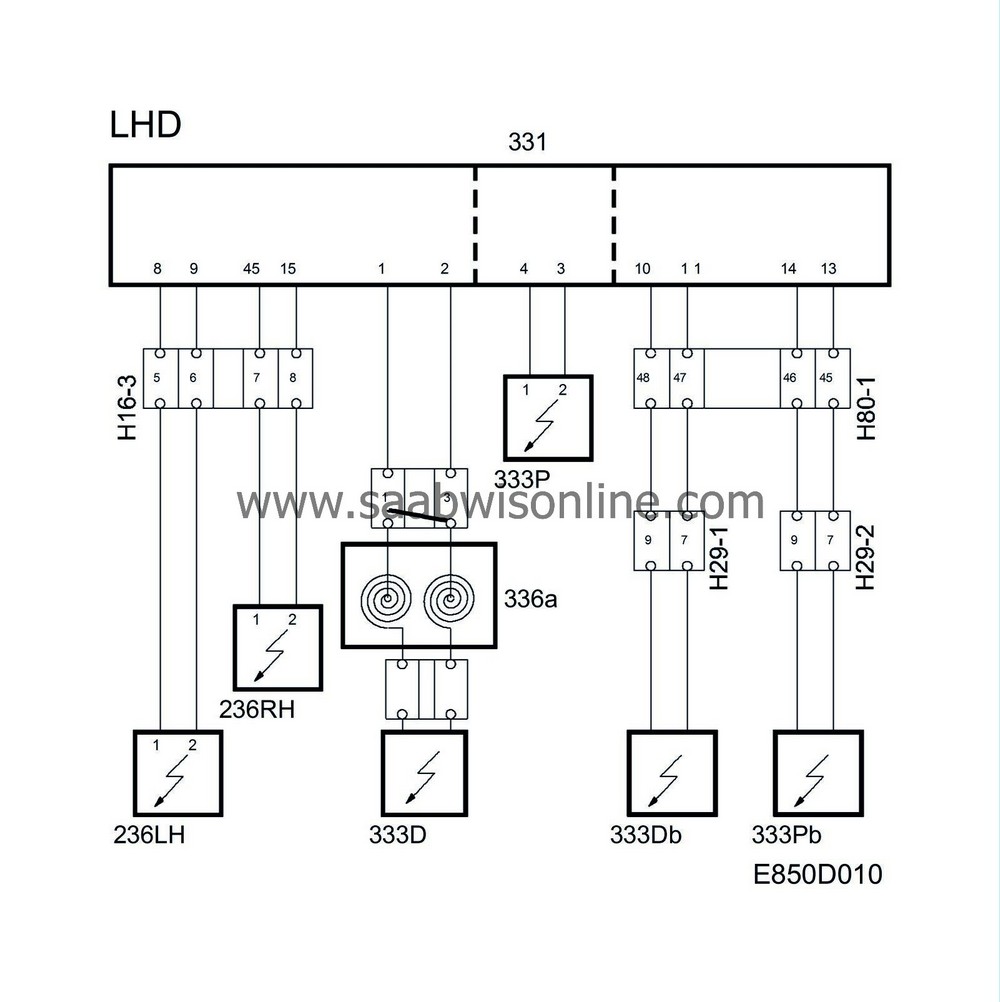
When the ignition switch is in the ON position and the system supplied with current, the control module carries out initial self-diagnosis for a maximum of 10 seconds. As a safety measure, the airbags cannot be activated during this period.
The electric detonators and the wiring, power supply, airbag warning lamp, microprocessor and side impact sensors are all checked during this self-diagnosis.
The airbag warning lamp lights up during the first test when the current is turned on for 3-4 seconds to check the lamp. Self-diagnosis then continues for as long as the ignition switch remains in the ON position.
There are 41 diagnostic trouble codes covering all sensors, wiring harnesses, airbags, seat-belt tensioners and internal control module faults.
The control module can measure shorting to ground and B+ as well as resistance for low and high in all ignition circuits. In case of a system malfunction, the Airbag warning lamp is illuminated.
The control module monitors the diagnostic trouble code conditions at different intervals, depending on the diagnostic trouble code concerned.
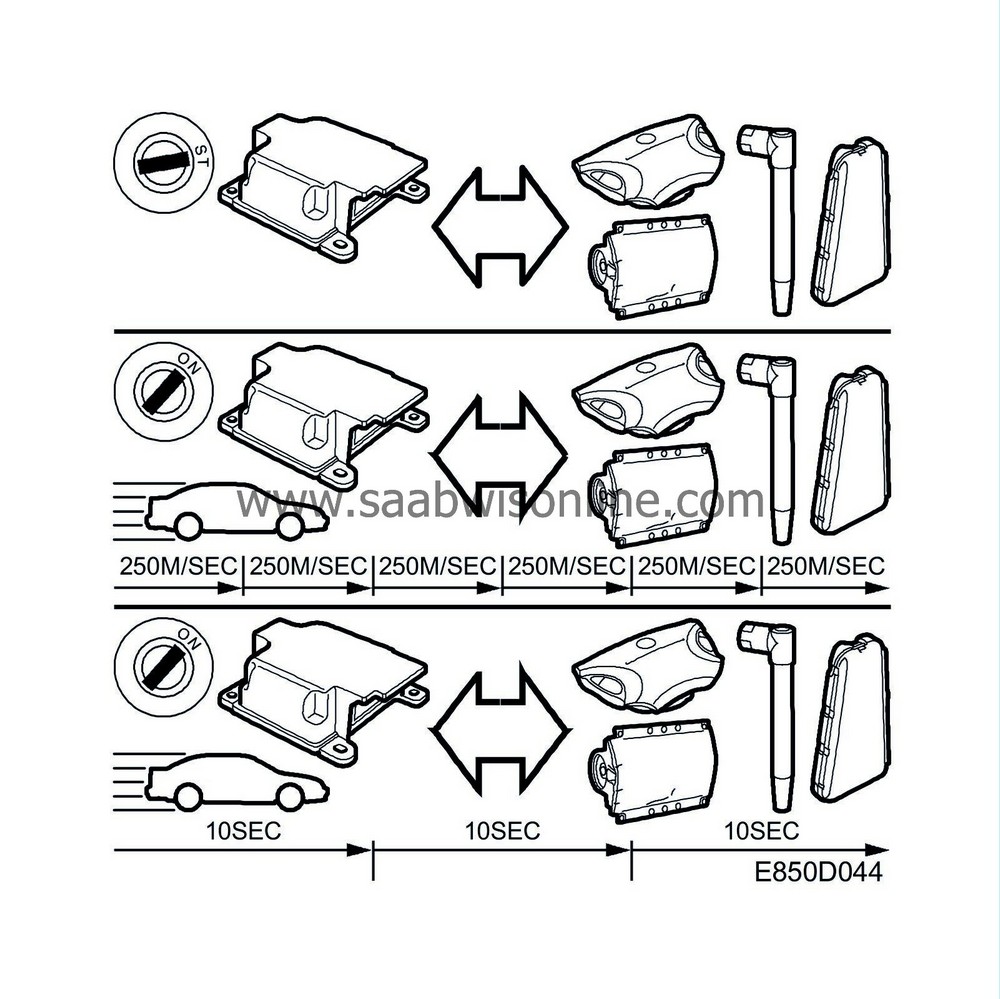
These are the different types of monitoring:
On starting
|
Within the first 10 seconds of turning the ignition switch to the ON position
|
Continuously
|
Every 250 milliseconds under normal operating conditions
|
Periodically
|
A 10-second cycle
|
Non-continuous monitoring
|
Event-controlled, e.g. reception of a fault message from a side impact sensor
|
After activation of the driver and passenger airbags, the control module will no longer be serviceable. The SRS control module therefore cannot be reused after activation of one of the front airbags.
The control module can be reused twice at most after activation of the seat-belt tensioners and/or side airbags, i.e. the side airbags and seat-belt tensioners can be activated a total of three times before the control module has to be changed.
Diagnostic trouble codes are generated for all activated airbags and seat-belt tensioners. The diagnostic trouble code for an activated front airbag cannot be cleared and in such case the control module will have to be changed.
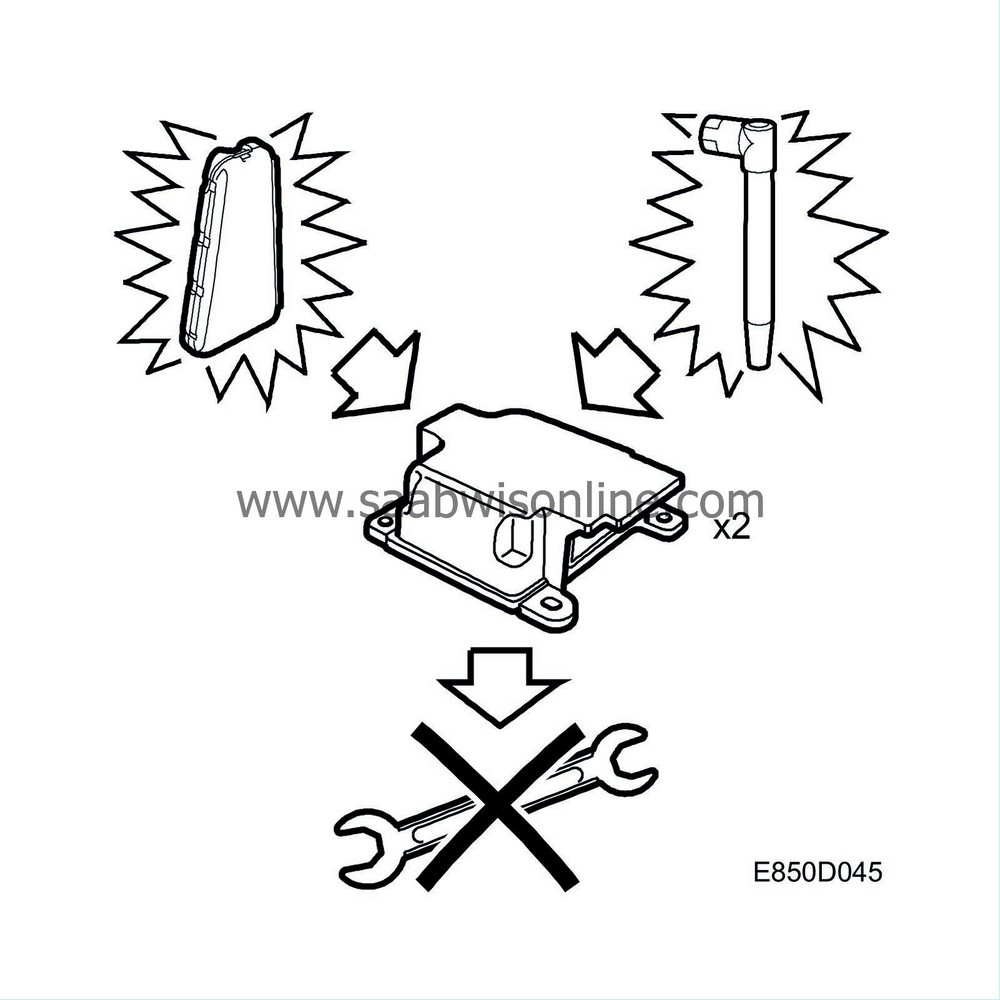
Storage of diagnostic trouble codes
Up to 8 diagnostic trouble codes can be stored in the SRS control module's memory, 5 of them prioritized places reserved for: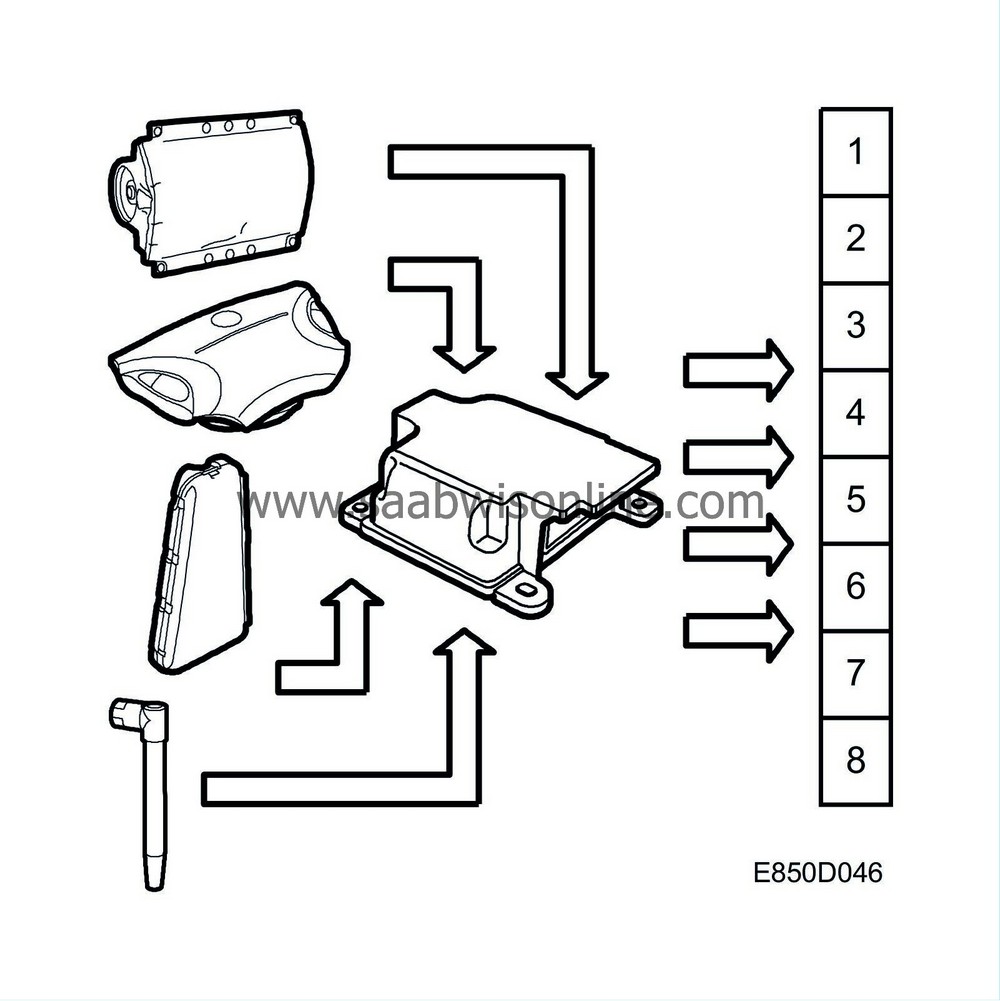
• |
driver airbag activated
|
• |
passenger airbag activated
|
• |
seat-belt tensioner activated
|
• |
driver's side airbag activated
|
• |
passenger's side airbag activated.
|
If no prioritized diagnostic trouble code has been generated, the eight places are available for ordinary diagnostic trouble codes. If one or more of the prioritized diagnostic trouble codes turns up after ”non-priority” codes have been generated, these codes will write over the last 5 ”non-priority” codes.
Programming the SRS control module |
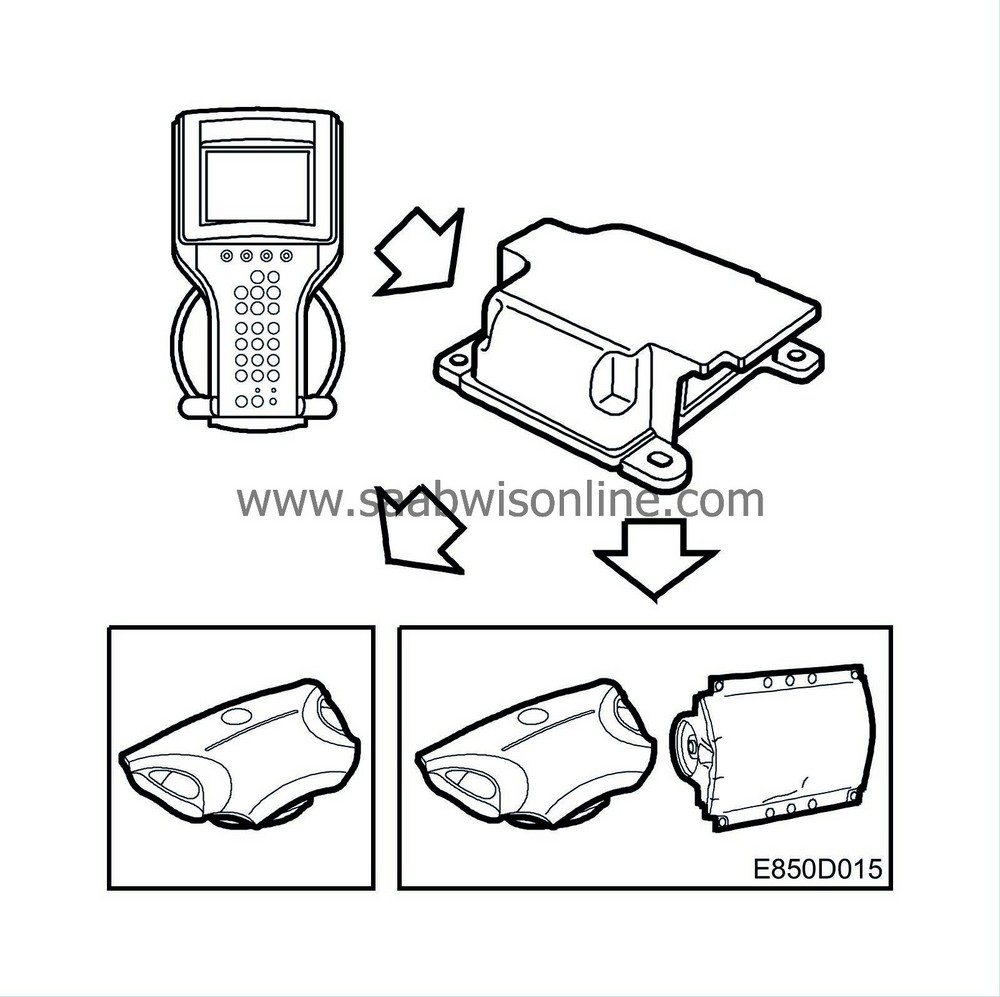
As supplied from the manufacturer, the SRS control module will not be functional until it has been programmed for the car in which it is installed. Programming entails comparing the control module functions with the hardware present in the car.
The control module checks whether the requested programming is compatible with the components that it detects electrically in the car, until the ignition is switched off. If the detected components are not compatible with the desired programming, a diagnostic trouble code will be generated. In this way it is possible to find out why the car's equipment and the desired control module programming are incompatible.
When the SRS control module has been chang ed, the spare parts control module must be programmed for the car it will be installed in. This is done using a diagnostics instrument.
After programming has been successfully completed, the parameters will be locked in the control module and cannot be changed.
Power supply |
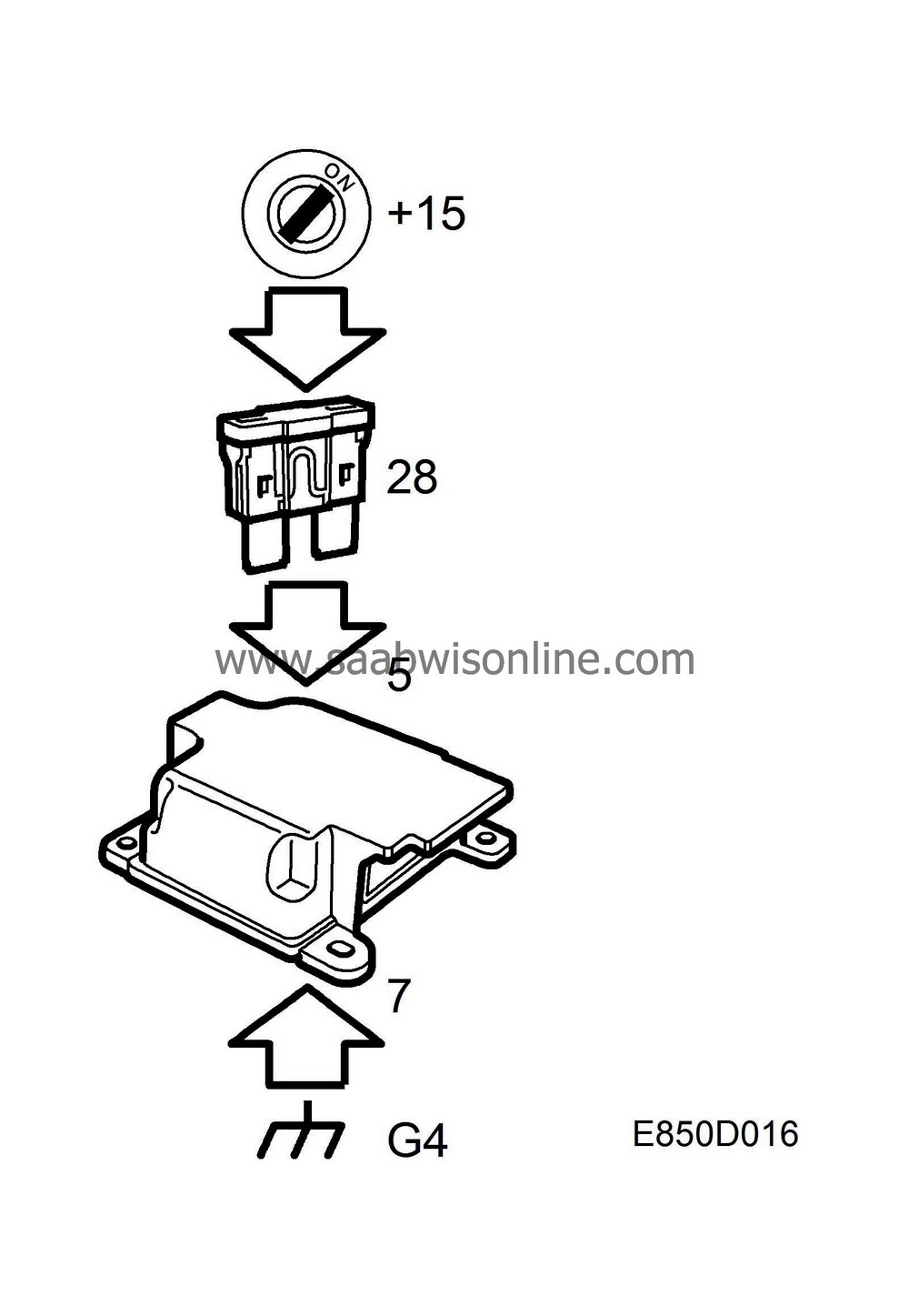
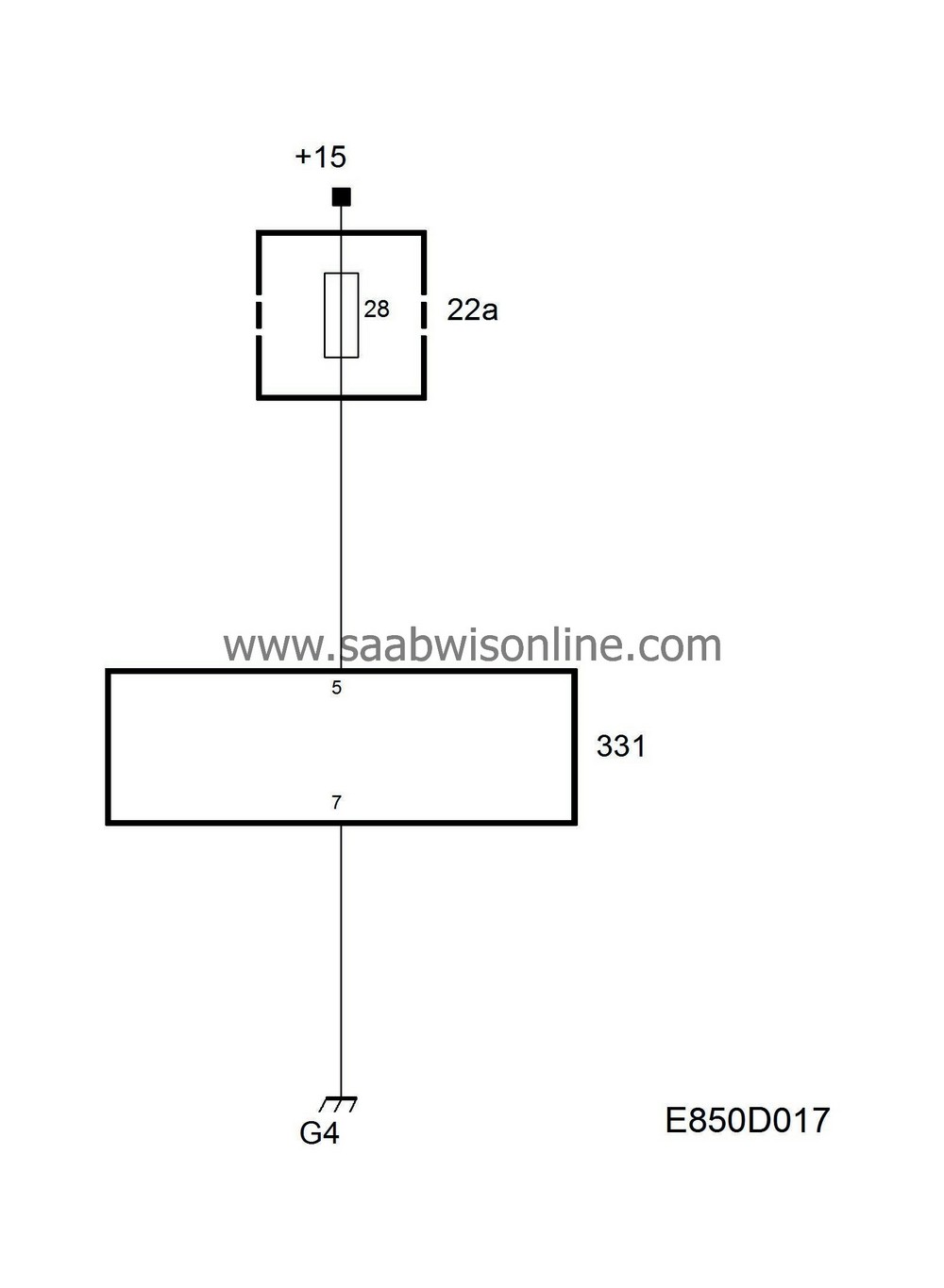
With the ignition switch in the ON position, current (+15 circuit) is supplied to pin 5 of the control module via fuse 28. The control module is designed to operate on a power supply of between 9 and 16 V.
Grounding |
The control module is connected to ground via pin 7 and the three retaining screws. No ground cables from other systems must be connected to the retaining screws as this could cause malfunctioning of the SRS.
A poor ground connection will not cause a diagnostic trouble code to be generated. When connection to ground is restored after having been interrupted, it corresponds to power turn-on and the control module again runs through the on-board diagnostics program. The airbag warning lamp will then lights up for 3-4 seconds.
Connector |
The control module's connector incorporates 5 short-circuiting jumpers which, when the connector is unplugged, short-circuit the leads in pairs to the two electric detonators for the front airbags, the two electric detonators for the side airbags and also short-circuit the airbag warning lamp's wiring to ground.