Fuel pump, V6
Fuel pump, V6 |
General description |
The vane type feed pump is located in the fuel pump.
The high pressure part of the fuel pump comprises an inner cam and pump plungers mounted parallel to the rotation of the pump shaft. It is a tandem pump and consequently compact with only small power requirements for its drive.
The volume available in the fuel rail is controlled by the fuel quantity valves. They protect the fuel pump against high load and maintain a suitable fuel temperature, i.e. only the amount of fuel and the pressure that is required is available in the fuel rail.
Feed pump |
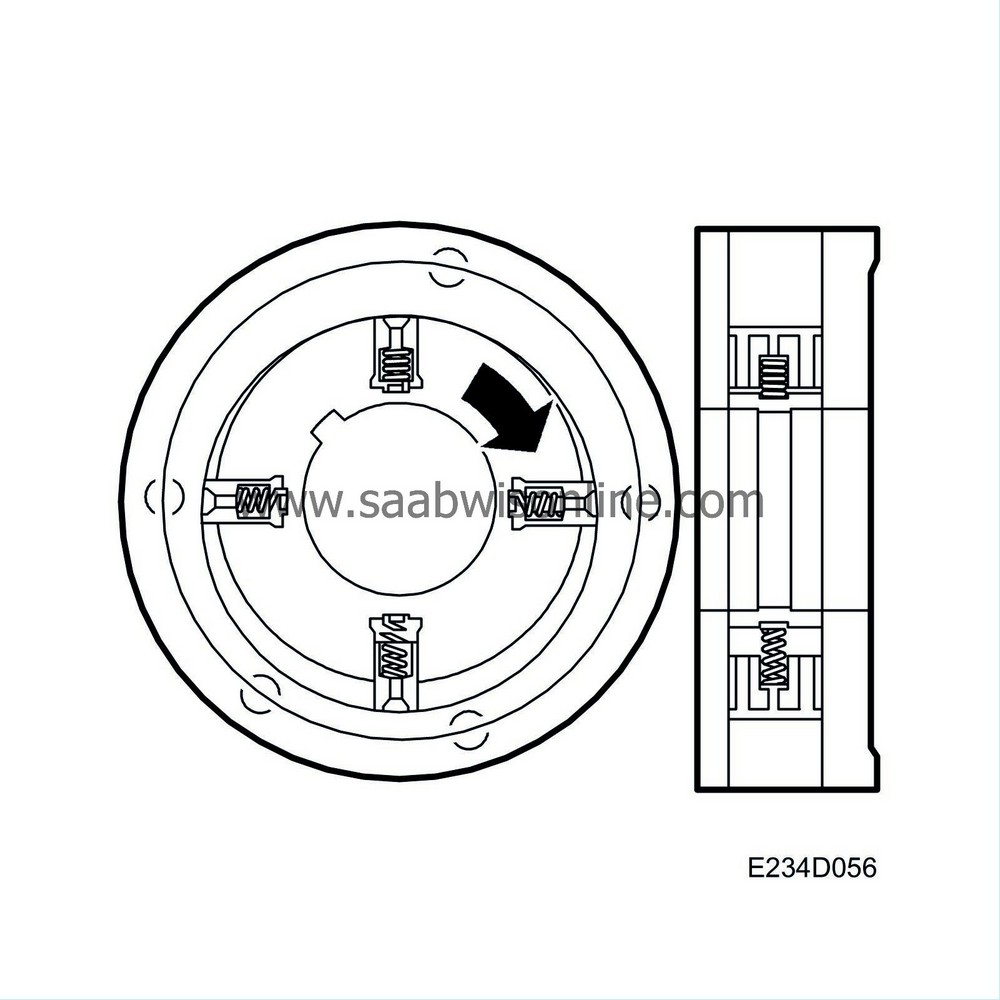
The rotor feed pump has four vanes that rotate with the pump shaft inside an eccentric ring. As the rotor goes round, fuel is drawn from the fuel tank. The fuel will then pass to the fuel quantity valves and on to the high pressure part of the pump. Under each vane in the rotor is a spring that presses the vane out towards the eccentric ring wheel. These springs reduce internal leakage to a minimum.
Control valve |
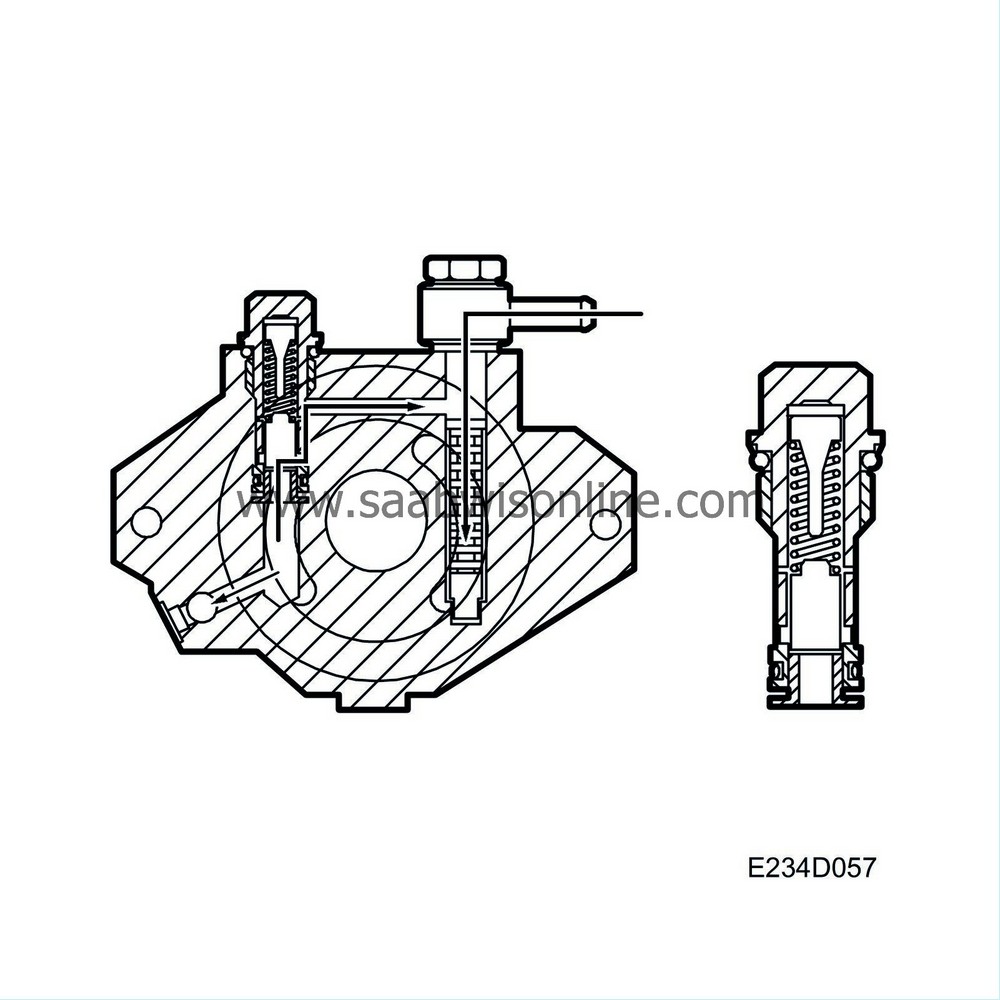
The control valve maintains the feed pressure below a certain level. As the engine speed increases, so will the speed of the pump rotor and the feed pressure. If the feed pressure exceeds 1.5 MPa, the control valve will open and lead the fuel to the suction side of the pump. If the feed pressure becomes too high and exceeds the calculated pressure of the power stage, there is a risk that the engine may be damaged and the fuel consumption will be too high.
Fuel control valves |
The fuel control valves are two electromagnetic valves with one solenoid that are controlled by the power stage. This control module sends a voltage impulse to the solenoid that controls the fuel control valve. The valve opens and closes depending on the length of the signal. The fuel control valve opening duration determines the amount of fuel and at what pressure the fuel is to enter the fuel rail. As theses valves only supply the amount of fuel that is required, the load on the fuel pump will consequently be lower (compared with the pump delivering excess pressure), which also helps to keep down fuel consumption.
Fuel control valve On/Off |
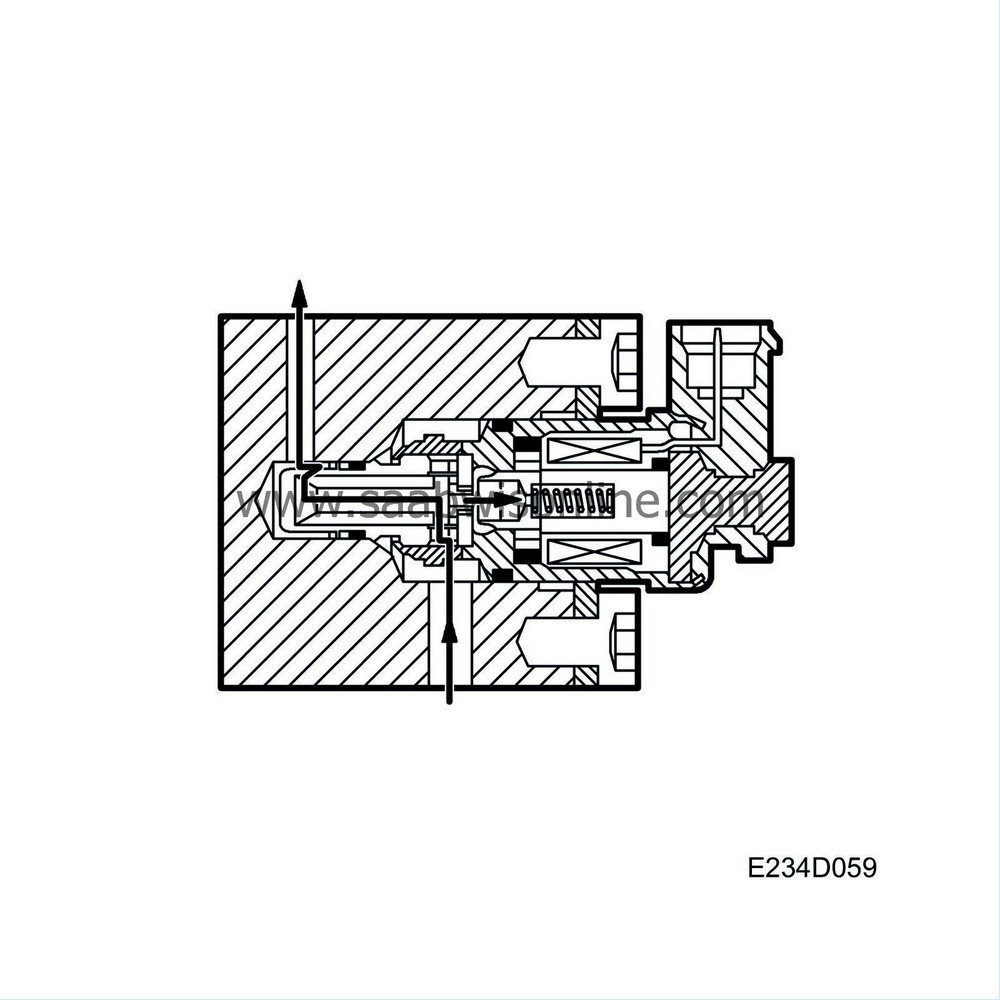
Current flow through the valve coil, opening the valve, and fuel is supplied to the high pressure side of the fuel pump.
As there is no current flowing through the coil, the valve will close and fuel is stopped from flowing to the high pressure side of the pump.
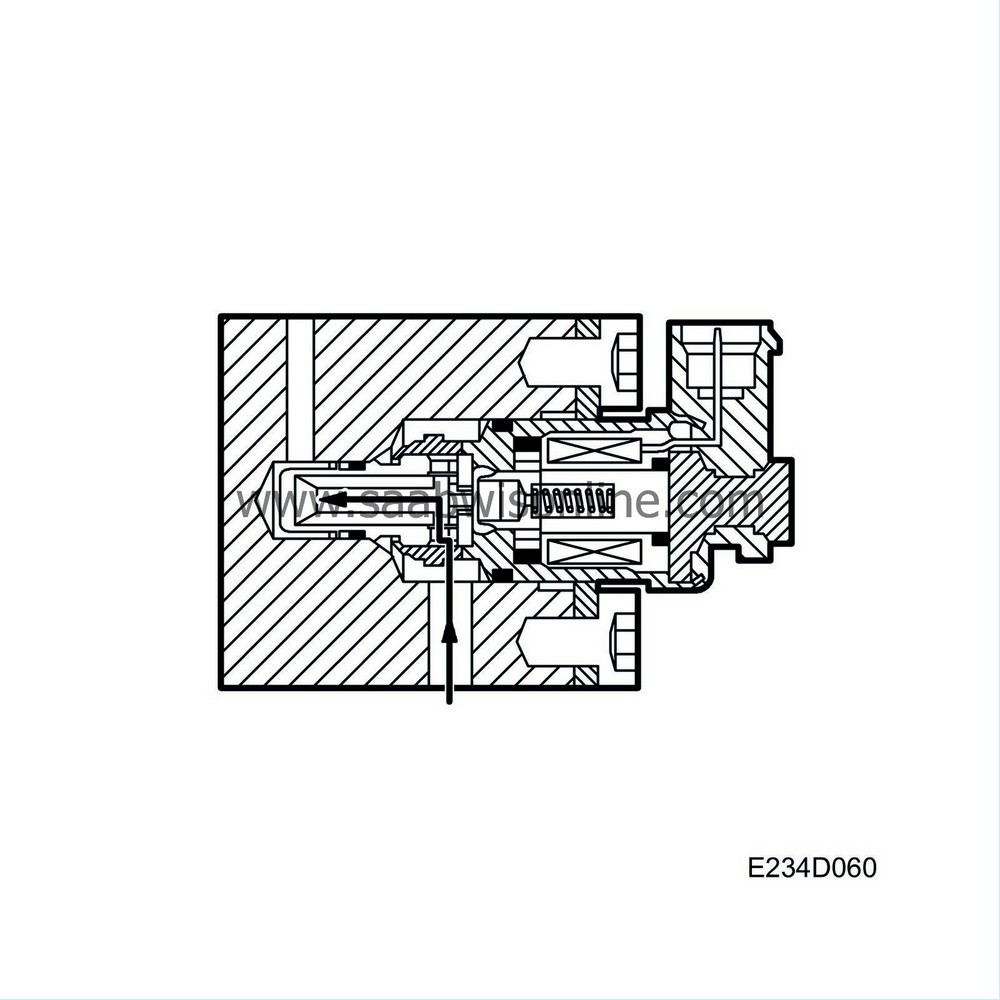
Check valve |
A check valve is mounted between the fuel control valves and the high pressure part of the pump. This valve prevents return fuel from the high pressure side flowing back to the fuel control valves.
Check valve Open
When fuel is being supplied from the fuel control valves, this valve is open. The fuel pressure overcomes a spring force and fuel is able to flow into the high pressure part of the pump.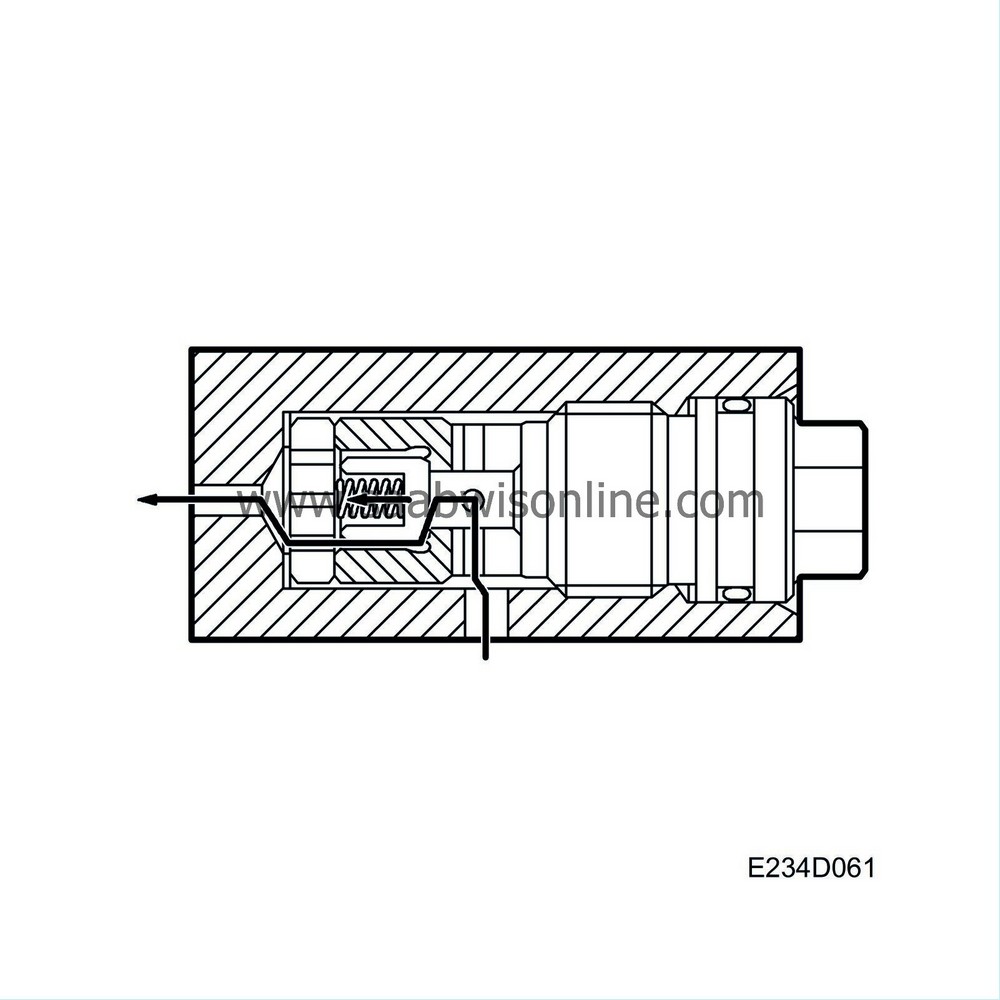
Check valve Closed
When fuel is not being supplied to the high pressure part of the pump, the check valve will be shut. Fuel in the high pressure part of the pump then presses against the valve, which remains closed.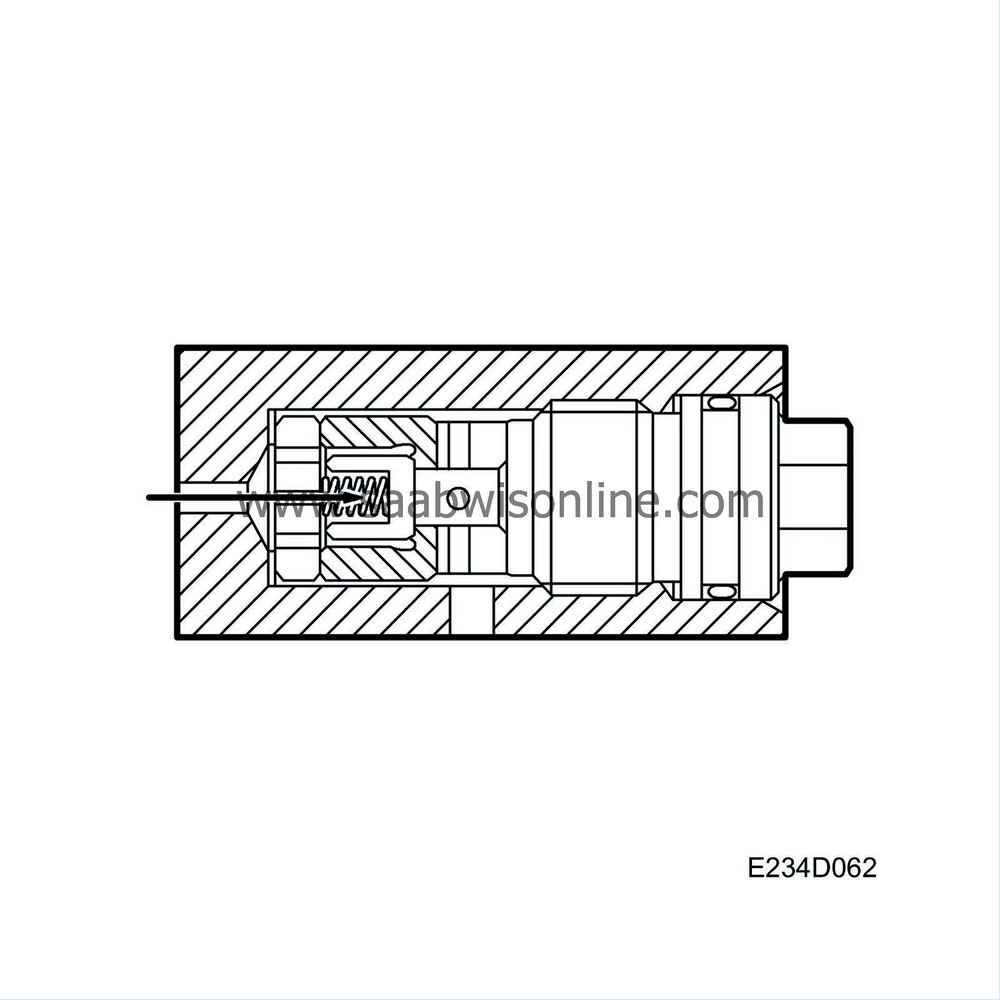
High pressure zone |
The high pressure pump receives fuel from the low pressure zone via the fuel control valves. These valves then supply fuel at high pressure to the fuel rail.
The fuel pump drive shaft and oval inner cam are one unit and consequently rotate at the same speed. Inside the oval inner cam are two twin pump plungers, one mounted horizontally and one mounted vertically. This means that there is always one pump drawing fuel, while the other delivers fuel at high pressure. During one pump revolution (two engine revolutions), the pump will deliver fuel to the fuel rail four times. The unit with pump plungers is in a fixed position and does not rotate.
The oval inner cam allows two intakes and two exhausts per revolution from each pair of plungers and since there are pairs of plungers both horizontally and vertically mounted, this will take place four times per pump revolution.
The intake phase starts when plungers in pair 1 are able to move away from each other. A signal from the power stage then opens the fuel control valve 1 and fuel is allowed to flow past the check valve and into the chamber. The opening duration of fuel control valve 1 is regulated depending on the fuel pressure that the power stage has determined. If the opening duration is short, the fuel pressure will be low and if the opening duration is long, the pressure will be high. Fuel control valve 2 will open shortly after fuel control valve 1 has closed.
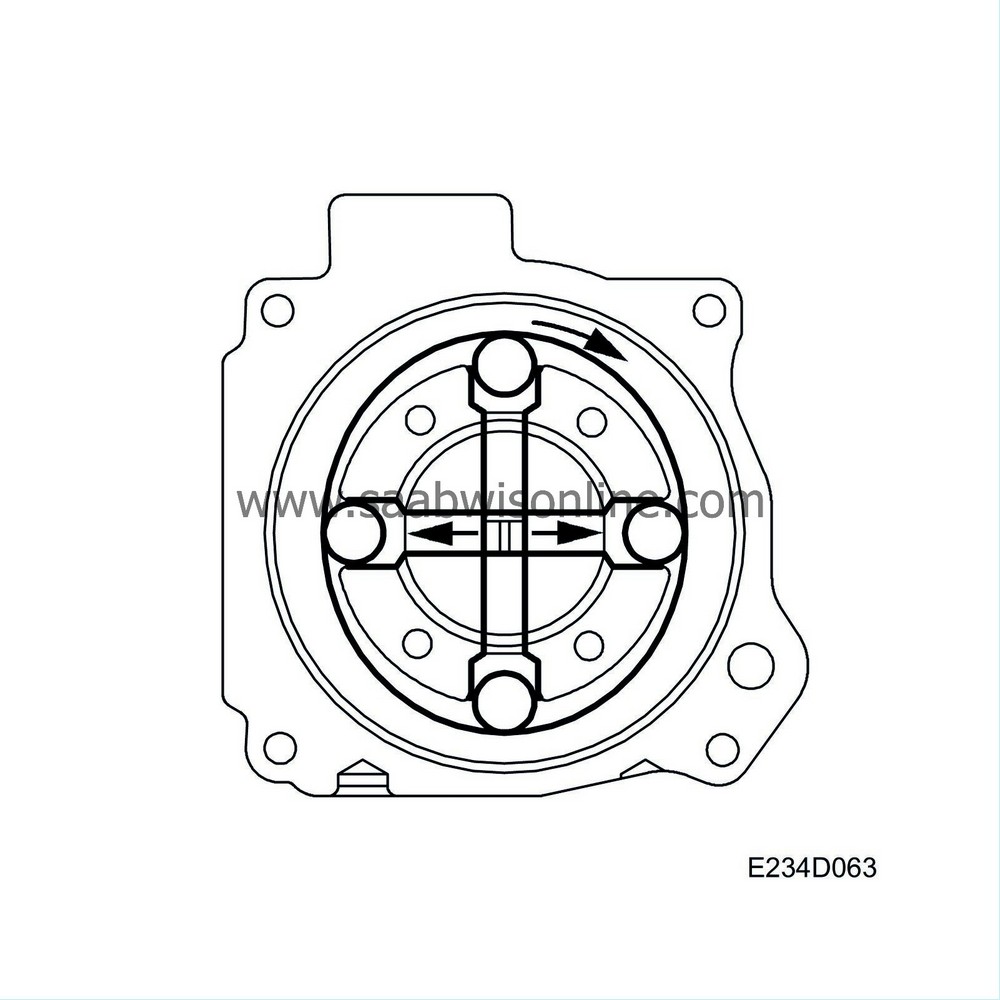
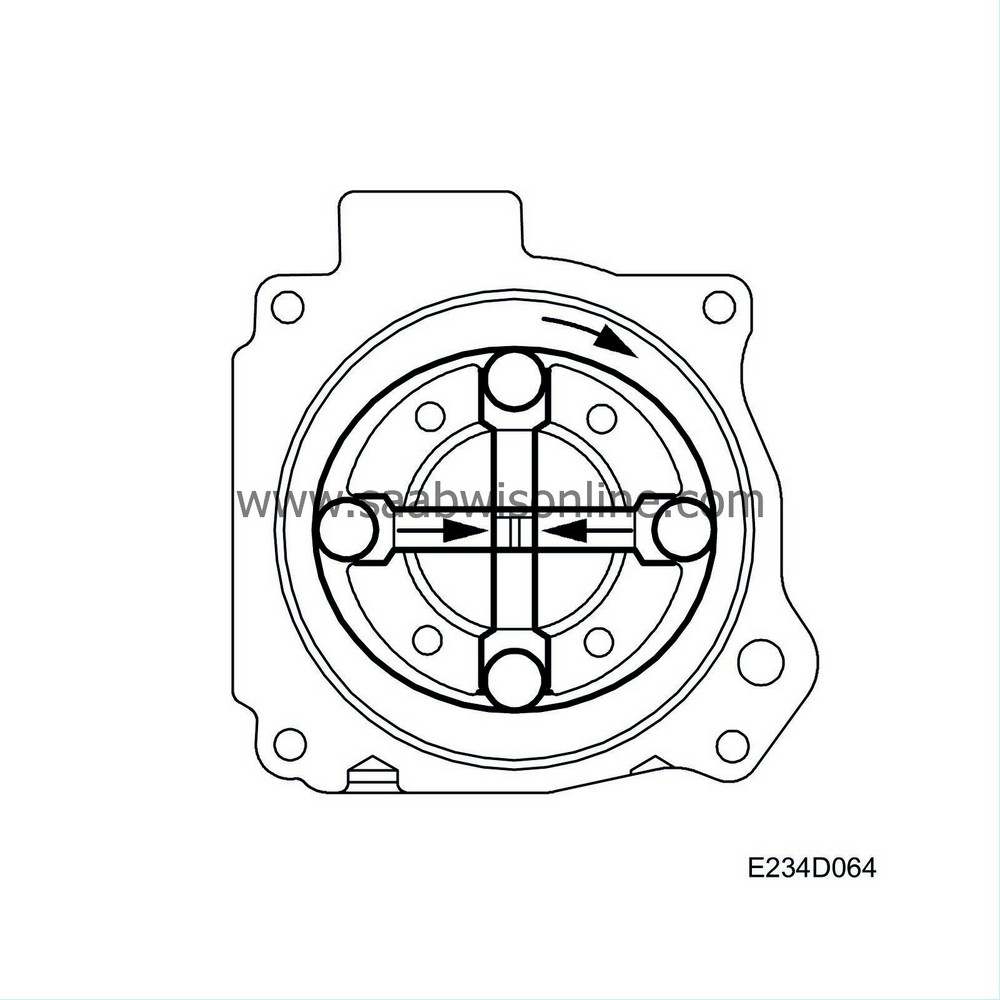
The fuel quantity can vary between 0 and 100%, which means that the plungers are not always in contact with the surface of the cam ring. The plungers will only draw fuel as long as the fuel control valves are open. Low pressure gives small volume and consequently a short plunger travel.
The crankshaft position sensor determines when the fuel control valves are to open because the fuel pump and the crankshaft positions are fixed in relation to each other. How long they are to be open is determined by the fuel pressure which is needed in the fuel rail, which is in turn determined by the power stage.
Outlet valve |
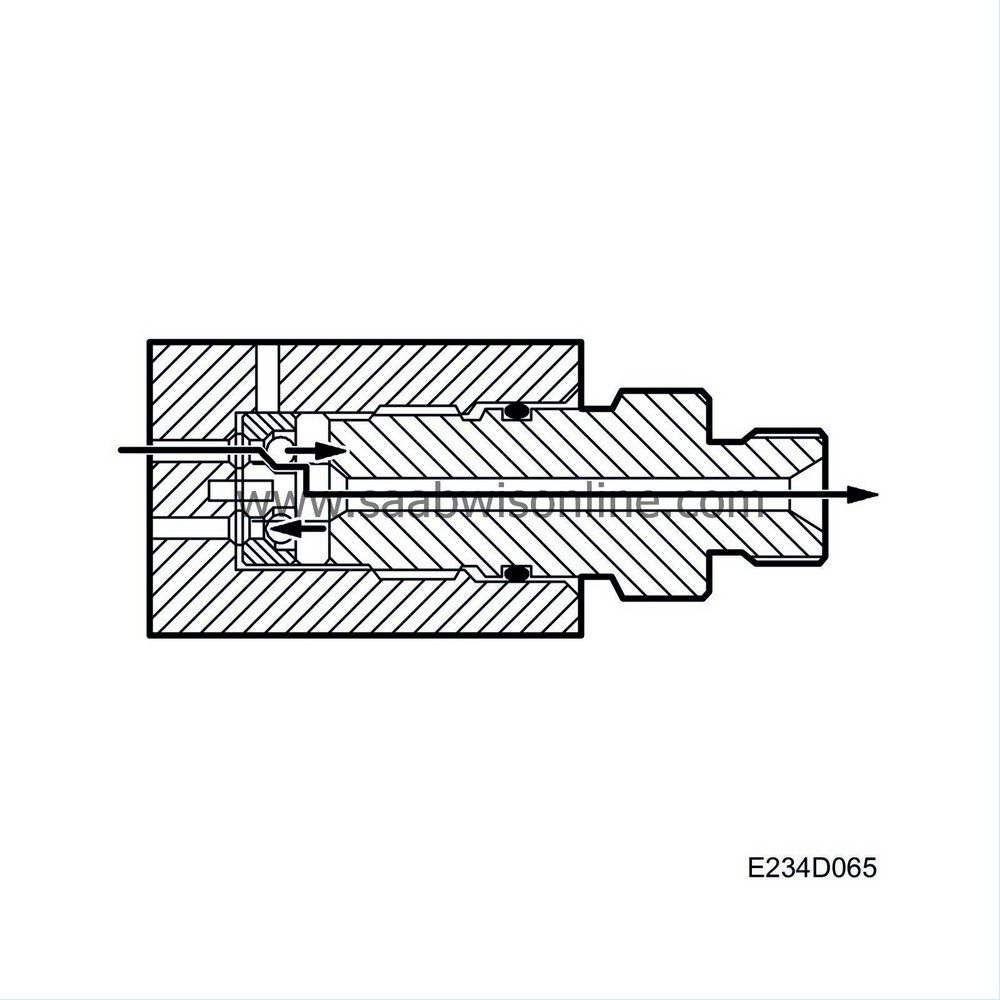
An outlet valve with two ports and two balls is fitted in the fuel pump outlet. It is used to make sure the pressure from plunger pair 1 is not returned to plunger pair 2 while the pump is operating. When fuel pressure from plunger pair 1 exceeds the fuel rail pressure, the valve will open to allow the fuel to be forced out. When the fuel pressure from plunger pair 2 increases, it will open for that pressure. At the same time, the system is protected against a return flow of the fuel.
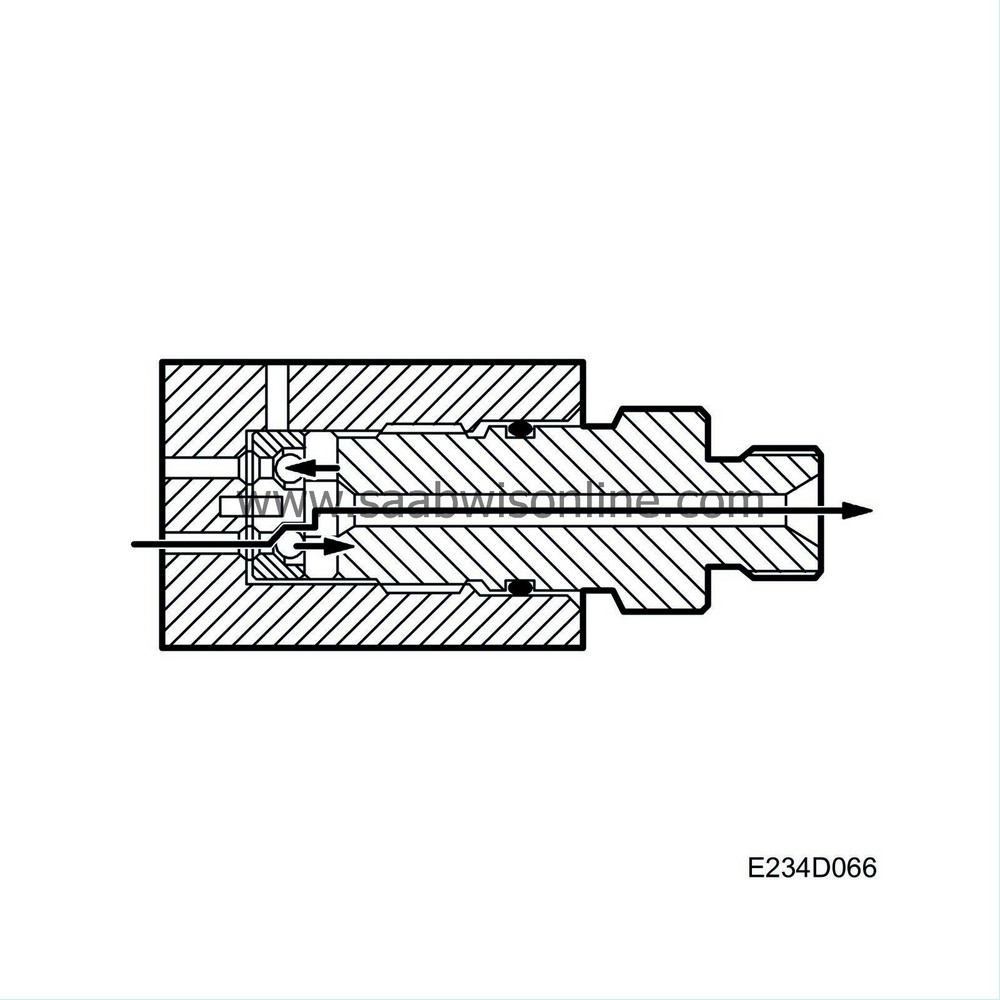
Fuel rail |
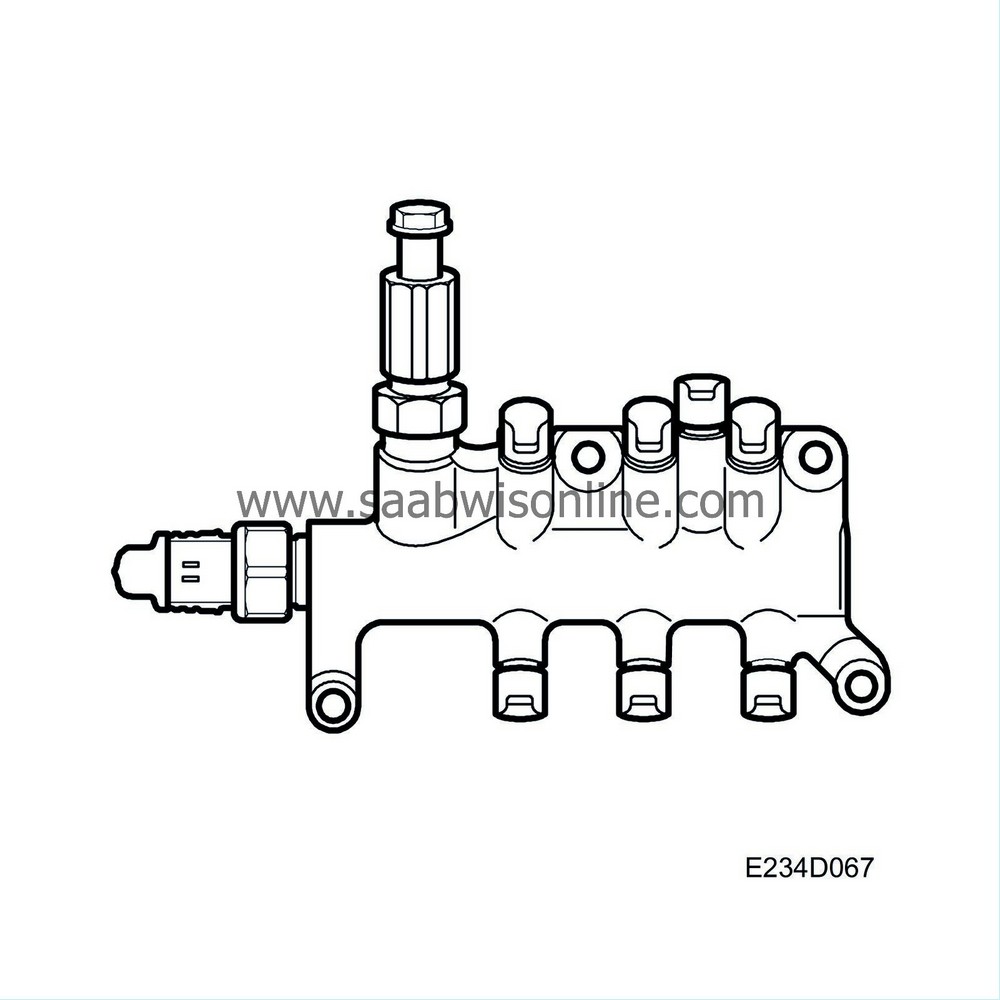
Fuel from the fuel pump is delivered at a pressure of 25 - 135 MPa to the fuel rail and then out to the different injectors. There is a pressure sensor and a safety valve on the fuel rail to lead the fuel back to the tank. The pressure sensor sends information on the pressure in the fuel rail to the engine control module. It is piezo-ceramic type and the information is used to finely adjust the pressure in the fuel rail.
The safety valve protects the fuel rail against excessive pressure. If the pressure in the fuel rail exceeds 150 MPa, the valve will open and allow fuel to pass back to the tank. The pressure must drop to 30 MPa before the safety valve closes.
Fuel injector |
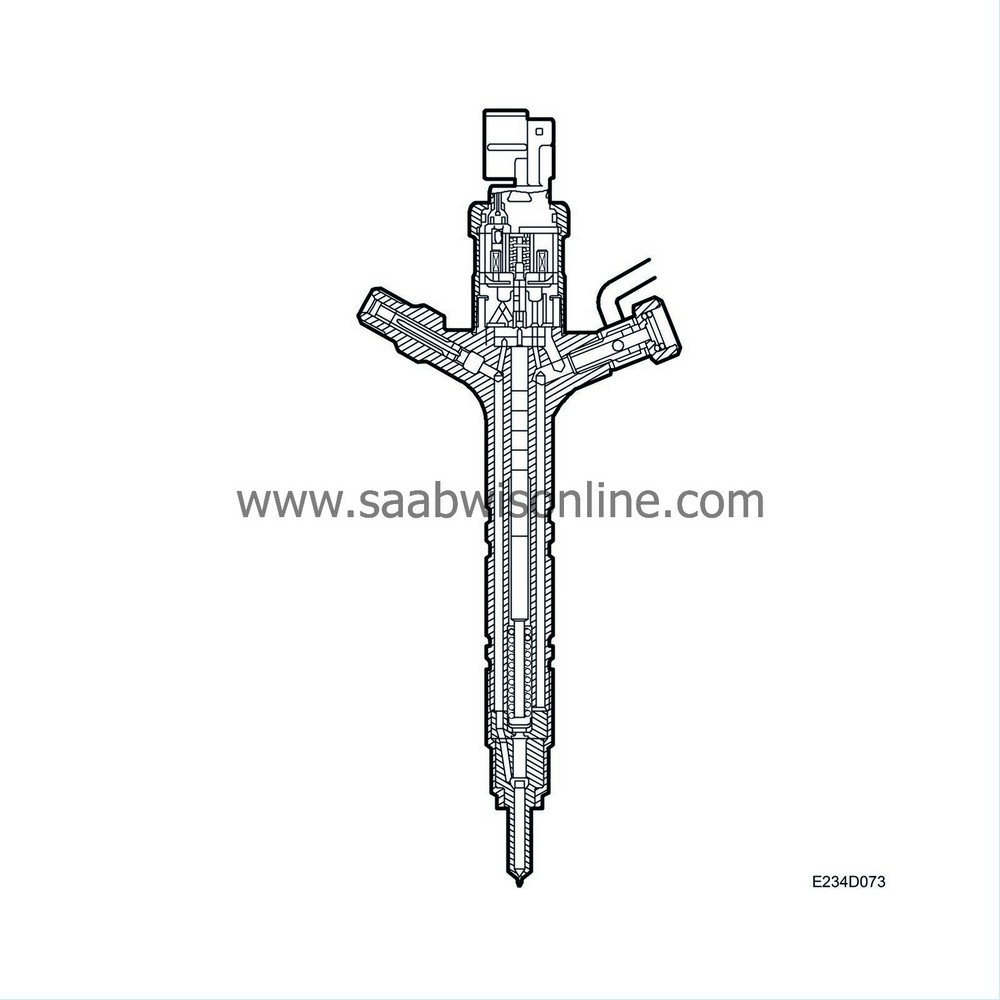
The operation of the fuel injector is controlled by the engine control module, which sends a signal to the power stage for opening the injector. Each injector receives fuel under pressure from the fuel rail via the fuel pipe leading to each cylinder. The injection timing and injection quantity is precisely calculated by the control module to obtain an optimum injection.
The compact injectors are electrically operated and have return connections to lead fuel back to the tank.
Function Opened/Closed injector |
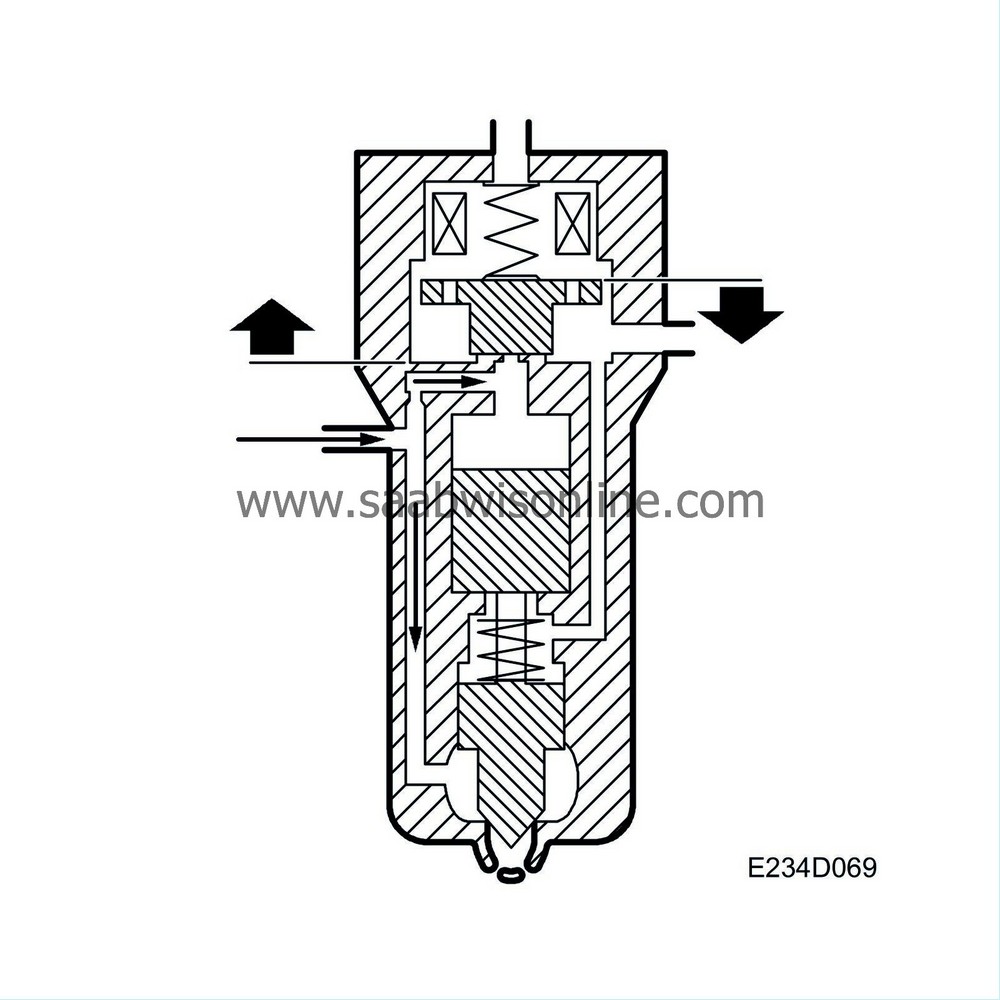
When there is no current flowing through the solenoid in the injector, the spring pressure forces the electromagnet against the pressure of the control chamber and the injector outlet is closed. Fuel pressure will force down the operating plunger and a spring will transfer this force to the nozzle, pressing it closed in its seat. Fuel will then not enter the combustion chamber.
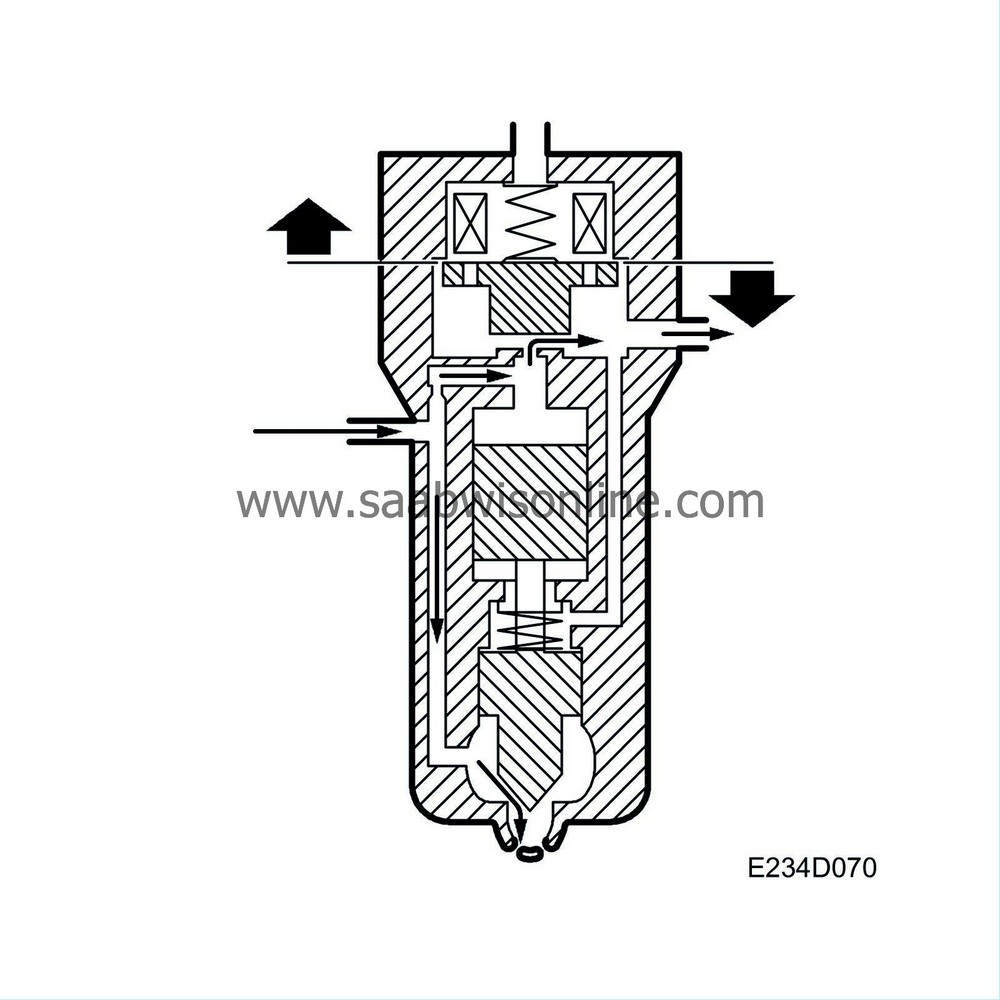
When current is flowing through the solenoid, the electromagnet will lift and the valve outlet will open. Fuel starts to flow from the control chamber and the pressure on the operating plunger will drop, allowing it to lift. The pressure from the fuel rail will then lift the nozzle and injection will take place. The fuel from the outlet will reach the return connection as well as below the operating plunger. This helps to lift the operating plunger at the start of injection and to close it at the end of injection. As long as current is flowing through the solenoid, the nozzle will remain in its upper position but as soon as current to the solenoid is cut, the nozzle will be pressed closed and fuel injection will cease.
See animation
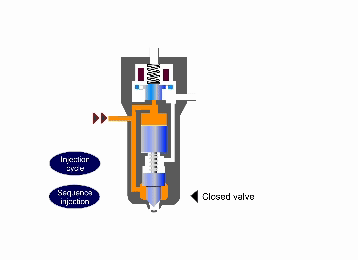
Electrical connection |
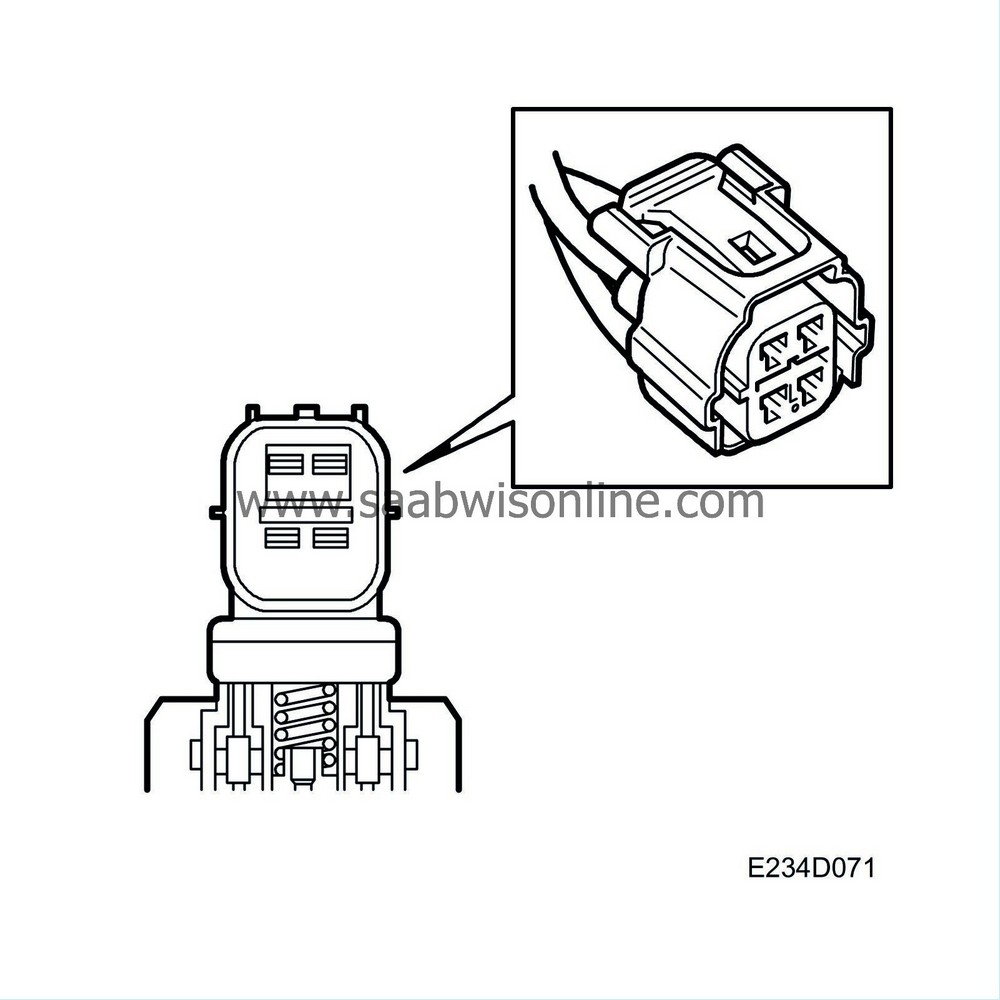
All six injectors have four connections, two for opening and closing plus two more, each connected to a resistor that measures the voltage through the injector so that the engine control module can compensate the timing of each individual injector depending on the tolerances that are inherent in them. The voltage is measured continuously but the engine control module will make only one adjustment each time the engine is started.
A high current is required to lift the electromagnet quickly, so the injectors have their own power stage to amplify the 12V signal from the engine control module. The power stage comprises a transformer to charge a condenser and a control section to ground the injector when it is to open. The power stage receives signals from all the sensors and then calculates the data to obtain the correct injection timing. A signal is then sent to the power stage, which handles the opening of each injector.