Dual-mass flywheel 4-cyl. diesel
Dual-mass flywheel 4-cyl. diesel |
Combustion in a piston engine gives rise to torsional vibrations in the crankshaft and flywheel. These vibrations are transferred to the transmission and via the engine mountings to the subframe and body. The crankshaft and flywheel torque produced by combustion varies, especially at low engine speeds. This means that gears not engaged will vibrate. Gearbox rattle can easily arise when the engine is idling, at high engine loads and when the engine is used for braking at low speeds. The solution is a dual-mass flywheel that comprises two separate flywheel masses; a primary and a secondary mass with a spring damper system connecting the two. This almost fully eliminates torsional vibrations in the gearbox and transmission. This means that the entire transmission becomes smoother. It prevents gearbox rattle when no gears are engaged and avoids body vibrations transmitted through the engine mountings.
This design solution increases gearchange quality and reduces gearbox wear. In addition, fuel consumption is reduced since it is possible to drive at lower engine speeds.
The primary section of the dual-mass flywheel is attached to the engine and the secondary mass on the transmission side. These two masses are elastically attached with a spring assembly that absorbs torsional vibrations from the engine.
Wide fluctuations of torque are above all produced during gearchanges under load at lower engine speeds, when driving at very low engine speeds when high torque is required and when the engine is started and stopped. These torque peaks are absorbed by the arched springs. At high speeds, the springs are pressed out against the spring housing, reducing their flexation. On the other hand, at how speeds, variations in torque are small, reducing the significance of the outer springs. Dual-mass flywheels do not have the springs that are normally fitted in the centre of the clutch plate, as the flywheel itself has taken over their role.
A pulley with vibration damper is fitted on the crankshaft belt circuit to prevent torsional vibrations being transmitted to the components driven by the drive belt.
To further dampen engine vibrations, the upper engine mountings and the lower mounting on the subframe are of the hydrolastic type.
4-cylinder diesel engines, as well as having a dual-mass flywheel, have a new clutch plate centre and a new pressure plate. There are no springs around the centre of the clutch plate as the flywheel itself has taken over their role.
The new pressure plate is fully self-adjusting, which means that the compression springs acted on by the release bearing are always in the same position relative to the release bearing. The diaphragm spring can move between an adjustment ring and a wear ring.
When the clutch lining wears, the wear ring moves with the pressure surface of the pressure plate. This movement reduces the load on the adjustment ring, which is rotated by two small springs and locked in position by a catch in the pressure plate housing. This means that the diaphragm spring maintains its original position.
This has several benefits, such as:
- Constant pedal force irrespective of clutch wear
- Improved service life of clutch and pressure plate
- Reduced pedal force
This new concept means that the pressure plate and clutch plate centre should be changed as a unit.

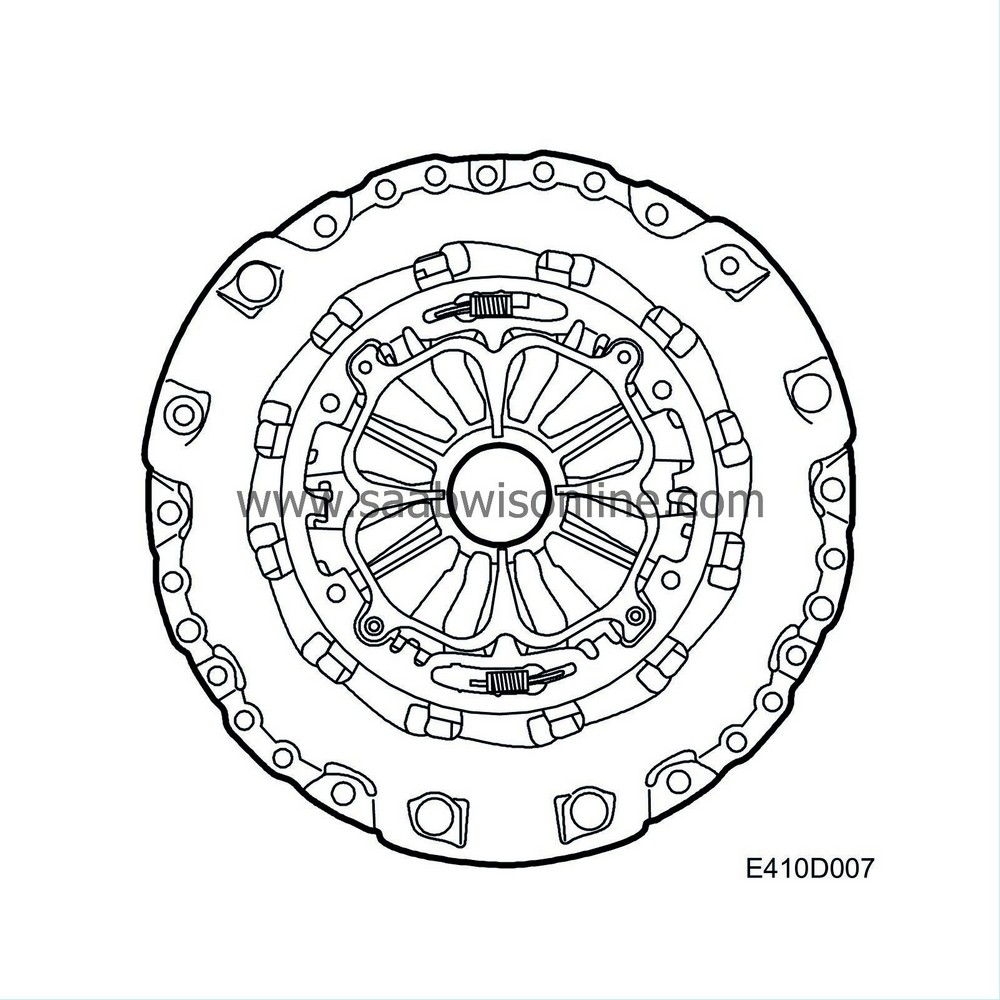