Boost Control System Description (LDK with Turbocharger)
Boost Control System Description (LDK with Turbocharger) |
(1) Evaporative Emission (EVAP) Canister Vent Solenoid Valve
(2) EVAP Canister
(3) Non-Return Valve
(4) EVAP Canister Purge Solenoid Valve
(5) High Pressure Fuel Pump
(6) Camshaft Position Actuator Solenoid Valve
(7) Turbocharger Bypass Valve Solenoid
(8) Turbocharger Bypass Valve
(9) Mass Air Flow (MAF)/Intake Air Temperature (IAT) Sensor
(10) Turbocharger Wastegate Actuator
(11) Turbocharger Wastegate Diaphragm Valve
(12) Camshaft Position Sensor
(13) Ignition Coil/Module and Spark Plug
(14) Fuel Injector
(15) Charge Air Cooler
(16) Intake Air Pressure and Temperature Sensor
(17) Throttle Body
(18) Manifold Absolute Pressure (MAP) Sensor
(19) Fuel Rail Pressure Sensor
(20) Engine Coolant Temperature (ECT) Sensor
(21) Exhaust Manifold
(22) Turbocharger
(23) Heated Oxygen Sensor (HO2S) 1 and 2
(24) Catalytic Converter
(25) Crankshaft Position Sensor
(26) Fuel Pump Module
(27) Accelerator Pedal
(28) Theft Deterrent
(29) Data Link Connector (DLC)
(30) Malfunction Indicator Lamp (MIL)
(31) GMLAN Serial Data
(32) Engine Control Module (ECM)
Boost Control Description and Operation |
A turbocharger is a compressor that is used to increase the power output of an engine by increasing the mass of the oxygen and therefore the fuel entering the engine. This BorgWarner™ dual-scroll turbocharger is mounted on the exhaust manifold and the lightweight turbine is driven by the waste energy generated by the flow of the exhaust gases. The turbine is connected by a shaft to the compressor which is mounted in the induction system of the engine. The compressor vanes compress the intake air above atmospheric pressure, thereby greatly increasing the density of the air entering the engine. The turbocharger is capable of producing up to 20 psi or 1.40 bar, of power-enhancing boost.
The turbocharger incorporates a wastegate that is controlled by a pressure differential, that is determined by the engine control module (ECM) by means of a PWM solenoid, in order to regulate the pressure ratio of the compressor. A turbocharger bypass valve is integrated within the unit, and is also controlled by the ECM by utilizing a remotely mounted solenoid to prevent compressor surging and damage from vibrations by opening during abrupt closed throttle conditions. When the bypass valve is commanded open during closed throttle deceleration conditions, the bypass valve allows the air to recirculate in the turbocharger and maintain compressor speed. Within a calibrated range during the closed throttle event, or upon a wide open throttle command the bypass valve will then close to optimize turbo response.
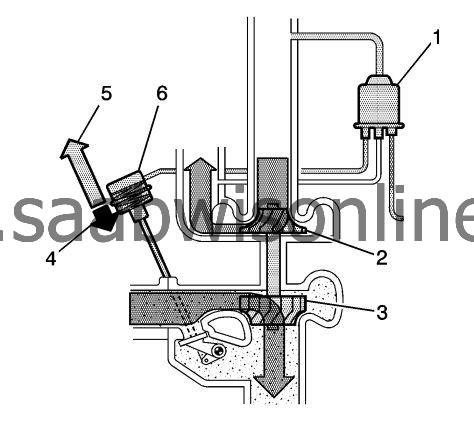
(1) Turbocharger Wastegate Actuator Solenoid Valve with Duty Cycle at 100 percent
(2) Compressor
(3) Turbine
(4) Exhaust Gas Pressure
(5) Spring Force
(6) Turbocharger Wastegate Diaphragm Valve
The wastegate is completely closed at idle. All of the exhaust energy is passing through the turbine. There are three reasons that the wastegate remains closed:
• |
There is a lack of compressor outlet pressure. Lower compressor outlet pressures tend to close the wastegate via the pneumatic connection to the diaphragm valve.
|
• |
The return spring within the diaphragm valve is helping to keep the wastegate closed.
|
• |
The low energy of the exhaust gas flow is not enough to overcome the return spring force.
|
During normal operation, if a wide open throttle were to be requested at lower engine speeds, the ECM will command the boost control solenoid with a duty cycle of 100 % to minimize any turbo lag. During engine loads in the middle and upper RPM ranges, the ECM will command the boost control solenoid, with a duty cycle of 65-80 %. Manifold pressures of up to 240 kPa are possible.
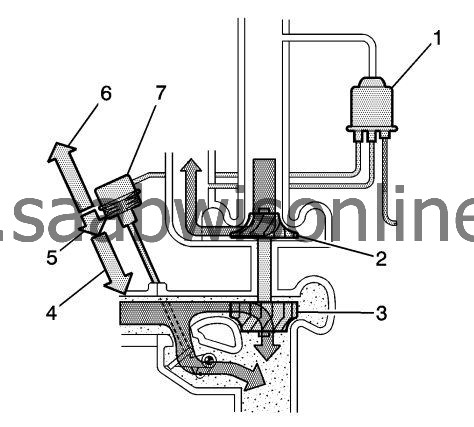
(1) Turbocharger Wastegate Actuator Solenoid Valve with Duty Cycle at 0 percent
(2) Compressor
(3) Turbine
(4) Regulating Pressure
(5) Exhaust Gas Pressure
(6) Spring Force
(7) Turbocharger Wastegate Diaphragm Valve
When certain DTCs are set the ECM will limit the amount of available boost pressure. Limiting boost pressure is accomplished by the ECM controlling the turbocharger wastegate actuator solenoid valve and maintaining the duty cycle at 0 %. This means that the ECM will not actively close the wastegate during greater engine loads. The system at this point is limited to mechanical boost. Mechanical boost means that the wastegate will still move, but the amount of motion is limited by the mechanical properties of the return spring within the diaphragm valve, the pneumatic properties of the actuator, and the physics of the exhaust gas flow in the exhaust system. In this mode of operation the manifold pressure will attain a maximum pressure of 140 kPa.
The turbocharger wastegate diaphragm valve assembly has a threaded rod and nut that connects the diaphragm of the valve to the wastegate. This rod is adjusted to BorgWarner™ factory specifications and is not adjustable.