PWM signals
PWM signals |
Measuring PWM |
PWM signals , i.e. communication between control modules, are always positive-triggered, i.e. the pulse is a positive voltage pulse from the battery. Other PWM outputs (inputs) are often negative-triggered, such as the injectors which are constantly supplied with positive current and pulsed with ground from the control module.
Measuring with voltmeter |
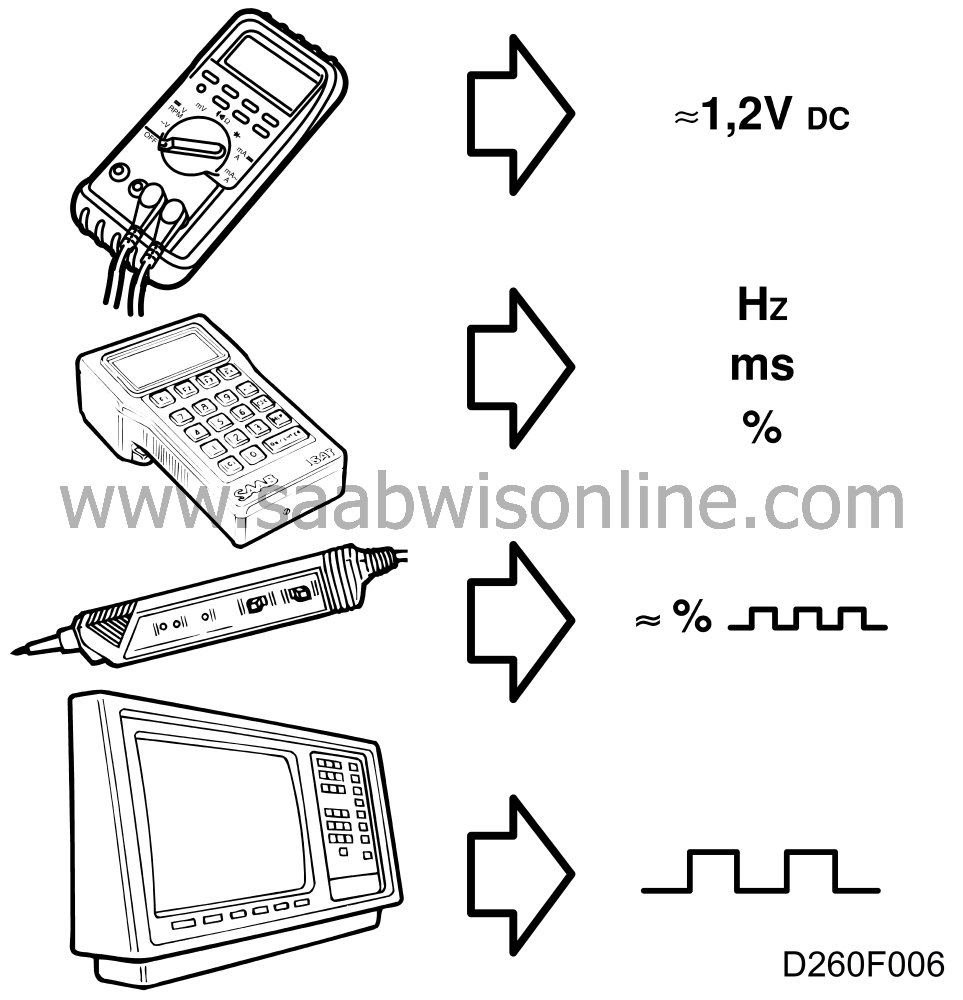
If you measure PWM with a voltmeter, the voltmeter will show the average voltage present on the cable, i.e. if the pulse ratio increases we obtain a higher average voltage. With the voltmeter we can obtain a rough estimate of the pulse ratio. At a pulse ratio of 9%%, the result is often about 1.2 V (0.09 x 13 V = 1.17 V). If the PWM is positive-triggered, connect the red test lead to the cable and the black test lead to a good ground. If the PWM is negative-triggered, connect the black test lead to the cable and the red test lead to battery positive voltage. If the voltmeter is equipped with a Smooth function, select this function.
Taking readings with the diagnostics instrument or multimeter with pulse measurement capability |
Connect the red measuring cable to the wire and the black measuring cable to safe ground. Then select positive or negative-triggering. You can now measure frequency, pulse time and pulse ratio.
Measuring with Logic Probe |
Connect battery + (positive) supply voltage and a good ground. Then apply the tip of the probe to the cable. The Logic Probe shows the presence of pulses, if any, and gives a rough estimate of the pulse ratio.
Measuring with oscilloscope |
Frequency and pulse duration readings can be obtained at the same time as a picture of the pulses is obtained. You can then see how pulse duration changes when the value of the information changes. For further information on PWM signals, see Service Manual 3.2 Electrical System, Wiring diagrams.