Component description, ORVR
Component description, ORVR |
Filler pipe |
Fuel is poured into the tank through the filler pipe (25 mm). It then passes through a non-return valve before actually entering the tank.
High up in the filler pipe is an insert to ensure that the fuel pump nozzle makes a good fit in the pipe when refuelling.
Important | ||
Draining the fuel tank must not be done by siphoning off the fuel via the filler pipe. This will damage the filler pipe. |
||
Non-return valve, fuel tank |
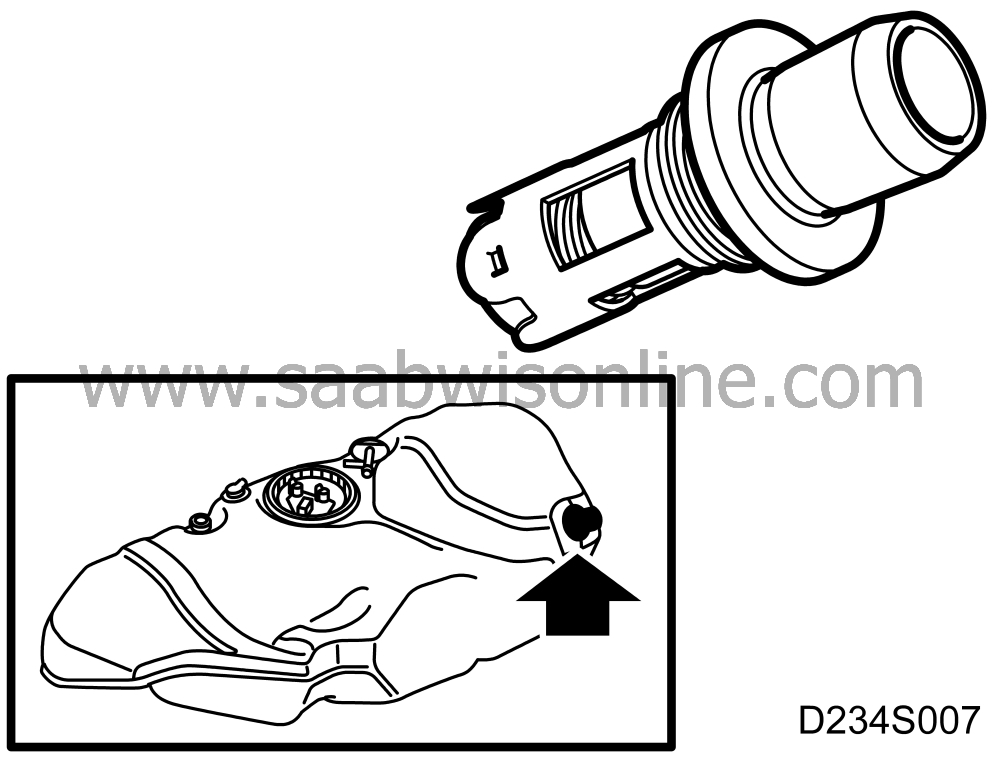
The non-return valve ensures that the fuel vapour (hydrocarbons) in the tank is not carried back up in the filler pipe.
Fuel tank |
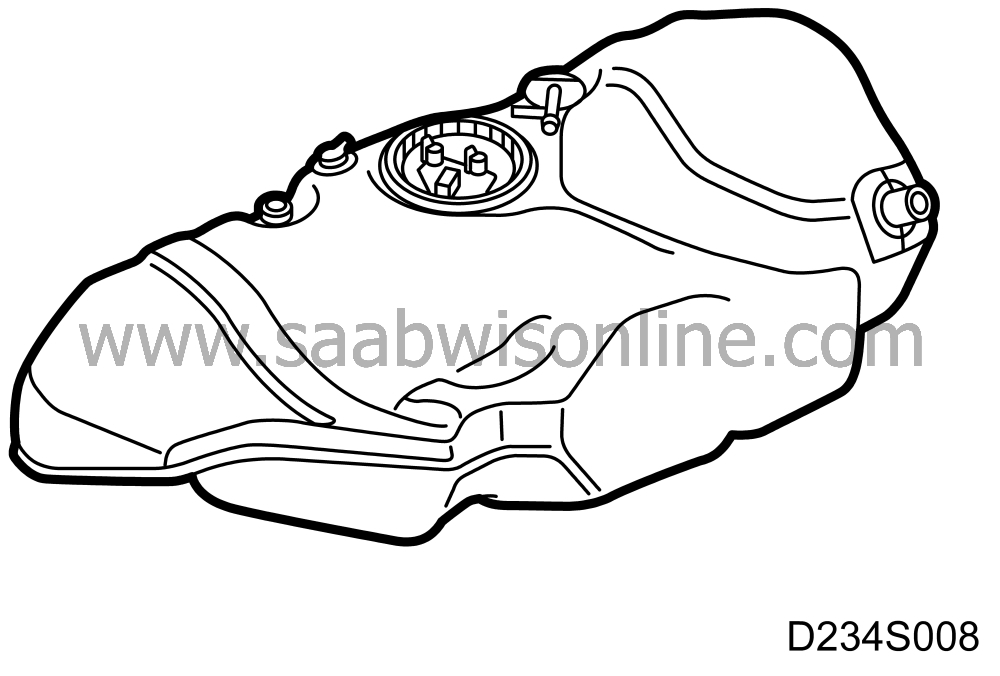
Tank capacity is 64 litres. All tank components are welded except the pressure sensor and fuel pump.
Float valve |
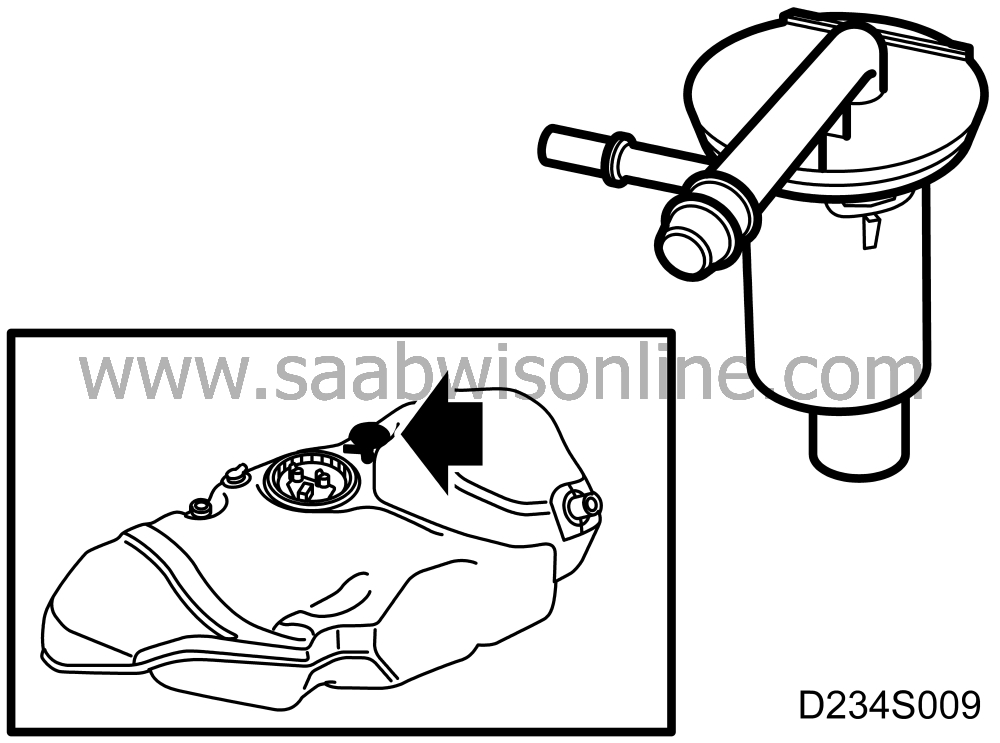
The float valve is connected to the evaporative emission canister by a hose. This prevents fuel in liquid form from reaching the evaporative emission canister. On refuelling, the vapour in the tank is pressed through the float valve and into the evaporative emission canister until the tank is full. The valve then closes.
A spring-loaded float closes the valve when the tank is full or in the event of rollover.
Evaporative emission canister |
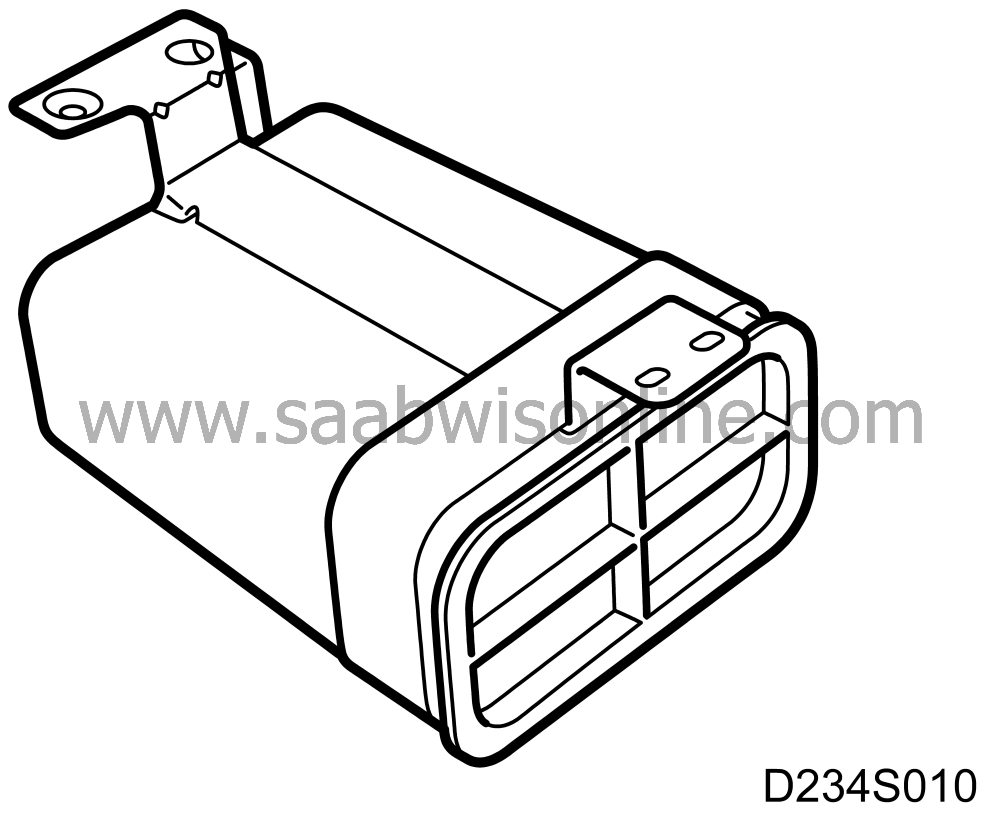
The evaporative emission canister, which is mounted behind the tank, consists of a container filled with special charcoal in pellet form and is mounted behind the tank. Charcoal in pellet form is used so that the evaporative emission canister will exert as little counterpressure as possible. The hydrocarbons which evaporate in the tank pass through a hose to the evaporative emission canister. The activated charcoal in the evaporative emission canister gradually becomes saturated as it absorbs the hydrocarbons.
The evaporative emission canister is connected by hoses to the fuel tank and the intake manifold. It is also in communication with the surrounding air. When the engine is started, ambient air is sucked through the evaporative emission canister via the purge valve and into the intake manifold. The hydrocarbons follow along with the air and are burnt in the engine.
The evaporative emission canister absorbs about 80-90 grammes of hydrocarbons per full refuelling of the tank. The time it takes to purge the evaporative emission canister of hydrocarbons depends on how the car is driven. It will be fully purged next time refuelling takes place. The evaporative emission canister can absorb 150 grammes of hydrocarbons at most.
Shut-off valve |
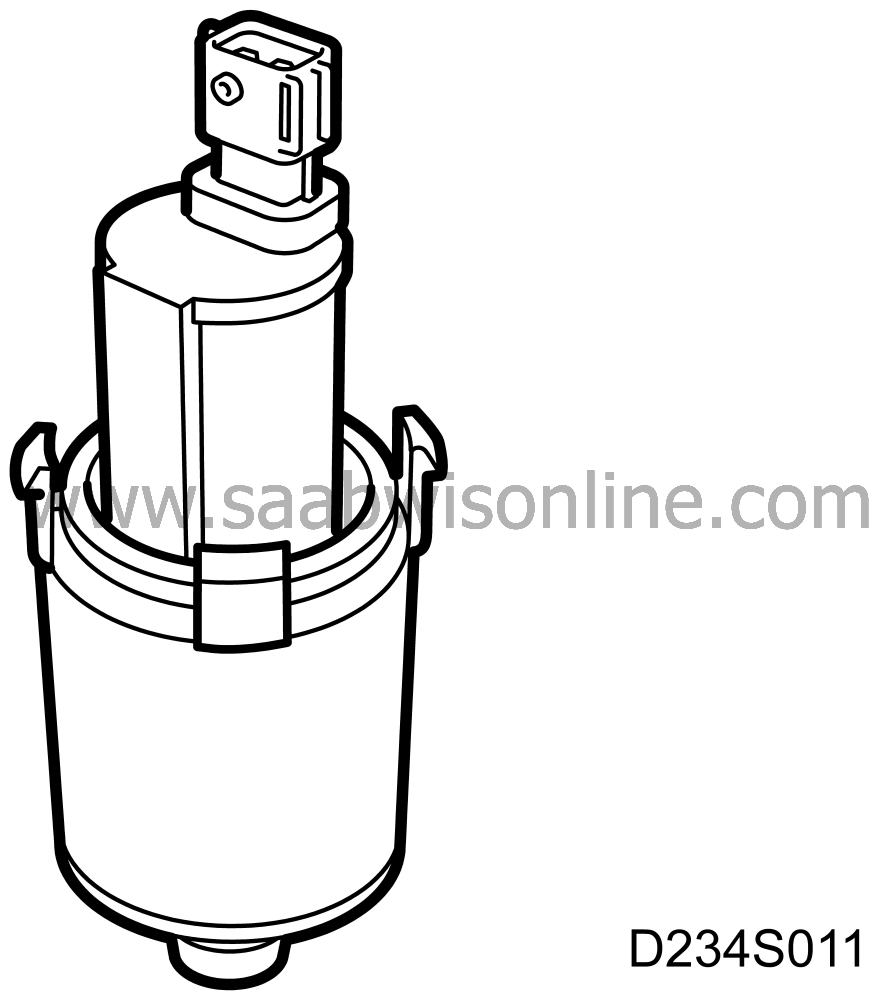
The shut-off valve is connected to the evaporative emission canister's air connection and is supplied with current from the main relay.
The valve is open in the zero current state.
When the engine is running, the valve closes only when a tank integrity check is performed.
The shut-off valve is used for OBD II diagnostics.
Pressure sensor, fuel tank |
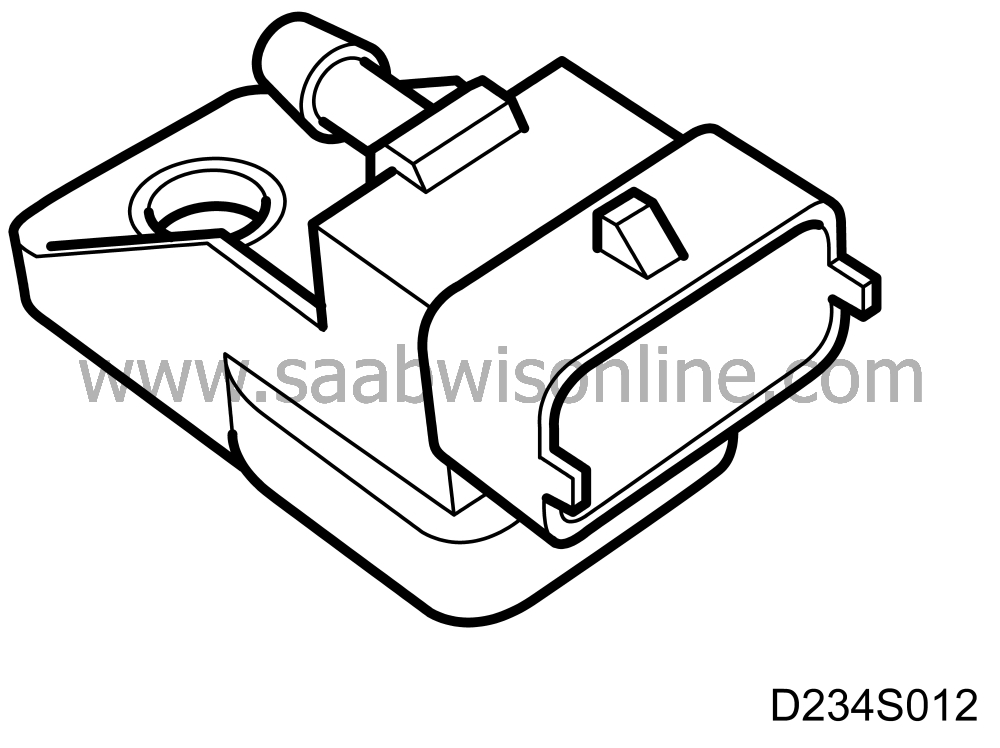
A differential pressure sensor is mounted on the tank. It compares the pressure in the tank with barometric pressure.
The pressure sensor is supplied with 5 V from the control module.
Depending on the pressure difference between the tank and the atmosphere, the pressure sensor supplies the control module with a proportional voltage.
When there is no pressure difference, the voltage from the pressure sensor will be about 2.5 V.
The pressure sensor is used for OBD II diagnostics.
EVAP canister purge valve |
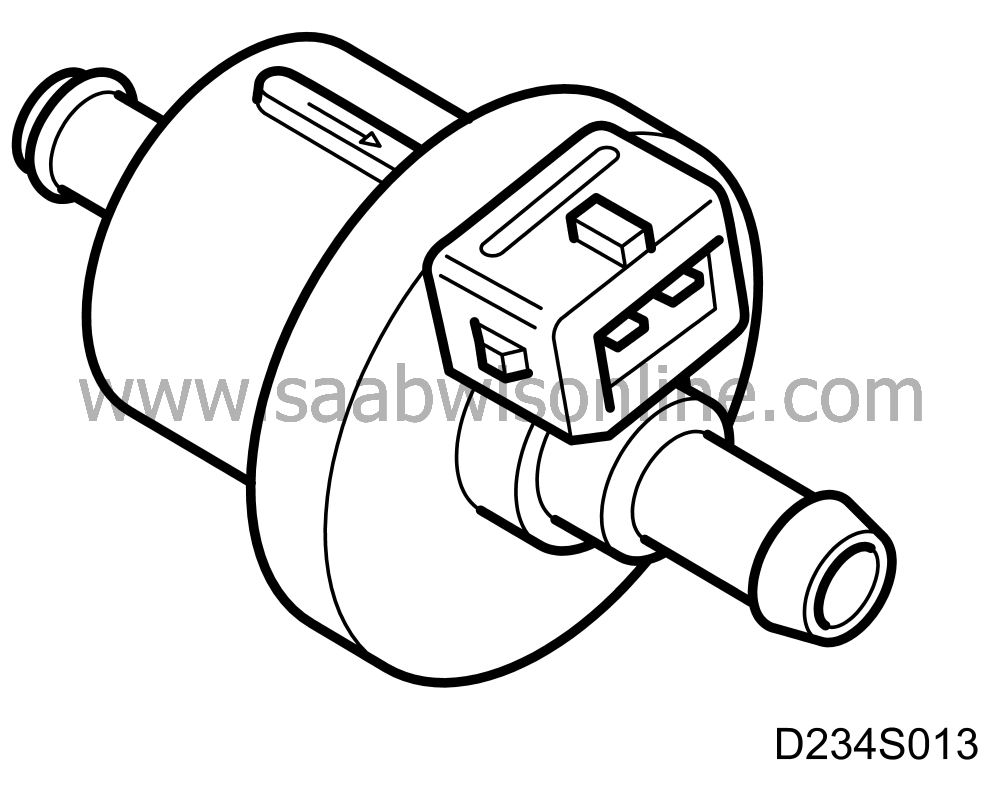
The evap canister purge valve consists of a solenoid valve in the hose between the evaporative emission canister and the intake manifold. It is used to control the quantity of air/hydrocarbons from the evaporative emission canister that is passed into the engine and burnt.
Shut-off valve, rollover |
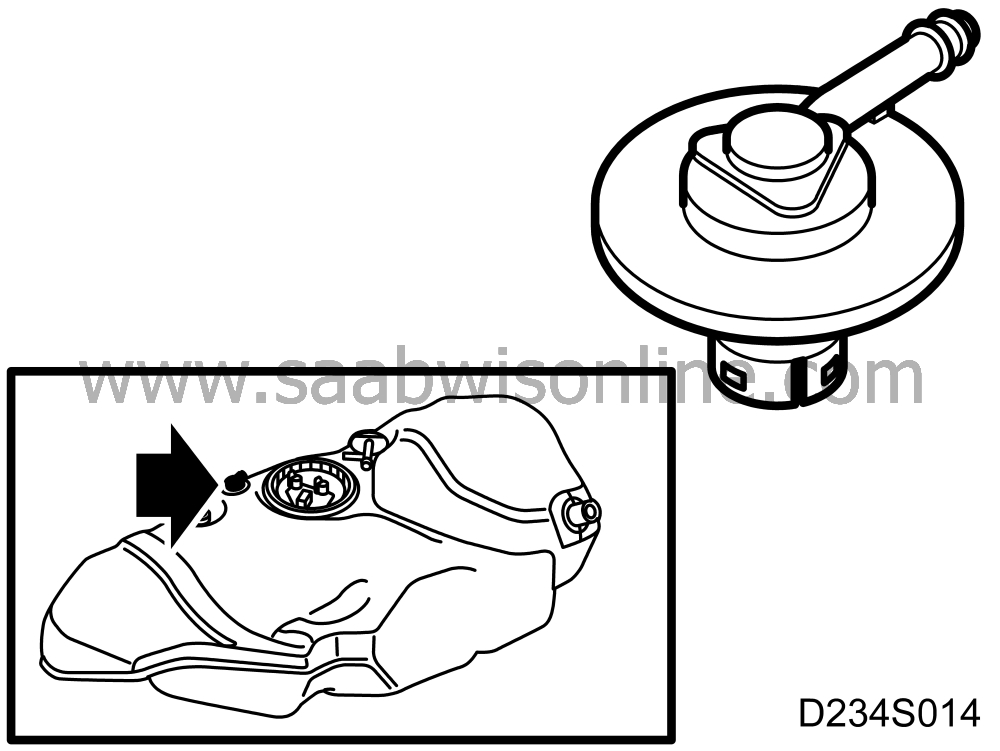
The rollover shut-off valve closes only in connection with a rollover and prevents fuel leakage should this happen. A hose connects the valve to the evaporative emission canister. Air which expands in the tank is purged through the valve and the evaporative emission canister.