INSPECTION
INSPECTION |
CYLINDER BLOCK |
Visually check for cracks and damage. Especially, inspect the important parts by means of red lead check.
Check the oil passages for clogging.
Inspect the cylinder block surface that mates with cylinder head for warping by using a straight edge, and correct by grinding if necessary.
Warping limit:
0.025 mm (0.00098 in)
Grinding limit:
0.1 mm (0.004 in)
Standard height of cylinder block:
201.0 mm (7.91 in)
CYLINDER AND PISTON |
The cylinder bore size is stamped on the cylinder block’s front upper surface.
Note | ||
• |
Measurement should be performed at a temperature of
20°C (68°F).
|
|
• |
Standard sized pistons are classified into two grades, “A” and “B”.
These grades should be used as guide lines in selecting a standard
piston.
|
Standard diameter:
A: 99.505 — 99.515 mm (3.9175 — 3.9179 in)
B: 99.495 — 99.505 mm (3.9171 — 3.9175 in)
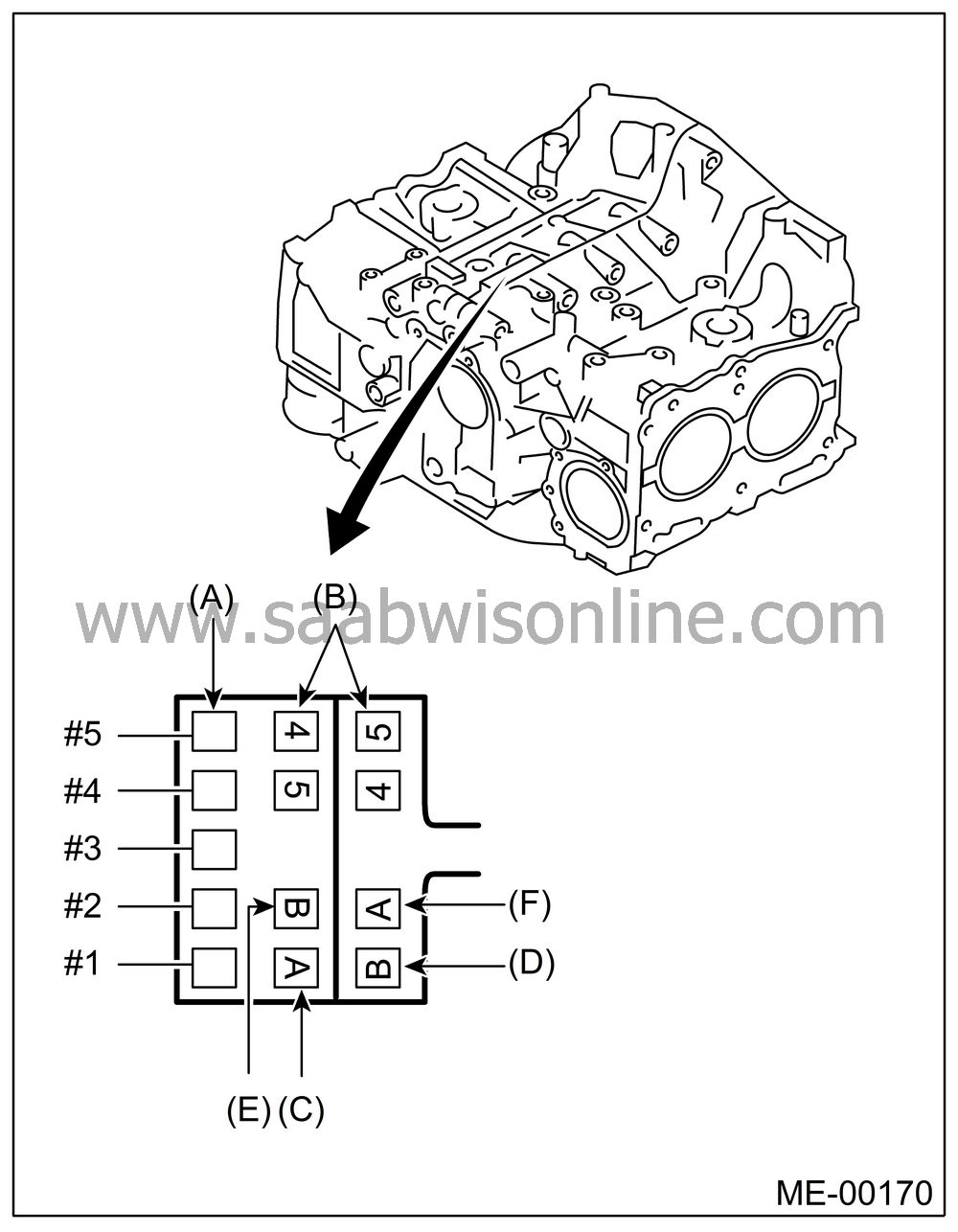
(A)
|
Main journal
size mark
|
(B)
|
Cylinder
block (RH)-(LH) combination mark
|
(C)
|
#1
cylinder bore size mark
|
(D)
|
#2
cylinder bore size mark
|
(E)
|
#3
cylinder bore size mark
|
(F)
|
#4
cylinder bore size mark
|
How to measure the inner diameter of each cylinder:
Measure the inner diameter of each cylinder in both the thrust and piston pin directions at the heights as shown in the figure, using a cylinder bore gauge.
Note | ||
Measurement should be performed at a temperature of 20°C (68°F). |
Taper:
Standard
0.015 mm (0.0006 in)Out-of-roundness:
Standard
0.010 mm (0.0004 in)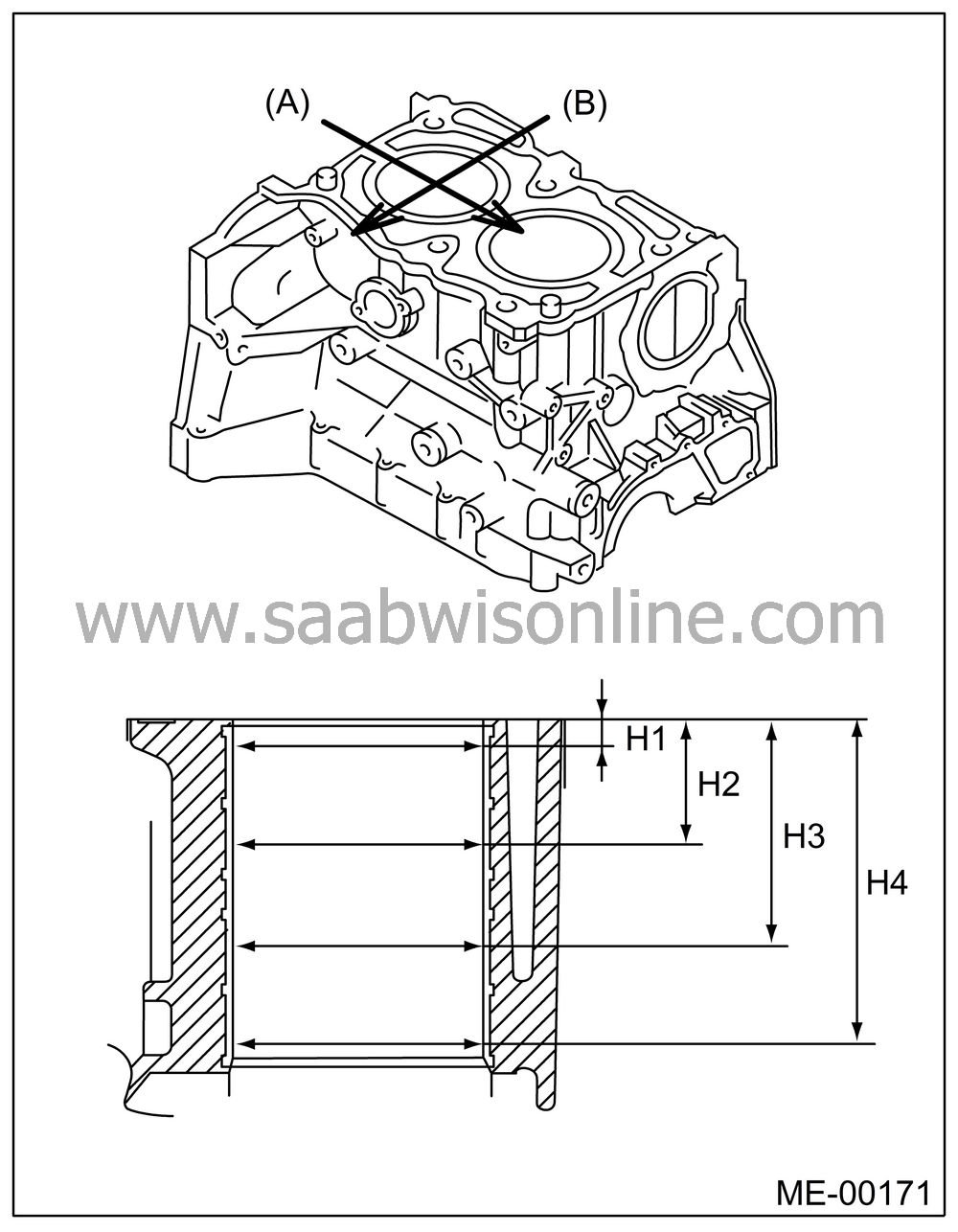
(A)
|
Piston
pin direction
|
(B)
|
Thrust
direction
|
H1
|
10 mm (0.39
in)
|
H2
|
45 mm (1.77
in)
|
H3
|
80 mm (3.15
in)
|
H4
|
115 mm
(4.53 in)
|
When the piston is to be replaced due to general or cylinder wear, determine a suitable sized piston by measuring the piston clearance.
How to measure the outer diameter of each piston:
Measure the outer diameter of each piston at the height as shown in the figure. (Thrust direction)
Note | ||
Measurement should be performed at a temperature of 20°C (68°F). |
Piston grade point H:
37.0 mm (1.457 in)
Standard
A: 99.505 — 99.515 mm (3.9175 — 3.9179 in)
B: 99.495 — 99.505 mm (3.9171 — 3.9175 in)
0.25 mm (0.0098 in) oversize
99.745 — 99.765 mm (3.9270 — 3.9278 in)
0.50 mm (0.0197 in) oversize
99.995 — 100.015 mm (3.9368 — 3.9376 in)
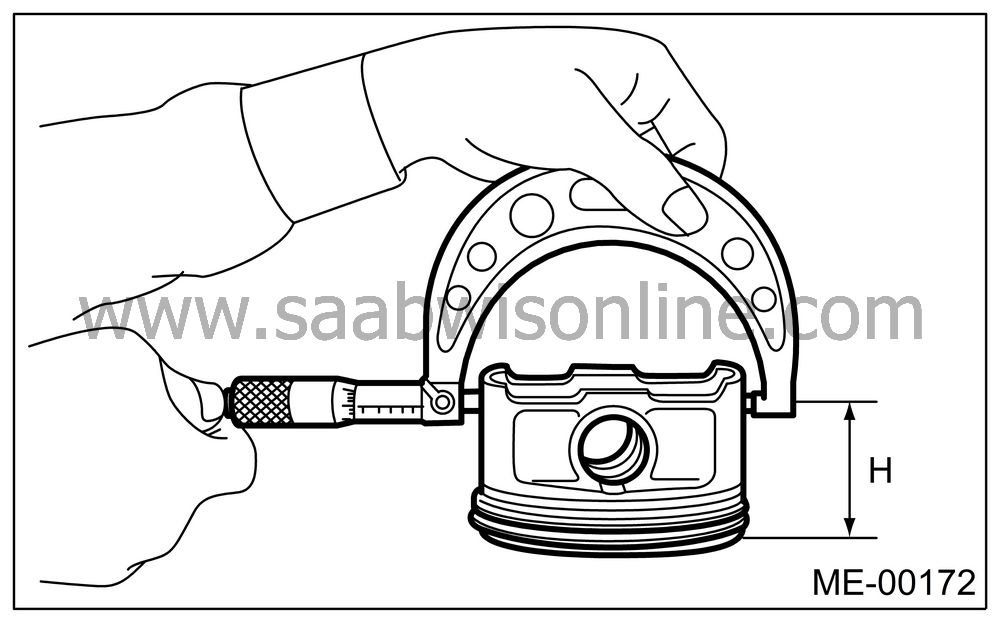
Calculate the clearance between cylinder and piston.
Note | ||
Measurement should be performed at a temperature of 20°C (68°F). |
Cylinder to piston clearance at 20°C (68°F):
Standard
−0.010 — 0.010 mm (−0.00039 — 0.00039 in)Boring and honing
If the value of taper, out-of-roundness, or cylinder-to-piston clearance measured exceeds the standard value or if there is any damage on the cylinder wall, rebore it to use an oversize piston.
Important | ||
When any of the cylinders needs reboring, all other cylinders must be bored at the same time, and use oversize pistons. Do not perform boring on one cylinder only. Nor use an oversize piston for one cylinder only. |
||
If the cylinder inner diameter exceeds limit after boring and honing, replace the cylinder block.
Limit of cylinder inner diameter:
100.015 mm (3.9376 in)
Note | ||
Immediately after reboring, the cylinder diameter may differ from its real diameter due to temperature rise. Thus, pay attention when measuring the cylinder diameter. |
Limit of cylinder boring:
0.5 mm (0.020 in)
PISTON AND PISTON PIN |
Check the pistons and piston pins for damage, cracks and wear, and the piston ring grooves for wear and damage. Replace if defective.
Measure the piston-to-cylinder clearance at each cylinder.

Make sure that the piston pin can be inserted into the piston pin hole with a thumb at 20°C (68°F). Replace if defective.
Clearance between piston hole and piston pin:
Standard
0.004 — 0.008 mm (0.0002 — 0.0003 in)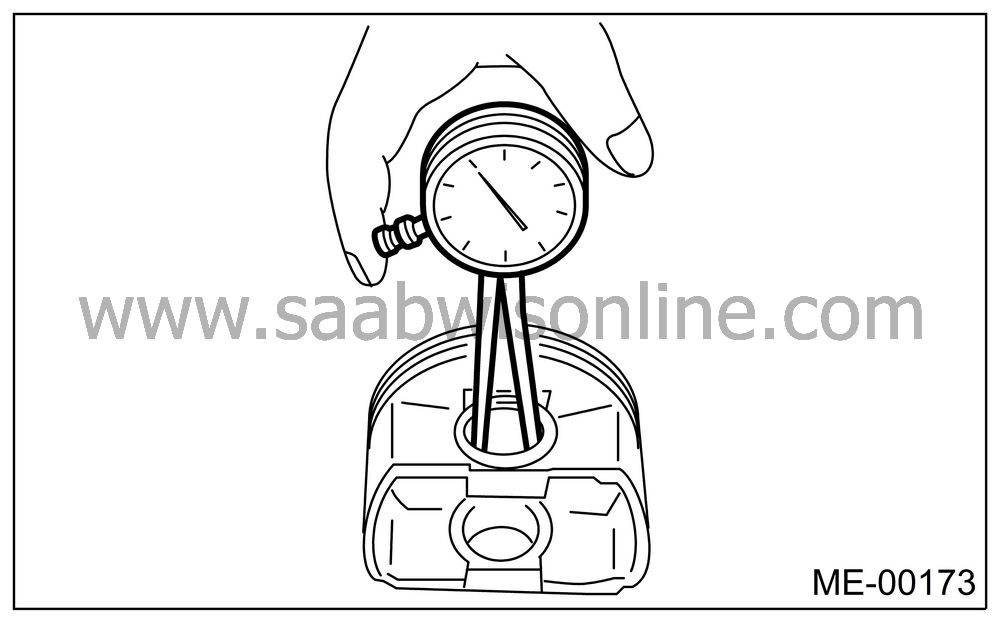
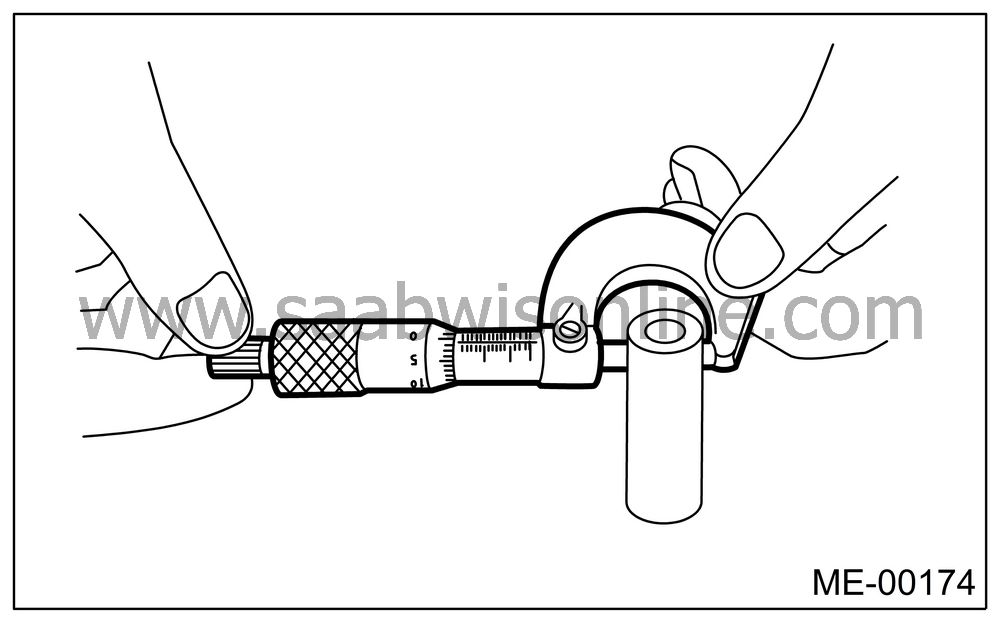
Check the snap ring installation groove (A) on the piston for burr. If necessary, remove burr from the groove so that the piston pin can lightly move.
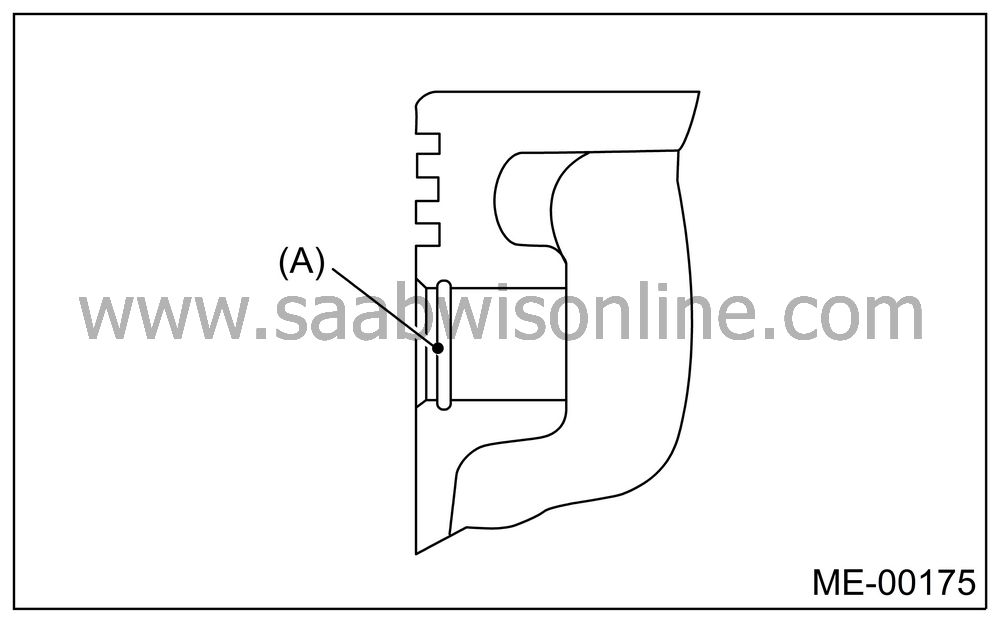
Check the piston pin snap ring for distortion, cracks and wear.
PISTON RING |
If the piston ring is broken, damaged or worn, or if its tension is insufficient, or when the piston is replaced, replace the piston ring with a new one of the same size as the piston.
Important | ||
• |
Mark is displayed on the end
of top and second rings. When installing the rings to the piston,
face these marks upward.
|
|
• |
Oil ring consists of the upper rail, expander and lower
rail. Be careful about the direction of rail when installing the
oil ring to piston.
|
|
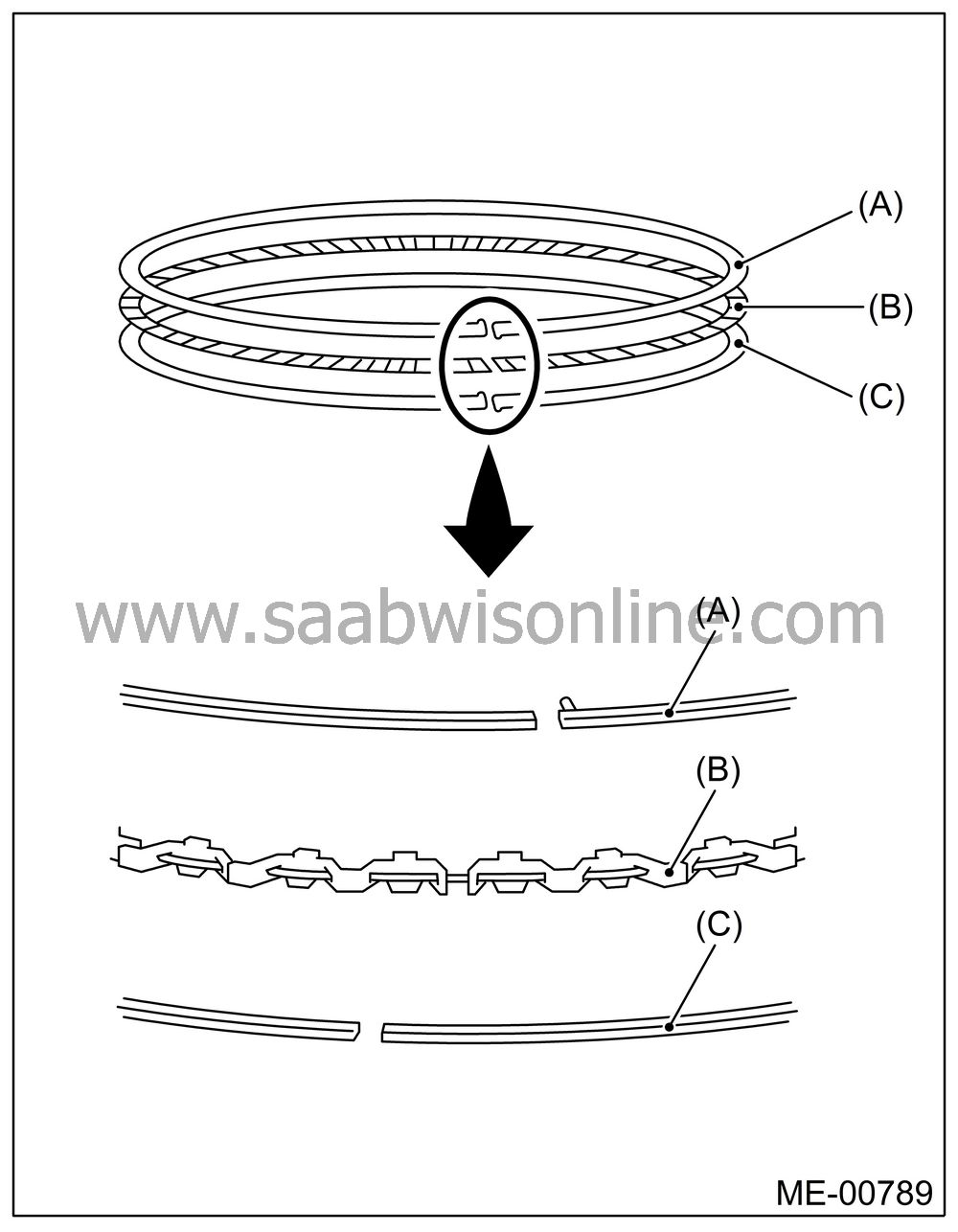
(A)
|
Upper rail
|
(B)
|
Expander
|
(C)
|
Lower rail
|
Clean the piston ring groove and piston ring.
Squarely place the piston ring and oil ring in cylinder, and measure the piston ring gap with a thickness gauge.
Standard
mm (in)
|
|||
Piston ring gap
|
Top ring
|
0.20 — 0.35
(0.0079 — 0.0138) |
|
Second ring
|
0.37 — 0.52
(0.0144 — 0.020) |
||
Oil ring rail
|
0.20 — 0.50
(0.0079 — 0.0197) |
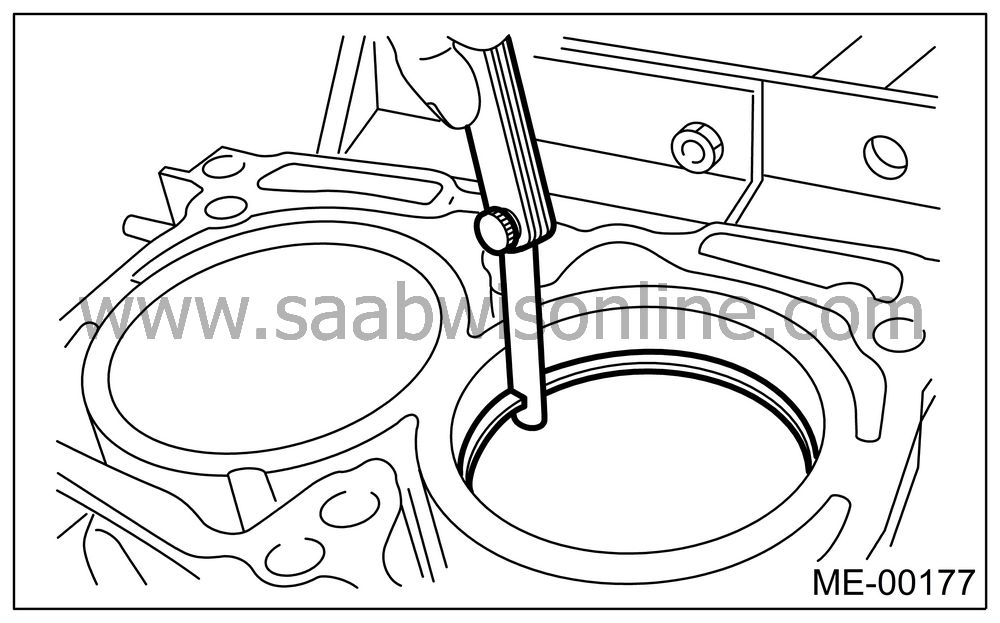
Measure the clearance between piston ring and piston ring groove with a thickness gauge.
Standard
mm (in)
|
||
Clearance between piston ring and piston ring groove
|
Top
ring
|
0.040 — 0.080
(0.0016 — 0.0031) |
Second
ring
|
0.030 — 0.070
(0.0012 — 0.0028) |
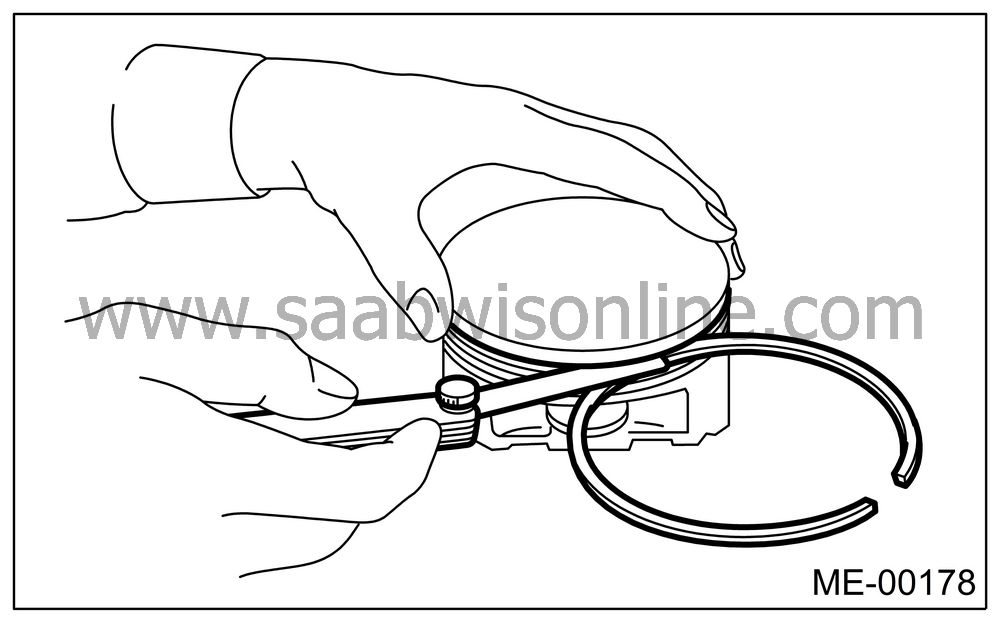
CONNECTING ROD |
Replace the connecting rod, if the large or small end thrust surface is damaged.
Check for bend or twist using a connecting rod aligner. Replace the connecting rod if the bend or twist exceeds the limit.
Limit of bend or twist per 100 mm (3.94 in) in length:
0.10 mm (0.0039 in)
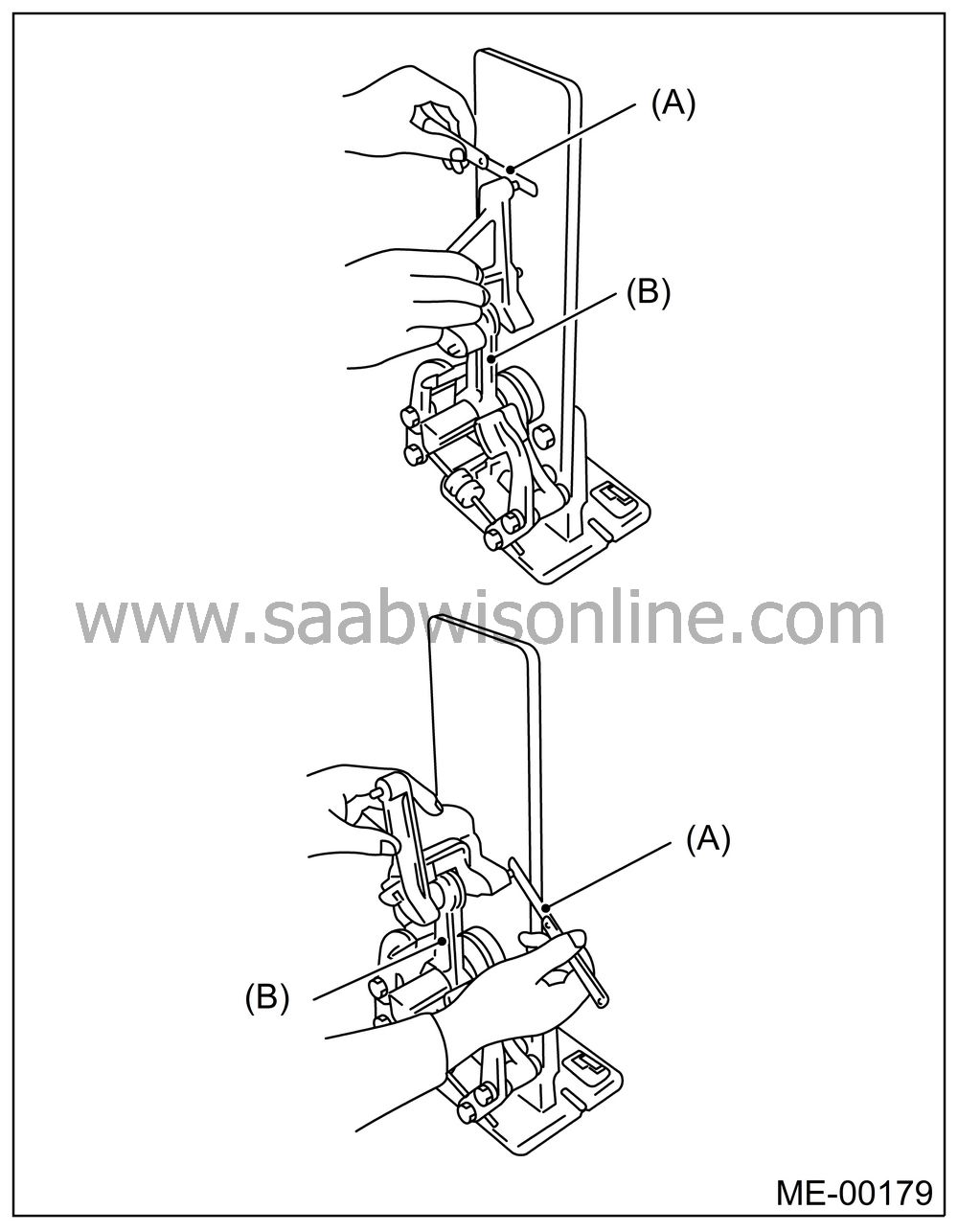
(A)
|
Thickness
gauge
|
(B)
|
Connecting
rod
|
Install the connecting rod fitted with bearing to crankshaft and measure the side clearance (thrust clearance). If side clearance exceeds the limit, replace the connecting rod.
Connecting rod side clearance:
Standard
0.070 — 0.330 mm (0.0028 — 0.0130 in)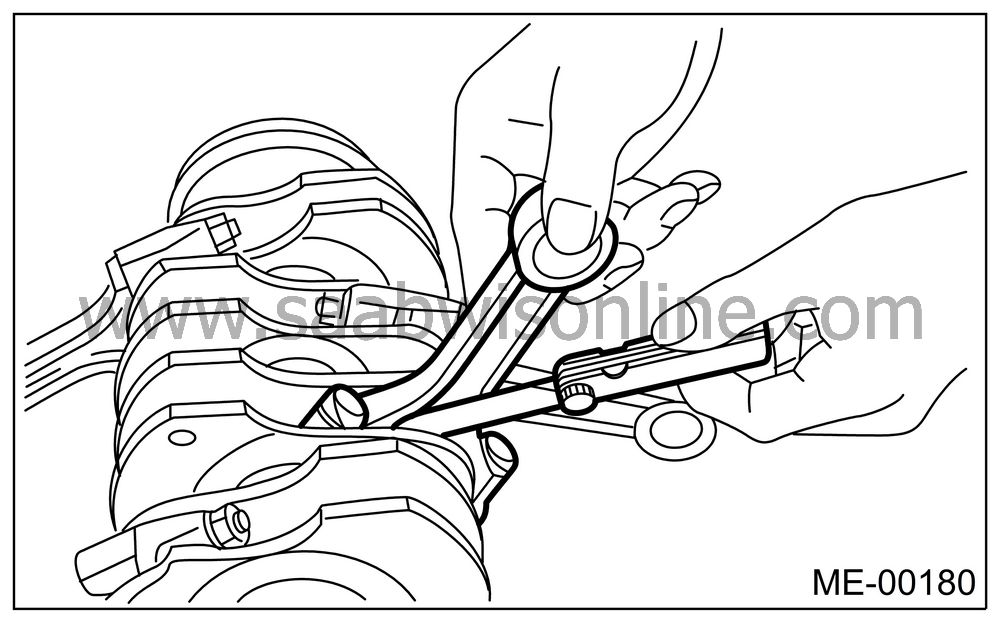
Inspect the connecting rod bearing for scar, peeling, seizure, melting, wear, etc.
Measure the oil clearance on individual connecting rod bearings by means of plastigauge. If any oil clearance is not within the specification, replace the defective bearing with a new one of standard size or undersize as necessary. (See the table below.)
Connecting rod oil clearance:
Standard
0.016 — 0.044 mm (0.00063 — 0.0017 in)
Unit: mm (in)
|
||
Bearings
|
Bearing
size
(Thickness at center) |
Outer
diameter of crank pin
|
Standard
|
1.492 — 1.501
(0.0587 — 0.0591) |
51.984 — 52.000
(2.0466 — 2.0472) |
0.03 (0.0012)
undersize |
1.510 — 1.513
(0.0594 — 0.0596) |
51.954 — 51.970
(2.0454 — 2.0461) |
0.05 (0.0020)
undersize |
1.520 — 1.523
(0.0598 — 0.0600) |
51.934 — 51.950
(2.0446 — 2.0453) |
0.25 (0.0098)
undersize |
1.620 — 1.623
(0.0638 — 0.0639) |
51.734 — 51.750
(2.0368 — 2.0374) |
Inspect the bushing at connecting rod small end, and replace if worn or damaged. Also measure the piston pin clearance at the connecting rod small end.
Clearance between piston pin and bushing:
Standard
0 — 0.022 mm (0 — 0.0009 in)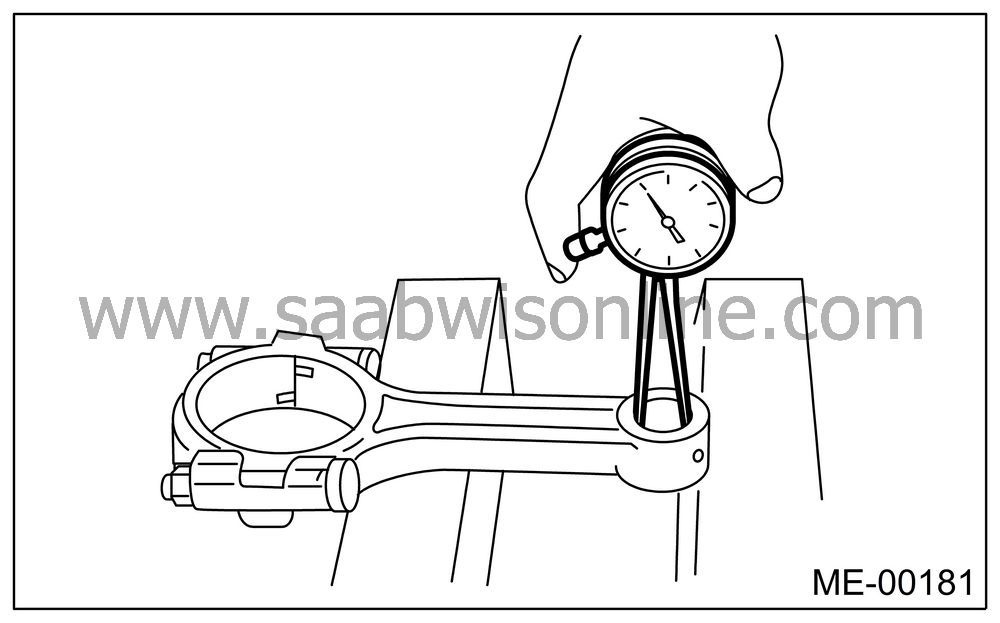
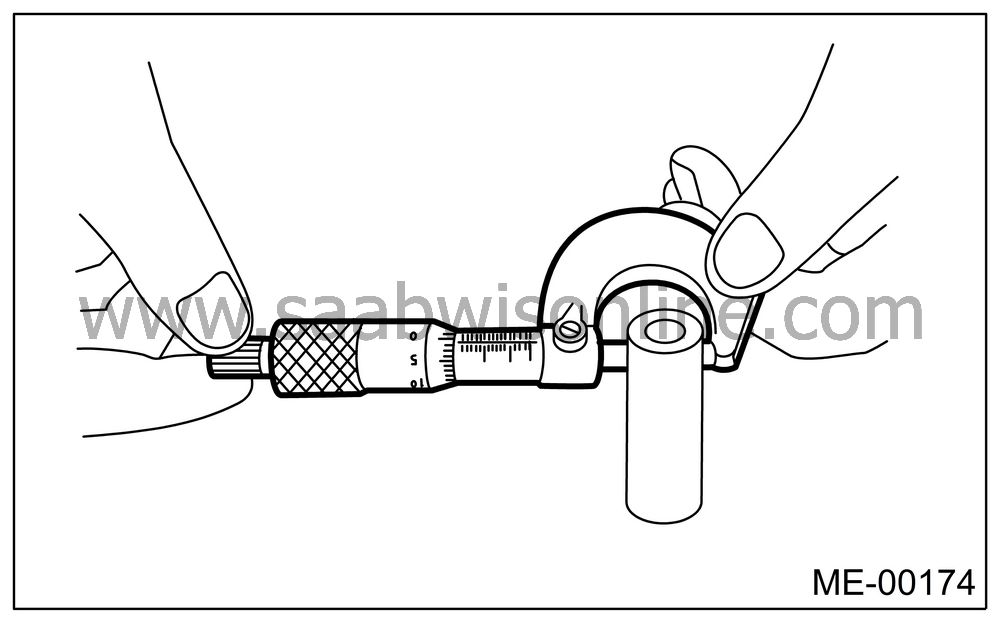
Replacement procedure is as follows.
Remove the bushing from connecting rod with ST and press.
Press the bushing with ST after applying oil on the periphery of bushing.
ST 32005122 CONNECTING ROD BUSHING REMOVER AND INSTALLER
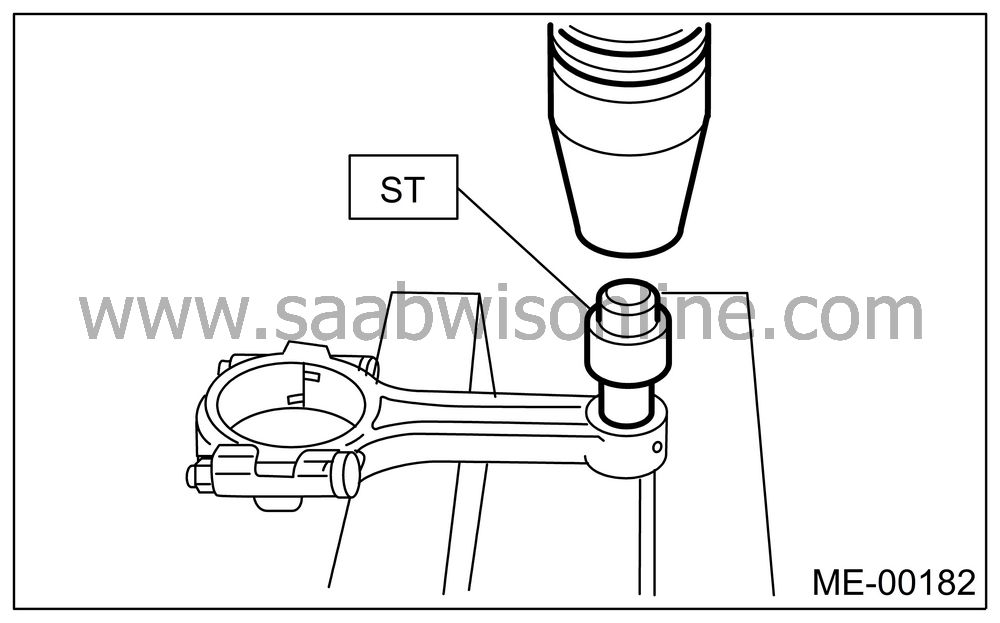
Make two 3 mm (0.12 in)-holes in bushing. Ream the inside of bushing.
After completion of reaming, clean the bushing to remove chips.
CRANKSHAFT AND CRANKSHAFT BEARING |
Clean the crankshaft completely, and check it for cracks using red lead. Replace if faulty.
Measure the bend of crankshaft. If it exceeds the limit, repair or replace it.
Note | ||
If a suitable V-block is not available, install #1 and #5 crankshaft bearing on cylinder block, position the crankshaft on these bearings, and then measure the crankshaft bend using a dial gauge. |
Crankshaft bend limit:
0.035 mm (0.0014 in)
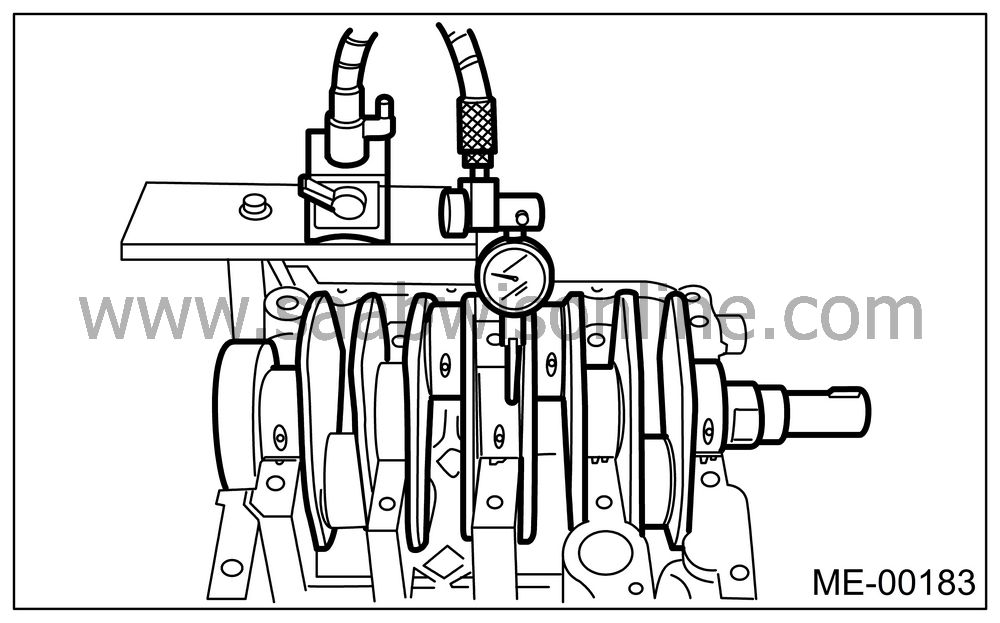
Inspect the crank journal and crank pin for wear. If they are not within the specifications, replace the bearing with a suitable (undersize) one, and replace or recondition crankshaft as necessary. When grinding the crank journal or crank pin, finish them to the specified dimensions according to the undersize bearing to be used.
Crank pin:
Out-of-roundness
0.003 mm (0.0001 in)Cylindricality
0.004 mm (0.0002 in)Grinding limit
To 51.750 mm (2.0374 in) dia.Crank journal:
Out-of-roundness
0.005 mm (0.0002 in)Cylindricality
0.006 mm (0.0002 in)Grinding limit
To 59.750 mm (2.3524 in) dia.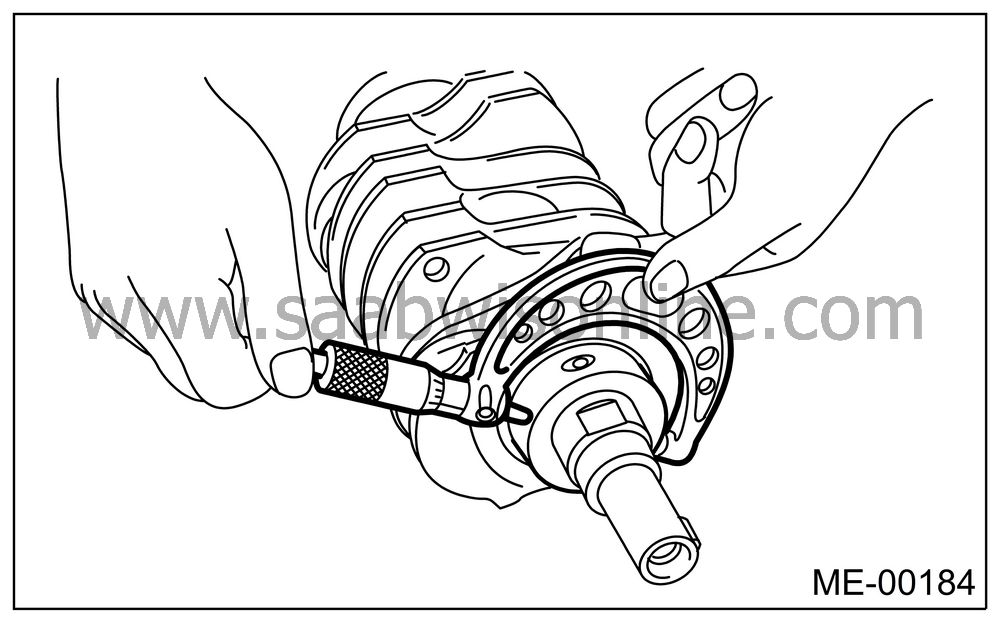
Unit: mm (in)
|
||||
Crank journal outer diameter
|
Crank pin outer diameter
|
|||
#1, #3
|
#2, #4, #5
|
|||
Standard
|
Journal
O.D.
|
59.992 — 60.008
(2.3619 — 2.3625) |
59.992 — 60.008
(2.3619 — 2.3625) |
51.984 — 52.000
(2.0466 — 2.0472) |
Bearing
size
(Thickness at center) |
1.998 — 2.011
(0.0787 — 0.0792) |
2.000 — 2.013
(0.0787 — 0.0793) |
1.492 — 1.501
(0.0587 — 0.0591) |
|
0.03 (0.0012)
undersize |
Journal
O.D.
|
59.962 — 59.978
(2.3607 — 2.3613) |
59.962 — 59.978
(2.3607 — 2.3613) |
51.954 — 51.970
(2.0454 — 2.0461) |
Bearing
size
(Thickness at center) |
2.017 — 2.020
(0.0794 — 0.0795) |
2.019 — 2.022
(0.0795 — 0.0796) |
1.510 — 1.513
(0.0594 — 0.0596) |
|
0.05 (0.0020)
undersize |
Journal
O.D.
|
59.942 — 59.958
(2.3599 — 2.3605) |
59.942 — 59.958
(2.3599 — 2.3605) |
51.934 — 51.950
(2.0446 — 2.0453) |
Bearing
size
(Thickness at center) |
2.027 — 2.030
(0.0798 — 0.0799) |
2.029 — 2.032
(0.0799 — 0.0800) |
1.520 — 1.523
(0.0598 — 0.0600) |
|
0.25 (0.0098)
undersize |
Journal
O.D.
|
59.742 — 59.758
(2.3520 — 2.3527) |
59.742 — 59.758
(2.3520 — 2.3527) |
51.734 — 51.750
(2.0368 — 2.0374) |
Bearing
size
(Thickness at center) |
2.127 — 2.130
(0.0837 — 0.0839) |
2.129 — 2.132
(0.0838 — 0.0839) |
1.620 — 1.623
(0.0638 — 0.0639) |
Measure the side clearance of crankshaft at center bearing. If clearance exceeds the limit, replace the bearing.
Crankshaft side clearance:
Standard
0.030 — 0.115 mm (0.0012 — 0.0045 in)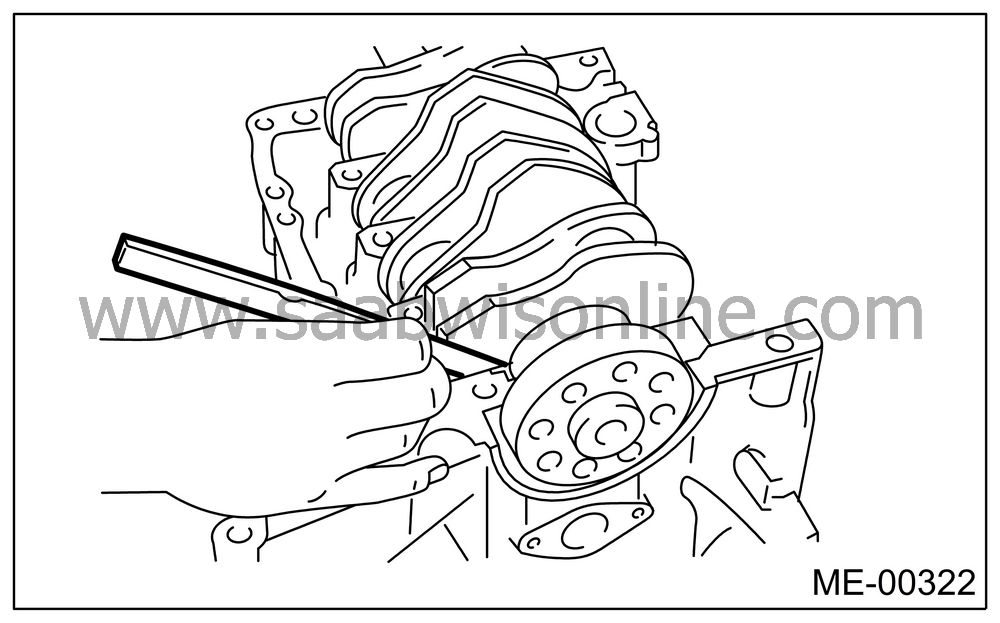
Inspect individual crankshaft bearings for signs of flaking, seizure, melting and wear.
Measure the oil clearance on each crankshaft bearing by means of plastigauge. If the measurement is not within the specification, replace the defective bearing with an undersize one, and replace or recondition the crankshaft as necessary.
Crankshaft oil clearance: