Crankshaft position sensor
Crankshaft position sensor |
The ECM receives information on the position and speed of the crankshaft from the crankshaft position sensor on pin 41.
A perforated disc with 58 ribs is mounted on the crankshaft. The sensor is of the inductive type and is mounted in the crankcase wall of the engine. The distance between the sensor and the perforated disc is within the range 0.4-1.3 mm and is not adjustable.
The sensor acts as a generator and supplies a sinusoidal alternating current. The ECM can determine engine speed by measuring the frequency. Two ribs are missing after the 58th rib on the perforated disc. When rib 1 passes the sensor, the ECM knows that the crankshaft is 117° before top dead centre (BTDC).
The voltage from the crankshaft position sensor varies with engine speed. During idling the voltage is 7-10 V (AC) and at 2500 rpm it is approx. 15-20 V (AC). However, it is the frequency and not the voltage which is of interest to the ECM.
The ECM chiefly uses engine speed and crankshaft position to calculate ignition timing, fuel injection timing, fuel injection time and boost pressure and for idle speed control.
Fuel injection is switched off when engine speed exceeds 6200 rpm.
As soon as the ECM receives pulses from the crankshaft position sensor, the ECM grounds the main and fuel pump relays.
If the sensor fails to work or if there is a break in the circuit, the engine will not start.
The sensor resistance is 540±55 Ohm.
Engine speed signal |
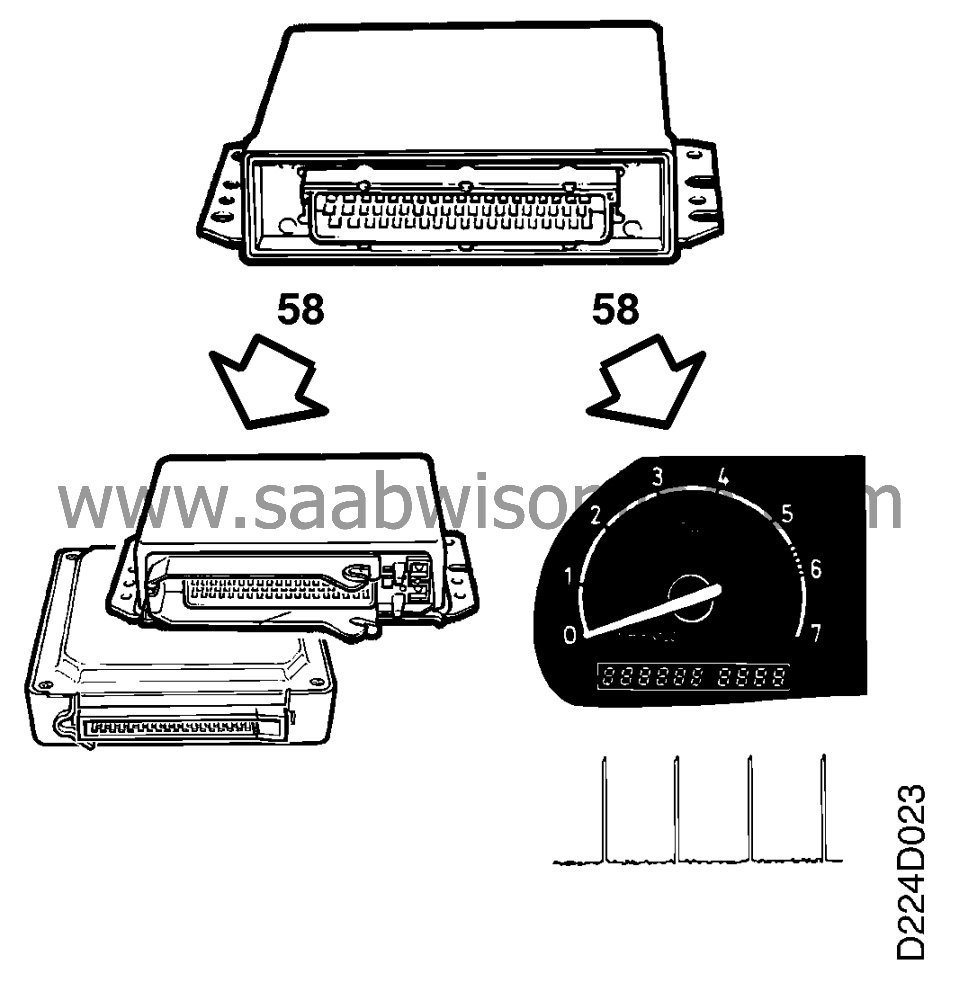
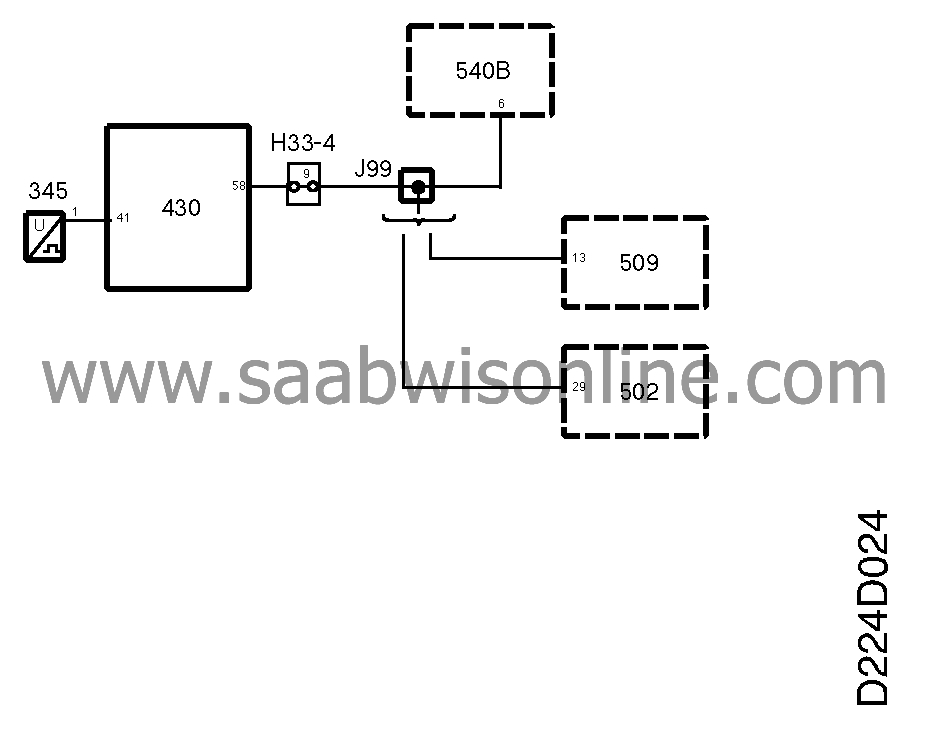
The ECM emits an engine speed signal from pin 58.
The signal is a pulse train which varies between 0 and Batt+ and which measures approx. 30 Hz during idling and approx. 85 Hz at 2500 rpm. This corresponds to 2 pulses per crankshaft rotation.
The engine speed signal is used by the main instrument, the clutch control module and the automatic transmission control module.
If the engine speed signal is shorted to ground, the engine can be started but will stop a short time afterwards.