INSTALLATION
INSTALLATION |
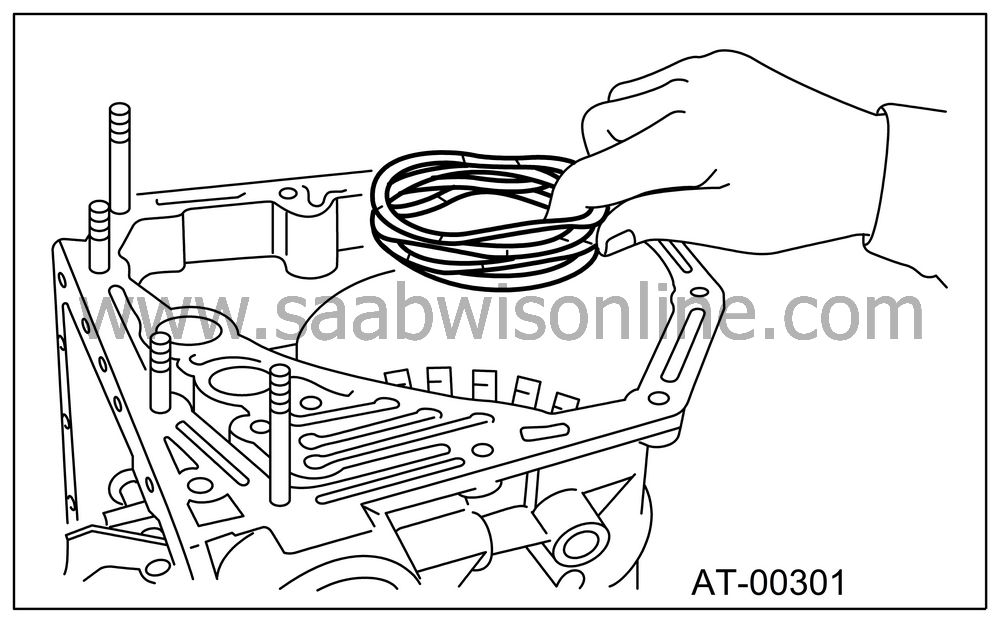
Install spring retainer.
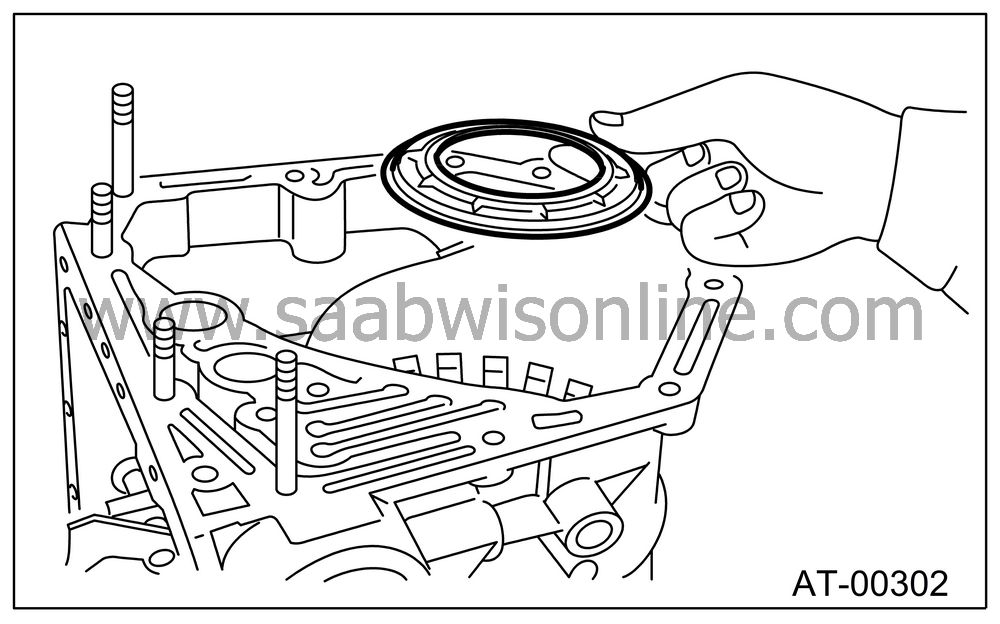
Install the one-way clutch inner race, spring retainer and return spring.
Tighten socket head bolts evenly from the rear side of the transmission case.
Tightening torque:
25 Nm (2.5 kgf-m, 18.1 ft-lb)
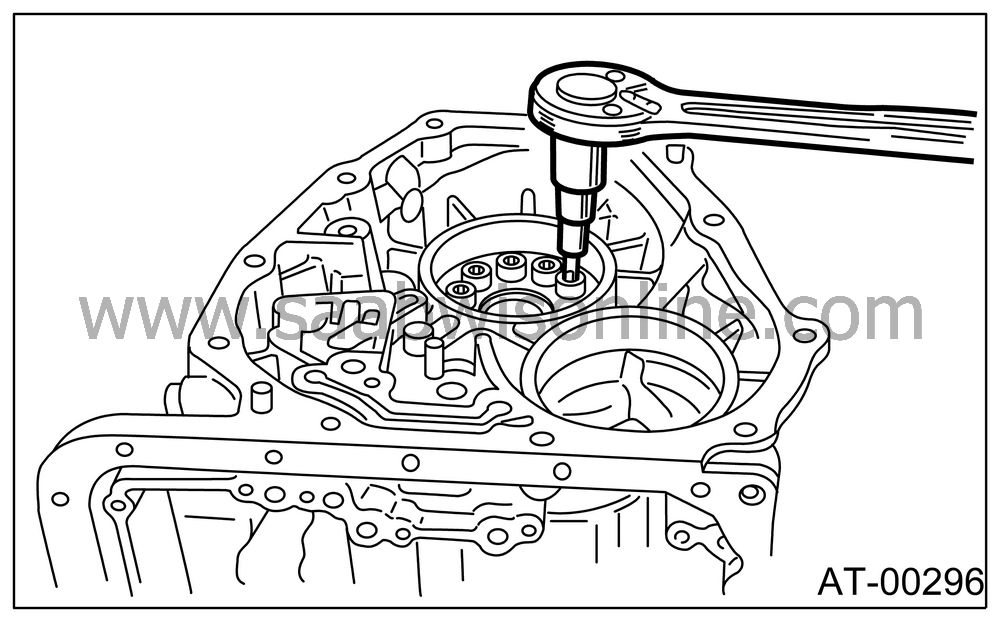
Place the front side of transmission body up.
Install thrust needle bearing.
Place the dish plate, driven plate, drive plate and retaining plate neatly in this order on surface table.
Set the micro gauge to retaining plate, and read its scale. Make more than three measurements at even distance and take the average value.
Note | ||
The value, which is read in the gauge at this time, is zero point. |
Scale and record the weight “Z” of a flat board which will be put on plates.
Note | ||
• |
Use a stiff flat board which does not bend against load.
|
|
• |
Use a flat board of its weight less than 83 N (8.5 kgf,
18.7 lb).
|
Put the flat board on retaining plate.
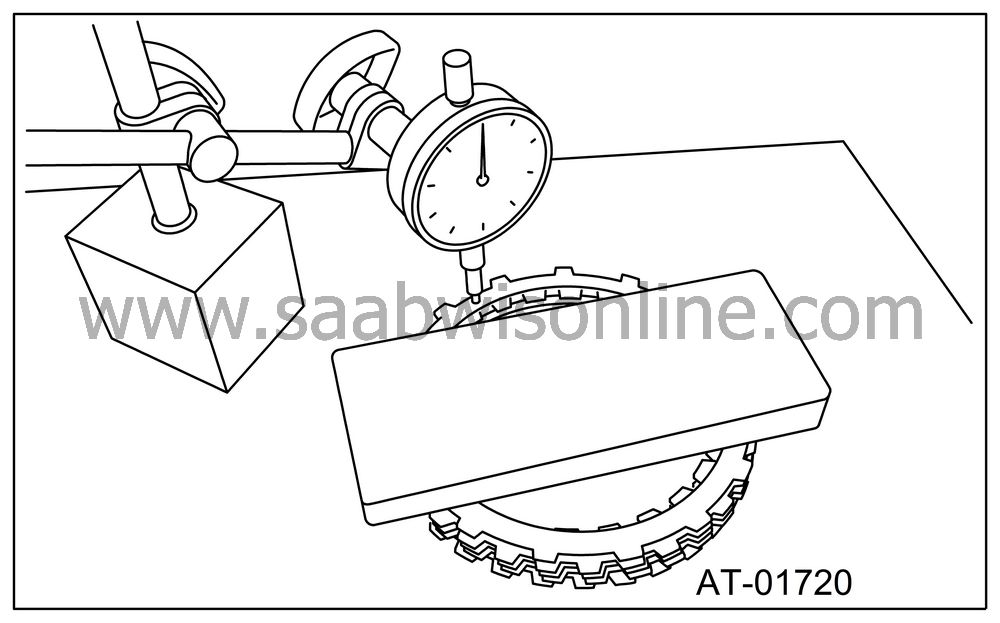
Using the following formula, calculate “N” indicated on the push/pull gauge.
N = 83 N (8.5 kgf, 18.7 lb) − Z
N: Value indicated on push/pull gauge
83 N (8.5 kgf, 18.7 lb): Load applied to clutch plate
Z: Flat board weight
Press the center of retaining plate applying force of N with push/pull gauge, and then measure and record the height A. Make more than three measurements at even distance and take the average value.
Note | ||
If three points, measure the height every 120°. If four points, measure the height every 90°. |
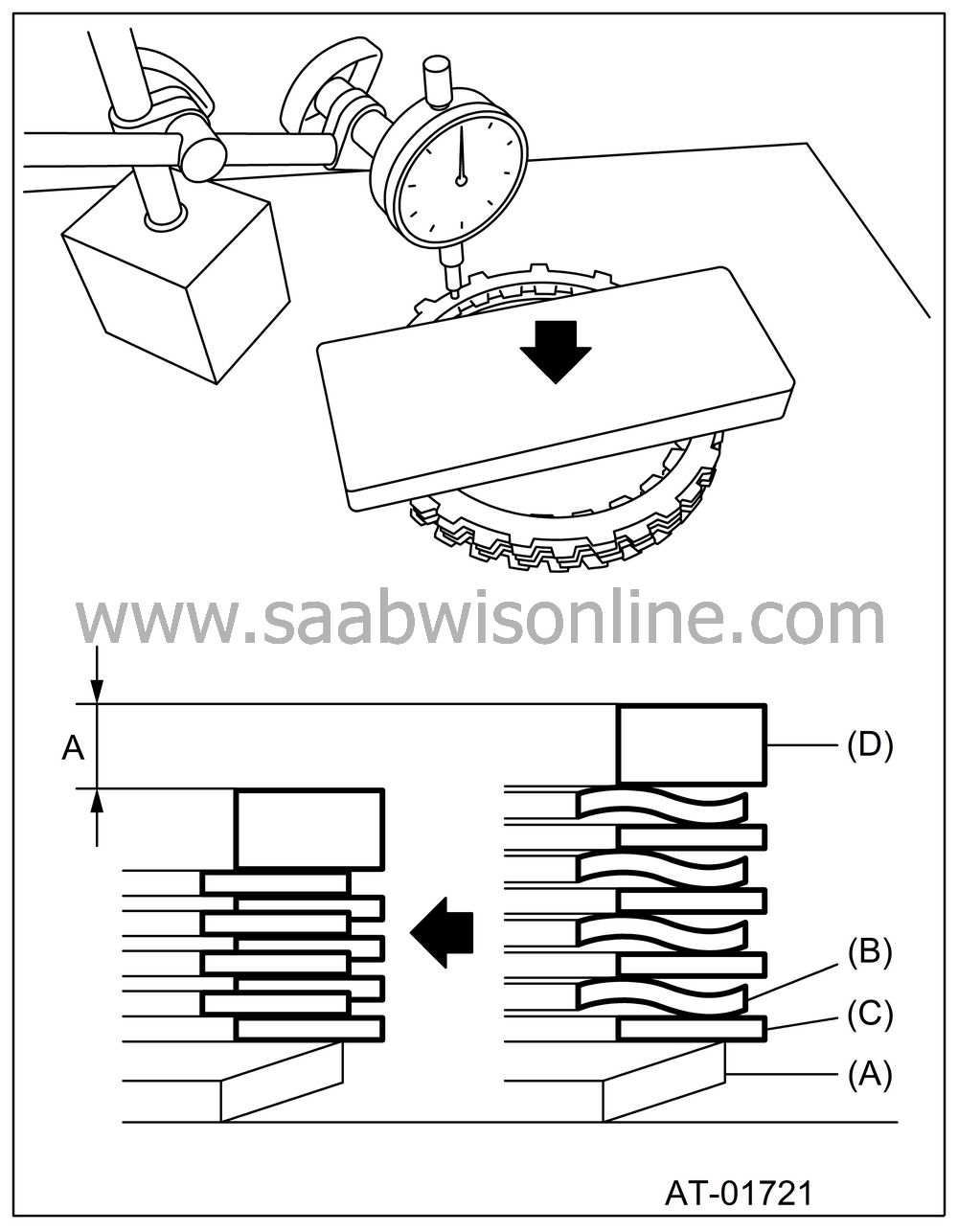
(A)
|
Dish plate
|
(B)
|
Driven
plate
|
(C)
|
Drive plate
|
(D)
|
Retaining
plate
|
Installation of the low & reverse brake:
Install the dish plate, driven plate and retaining plate, and then secure them with snap ring.
Note | ||
Pay attention to the orientation of dish plate. |
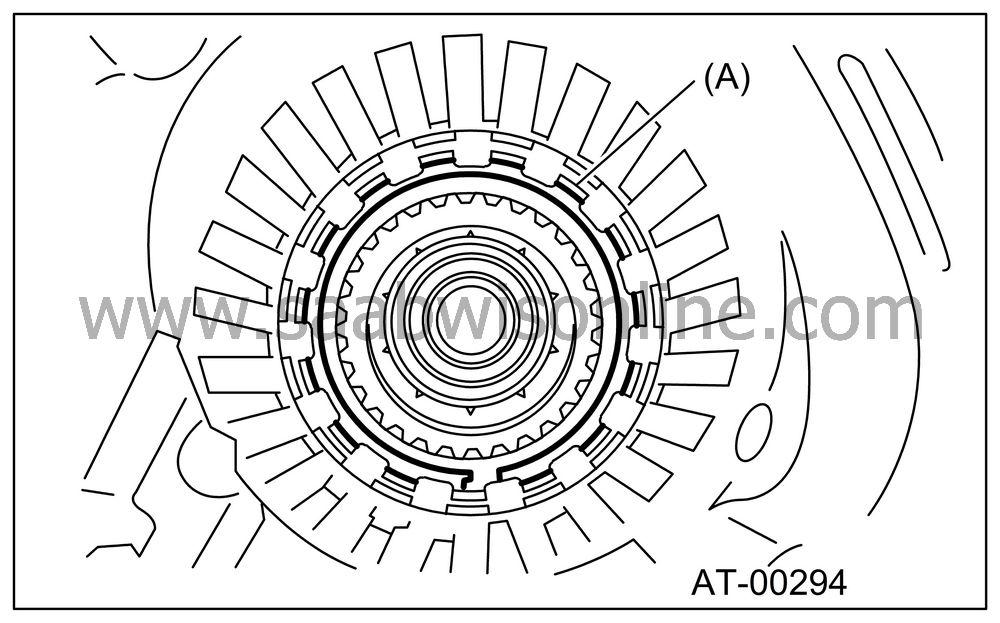
(A)
|
Snap ring
|
Apply compressed air intermittently to check for operation.
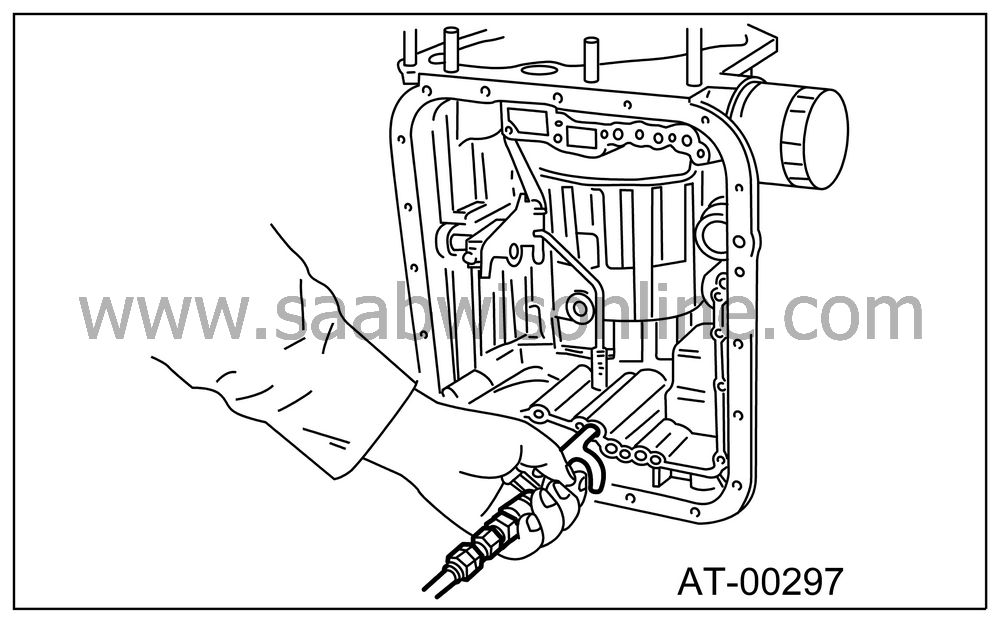
Place the same thickness of shim on both sides to prevent the plate from tilting, and then measure and record the clearance B.
Note | ||
Do not press the shim downward with excessive force, or else the waveform of drive plates will be broken down. |
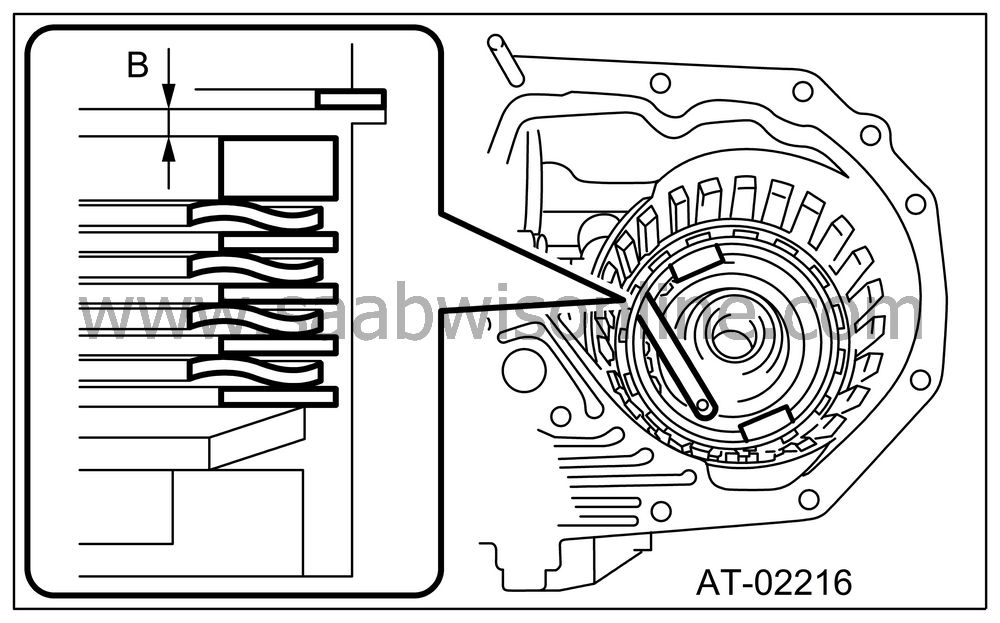
Piston stroke calculation
Select the retaining plate within the specification by calculating with A and B dimensions which have been recorded before. If the calculated value exceeds the service limit, replace the drive plate with a new one and adjust it within the specification.
T = A + B
T: Piston stroke
A: Collapse amount of drive plate
B: Clearance between retaining plate and snap ring
Saab 9-2X 2.5i Linear
Initial standard:
2.15 — 2.65 mm (0.073 — 0.093 in)Limit thickness:
2.95 mm (0.104 in)Saab 9-2X 2.0T Aero
Initial standard:
2.70 — 3.20 mm (0.106 — 0.126 in)Limit thickness:
3.90 mm (0.154 in)
Retaining plate
|
|
Part
number
|
Thickness
mm (in)
|
32006573
|
3.8
(0.150)
|
32006566
|
4.1
(0.161)
|
32006567
|
4.4
(0.173)
|
32006568
|
4.7
(0.185)
|
32006569
|
5.0
(0.197)
|
32006570
|
5.3
(0.209)
|
32006571
|
5.6
(0.220)
|
32006572
|
5.9
(0.232)
|
Install the low & reverse brake leaf spring.
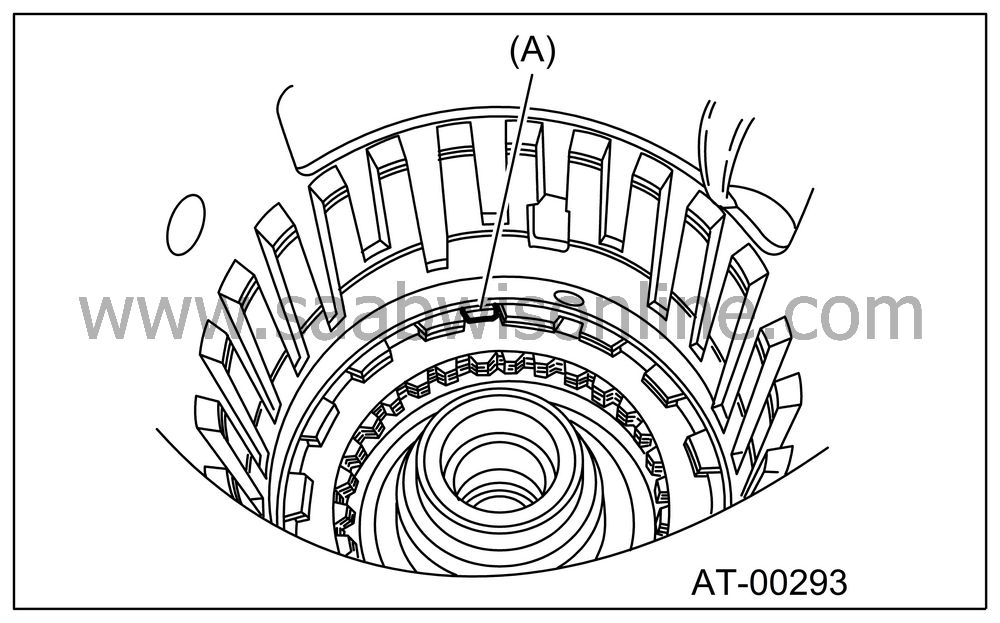
(A)
|
Leaf spring
|
Install the 2-4 brake piston and 2-4 brake retainer by aligning hole of 2-4 brake retainer and hole of transmission case.
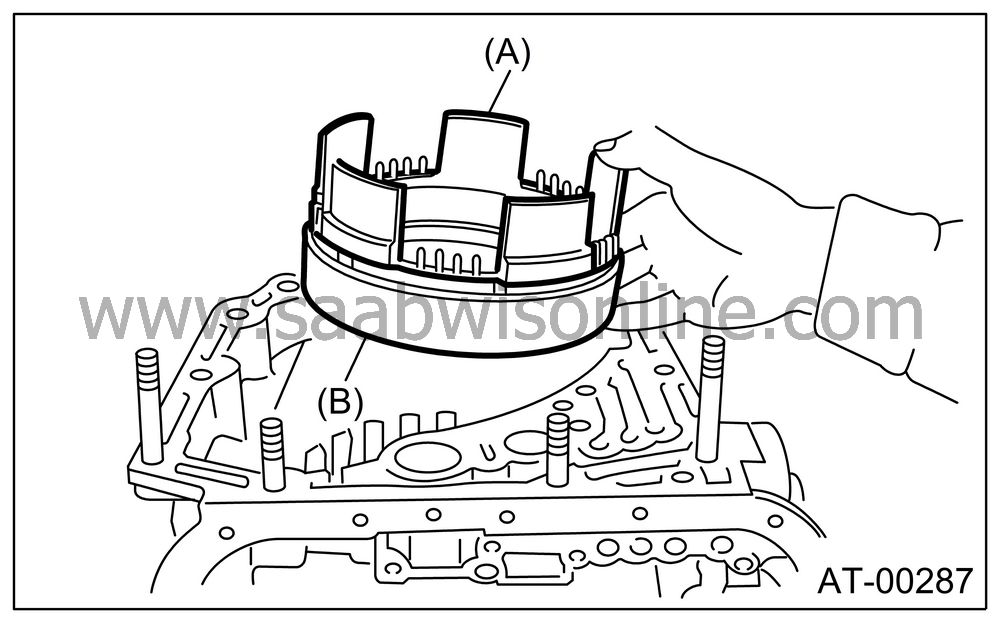
(A)
|
2-4 brake
piston
|
(B)
|
2-4 brake
piston retainer
|
Install 2-4 brake piston return spring to transmission case.
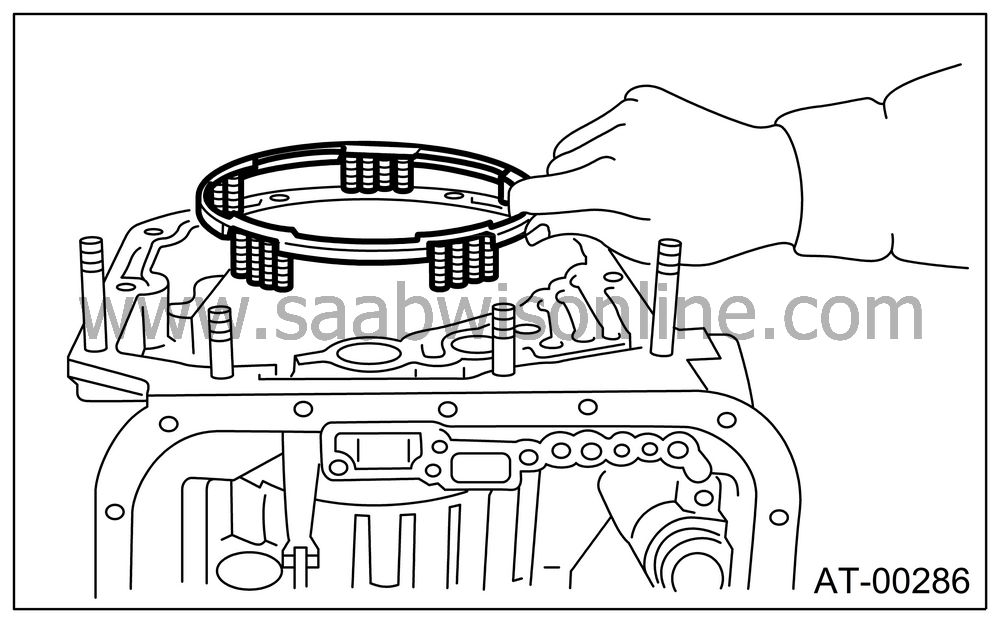
Position snap ring in transmission. Using ST, press the snap ring into place.
ST 32005113 COMPRESSOR
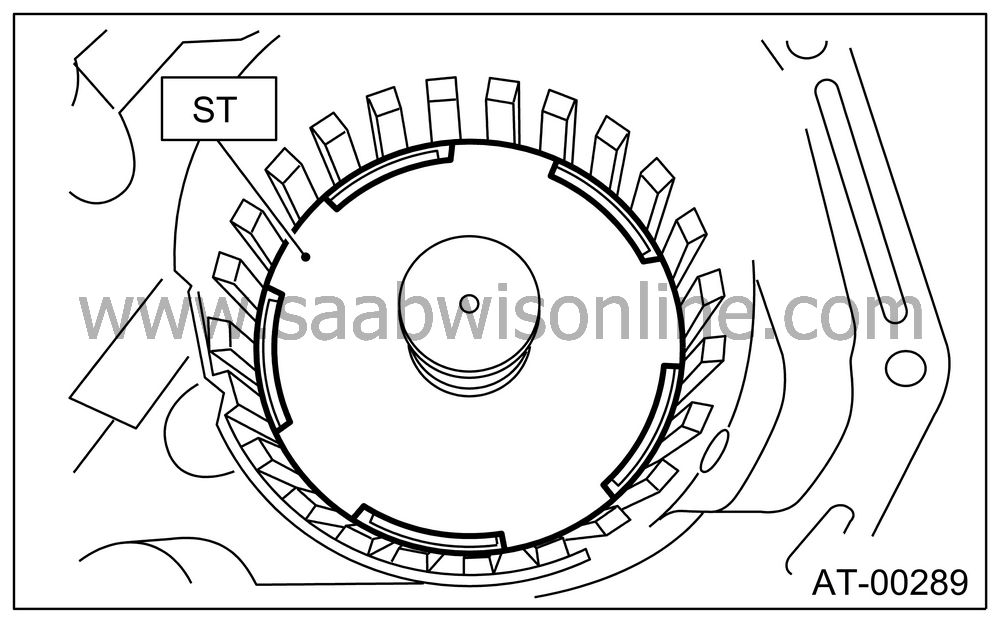
Install planetary gear and low clutch assembly to transmission case.
Install carefully while rotating the low clutch and planetary gear assembly slowly paying special attention not to damage the seal ring.
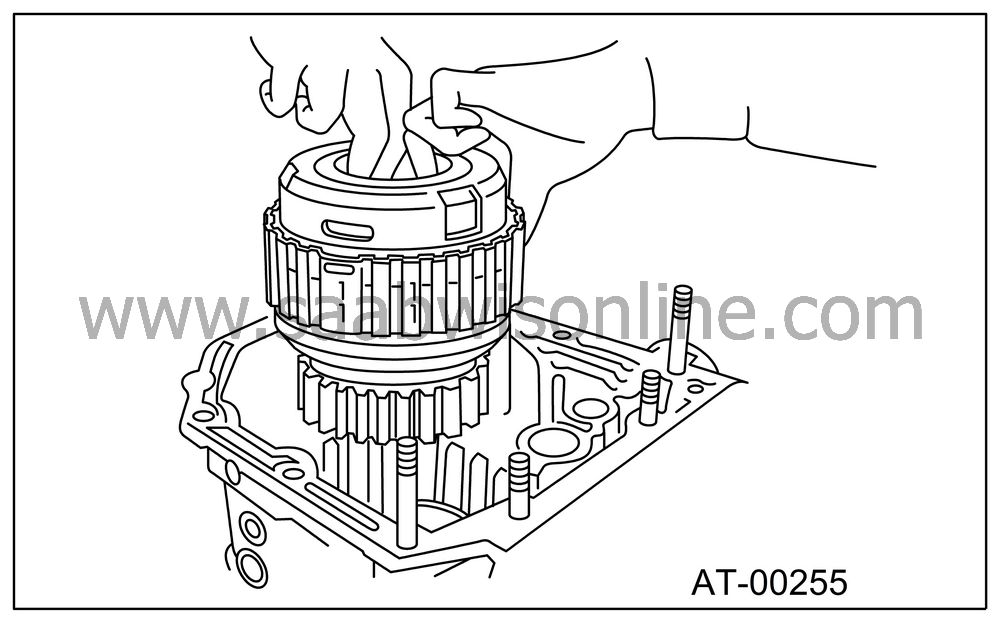
Selection of 2-4 brake retaining plate (Saab 9-2X 2.0T Aero)
Install pressure plate, drive plate, driven plate, retaining plate and snap ring.
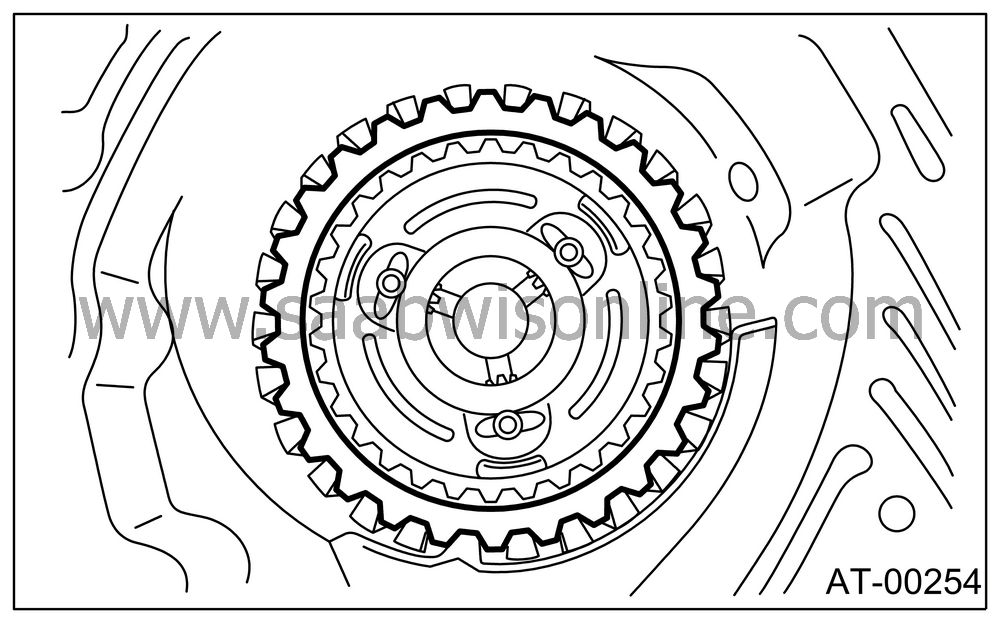
Install a new 2-4 brake oil seal to transmission case.
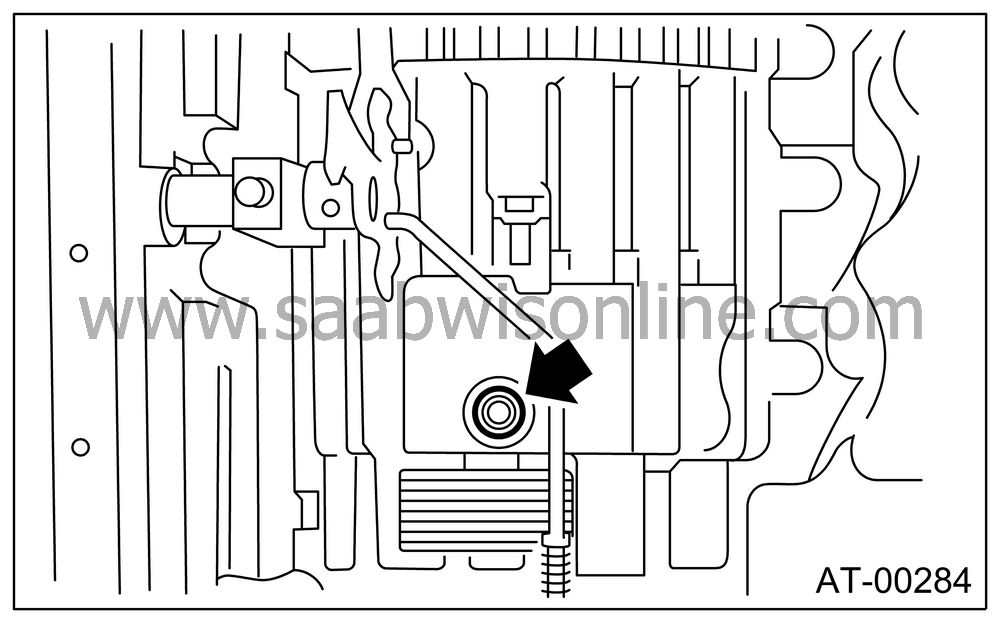
After all 2-4 brake component parts have been installed, blow in air intermittently and confirm the operation of the brake.
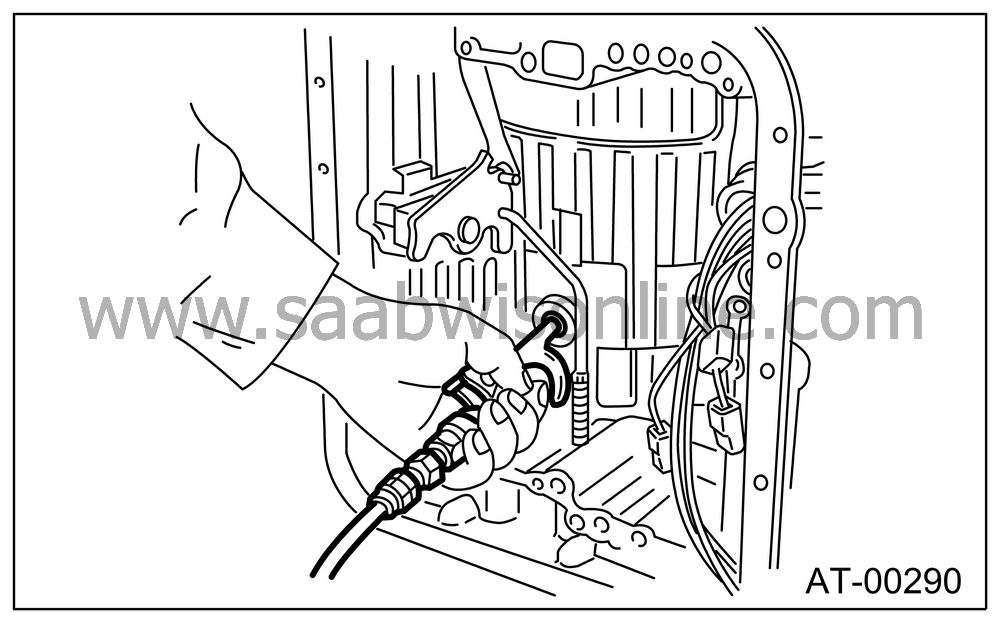
Check the clearance between the retaining plate and the snap ring.
Note | ||
Select a retaining plate with a suitable value from the following table, so that the clearance becomes the standard value. |
||
If it exceeds the service limit, replace the drive plate with a new one and adjust it within the specification. |
Initial standard:
0.8 — 1.2 mm (0.031 — 0.047 in)
Limit thickness:
1.5 mm (0.059 in)
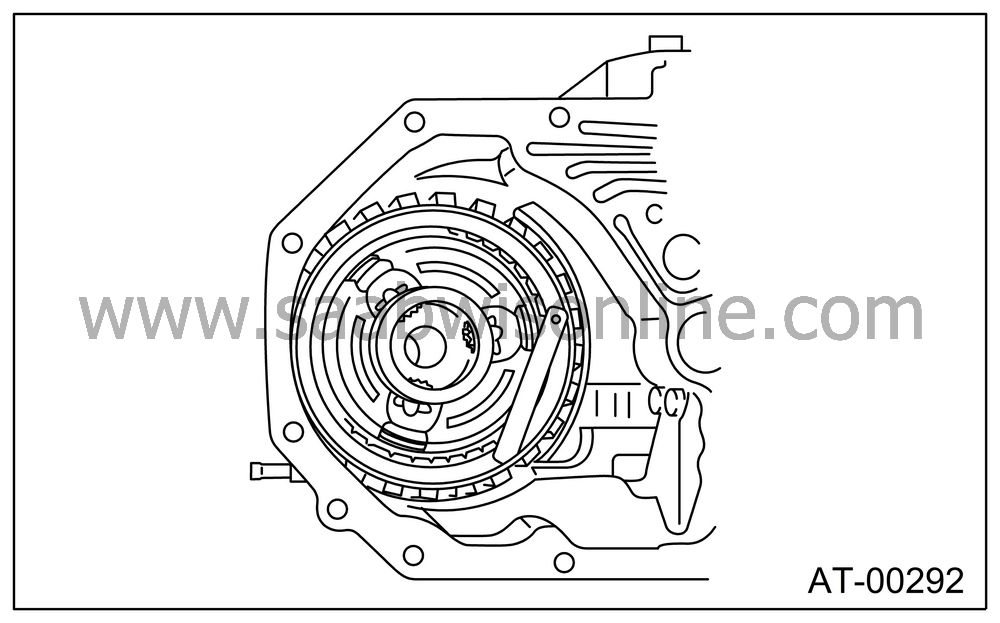
Retaining plate | |
Part No. | Thickness mm (in) |
32006521
|
5.6
(0.220)
|
32006522
|
5.8
(0.228)
|
32006523
|
6.0
(0.236)
|
32006524
|
6.2
(0.244)
|
32006525
|
6.4
(0.252)
|
32006526
|
6.6
(0.260)
|
Selection of 2-4 brake retaining plate (Saab 9-2X 2.5i Linear)
Place the dish plate, driven plate, drive plate and retaining plate neatly in this order on surface table.
Set the micro gauge to clutch, and read its scale.
Note | ||
The value, which is read in the gauge at this time, is zero point. |
Scale and record the weight “Z” of a flat board which will be put on plates.
Note | ||
• |
Use a stiff flat board which does not bend against load.
|
|
• |
Use a flat board of its weight less than 100 N (10.2
kgf, 22.5 lb).
|
Put the flat board on retaining plate.
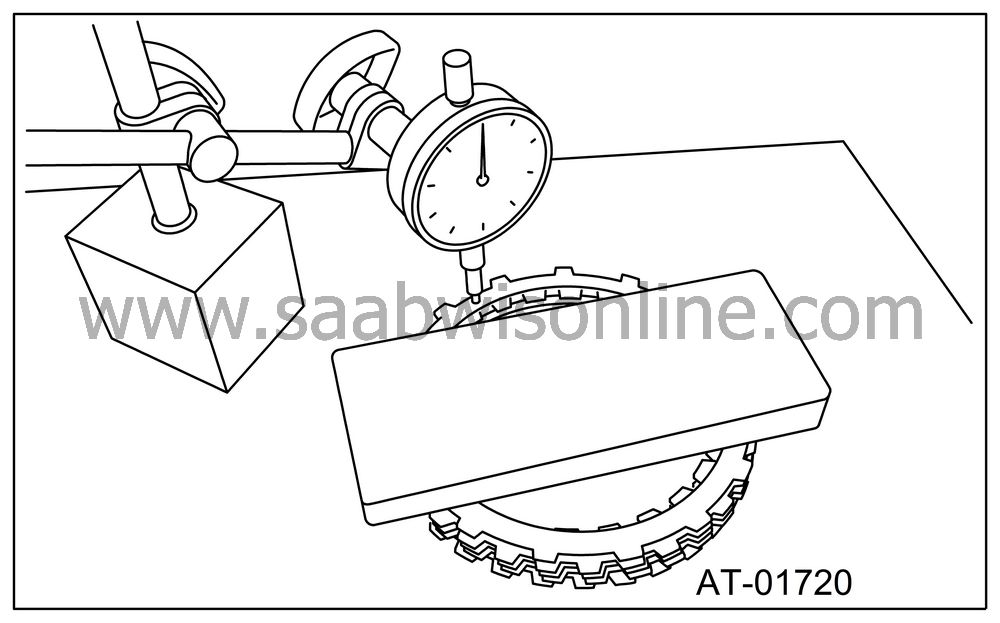
Using the following formula, calculate “N” indicated on the push/pull gauge.
N = 100 N (10.2 kgf, 22.5 lb) − Z
N: Value indicated on push/pull gauge
100 N (10.2 kgf, 22.5 lb): Load applied to clutch plate
Z: Flat board weight
Press the center of retaining plate applying force of N with push/pull gauge, and then measure and record the height A. Make more than three measurements at even distance and take the average value.
Note | ||
If three points, measure the height every 120°. If four points, measure the height every 90°. |
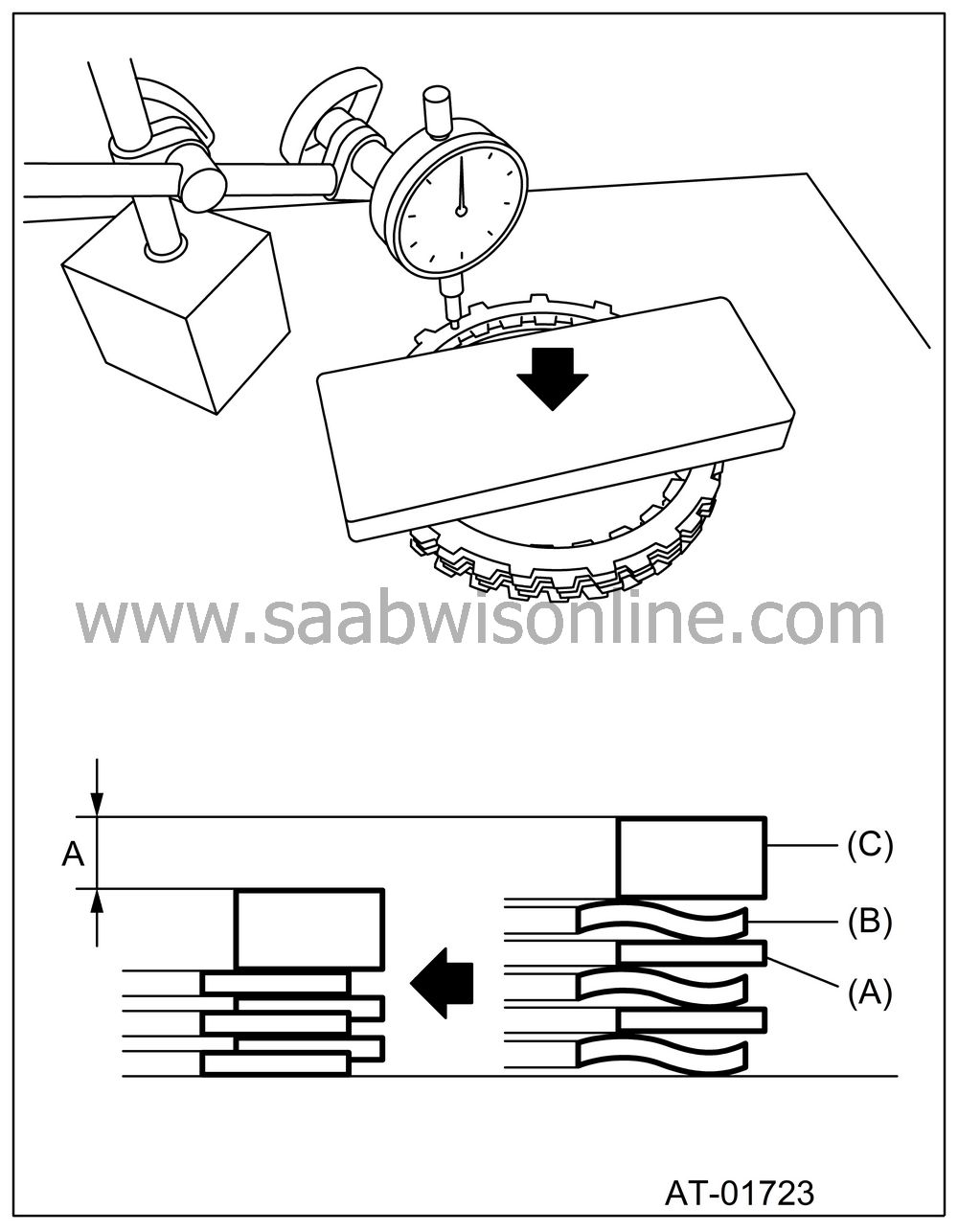
(A)
|
Driven
plate
|
(B)
|
Drive plate
|
(C)
|
Retaining
plate
|
Install the pressure plate, drive plate, driven plate, retaining plate and snap ring.
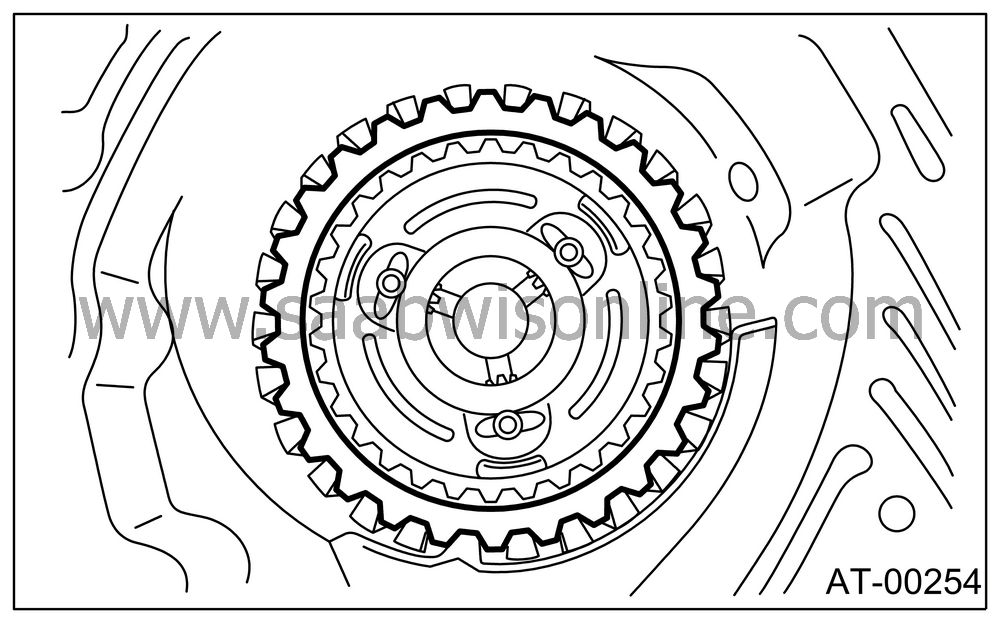
Install a new 2-4 brake oil seal to transmission case.
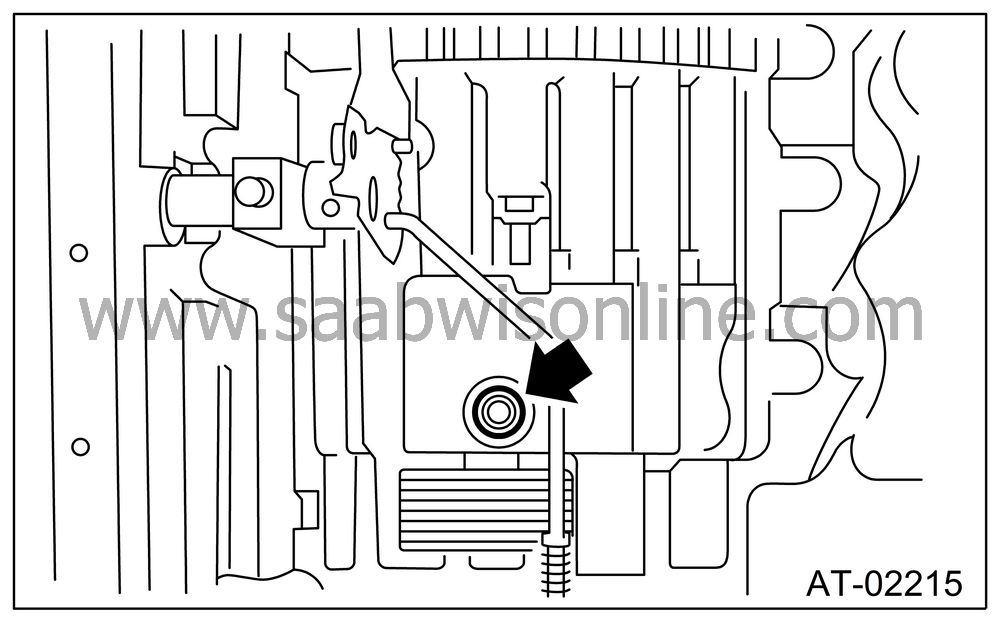
After all 2-4 brake component parts have been installed, blow air intermittently and confirm the operation of brake.
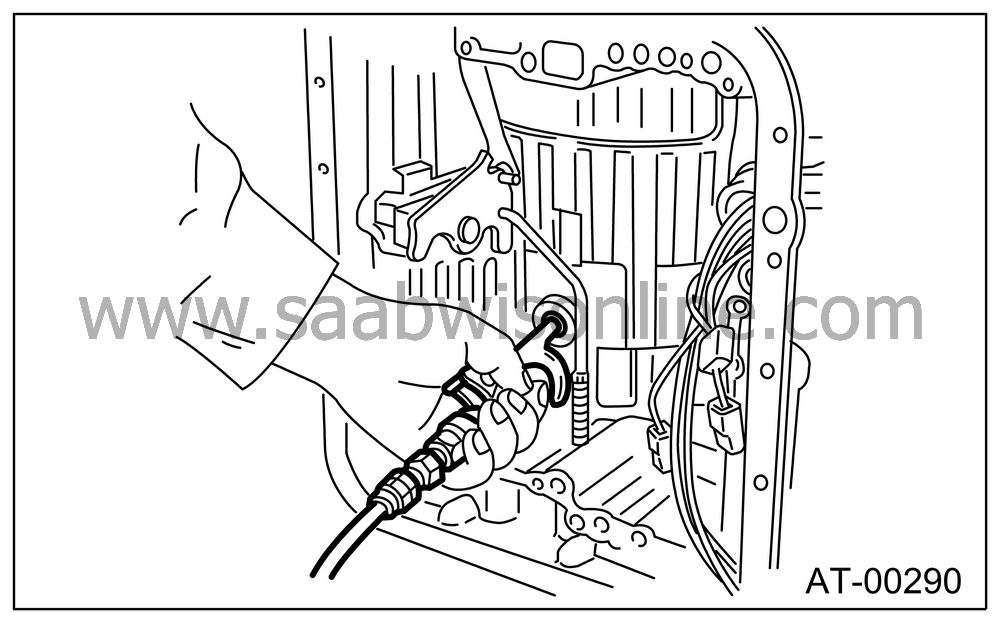
Measure and record the clearance B between the retaining plate and snap ring.
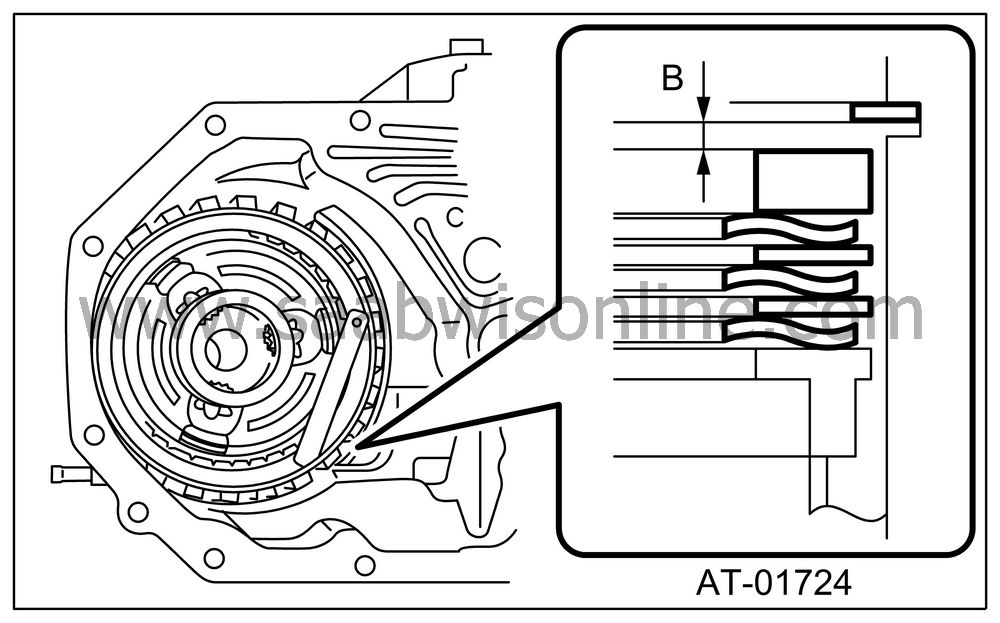
Piston stroke calculation
Select the retaining plate within the specification by calculating with A and B dimensions which have been recorded before. If the calculated value exceeds the usage limit, replace the drive plate with a new one and adjust it within the specitication.
T = A + B
T: Piston stroke
A: Collapse amount of drive plate
B: Clearance between retaining plate and snap ring
Initial standard:
1.7 — 2.1 mm (0.067 — 0.083 in)
Limit thickness:
2.3 mm (0.091 in)
Retaining plate | |
Part number | Thickness mm (in) |
32006521
|
5.6
(0.220)
|
32006522
|
5.8
(0.228)
|
32006523
|
6.0
(0.236)
|
32006524
|
6.2
(0.244)
|
32006525
|
6.4
(0.252)
|
32006526
|
6.6
(0.260)
|
Be careful not to mistake the location of the leaf spring to be inserted.
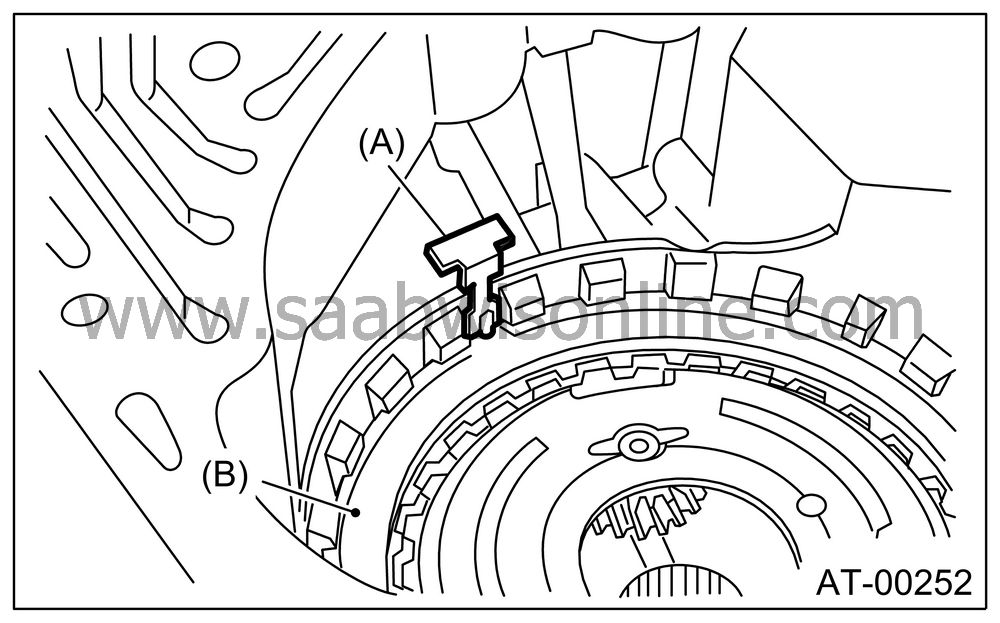
(A)
|
Leaf spring
|
(B)
|
Retaining
plate
|
Install thrust needle bearing in the correct direction.
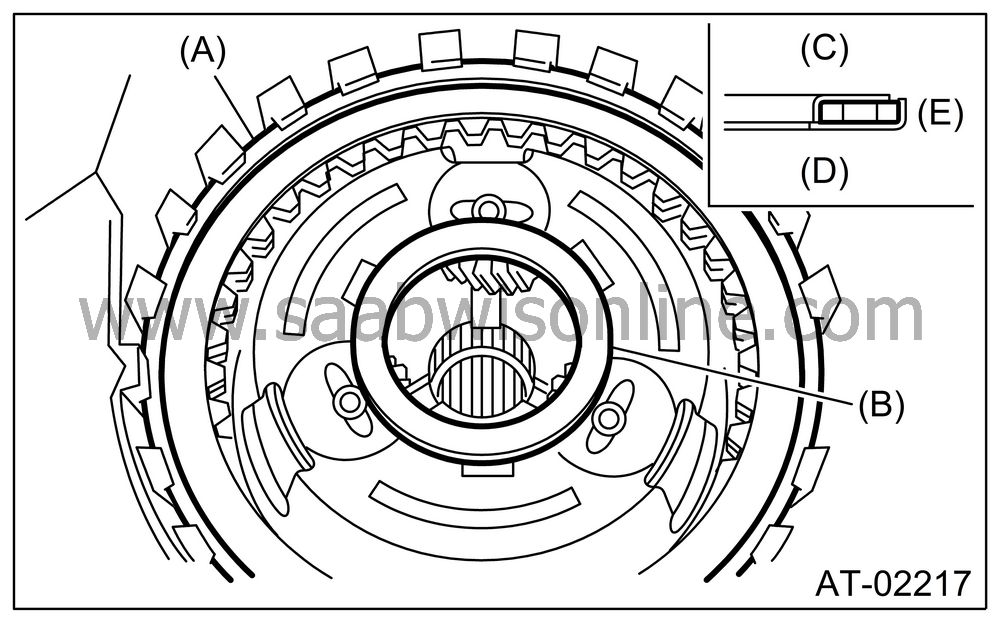
(A)
|
Snap ring
|
(B)
|
Thrust
needle bearing
|
(C)
|
Upside
|
(D)
|
Downside
|
(E)
|
Outside
|
Install front sun gear and thrust needle bearing.
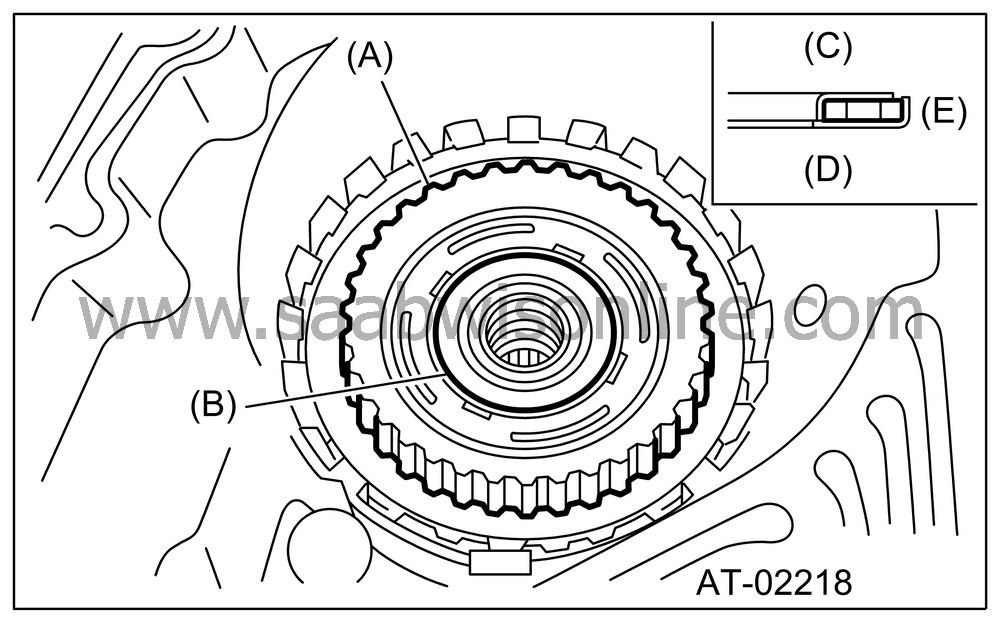
(A)
|
Front sun
gear
|
(B)
|
Thrust
needle bearing
|
(C)
|
Clutch
hub side
|
(D)
|
Front sun
gear side
|
(E)
|
Outside
|
Install the high clutch hub.
Attach the thrust needle bearing to the hub with vaseline and install the hub by correctly engaging the splines of the front planetary carrier.
Install the thrust needle bearing in proper direction.
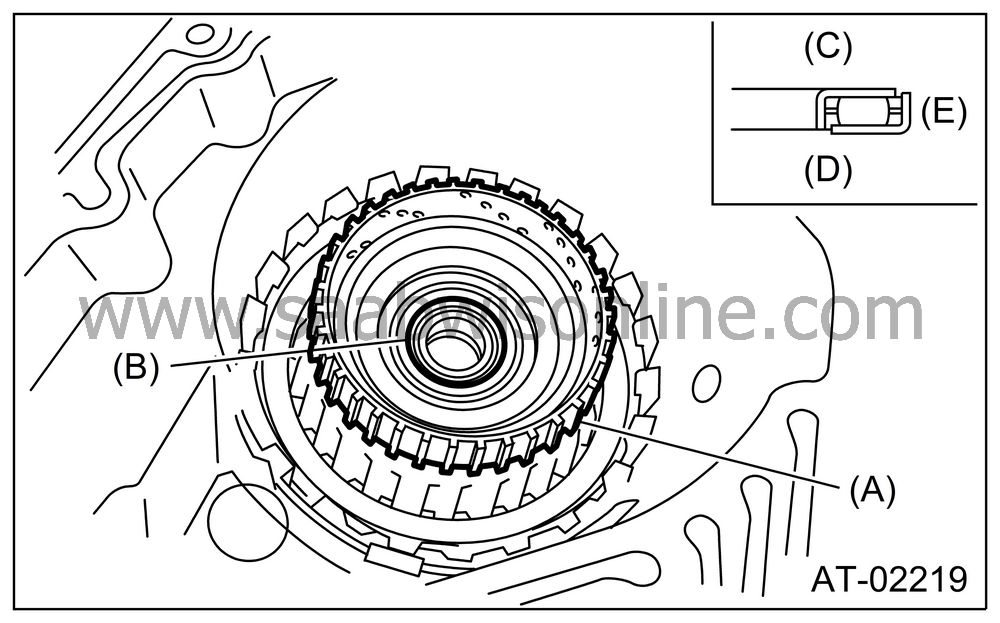
(A)
|
High clutch
hub
|
(B)
|
Thrust
needle bearing
|
(C)
|
Upside
|
(D)
|
Downside
|
(E)
|
Outside
|
Install the high clutch assembly.
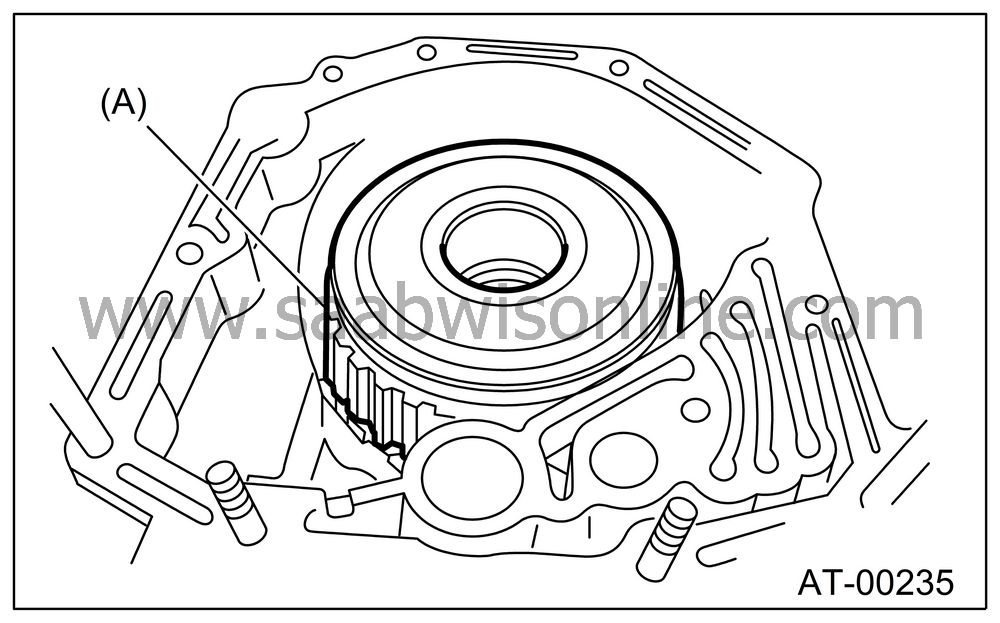
(A)
|
High clutch
and reverse clutch assembly
|
Adjust total end play.

Install the thrust needle bearing in proper direction.
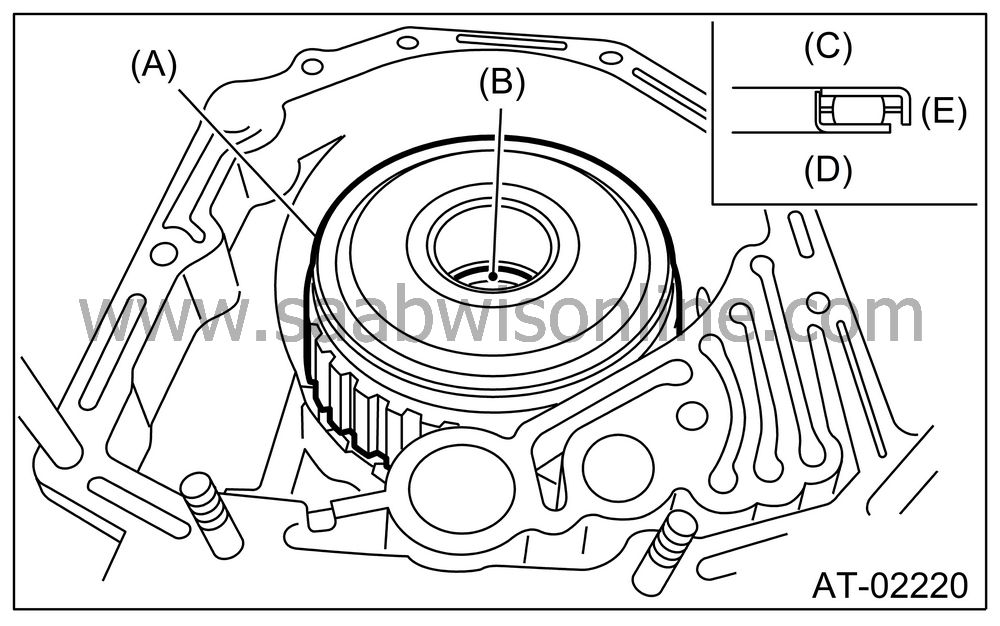
(A)
|
High clutch
and reverse clutch ASSY
|
(B)
|
Thrust
needle bearing
|
(C)
|
Upside
|
(D)
|
Downside
|
(E)
|
Outside
|
Install the oil pump housing assembly.
Install the converter case assembly to the transmission case assembly.

Insert inhibitor switch and transmission connector into stay.
Install air breather hose.

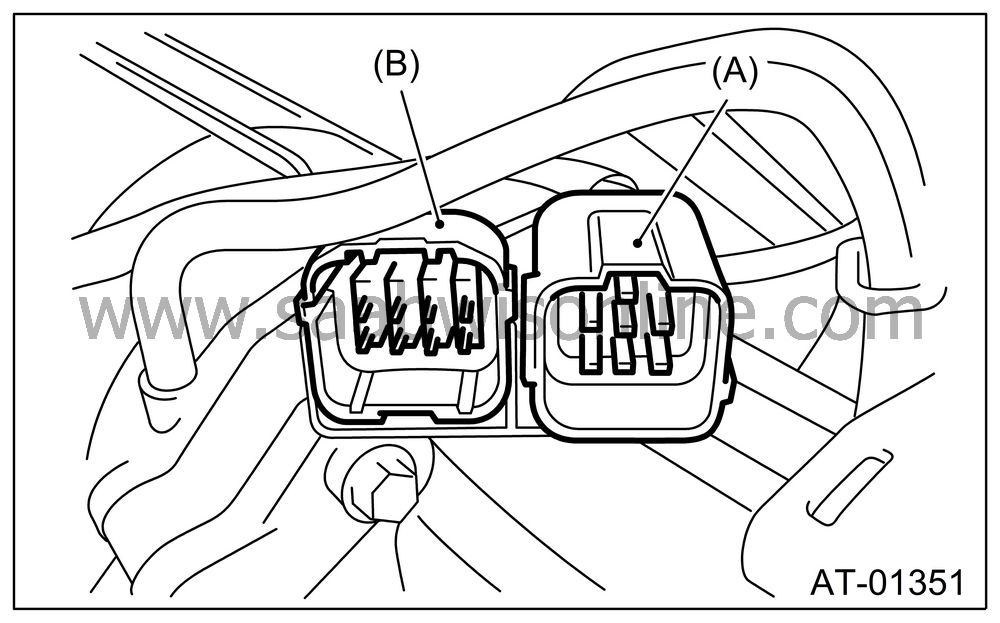
(A)
|
Transmission
harness
|
(B)
|
Inhibitor
switch harness
|
Install oil cooler pipes.

Install the oil charge pipe with O-ring.

Insert the input shaft while turning lightly by hand. At this time, not to damage the bushing.
Normal protrusion A:
50 — 55 mm (1.97 — 2.17 in)
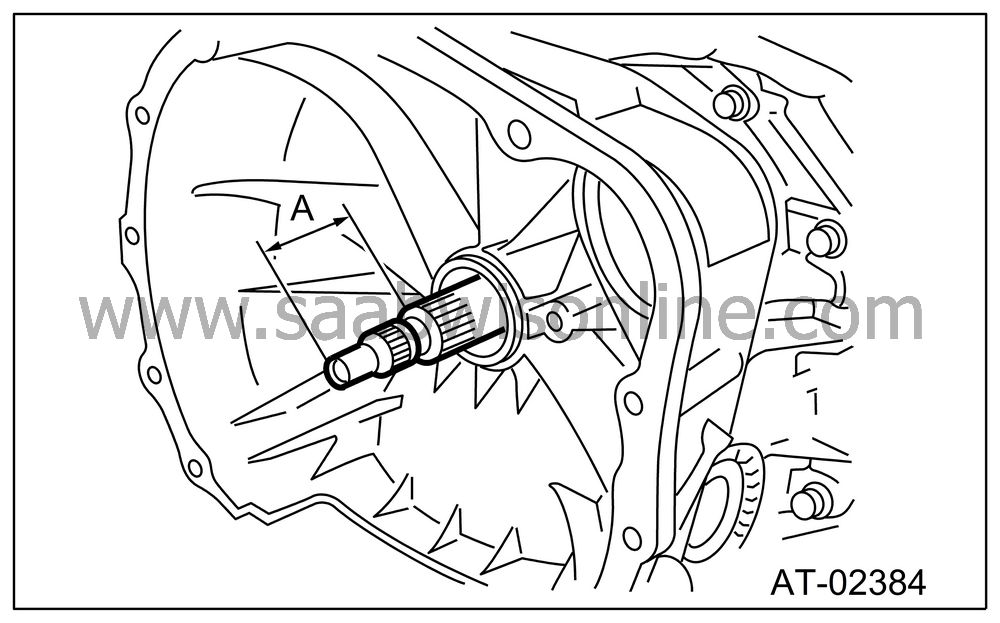
Install the torque converter clutch assembly.

Install the transmission assembly to the vehicle.
